CNC Mill Tutorials - 5 - Drilling, Reaming, Tapping and Boring
Summary
TLDRIn this instructional video, viewers learn the process of drilling, tapping, and reaming in metalworking. The tutorial covers drilling five distinct holes, including a half-inch through hole, a reamed hole, a tapped hole for a 1/2-13 threaded bolt, a counterbored hole, and a countersunk hole. Key techniques such as center drilling, using cutting oil, and proper RPM settings are emphasized for precision and accuracy in machining.
Takeaways
- 🛠️ The video demonstrates how to drill, tap, and ream holes for various purposes.
- 🔩 It covers the process of drilling five different types of holes: a half-inch through hole, a reamed hole, a tapped hole for a threaded bolt, a counterbored hole, and a countersunk hole.
- 📏 The first hole is drilled using a half-inch drill bit, run at low range RPM with cutting oil for lubrication.
- 🔧 A reamed hole is prepared by initially drilling with a 31/64 inch bit, then reaming to achieve the exact size.
- 🗜️ The third hole is drilled to a depth of 3/4 inch and tapped for a 1/2-13 threaded bolt, using a 27/64 inch drill bit as per the tap reference chart.
- 🔩 Tapping is performed using a gun tap for starting threads and a bottoming tap to complete the threads to the bottom of the hole.
- 🔩 The process of tapping involves applying constant pressure, using cutting oil, and alternating between screwing in and backing out to clear chips.
- 🔩 A counterbored hole is drilled by first drilling a half-inch through hole and then raising the knee to achieve the desired counterbore depth.
- 🔩 A countersink is added to a 3/8-inch through hole using an 82-degree countersink bit, ensuring proper alignment with a bottom guide pin.
- 🛠️ The process emphasizes the importance of using cutting oil, maintaining proper pressure, and checking the accuracy of the work with the actual bolt or screw.
Q & A
How many holes are planned to be drilled in the video?
-Five holes are planned to be drilled.
What is the size of the first hole to be drilled?
-The first hole is a half-inch through hole.
What is the purpose of reaming a hole?
-Reaming is used to bring a hole to an exact size, which is why a 31/64 drill bit is used before reaming the second hole.
What is the depth of the hole that is tapped for a 1/2-13 threaded bolt?
-The depth of the hole for the 1/2-13 threaded bolt is 3/4 inch.
What size drill bit is used for the hole that will be tapped for a 1/2-13 threaded bolt?
-A 27/64 drill bit is used for the hole that will be tapped for a 1/2-13 threaded bolt.
Why is a counterbore performed on the half-inch through hole?
-A counterbore is performed to create a flat surface around the hole to allow a bolt head to sit flush.
What is the purpose of using a center drill before drilling the actual holes?
-Center drilling acts as a pilot to prevent larger drill bits from wobbling or walking on the surface.
What is the significance of the scratch marks being inconsistent on the forward hole?
-Inconsistent scratch marks on the forward hole indicate that the hole may not be as accurate as the reamed hole, which appears shiny and more accurate.
What are the two types of taps used in the video?
-The two types of taps used are the gun tap, which is more aggressive for starting threads, and the bottoming tap, which allows threads to reach the bottom of the hole.
How is cutting oil applied during the tapping process?
-Cutting oil is applied before the tapping process begins and is used throughout to ensure smooth operation and reduce friction.
What is the purpose of the bottom guide pin on the counterbore bit?
-The bottom guide pin on the counterbore bit ensures proper alignment during the counterboring process.
How is the depth checked during the countersinking process?
-The depth during the countersinking process is checked by going down a certain depth, checking it with the bolt, and then iterating until it is fine and within tolerance.
Outlines
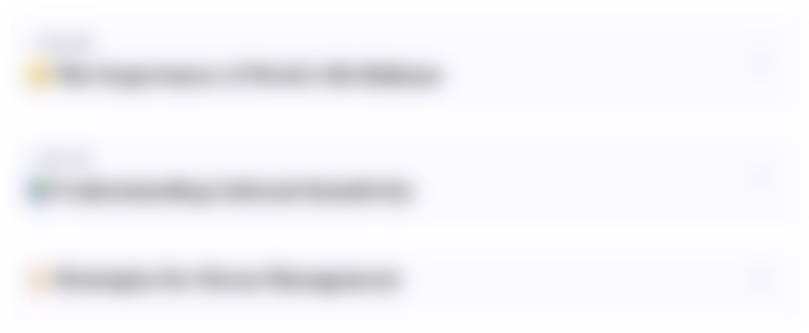
Esta sección está disponible solo para usuarios con suscripción. Por favor, mejora tu plan para acceder a esta parte.
Mejorar ahoraMindmap
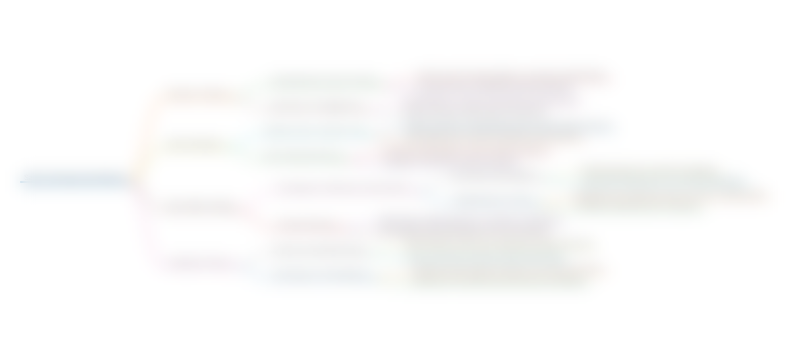
Esta sección está disponible solo para usuarios con suscripción. Por favor, mejora tu plan para acceder a esta parte.
Mejorar ahoraKeywords
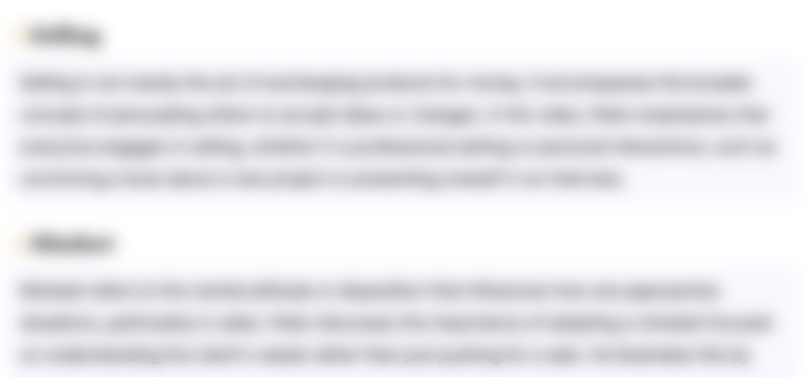
Esta sección está disponible solo para usuarios con suscripción. Por favor, mejora tu plan para acceder a esta parte.
Mejorar ahoraHighlights
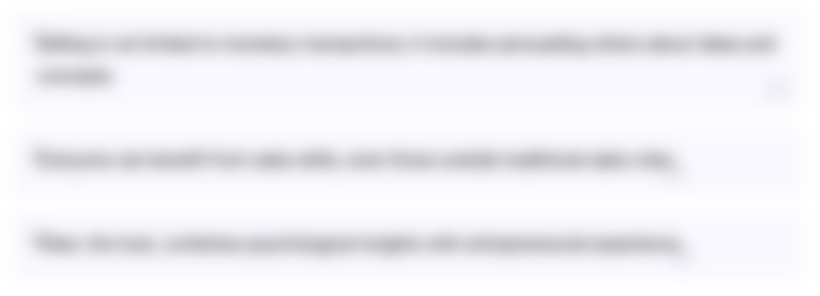
Esta sección está disponible solo para usuarios con suscripción. Por favor, mejora tu plan para acceder a esta parte.
Mejorar ahoraTranscripts
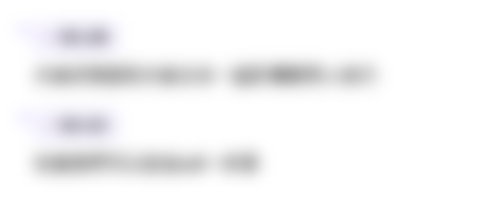
Esta sección está disponible solo para usuarios con suscripción. Por favor, mejora tu plan para acceder a esta parte.
Mejorar ahora5.0 / 5 (0 votes)