Tableting Granulation - How it works
Summary
TLDRThis video from LFA explores granulation in pharmaceutical tablet production, highlighting three key reasons: improving flowability, compressibility, and API distribution. It explains the angle of repose test for assessing flowability and the option of direct compression for sensitive APIs. The video delves into dry and wet granulation methods, including slugging, roller compaction, and fluid bed granulation, emphasizing the importance of milling for granule size standardization. It concludes with the addition of lubricants for easier tablet pressing and offers resources for further information.
Takeaways
- 🌟 Granulation is a process used to improve the flowability, compressibility, and uniform distribution of the active pharmaceutical ingredient (API) in a formulation.
- 📏 The angle of repose is a key test to determine the flowability of a powder; a low angle indicates good flowability, while a high angle suggests the need for granulation.
- 💊 Direct compression is a cost-efficient method for tableting where a formulation can be compressed without granulation, suitable for heat and moisture-sensitive APIs.
- 🔄 Mix validation is crucial to ensure the correct and consistent mixing of the tablet formulation, especially when direct compression is used.
- 🌡️ Dry granulation is preferred when a formulation is sensitive to moisture or heat, and it involves combining granules without the need for any liquid.
- 🔩 Slugging is a technique where large tablets are formed and then granulated to improve flowability before final compression.
- 🌀 Roller compaction is a method where a formulation is compacted into a ribbon by rollers and then granulated to create the desired granule size.
- 💧 Wet granulation involves the use of a binder in a liquid solution or suspension to cause aggregation of particles and improve flowability.
- 🌬️ Fluid bed granulation is a form of wet granulation where hot air and binder spraying within a unit help form granules by creating bridges between particles.
- ⚙️ After granulation, milling is necessary to standardize the granule size distribution, and lubricants are added to facilitate easier flow through the tablet press.
Q & A
What are the three main reasons for granulation in pharmaceutical formulation?
-The three main reasons for granulation in pharmaceutical formulation are to improve the flowability of the formulation, to make the formulation more compressible, and to ensure a consistent spread of the active pharmaceutical ingredient (API) throughout the formulation.
How can you test the flowability of a tablet formulation?
-The flowability of a tablet formulation can be tested by measuring the angle of repose. A small angle indicates good flowability, which is suitable for direct compression, while a high angle suggests that granulation is needed as the formulation may not flow well and could cause issues like arching, bridging, or rat holing during tablet compression.
What is direct compression in tableting and why is it cost-efficient?
-Direct compression in tableting is a process where the API and excipients are mixed and then directly compressed into tablets without any further steps like granulation. It is cost-efficient because it simplifies the manufacturing process, reducing the need for additional equipment and steps, and is also suitable for sensitive APIs that may be affected by heat and moisture.
Why is mix validation important in tablet formulation?
-Mix validation is important in tablet formulation to ensure that the API and other components have been mixed correctly and uniformly. This prevents issues like segregation and ensures consistent dosage and quality of the final product.
What is dry granulation and when is it used?
-Dry granulation is a process that combines granules without the need for any liquid. It is generally used when the formulation is sensitive to moisture or heat, as it avoids the use of solvents that could degrade the API or cause other issues.
What is slugging and how does it relate to dry granulation?
-Slugging is a process where a tablet press is used to form large tablets that vary in weight due to poor flowability of the formulation. These 'slugs' are then passed through a granulator to break them down into granules, which are then compressed again to form the final tablets. This is related to dry granulation as it is an alternative method to improve the flowability of the formulation.
What is roller compaction and how does it differ from other granulation methods?
-Roller compaction is a process where the formulation is fed through a roller compactor, where two rollers compact the powder to form a ribbon. This ribbon then passes through a granulator where it is forced against a mesh to create granules of the desired size. It differs from other granulation methods as it uses mechanical pressure to form the ribbon before granulation, and it's often used for formulations that are sensitive to the addition of liquids.
How does wet granulation work and what is its purpose?
-Wet granulation involves the use of an adhesive, often a binder, which is incorporated into the formulation as a solution or suspension in a suitable liquid. The purpose of wet granulation is to cause aggregation of particles, forming solid bridges between them to create granules of a consistent size. This process is popular as it is applicable to most formulations and can improve the flowability and compressibility of the final product.
What is the role of a fluid bed granulator in wet granulation?
-A fluid bed granulator is used in wet granulation to facilitate the binding of granules. Hot air is fed into the bed, lifting the granules while they are sprayed with the binder solution. This causes the granules to bind together, forming bridges between them. The fluid bed granulator allows for a controlled environment where the granulation process can be easily monitored and adjusted.
Why is milling necessary after granulation?
-Milling is necessary after granulation to break down large granules and create a standardized granule distribution. This ensures uniformity in the final product, which is important for consistent tablet weight and dissolution properties.
What is the purpose of adding a lubricant after the granulation process?
-The purpose of adding a lubricant after the granulation process is to coat the final granules. This coating allows the formulation to flow more easily through the tablet press, reducing friction and preventing the tablets from sticking to the press or each other.
Outlines
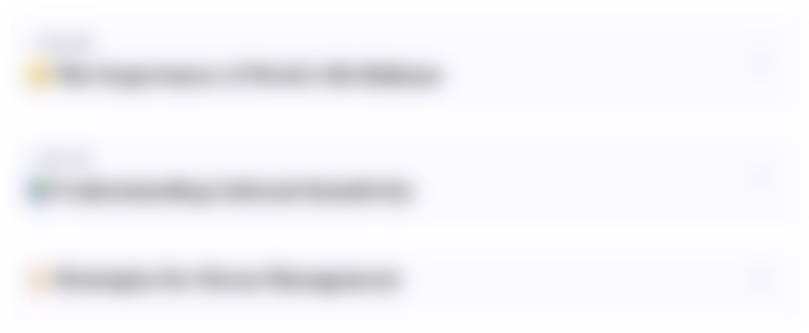
Esta sección está disponible solo para usuarios con suscripción. Por favor, mejora tu plan para acceder a esta parte.
Mejorar ahoraMindmap
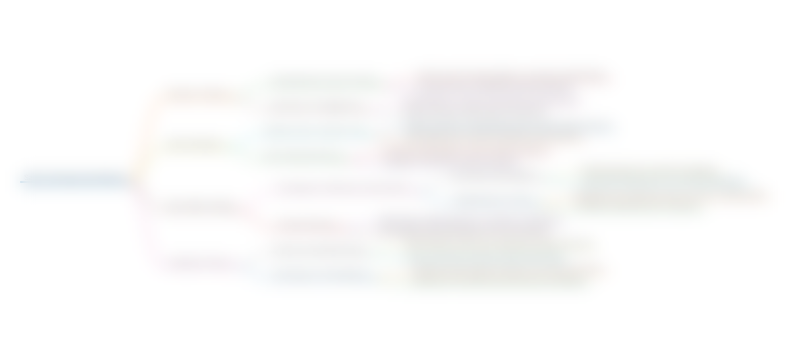
Esta sección está disponible solo para usuarios con suscripción. Por favor, mejora tu plan para acceder a esta parte.
Mejorar ahoraKeywords
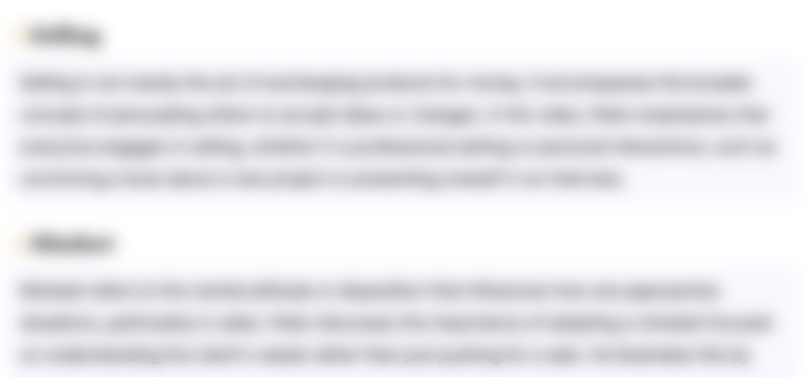
Esta sección está disponible solo para usuarios con suscripción. Por favor, mejora tu plan para acceder a esta parte.
Mejorar ahoraHighlights
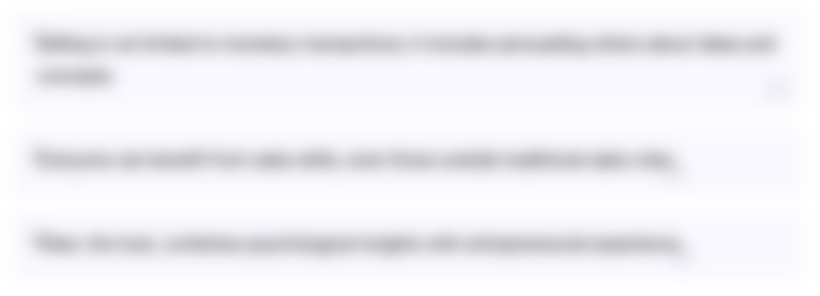
Esta sección está disponible solo para usuarios con suscripción. Por favor, mejora tu plan para acceder a esta parte.
Mejorar ahoraTranscripts
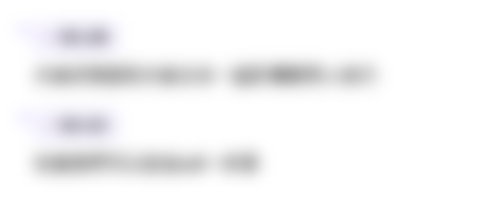
Esta sección está disponible solo para usuarios con suscripción. Por favor, mejora tu plan para acceder a esta parte.
Mejorar ahora5.0 / 5 (0 votes)