Powder Metallurgy Touches Your Life, Part 1
Summary
TLDRThis video highlights the significance of powder metallurgy (PM), a versatile and sustainable metal forming technology that touches various aspects of daily life. From manufacturing complex parts in automotive, defense, and healthcare industries, to producing high-quality components for consumer products, PM offers numerous advantages such as reduced waste, energy savings, and cost-effectiveness. The video explains various PM techniques, including press and sinter, powder injection molding, hot isostatic pressing, and others, showcasing their ability to create both small and large parts with precision and reliability while promoting environmentally friendly production methods.
Takeaways
- π Powder metallurgy (PM) is a versatile technology used in various industries to create metal components.
- π PM is found in everyday life, including in food production, transportation, healthcare, communication, and recreation.
- π The PM process begins with metal powders that are shaped under pressure and then heated to form solid components.
- π PM allows the creation of complex or unique metal parts that would be impossible or impractical with traditional manufacturing methods.
- π The PM process minimizes waste, reduces scrap, and improves material utilization, contributing to sustainability.
- π PM offers advantages such as improved part-to-part repeatability, long-term reliability, and cost-effectiveness, particularly in high-volume production.
- π Conventional PM (press and sinter) shapes metal powder in custom dies under high pressure, followed by sintering at controlled temperatures to finalize parts.
- π Powder injection molding (PIM) is ideal for producing small, complex parts using fine metal powders mixed with a binder.
- π Hot isostatic pressing (HIP) is used for large, complex parts, using high pressure and temperature to fully compact and densify the powder.
- π Other PM techniques include cold isostatic pressing, world compacting, and spray forming, each suited to different part requirements and sizes.
Q & A
What is powder metallurgy (PM)?
-Powder metallurgy (PM) is a technology used to produce metal components by shaping metal powders through the application of pressure and heat, resulting in finished components with specific metallurgical properties.
How does powder metallurgy impact our daily lives?
-Powder metallurgy touches various aspects of daily life, from manufacturing components used in transportation, electronics, healthcare, leisure activities, to defense, and energy sectors.
What are the primary advantages of using powder metallurgy for metal forming?
-The key advantages of powder metallurgy include the ability to create complex shapes, reduce machining and scrap, improve material yield, ensure repeatability, and offer cost-effective manufacturing for high-volume production.
How does powder metallurgy contribute to sustainability in manufacturing?
-Powder metallurgy contributes to sustainability by reducing energy consumption, minimizing waste through improved material utilization, recycling scrap, and offering longer product life due to the enhanced durability of components.
What is the process of conventional powder metallurgy?
-Conventional powder metallurgy, or press and sinter, involves shaping metal powders under pressure in custom dies to form 'green compacts,' which are then sintered in controlled atmospheres to achieve the desired metallurgical properties.
What is powder injection molding, and how does it differ from traditional powder metallurgy?
-Powder injection molding uses fine metal powders mixed with a binder to create complex shapes, typically in smaller parts. The binder is later removed, and the parts are sintered to achieve high density, whereas traditional powder metallurgy generally focuses on larger components and simpler shapes.
What is hot isostatic pressing (HIP) and how is it used in powder metallurgy?
-Hot isostatic pressing (HIP) involves enclosing metal powder in a custom container, applying high-pressure gas at elevated temperatures to compact and sinter the powder. This process is particularly useful for large parts with complex shapes.
What is the purpose of cold isostatic pressing in powder metallurgy?
-Cold isostatic pressing uses a liquid pressurizing medium to apply uniform pressure on metal powders at room temperature. This process is typically used for specific applications requiring particular material properties.
How does the world compact process work in powder metallurgy?
-The world compact process produces continuous strips or sheets of metal powder, which can then be used to fabricate thin, flat products like plates and sheets. It is an innovative method for manufacturing large quantities of thin, uniform products.
What are the key benefits of powder metallurgy in manufacturing?
-Powder metallurgy offers multiple benefits, including reduced energy consumption, improved material yield, design flexibility, enhanced component reliability, and cost-effectiveness, especially in moderate to high-volume production.
Outlines
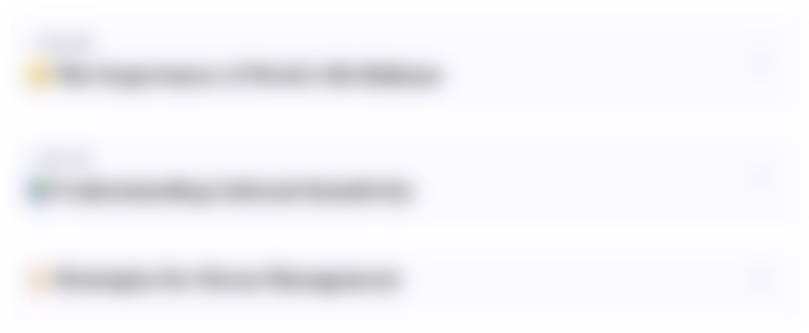
This section is available to paid users only. Please upgrade to access this part.
Upgrade NowMindmap
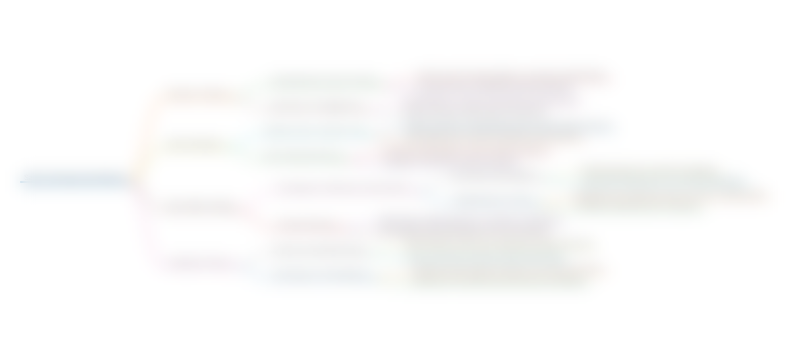
This section is available to paid users only. Please upgrade to access this part.
Upgrade NowKeywords
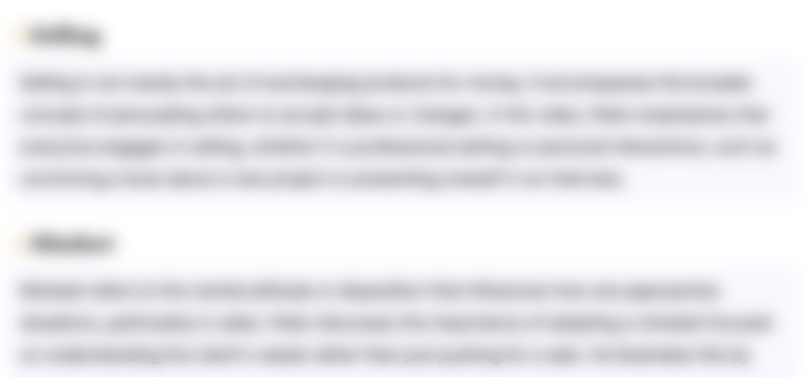
This section is available to paid users only. Please upgrade to access this part.
Upgrade NowHighlights
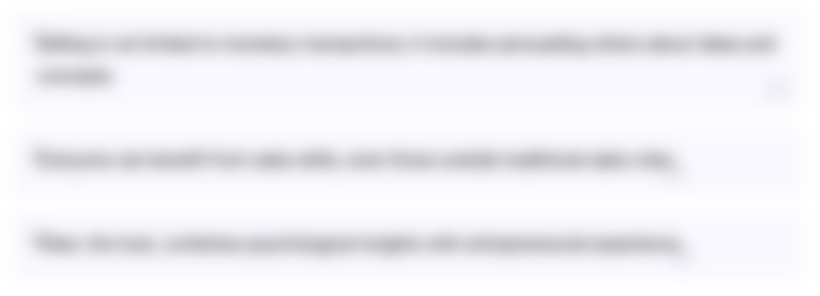
This section is available to paid users only. Please upgrade to access this part.
Upgrade NowTranscripts
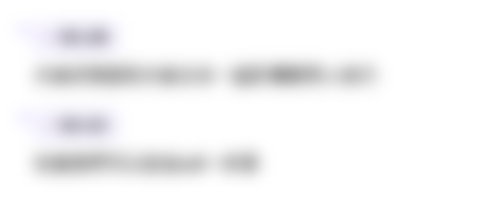
This section is available to paid users only. Please upgrade to access this part.
Upgrade Now5.0 / 5 (0 votes)