Introduction to Lean Thinking (2017)
Summary
TLDRThis video introduces lean thinking as an operational strategy aimed at continuous improvement and waste elimination. It emphasizes the importance of people, teamwork, and respect for individuals in the process. Lean helps organizations enhance productivity, reduce costs, and improve quality by focusing on waste types like waiting, defects, and excess motion. Success stories from companies like FedEx and Franciscan Health showcase lean’s impact. Gemba Academy offers comprehensive training on lean tools and concepts to help individuals and businesses achieve operational excellence, making lean applicable to any industry.
Takeaways
- 😀 Lean thinking is an operational excellence strategy focused on continuous improvement and eliminating waste in processes.
- 😀 Lean is not just about speeding up production; it also focuses on improving product quality and process stability.
- 😀 Lean's main goal is to create customer value by improving the way people and organizations work.
- 😀 Lean focuses on the elimination of different types of waste, such as waiting, defects, and excess motion, which can lead to productivity loss and even injuries.
- 😀 Lean is a people-centered system, where the development and engagement of individuals are key to successful implementation.
- 😀 The 'lean house' structure includes two main pillars: continuous improvement (tools and concepts) and respect for people (developing employees).
- 😀 Continuous improvement (kaizen) and teamwork are fundamental concepts of lean thinking.
- 😀 Lean practices lead to increased employee engagement, better morale, reduced operating costs, and improved safety.
- 😀 Real-world examples show the practical benefits of lean, such as FedEx reducing accuracy failures by 30% and a 60% decrease in injury rates.
- 😀 Lean can result in significant financial savings and improvements, as seen with Grand Rapids' Water Department, which saved $500,000 annually by improving inventory management.
- 😀 Lean tools like 5S, value stream mapping, and the seven wastes can be applied by anyone in any industry to drive improvement.
Q & A
What is lean thinking?
-Lean thinking is an operational excellence strategy that helps organizations and individuals continuously improve the way they work by focusing on eliminating waste, enhancing efficiency, and developing people.
What is the main focus of lean thinking?
-The main focus of lean thinking is the persistent pursuit and elimination of waste in processes. This includes waste from waiting, defects, excess motion, and other inefficiencies that reduce productivity and quality.
Why is the people aspect so important in lean thinking?
-The people aspect is crucial in lean thinking because the greatest value of lean lies in the development of people. Lean is not just about tools and processes; it is a people-based system that emphasizes teamwork, respect, and continuous improvement.
What are the two main pillars of the lean house?
-The two main pillars of the lean house are 'continuous improvement' and 'respect for people.' Continuous improvement refers to the various lean tools and concepts, while respect for people emphasizes the importance of developing individuals within the organization.
What are some common wastes identified in lean thinking?
-Common types of waste in lean thinking include waiting time, defects, excess motion, and unnecessary processes that contribute to inefficiency and reduced quality.
How does lean thinking impact product quality and stability?
-Lean thinking improves product quality and process stability by focusing on eliminating inefficiencies and ensuring that processes are stable and capable of producing high-quality products consistently.
Can lean thinking be applied to any industry?
-Yes, lean thinking is versatile and can be applied to any industry, from manufacturing to healthcare, service, and beyond. The principles of lean are adaptable to various organizational needs and objectives.
What are some tangible benefits organizations experience by adopting lean thinking?
-Organizations practicing lean thinking often experience benefits such as improved employee engagement, reduced operating costs, increased safety, higher quality products, and enhanced customer satisfaction, leading to long-term growth and profitability.
Can you share any real-life examples of lean success?
-Yes, examples of lean success include FedEx Office, which reduced accuracy failures by 30%, and Franciscan Health, which saved over $30,000 annually. Another example is the water department in Grand Rapids, Michigan, which reduced costs by $500,000 per year through lean practices.
What are some common lean tools used by organizations?
-Some common lean tools include 5S (organizational method), the seven wastes, and value stream mapping. These tools help identify inefficiencies, streamline processes, and improve overall performance.
Outlines
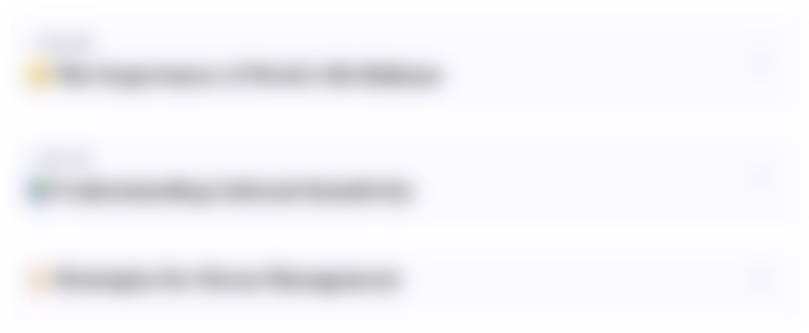
Dieser Bereich ist nur für Premium-Benutzer verfügbar. Bitte führen Sie ein Upgrade durch, um auf diesen Abschnitt zuzugreifen.
Upgrade durchführenMindmap
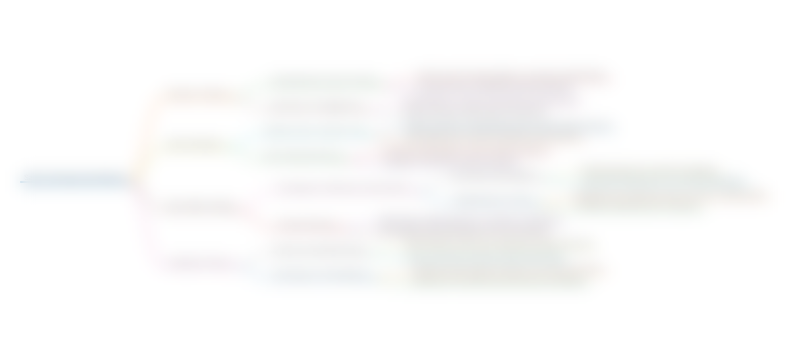
Dieser Bereich ist nur für Premium-Benutzer verfügbar. Bitte führen Sie ein Upgrade durch, um auf diesen Abschnitt zuzugreifen.
Upgrade durchführenKeywords
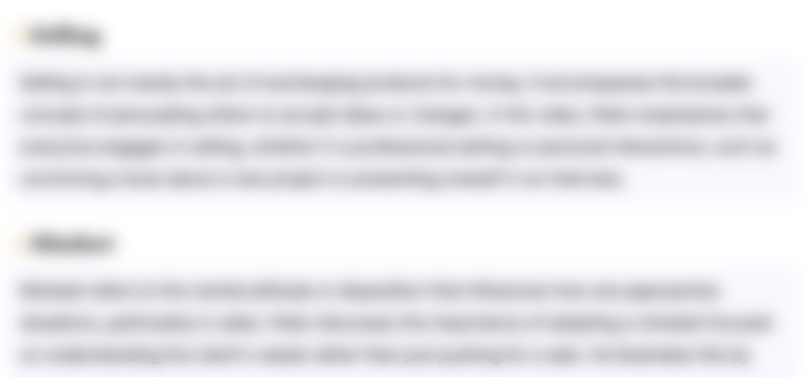
Dieser Bereich ist nur für Premium-Benutzer verfügbar. Bitte führen Sie ein Upgrade durch, um auf diesen Abschnitt zuzugreifen.
Upgrade durchführenHighlights
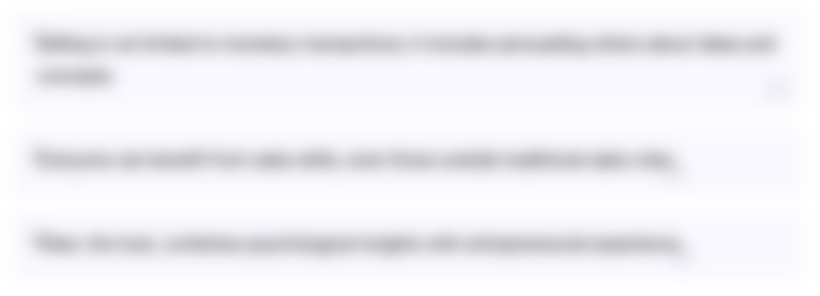
Dieser Bereich ist nur für Premium-Benutzer verfügbar. Bitte führen Sie ein Upgrade durch, um auf diesen Abschnitt zuzugreifen.
Upgrade durchführenTranscripts
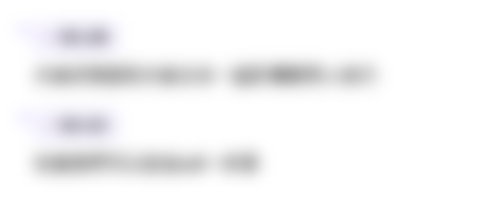
Dieser Bereich ist nur für Premium-Benutzer verfügbar. Bitte führen Sie ein Upgrade durch, um auf diesen Abschnitt zuzugreifen.
Upgrade durchführenWeitere ähnliche Videos ansehen
5.0 / 5 (0 votes)