Conventional Press-and-Sinter Powder Metallurgy
Summary
TLDRThis video provides an in-depth overview of conventional press and sinter powder metallurgy (PM) technology. It explains the process from metal powder preparation through blending, compaction, and sintering, highlighting the significance of aspect ratio and density in determining mechanical properties. Key applications in automotive and electric motor industries are showcased, demonstrating how PM offers cost-effective solutions for high-tolerance parts. The video emphasizes the crucial role of sintering in enhancing particle bonds and achieving desired strength, making it a valuable resource for understanding the advantages of powder metallurgy.
Takeaways
- 🔍 Conventional press and center powder metallurgy (PM) uses metal powders that are compacted and then sintered to create various components.
- 🧪 The process begins with high-quality scrap metal being melted and atomized to form fine powders, which are then processed to remove oxidation.
- ⚙️ The blending of powders with lubricants and alloying materials is crucial for achieving the desired mechanical properties in the final product.
- 📏 Aspect ratio plays a significant role in the design of PM components, affecting density and mechanical properties. A higher aspect ratio can lead to lower density in certain areas.
- 🏗️ Compaction involves forming the powder into a 'green compact' within a closed die, with density being influenced by the pressing force and powder characteristics.
- 🔥 Sintering is the next step, where the compacted part is heated to high temperatures to create strong metallurgical bonds between the powder particles.
- ⚖️ The relationship between density and tensile strength is critical, with increased density generally resulting in higher tensile strength.
- 🧬 Different microstructures achieved through heat treatment (e.g., ferrite, pearlite, martensite) can significantly enhance the material's yield strength.
- 🚗 PM components are widely utilized in various industries, including automotive, hydraulics, and electric motors, due to their efficiency and cost-effectiveness.
- 🌍 Powder metallurgy is a globally recognized manufacturing technique that provides solutions for producing high-tolerance parts efficiently.
Q & A
What is conventional press and center technology in powder metallurgy?
-Conventional press and center technology involves molding metal powder through compaction in a closed die, creating green compacts that are then sintered and finished to produce various parts used in automotive, agricultural, and recreational applications.
What role does aspect ratio play in powder metallurgy?
-Aspect ratio refers to the proportions of a component's dimensions. It affects density and mechanical properties, as components with high aspect ratios may experience significant variations in density and, consequently, their mechanical properties.
How does the compaction process affect the density of powder metal components?
-During compaction, applying pressure to the metal powder decreases porosity and increases the area of contact between particles, thereby enhancing the density of the compacted part.
What is the significance of the neutral axis in compaction?
-The neutral axis is a density divide within a component, typically found in high aspect ratio parts. It has lower density than the ends, which can lead to variations in mechanical properties if not properly understood during design.
What processes occur after the compacting phase in powder metallurgy?
-After compaction, parts are sintered in a furnace, where strong metallurgical bonds form between the powder particles. This is followed by cooling and any necessary finishing steps.
What is the typical process of producing metal powders in conventional PM?
-Metal powders are typically produced through water atomization, where molten metal is atomized into powder using high-pressure water, followed by dewatering, annealing, and screening to prepare for blending and compacting.
What are the mechanical properties that depend on density in powder metallurgy?
-Density significantly influences mechanical properties such as tensile strength. Higher density usually corresponds to higher tensile strength and improved wear resistance in the final product.
How does sintering contribute to the properties of powder metal components?
-Sintering involves heating compacted powders in a protective atmosphere, allowing particles to bond together, which enhances the overall strength and stability of the components.
What types of materials are commonly used in powder metallurgy components?
-Common materials include iron, copper, and various alloys, with lubricants and other additives used to facilitate the compaction process and improve properties.
Can you provide examples of applications for powder metallurgy components?
-Applications include parts for automotive transmissions, electric motor components, and specialized parts in agricultural machinery, showcasing the versatility of powder metallurgy in various industries.
Outlines
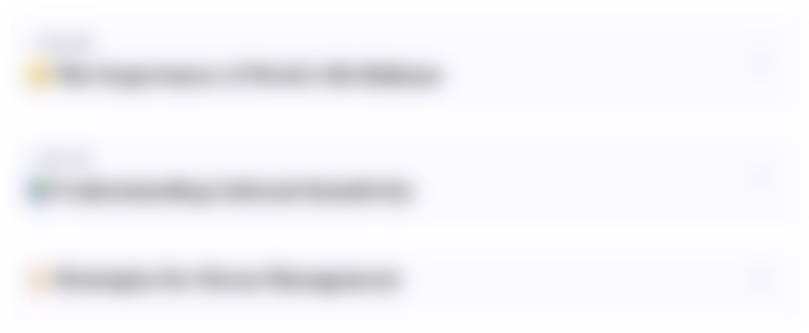
Esta sección está disponible solo para usuarios con suscripción. Por favor, mejora tu plan para acceder a esta parte.
Mejorar ahoraMindmap
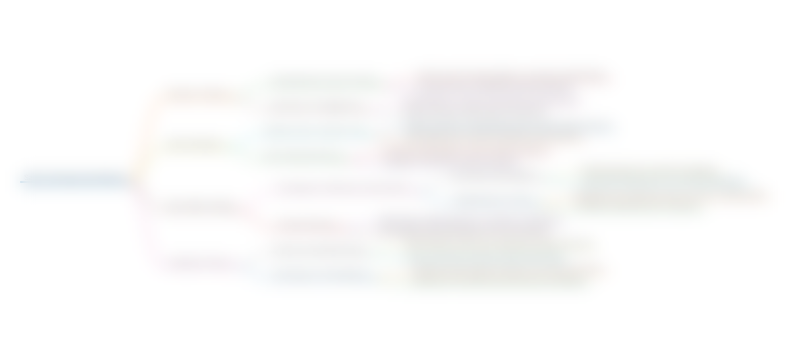
Esta sección está disponible solo para usuarios con suscripción. Por favor, mejora tu plan para acceder a esta parte.
Mejorar ahoraKeywords
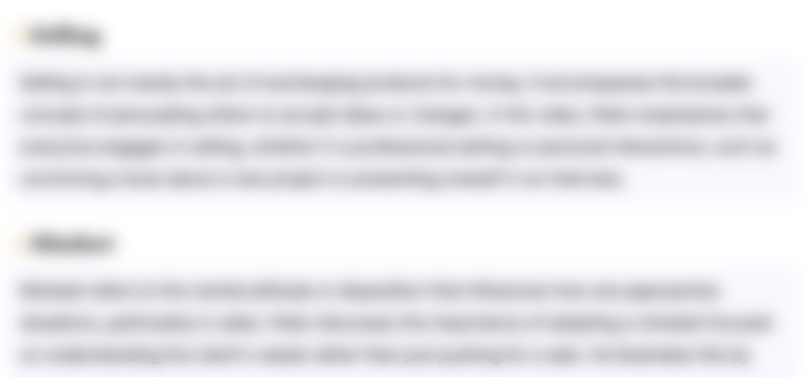
Esta sección está disponible solo para usuarios con suscripción. Por favor, mejora tu plan para acceder a esta parte.
Mejorar ahoraHighlights
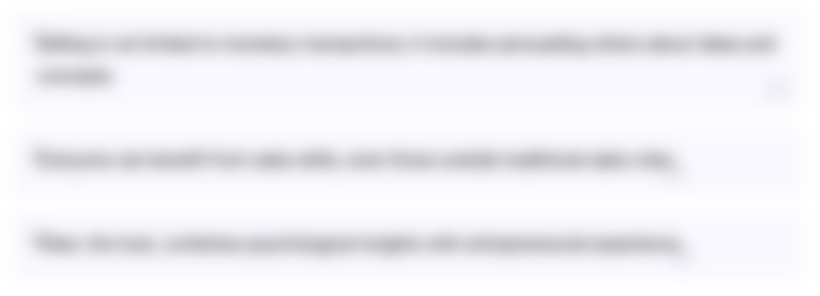
Esta sección está disponible solo para usuarios con suscripción. Por favor, mejora tu plan para acceder a esta parte.
Mejorar ahoraTranscripts
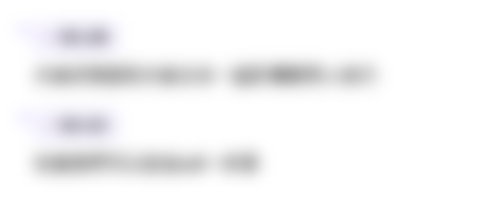
Esta sección está disponible solo para usuarios con suscripción. Por favor, mejora tu plan para acceder a esta parte.
Mejorar ahora5.0 / 5 (0 votes)