Electrochemical Grinding Process | How electrochemical grinding works
Summary
TLDRElectrochemical grinding is a hybrid machining process that combines traditional grinding with electrochemical machining to remove material through both abrasive action and chemical reaction. Utilizing a DC power supply, electrolyte tank, and a circulating system, it operates with the workpiece as an anode and the grinding wheel as a cathode. This process excels in grinding thin materials, such as turbine blades and tungsten carbide tool bits, without burrs or thermal distortion. However, it requires conductive materials and can be costly due to corrosive electrolytes and maintenance. This technique offers precision and efficiency, making it ideal for machining tough materials like stainless steel and high alloy steel.
Takeaways
- 🔌 Electrochemical grinding is a non-traditional machining process that combines elements of traditional grinding with electrochemical machining.
- 🛠️ The process requires a DC power supply, electrolyte tank, reservoir, electrolyte circulating system, nozzle, and grinding wheel, with the workpiece as an anode and the grinding wheel as a cathode.
- 💧 Common electrolytes used include sodium nitrate, sodium chloride, and potassium nitrate, which are fed at the machining interface through a nozzle to establish an electrical connection.
- 🚫 There is no direct contact between the wheel and the workpiece; only the abrasive particles from the grinding wheel make contact, maintaining a gap filled with electrolyte.
- 🛑 The grinding wheel facilitates the flow of electrolyte past the workpiece, removing material through the combined action of abrasive and chemical reaction.
- 🔧 Applications of electrochemical grinding include grinding turbine blades, sharpening hypodermic needles, grinding tungsten carbide tool bits, and working with thin-walled tubes, cemented carbide, and refractory materials.
- ✂️ It is particularly useful for grinding very thin materials without causing damage, which would occur with traditional grinding methods.
- 🔄 The process results in burr-free, heat-free machining with no hardening or cracking of the workpiece, and requires less frequent dressing of the grinding wheel.
- 🚀 Faster than traditional grinding for tough materials, electrochemical grinding offers efficiency and precision.
- ⚠️ However, it requires that both the wheel and the workpiece be good conductors of electricity, and the electrolyte can be corrosive.
- 💰 The process may not be economical for soft materials and involves high preventive maintenance costs.
Q & A
What is electrochemical grinding?
-Electrochemical grinding is a non-traditional machining process that combines elements of traditional grinding with electrochemical machining. It involves the removal of material through both mechanical abrasion by a grinding wheel and a chemical reaction.
How is electrochemical grinding different from traditional grinding?
-Unlike traditional grinding, electrochemical grinding does not involve direct contact between the grinding wheel and the workpiece. The workpiece material is removed by the abrasive particles in the electrolyte solution, which flows past the workpiece.
What are the key components required for electrochemical grinding?
-The essential components for electrochemical grinding include a DC power supply, an electrolyte tank, a reservoir electrolyte circulating system, a nozzle, a grinding wheel, and a working setup where the workpiece acts as an anode and the grinding wheel as a cathode.
What role does the electrolyte play in electrochemical grinding?
-The electrolyte, typically composed of sodium nitrate, sodium chloride, or potassium nitrate, forms an electric connection between the cathode (grinding wheel) and the anode (workpiece). It is fed at the machining interface and facilitates the removal of material through a chemical reaction.
How is the electrolyte applied in the electrochemical grinding process?
-The electrolyte is generally fed at the machining interface between the workpiece and the grinding wheel through a nozzle. It fills the gap between the wheel and the workpiece, allowing the abrasive particles to come in contact with the workpiece.
What are some applications of electrochemical grinding?
-Electrochemical grinding is used for grinding turbine blades, sharpening hypodermic needles, grinding tungsten carbide tool bits, grinding cutting tools, and processing thin-walled tubes, cemented carbide, refractory materials, stainless steel, and high alloy steel.
What are the advantages of using electrochemical grinding over traditional grinding?
-Advantages include the ability to grind very thin materials without damage, burr-free machining, no hardening or cracking of the workpiece, less frequent dressing of the grinding wheel, no heat generation, and thus no thermal distortion of the workpiece. It is also faster for grinding tough materials.
What are the disadvantages of electrochemical grinding?
-Disadvantages include the requirement for both the wheel and the workpiece to be good conductors of electricity, potential corrosive effects of the electrolyte on the tool and workpiece, and the process being uneconomical for soft materials. Additionally, preventive maintenance costs can be high.
What is the significance of maintaining a gap of 0.025 millimeters in electrochemical grinding?
-The gap of 0.025 millimeters is maintained to ensure that only the insulating abrasive particles from the grinding wheel come in contact with the workpiece, facilitating the removal of material without direct contact between the wheel and the workpiece.
How does the electrochemical grinding process affect the surface finish of the workpiece?
-The process results in a burr-free surface finish and avoids hardening and cracking of the workpiece, which are common issues with traditional grinding methods.
Why is electrochemical grinding considered faster than traditional grinding for tough materials?
-Electrochemical grinding is faster for tough materials because the chemical reaction in the electrolyte solution aids in the material removal process, reducing the reliance solely on mechanical abrasion.
Outlines
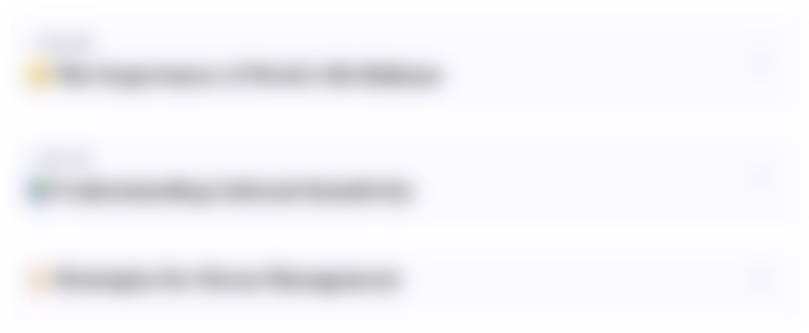
Dieser Bereich ist nur für Premium-Benutzer verfügbar. Bitte führen Sie ein Upgrade durch, um auf diesen Abschnitt zuzugreifen.
Upgrade durchführenMindmap
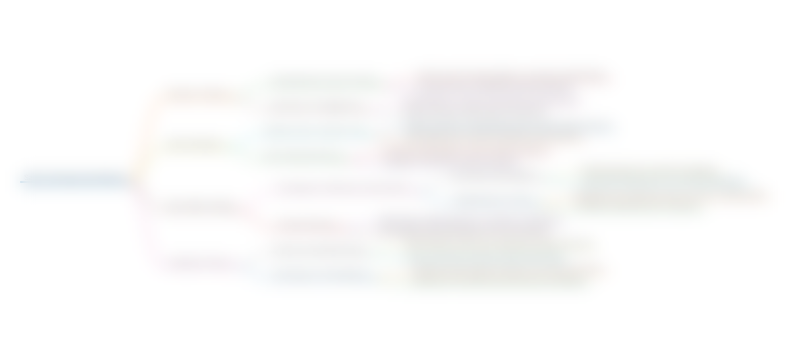
Dieser Bereich ist nur für Premium-Benutzer verfügbar. Bitte führen Sie ein Upgrade durch, um auf diesen Abschnitt zuzugreifen.
Upgrade durchführenKeywords
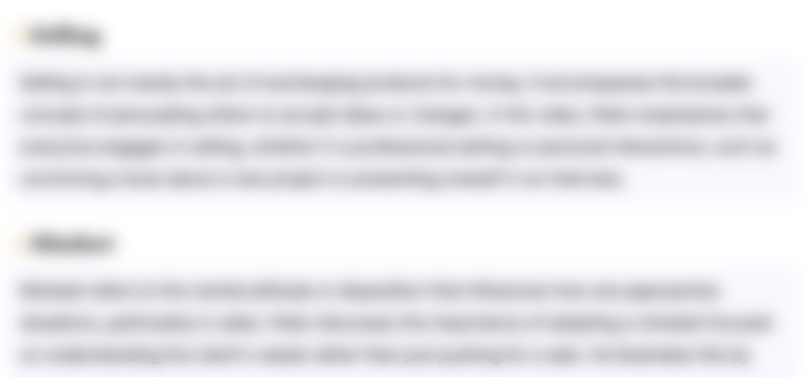
Dieser Bereich ist nur für Premium-Benutzer verfügbar. Bitte führen Sie ein Upgrade durch, um auf diesen Abschnitt zuzugreifen.
Upgrade durchführenHighlights
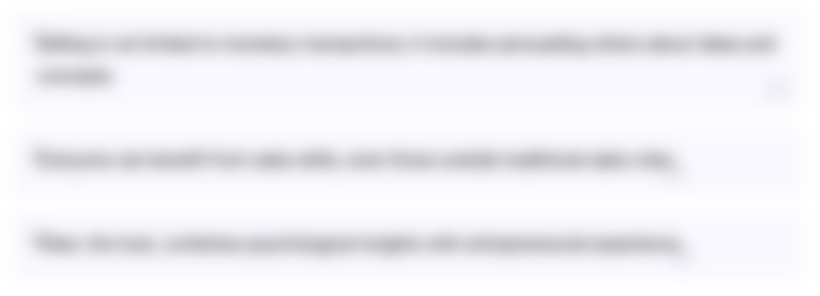
Dieser Bereich ist nur für Premium-Benutzer verfügbar. Bitte führen Sie ein Upgrade durch, um auf diesen Abschnitt zuzugreifen.
Upgrade durchführenTranscripts
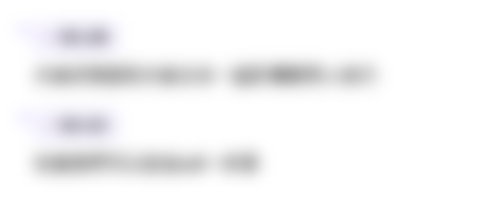
Dieser Bereich ist nur für Premium-Benutzer verfügbar. Bitte führen Sie ein Upgrade durch, um auf diesen Abschnitt zuzugreifen.
Upgrade durchführenWeitere ähnliche Videos ansehen
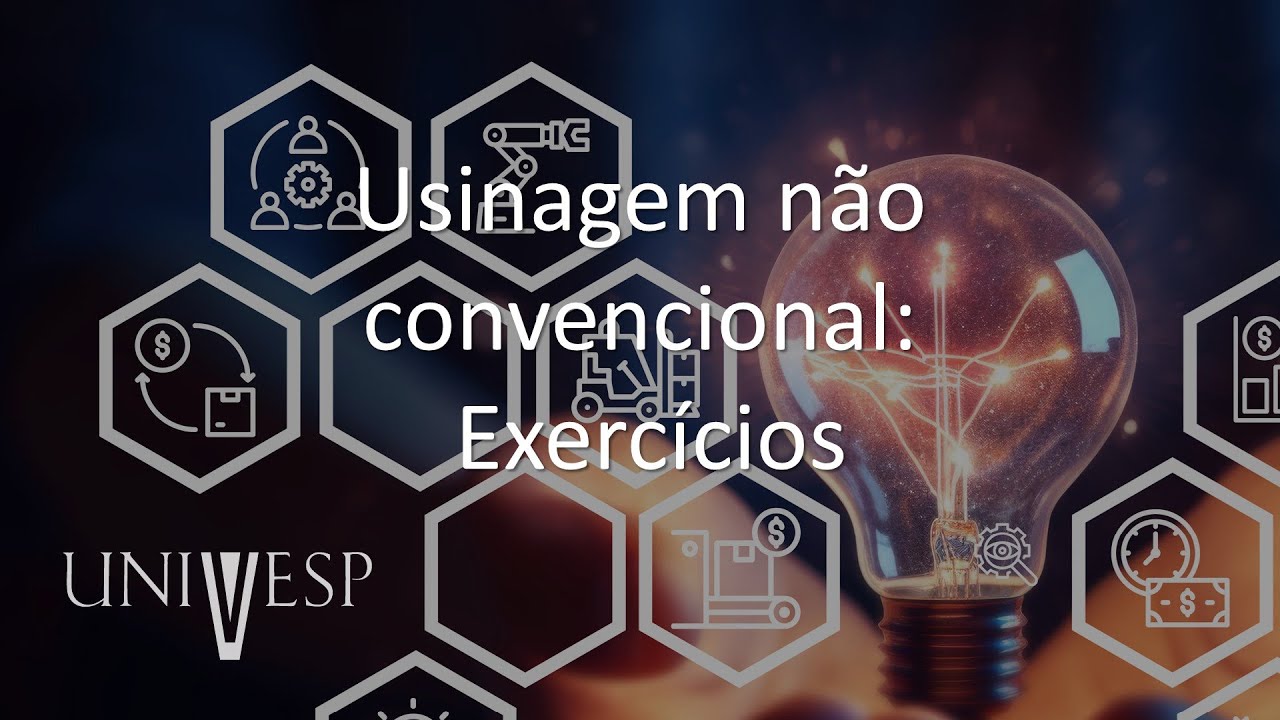
Materiais e Processos de Fabricação para Engenharia de Produção - Usinagem não convencional...
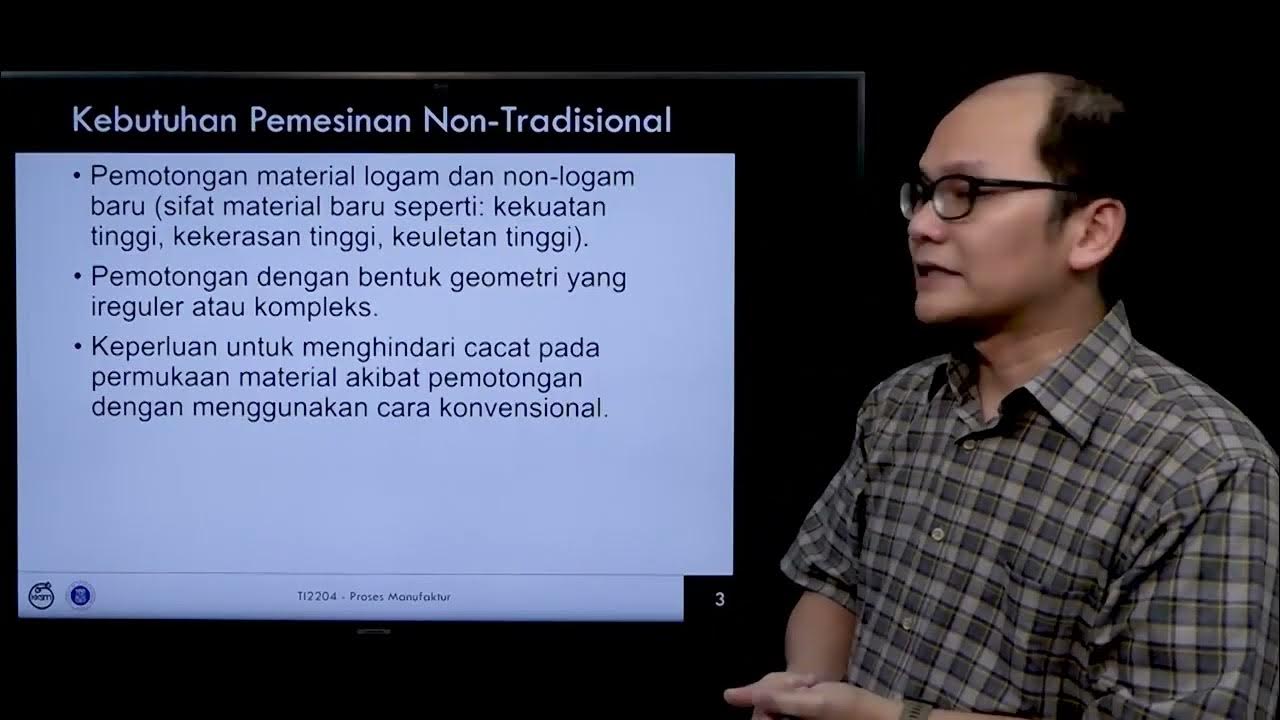
Proses Pemesinan Non Tradisional part 1

ELECTROCHEMICAL MACHINE (ECM): Construction and working of electrochemical Machining process.
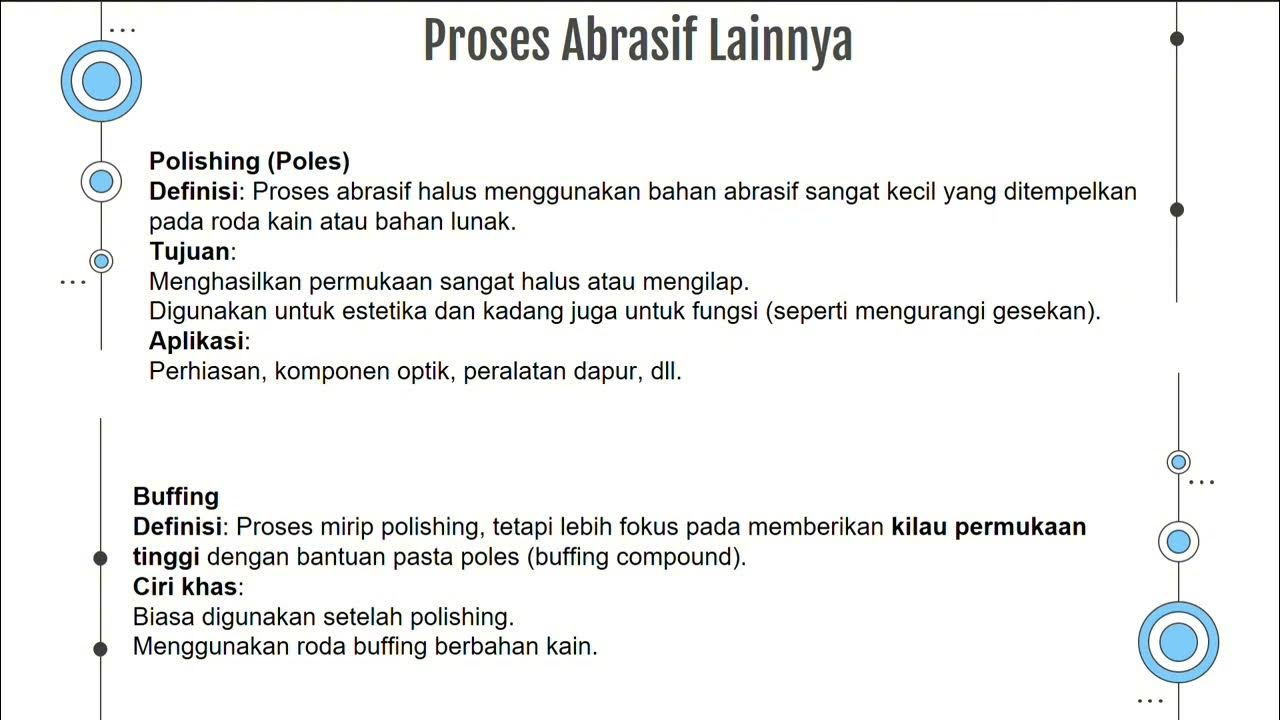
Gerinda dan Proses Abrasif Lainnya

Materiais e Processos de Fabricação para Engenharia de Produção: Usinagem não convencional

Design for Manufacturing Course 8 Part 1: CNC - DragonInnovation.com
5.0 / 5 (0 votes)