Granulation – In process checks in Pharmaceutical industry l LOD l Interview Question and answers
Summary
TLDRThis video provides a comprehensive overview of the key in-process checks in the granulation process within pharmaceutical manufacturing. It covers essential aspects like moisture content analysis, particle size distribution, bulk density, granule hardness, and flowability, among others. The script also explores techniques such as tap density measurement, binder content verification, and pH measurement of the granulation mix. The importance of these tests for maintaining product quality, stability, and regulatory compliance is emphasized. This knowledge is crucial for ensuring efficient, reproducible granulation, ultimately leading to better tablet manufacturing and drug efficacy.
Takeaways
- 😀 Moisture content analysis, particle size distribution, and bulk density testing are crucial checks in the granulation process.
- 😀 The frequency of in-process checks during granulation depends on product development and established procedures, typically every 30 minutes to hourly.
- 😀 Loss on drying (LOD) is measured by comparing the weight of a sample before and after drying to determine moisture content.
- 😀 Granulation endpoint is determined by monitoring parameters such as granule size, moisture content, and appearance.
- 😀 Particle size distribution impacts compressibility, tablet hardness, and dissolution rates, influencing overall product quality.
- 😀 Granule flowability is assessed using methods like the Carr Index and Hausner ratio, which depend on granule size, shape, and moisture content.
- 😀 Visual inspection of granules includes assessing their size, shape, color, and any agglomerates, which affect product quality.
- 😀 Binder content verification and pH measurement of the granulation mix are important to ensure proper formulation and stability.
- 😀 Over granulation can cause poor flowability, increased dust formation, and difficulties in downstream processing, such as tablet compression.
- 😀 In-process testing in granulation ensures adherence to good manufacturing practices, regulatory requirements, and overall product efficiency and reproducibility.
Q & A
What are the key in-process checks performed during the granulation process?
-The key in-process checks during granulation include moisture content analysis, particle size distribution, bulk density testing, tap density measurement, granule hardness assessment, granulation endpoint determination, granule flowability analysis, binder content verification, pH measurement of the granulation mix, and visual inspection of granule characteristics.
Why is moisture content analysis important in the granulation process?
-Moisture content analysis is crucial because it ensures that the granules have the correct moisture level for proper cohesion and flowability. If moisture content is too high or low, it can affect granule formation, lead to over- or under-granulation, and impact the final product quality.
How is moisture content, or loss on drying (LOD), measured during granulation?
-Moisture content is measured by weighing a sample before and after drying, with the weight difference representing the moisture lost. The formula for calculating LOD is: (Initial weight - Final weight) / Initial weight × 100.
What is the typical acceptable moisture range in granulation processes?
-The typical acceptable moisture range for granulation processes is between 1% and 4%. This range may vary depending on the specific formulation and product requirements.
What impact does bulk density have on the granulation process?
-Bulk density affects the compressibility of granules during tableting. Variations in bulk density can lead to inconsistent tablet hardness and disintegration rates, affecting the final product’s quality.
How is tap density measured, and what equipment is used?
-Tap density is measured by tapping a container filled with granules until the volume change stabilizes. The common equipment used for this measurement includes tap density testers.
What factors can lead to fluctuations in bulk density during granulation?
-Factors that can cause fluctuations in bulk density include variations in granule size, moisture content, and the presence of fines or agglomerates.
Why is controlling particle size distribution important in granulation?
-Particle size distribution influences the compressibility of granules and the tablet's dissolution profile. Smaller particles generally lead to better packing and faster dissolution, affecting bioavailability and tablet performance.
How is granule flowability typically evaluated during granulation?
-Granule flowability is typically evaluated using techniques such as the Carr Index and Hausner Ratio, which measure the powder’s flow properties based on bulk density and tap density.
Why is it important to monitor the granulation endpoint?
-Monitoring the granulation endpoint ensures that granules reach the desired size and cohesion. Over-granulation can lead to excessive particle size reduction, poor flowability, and difficulties in downstream processes like compression.
Outlines
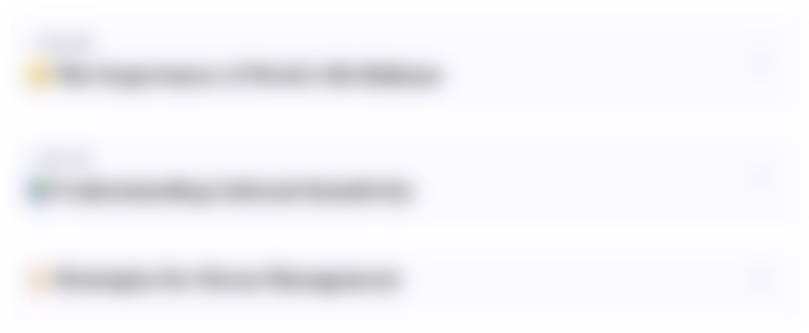
This section is available to paid users only. Please upgrade to access this part.
Upgrade NowMindmap
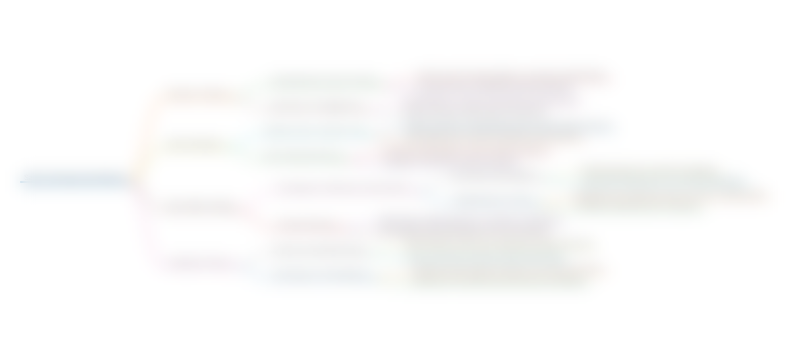
This section is available to paid users only. Please upgrade to access this part.
Upgrade NowKeywords
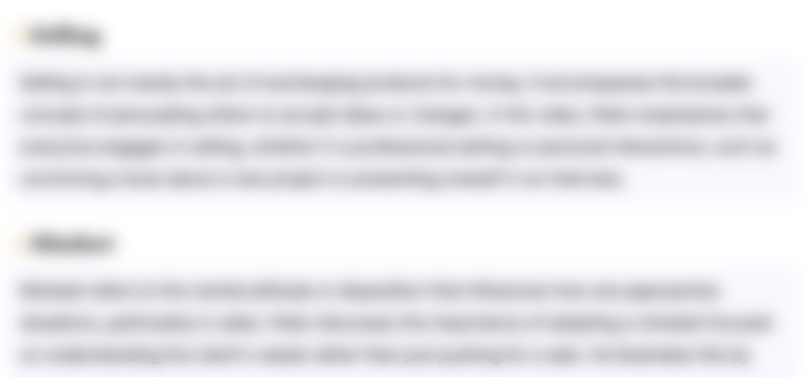
This section is available to paid users only. Please upgrade to access this part.
Upgrade NowHighlights
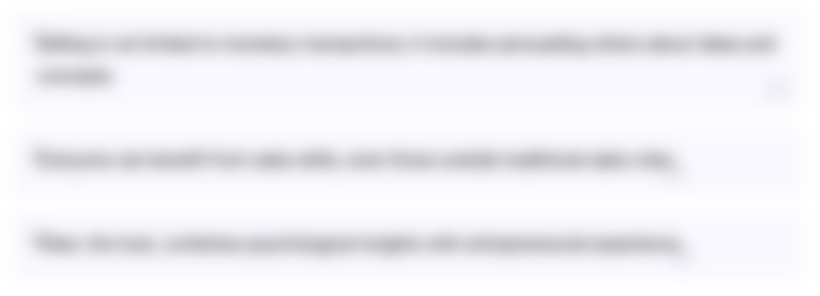
This section is available to paid users only. Please upgrade to access this part.
Upgrade NowTranscripts
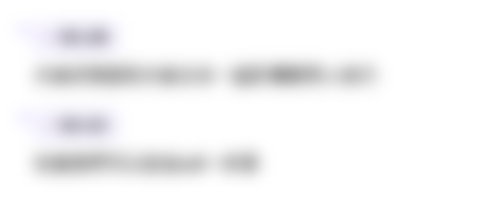
This section is available to paid users only. Please upgrade to access this part.
Upgrade NowBrowse More Related Video
5.0 / 5 (0 votes)