Rethink how you use 3D printer infill!
Summary
TLDRIn this video, the host explores the complexities of 3D printer infill, testing various patterns for speed, strength, and top surface support. Using PETG filament from sponsor VOXELPLA, the experiment compares 2D and 3D patterns, nozzle sizes, and the balance between infill and shell thickness. The results show cubic infill as the strongest and fastest, with aligned rectilinear excelling in surface support. The conclusion favors thicker shells over high infill for structural strength, offering insights for 3D printing enthusiasts.
Takeaways
- 😀 The video discusses the complexities of 3D printer infill, acknowledging the lack of a single 'best' answer due to varying needs and preferences.
- 🔍 The script explores three main aspects of infill: the best infill pattern, the use of thicker nozzles for infill, and the balance between infill and shell thickness.
- 📏 It compares infill patterns based on print speed, strength, and their ability to support the top surface of prints, using the same amount of material for each pattern.
- 🏗️ The video categorizes infill patterns into '2D', '3D', 'specialty', and 'dubious', highlighting their unique characteristics and applications.
- 🚀 The fastest infill pattern tested was concentric, which does a single continuous line, while the slowest was Lightning, due to its minimal material use and specific application.
- 💪 The strongest infill pattern in terms of bend load was cubic, which also printed quickly and supported top layers well.
- 🧩 The script notes that for structural prints, a thicker shell generally provides more strength than additional infill, except in specific part geometries that benefit from infill.
- 🌀 The video mentions that 3D and specialty infill patterns like cubic and lightning infill can provide better support for top surfaces compared to static 2D patterns.
- 🔧 The test used PETG filament from VOXELPLA, chosen for its balance of affordability, reliability, and suitability for mechanical applications.
- 🛠️ The methodology for testing involved adjusting infill percentages to ensure equal material usage across different shell thicknesses and infill densities.
- 📉 The results consistently showed that a thicker shell provided better strength than additional infill, suggesting a rule of thumb for part printing.
Q & A
What are the three main aspects of infill that the video aims to test?
-The video aims to test the 'best' infill pattern in terms of print speed, strength, and support for the top surface of the print; whether using a thicker nozzle for infill is beneficial; and whether more infill or a thicker shell provides better structural support.
Why did the author decide to use PETG for the tests instead of PLA or other materials?
-The author chose PETG because it's a good compromise material that is suitable for mechanical applications and provides reliable data, unlike PLA which is rigid but tends to creep, or polycarbonates and ABS which require a controlled environment for optimal printing.
What are the four categories of infill patterns mentioned in the script?
-The four categories of infill patterns are '2D', '3D', 'specialty', and 'dubious'.
Why is honeycomb considered an odd one out among the 2D infill patterns?
-Honeycomb is considered an odd one out because it is the only pattern that avoids crossing over itself, instead creating double-width walls in some spots.
What is the fastest infill pattern tested in the video?
-The fastest infill pattern tested is concentric, which does one single, continuous line.
Which infill pattern was found to be the strongest in the video's tests?
-Cubic infill pattern was found to be the strongest in the tests.
What is the general recommendation for infill percentage when printing structural parts?
-The general recommendation is to use just enough infill, around 15-20%, to ensure the part prints cleanly, and then use the rest of the material to increase the shell thickness.
What was the result of testing different shell thicknesses versus infill percentages for strength?
-The test results showed that a thicker shell always provided better strength than more infill, regardless of the starting infill percentage.
What is the significance of aligned rectilinear infill pattern in supporting the top solid layers?
-Aligned rectilinear provides almost perfect support for the top solid layers because its aligned pattern allows the first solid layer to bridge over cleanly at a 90° angle.
What is the author's suggestion for the default infill pattern in most cases?
-The author suggests that the default infill pattern should be cubic, or adaptive cubic, as it provides a good balance of strength, print speed, and support for the top surfaces.
Outlines
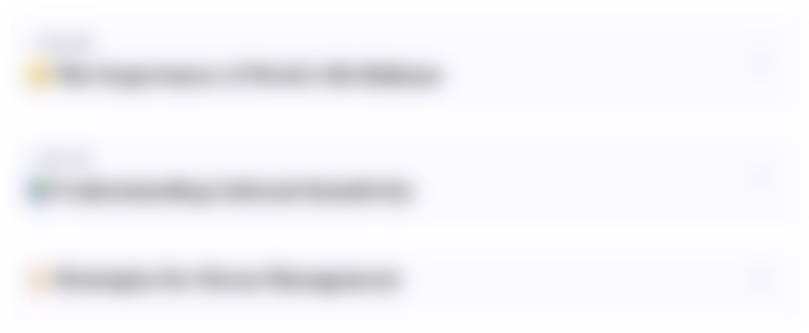
Esta sección está disponible solo para usuarios con suscripción. Por favor, mejora tu plan para acceder a esta parte.
Mejorar ahoraMindmap
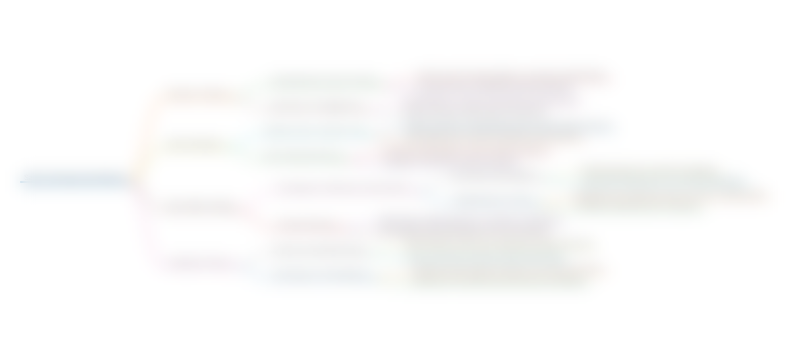
Esta sección está disponible solo para usuarios con suscripción. Por favor, mejora tu plan para acceder a esta parte.
Mejorar ahoraKeywords
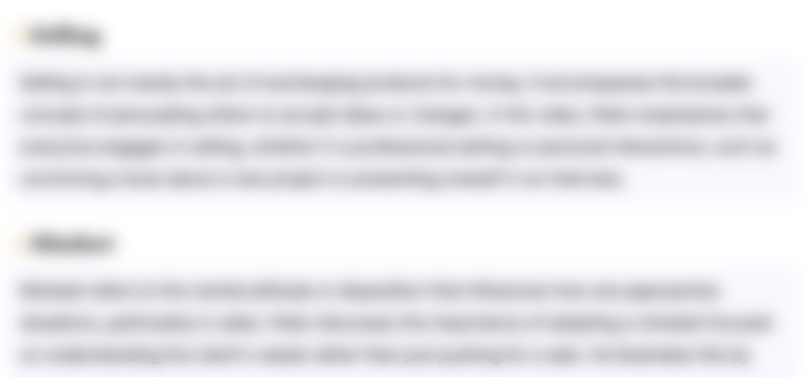
Esta sección está disponible solo para usuarios con suscripción. Por favor, mejora tu plan para acceder a esta parte.
Mejorar ahoraHighlights
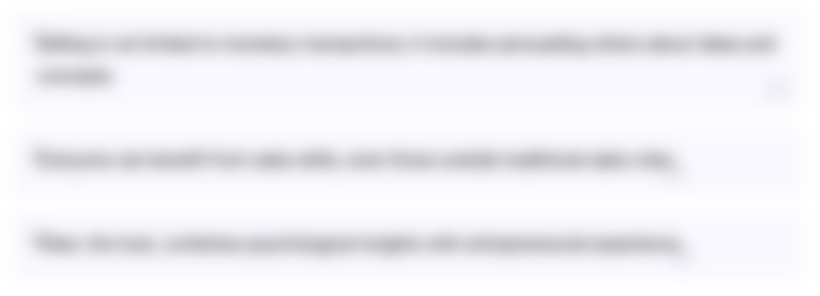
Esta sección está disponible solo para usuarios con suscripción. Por favor, mejora tu plan para acceder a esta parte.
Mejorar ahoraTranscripts
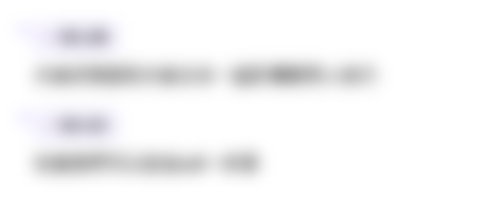
Esta sección está disponible solo para usuarios con suscripción. Por favor, mejora tu plan para acceder a esta parte.
Mejorar ahoraVer Más Videos Relacionados
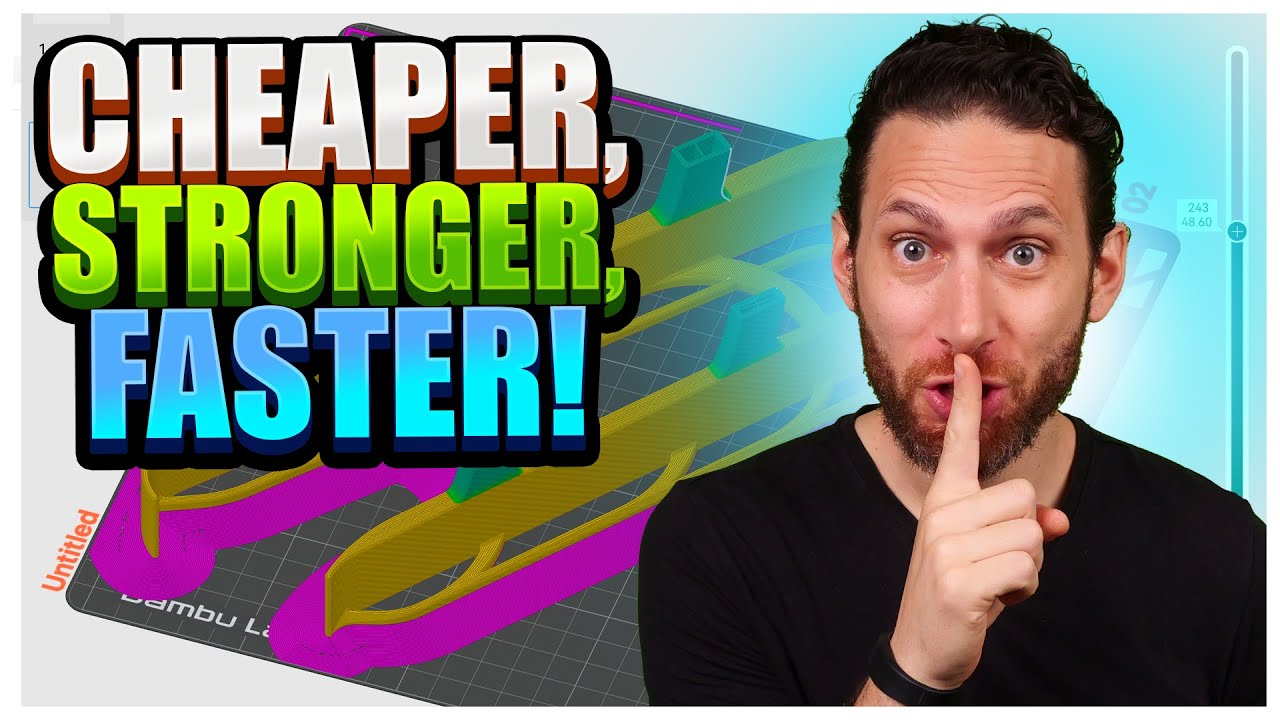
Rapidly Improve Your 3D Prints with Hidden Slicer Settings
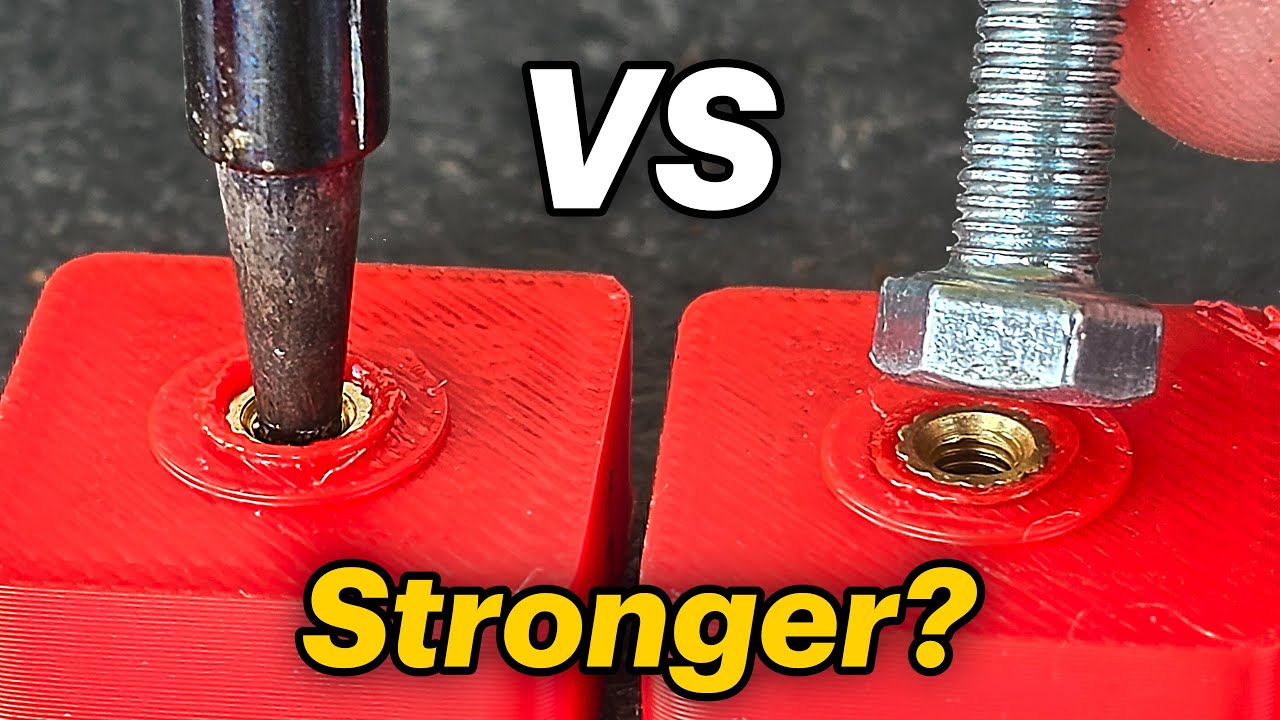
Even stronger Heat-Set Brass inserting method for 3D prints? Let's test it!
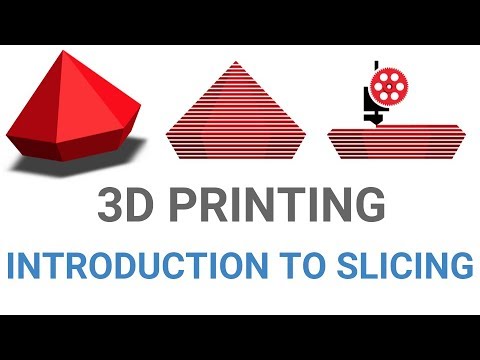
3D Printing - Introduction to Slicing
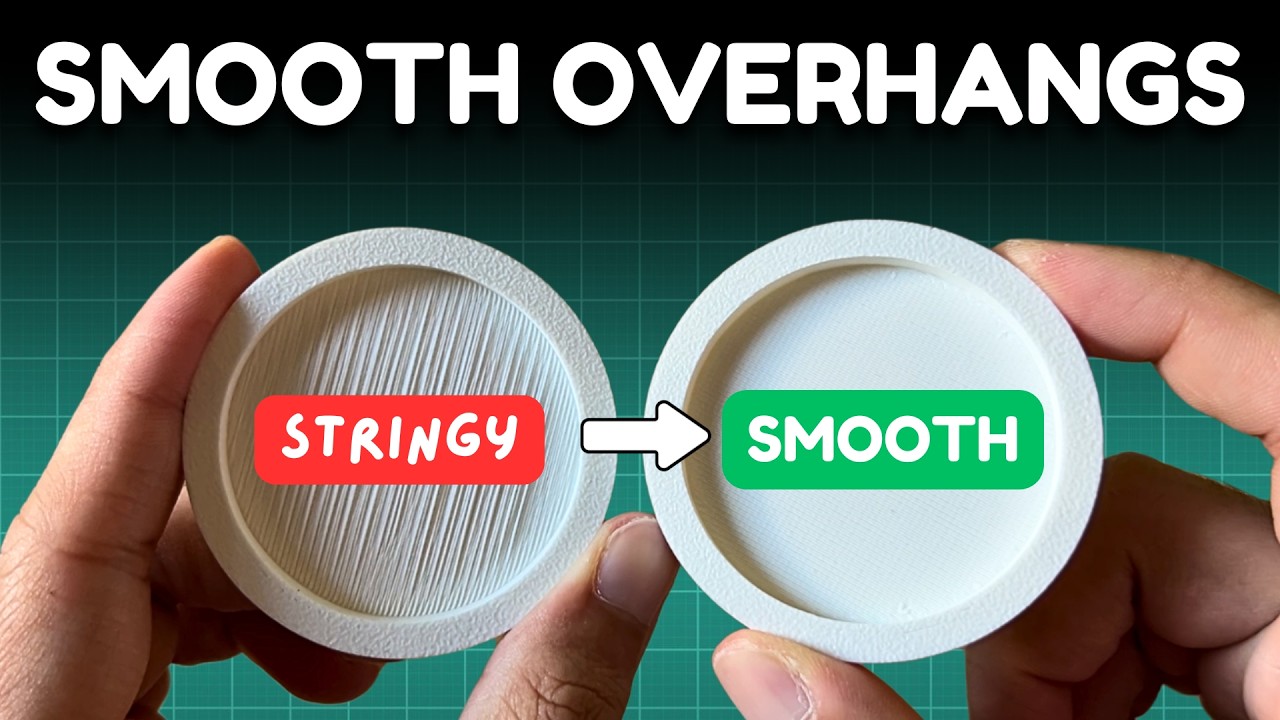
Best Slicer Settings For Printing Overhangs?
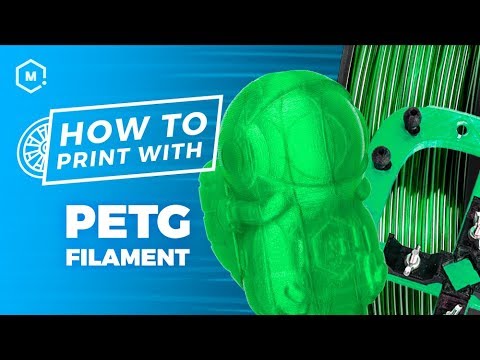
BEST TIPS FOR BETTER PRINTS WITH PETG | Everything you need to succeed with PETG filament

AnyCubic Tries Multicolor: The AnyCubic Kobra 3 Combo
5.0 / 5 (0 votes)