Materiais e Processos de Fabricação para Engenharia de Produção - Usinagem não convencional...
Summary
TLDRThis video tutorial delves into unconventional machining processes for engineering, particularly electrochemical machining, chemical machining, and wire EDM (electroerosion). The instructor walks through various exercises and formulas, focusing on material removal rates, efficiency calculations, and time estimations for processes like electrochemical cutting and chemical milling. The session covers specific calculations like removal rates based on material properties, electrode design, and machining parameters, with examples using different materials, including iron and aluminum alloys. Detailed explanations and problem-solving illustrate the intricacies of these advanced manufacturing methods.
Takeaways
- 😀 Electrochemical machining involves removing material by using an electrochemical reaction, and it can be calculated using specific formulas involving current, atomic mass, material resistivity, and electrode distance.
- 😀 The removal rate in electrochemical machining is directly proportional to the electric current applied; higher current results in higher material removal rates.
- 😀 The formula for calculating material removal rate in electrochemical machining considers factors like the material's atomic mass, valence, density, and resistivity of the electrolyte.
- 😀 Efficiency plays a crucial role in machining time calculations, as seen in exercises involving both electrochemical and electroerosion machining, where efficiency impacts the effective cutting speed.
- 😀 When machining a square hole in a plate, reducing the electrode size (for better fluid flow) can significantly decrease machining time, as demonstrated by comparing different electrode designs.
- 😀 In non-conventional machining processes, such as electrochemical machining, design adjustments like a smaller frontal area for the electrode can reduce machining time drastically by improving material removal efficiency.
- 😀 Chemical milling is used for creating cavities in materials like aluminum alloy, and involves applying chemicals like sodium hydroxide to remove material at a specified rate.
- 😀 The removal rate in chemical milling depends on the material type and chemical agent, with specific values for factors like penetration rate and attack factor, which are used to determine time and dimensions for the machining process.
- 😀 The area to be machined in chemical milling can be calculated by considering the geometry of the cut, such as subtracting circular areas from the rectangular region when corners are rounded.
- 😀 In wire electroerosion, the diameter of the electrode wire and the spark gap (socr) are key to determining the cutting width and removal rate, which can be used to calculate the advancement speed of the electrode wire.
Q & A
What is the focus of the video lesson?
-The video lesson focuses on non-conventional machining processes, including electrochemical machining, chemical machining, and electro-erosion machining. The lesson explores exercises related to the calculation of material removal rates in these processes.
What is the formula for calculating the material removal rate in electrochemical machining?
-The material removal rate in electrochemical machining is calculated using the formula: Rate = (Current × Atomic Mass × Valence) / (Faraday constant × Density of material × Resistivity of electrolyte). This shows the direct relationship between current, atomic mass, and other factors influencing material removal.
How does the current affect the material removal rate in electrochemical machining?
-The current has a direct proportionality to the material removal rate. Higher current results in a higher material removal rate, as more charge is available to cause the electrochemical reaction necessary for material removal.
What effect does the electrode design have on the material removal rate in electrochemical machining?
-The electrode design significantly affects the material removal rate. A smaller electrode area or one with a central hole, which facilitates electrolyte flow, reduces the frontal area of the electrode and thus reduces the material removal rate.
How do you calculate the time required for electrochemical machining to create a square hole in a steel plate?
-The time required for electrochemical machining is calculated by first determining the material removal rate using the formula. Then, the speed of the electrode movement is calculated, considering the efficiency factor. The time to machine the hole is found by dividing the distance (thickness of the plate) by the effective speed of the electrode.
Why is there a significant difference in machining time between two electrode designs in the electrochemical machining example?
-The machining time differs because one electrode design has a smaller frontal area due to the central hole, leading to a faster removal rate and shorter machining time. In contrast, the design with a larger frontal area requires more time to remove material.
What factors influence the speed of machining in chemical milling processes?
-The speed of machining in chemical milling is influenced by factors like the material to be milled, the chemical agent used (e.g., sodium hydroxide), and the penetration rate, which determines how quickly the material is removed. The geometry of the cavity and the time required to reach the desired depth also play important roles.
How is the area of the cavity to be milled calculated in chemical milling?
-The area of the cavity is calculated by first determining the area of the rectangular cavity and then subtracting the areas of the circular corners. These corners are treated as quarter circles with a given radius, and their area is subtracted from the total cavity area.
What is the effect of the re-etching factor (U) in chemical milling?
-The re-etching factor (U) represents the extra material that is removed below the mask during chemical milling. It is calculated based on the attack factor and is used to adjust the dimensions of the mask to ensure the correct final shape of the cavity.
What is the principle behind wire electro-erosion, and how does it affect material removal?
-Wire electro-erosion works by using a fine tungsten wire to discharge electrical pulses that erode the material. The material removal rate is influenced by the wire's diameter, discharge current, and other factors. The speed of material removal is calculated by considering these parameters and the width of the cut, which includes the wire diameter and any additional factors like the spark gap.
Outlines
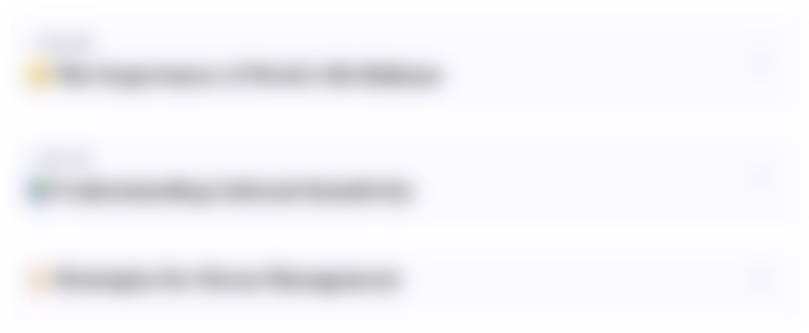
This section is available to paid users only. Please upgrade to access this part.
Upgrade NowMindmap
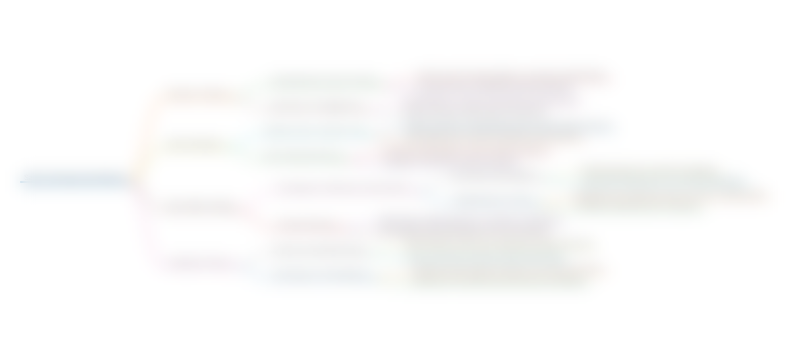
This section is available to paid users only. Please upgrade to access this part.
Upgrade NowKeywords
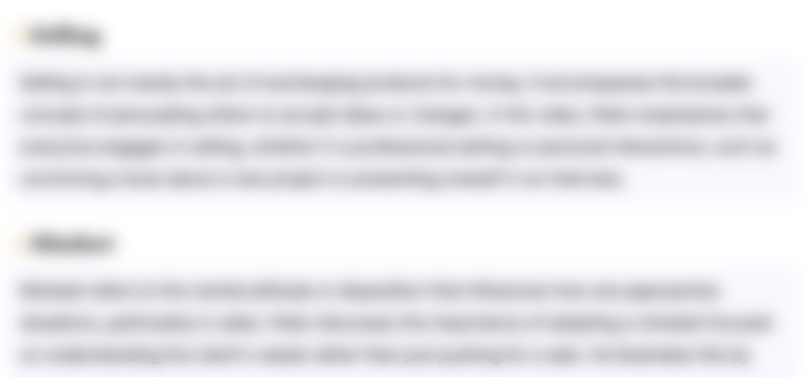
This section is available to paid users only. Please upgrade to access this part.
Upgrade NowHighlights
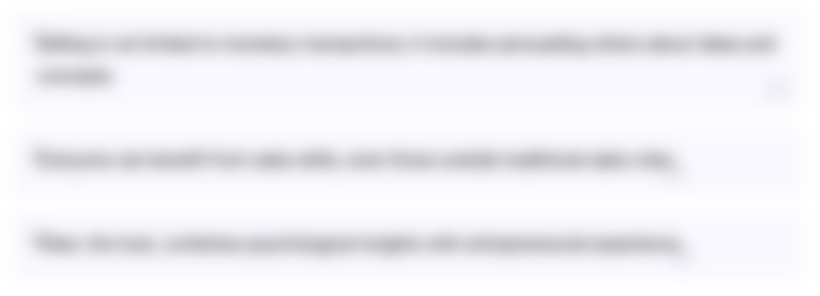
This section is available to paid users only. Please upgrade to access this part.
Upgrade NowTranscripts
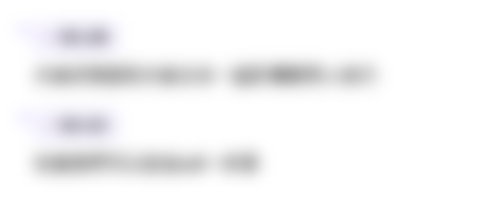
This section is available to paid users only. Please upgrade to access this part.
Upgrade NowBrowse More Related Video
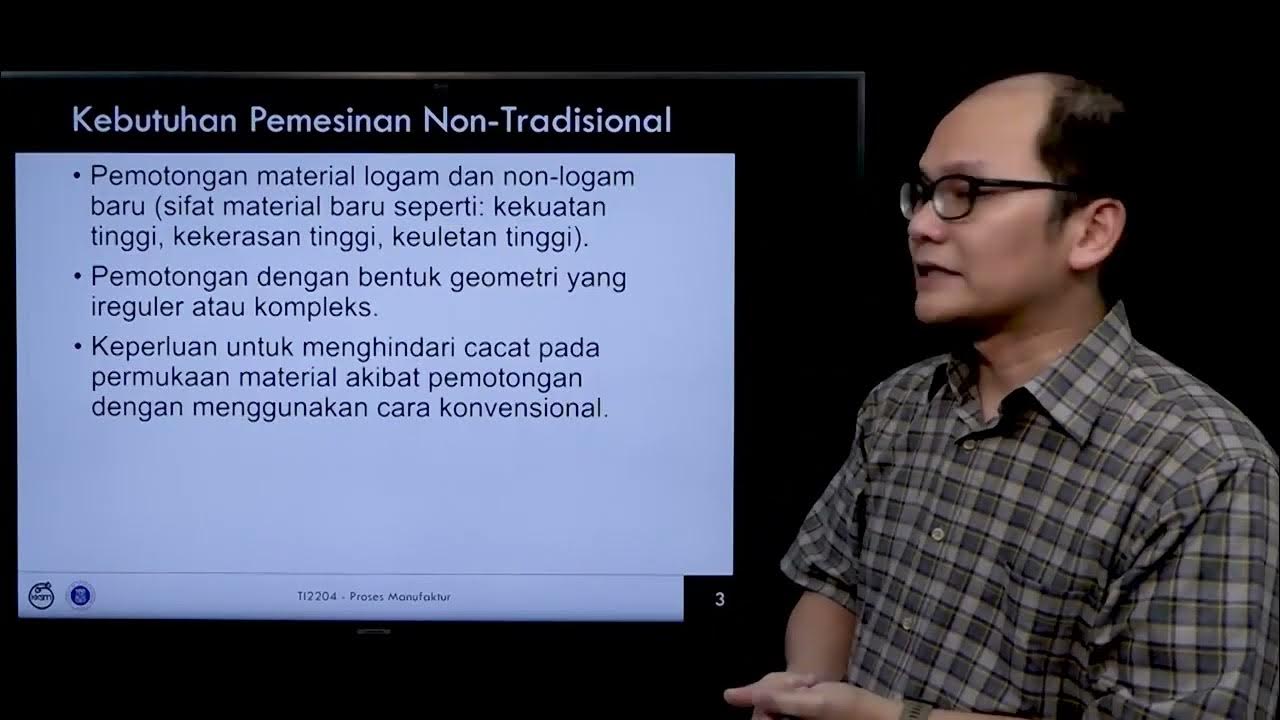
Proses Pemesinan Non Tradisional part 1

Materiais e Processos de Fabricação para Engenharia de Produção: Usinagem não convencional
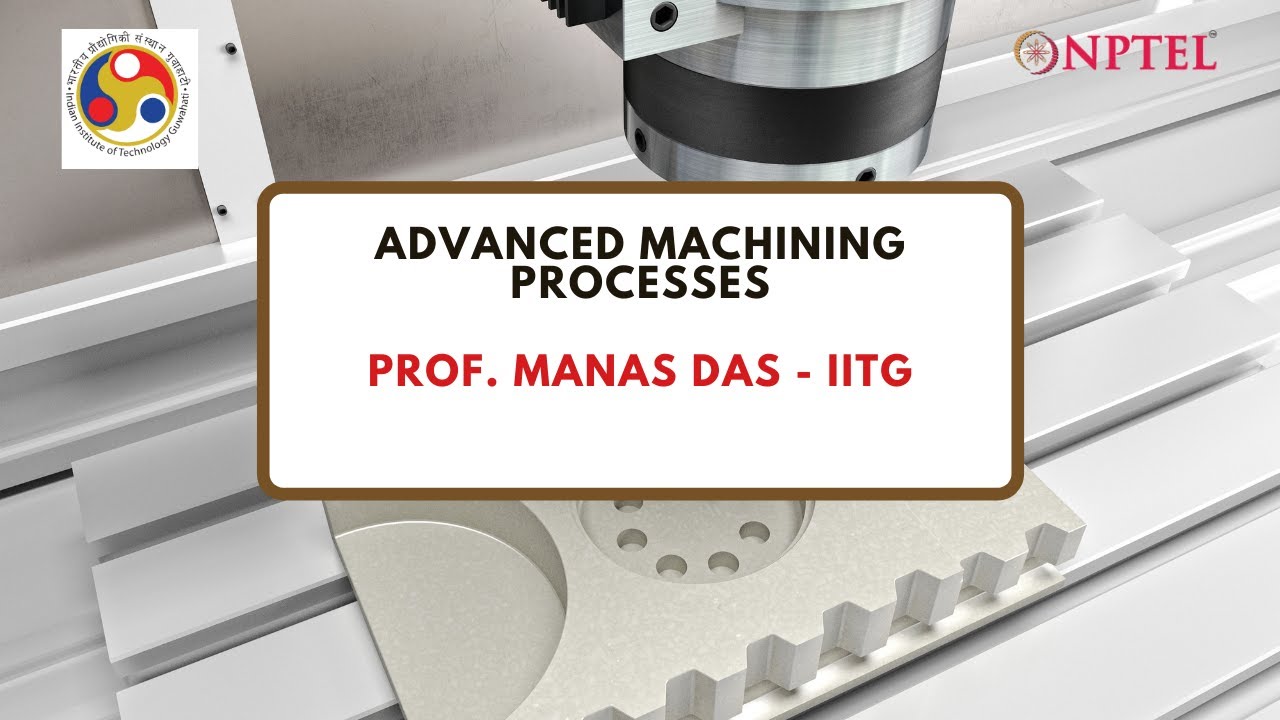
Introduction: Advanced Machining Processes
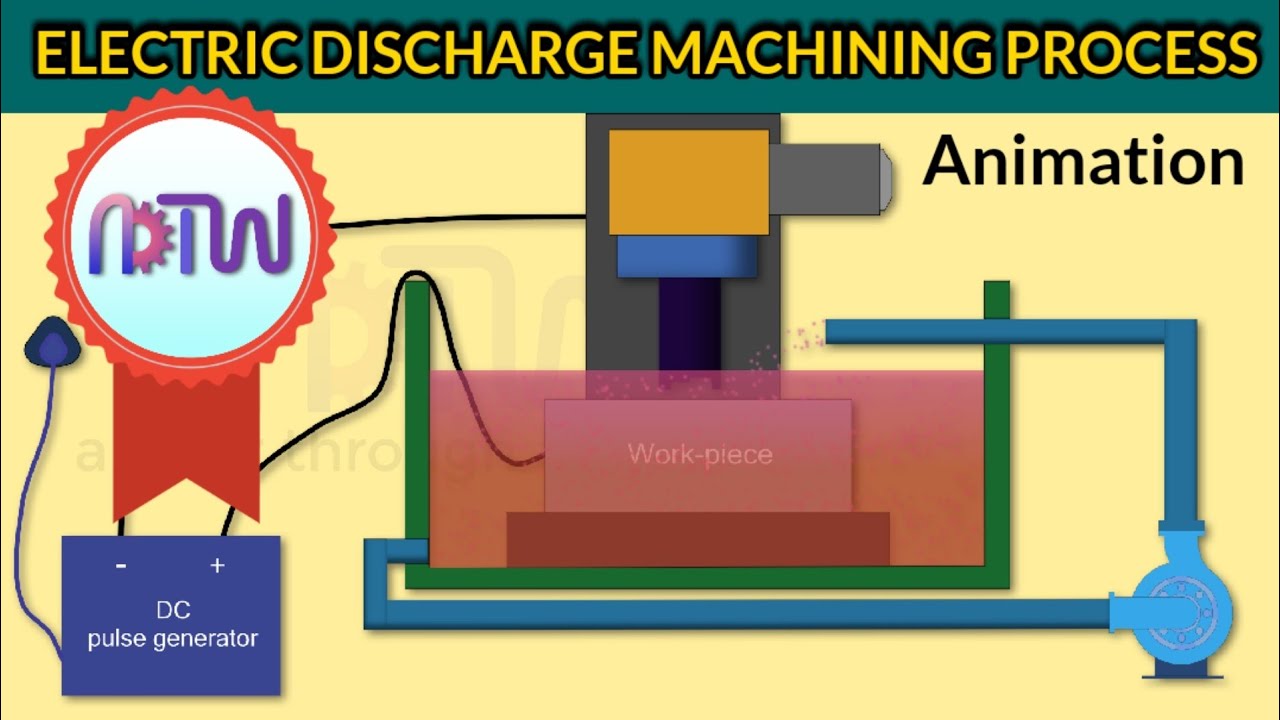
ELECTRIC DISCHARGE MACHINING PROCESS (Animation): How electric discharge maching works

Electrochemical Grinding Process | How electrochemical grinding works

Materiais e Processos de Fabricação para Engenharia de Produção - Usinagem convencional: Exercícios
5.0 / 5 (0 votes)