Drilling Machine Operations: Boring, Reaming, Counter Sinking, Spot Facing, Tapping | Shubham Kola
Summary
TLDRThis session covers various drilling machine operations, including drilling, reaming, boring, counter sinking, counter boring, spot facing, and tapping. Drilling creates cylindrical holes, while boring refines and corrects the size and roundness of pre-existing holes. Reaming smooths and sizes holes post-drilling. Spot facing creates a flat surface for fasteners. Tapping creates internal threads, and counterboring enlarges hole ends cylindrically. Countersinking forms a conical enlargement at the hole's end, with tools featuring multiple cutting edges.
Takeaways
- 🔩 Drilling operation involves creating a cylindrical hole by rotating a cutting tool called a drill, which leaves a rough internal surface and results in a hole slightly larger than the drill size.
- 📏 Boring operation is used to increase the diameter of an existing hole, often to correct its roundness and finish the internal surface, using a single-edged boring tool placed in a tapered boring bar.
- 🔧 Spot Facing operation is performed to produce a flat surface at the top of a drilled hole for seating bolt heads, washers, or nuts, aiming to achieve a high surface finish.
- 🔨 Tapping operation uses a tap as a cutting tool to create internal threads that match the size of external threads, which can be done manually or with external power.
- ⚒ Counterboring operation enlarges the end of a hole cylindrically, using a counterbore tool with cutting edges that may be straight or spiral, typically at a slower speed than drilling.
- 🔧 Reaming operation refines the size and finish of a hole after the initial drilling process, using a reamer, which is a multi-point cutting tool.
- 🔩 Countersinking operation creates a conical enlargement at the end of a hole, with the countersink tool featuring multiple cutting edges on its conical surface, and the included angle of the cone ranging from 60 to 90 degrees.
- 🛠 The speed of spindle in boring is less than that in reaming, indicating a slower process for achieving the desired hole finish.
- 🔗 Tapping can be performed by hand or with external power, demonstrating flexibility in the operation depending on the application and available equipment.
- 🔧 Reaming is essential for achieving the desired hole size and improving the internal surface finish, especially after the initial drilling process which often leaves an imperfect hole.
Q & A
What is the primary purpose of a drilling operation?
-The primary purpose of a drilling operation is to produce a cylindrical hole inside a workpiece by rotating the cutting edge of a tool called a drill.
Why is the internal surface of a hole usually rough after drilling?
-The internal surface of a hole is usually rough after drilling because the process involves the rapid removal of material by the rotating drill, which can leave behind an uneven surface.
What is the difference between drilling and boring operations?
-Drilling creates a hole in the workpiece, while boring is used to increase the diameter of an existing hole, often to improve its surface finish and correct its roundness.
How does the boring tool differ from a drill?
-The boring tool has only one cutting edge and is placed in a boring bar with a tapered shank, unlike a drill which is used for initial hole creation.
What is the purpose of spot facing operation?
-Spot facing is used to produce a flat seat for bolt heads, washers, or nuts at the opening of a drilled hole, providing a high surface finish at the top of the hole.
What is the function of a tap in a tapping operation?
-A tap is used in a tapping operation to create internal threads that can mate with external threads of identical size, effectively cutting threads into the hole.
Can tapping be performed manually or does it require external power?
-Tapping can be performed manually, but it can also be done using external power for increased efficiency and precision.
What is the primary goal of a counterboring operation?
-The primary goal of a counterboring operation is to enlarge the end of a hole cylindrically, using a counterbore tool with cutting edges that may be straight or spiral.
Why is the cutting speed in counterboring usually slower than drilling?
-The cutting speed in counterboring is usually slower than drilling because it is a precision operation that requires careful control to avoid damaging the workpiece, with speeds typically being around 25% smaller.
What is the main objective of reaming operation?
-Reaming is done to obtain the desired size of a hole and to finish the internal surface properly, using a reamer which is a multi-point cutting tool.
How does countersinking operation differ from other hole enlargement operations?
-Countersinking operation differs from other hole enlargement operations by creating a conical-shaped enlargement at the end of a hole, with the countersink tool having multiple cutting edges on its conical surface.
Outlines
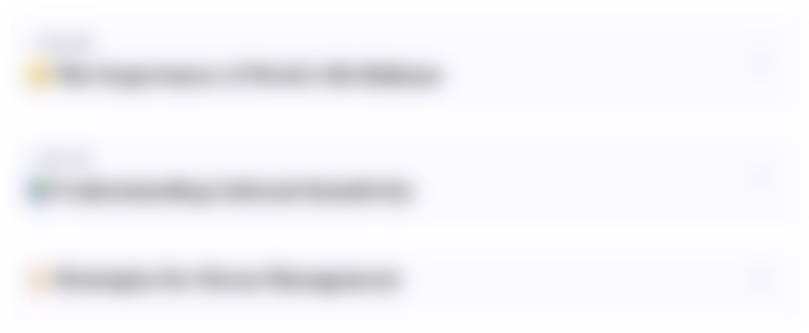
This section is available to paid users only. Please upgrade to access this part.
Upgrade NowMindmap
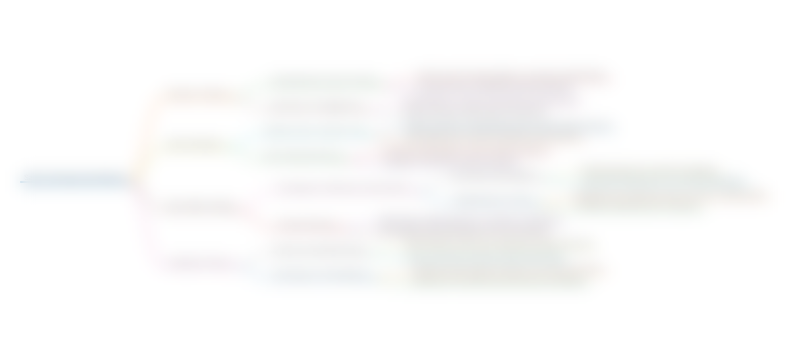
This section is available to paid users only. Please upgrade to access this part.
Upgrade NowKeywords
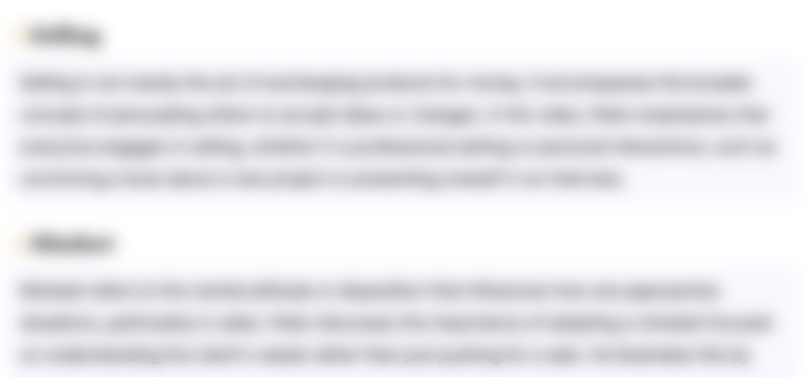
This section is available to paid users only. Please upgrade to access this part.
Upgrade NowHighlights
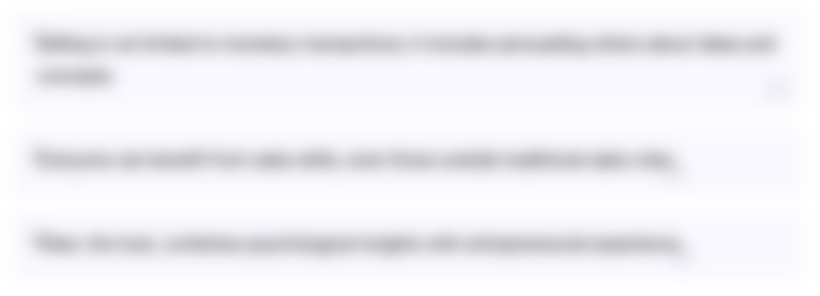
This section is available to paid users only. Please upgrade to access this part.
Upgrade NowTranscripts
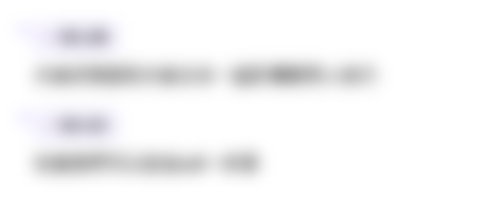
This section is available to paid users only. Please upgrade to access this part.
Upgrade NowBrowse More Related Video

All Lathe Machine Operations: Turning, Facing, Taper Turning, Boring, Knurling, Tapping, Forming
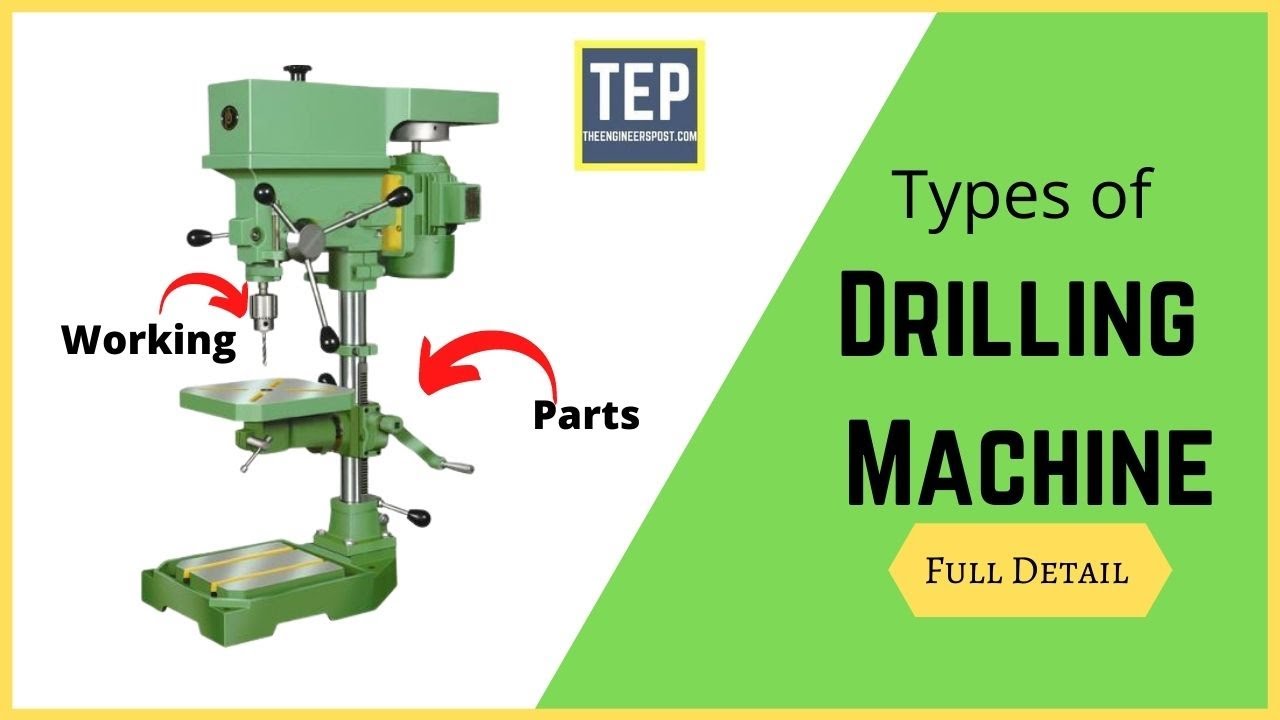
Drilling machine: Types, Parts, Operations, Working Principle, (Explained in detail)
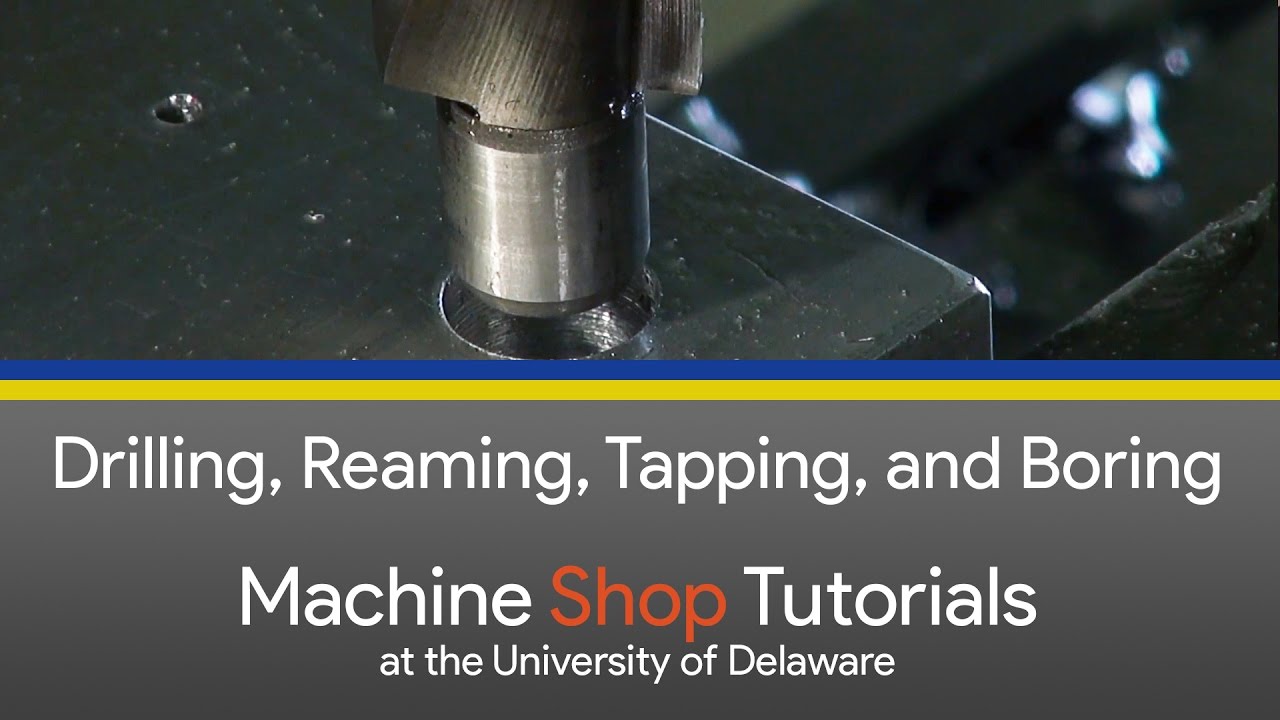
CNC Mill Tutorials - 5 - Drilling, Reaming, Tapping and Boring
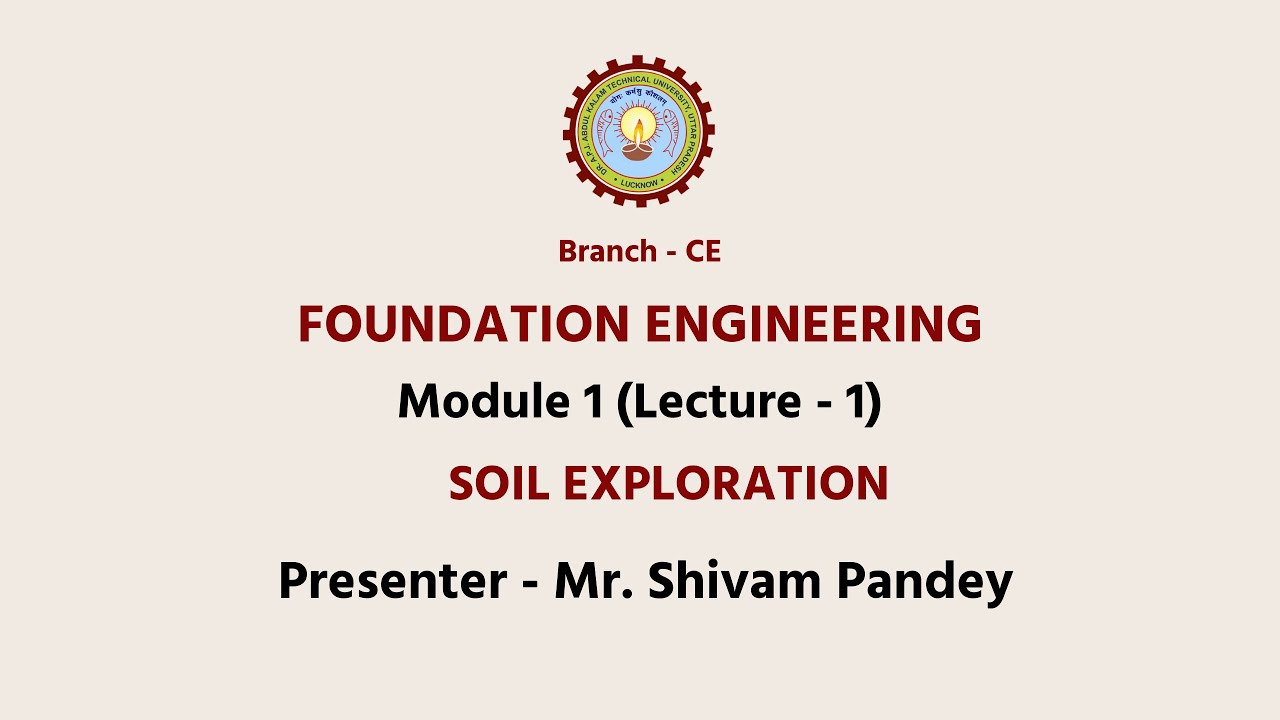
Foundation Engineering | Soil Exploration | AKTU Digital Education
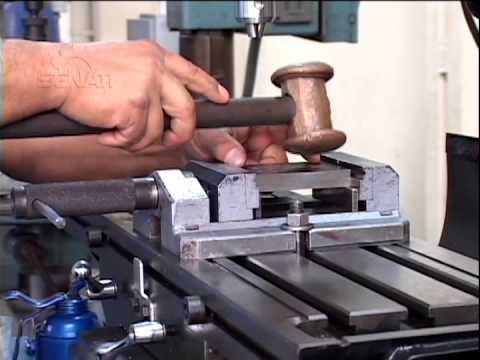
Taladrado

Benchwork and Layout part 1
5.0 / 5 (0 votes)