Tilo Schwarz: Toyota Kata = Enabling a Lean-Culture
Summary
TLDRTilo Schwartz, a management trainer and Kata coach, discusses the Toyota Kata, a management system focused on enhancing problem-solving abilities and making continuous improvement a daily habit. He shares his experience at Festool, where the implementation of this system led to operational excellence awards. Schwartz emphasizes the need for a shift from lean solutions to increasing adaptability and comfort with change. He also highlights the importance of a consistent management pattern for successful strategy implementation and the development of behaviors that support continuous improvement.
Takeaways
- π The Toyota Kata is a management system focused on enhancing problem-solving abilities and making continuous improvement a part of daily work, rather than just implementing lean solutions.
- π Festool, a German manufacturer of power tools, won two operational excellence awards in Germany by implementing a management system that integrated continuous improvement into everyone's daily tasks.
- π The concept of Toyota Kata was popularized by a book released in 2009, based on insights from Mike Rother's research on Toyota management, which was learned around 2008.
- π Continuous improvement efforts often face challenges where initial progress is not sustained, leading to a cycle of success and subsequent decline.
- π€ Three critical questions were posed to assess lean journey effectiveness: Are we satisfied with the results? Are the results sustainable? Is continuous improvement truly continuous?
- π The speaker's experience at Festool highlighted the gap between daily operations and continuous improvement efforts, with a focus on workshops and a few experts, rather than organizational-wide engagement.
- π§ The root cause of many improvement failures lies in the separation between improvement activities and daily work, leading to a need for a system where improvement is part of daily business.
- π Success in implementing strategy is not just about having a good plan but also about the ability to execute it, which is heavily influenced by the team's ability to handle problems effectively.
- π The Improvement Kata consists of a series of behaviors aimed at striving for challenges, understanding root causes, and validating solutions through quick experiments.
- π To create a culture of continuous improvement, it is essential to define and train desired behavior patterns until they become habits, which is achieved through consistent management practices at all levels of an organization.
Q & A
What is the Toyota Kata and how does it differ from other management systems?
-The Toyota Kata is a management system that focuses on increasing problem-solving ability by developing and changing behaviors, making people comfortable with change, and striving for continuous improvement as part of daily work. Unlike other approaches, it does not primarily focus on implementing lean solutions.
What were the three questions Tilo Schwartz asked himself and his team regarding their improvement process?
-Tilo Schwartz asked if they were satisfied with the results of their improvement process, whether the results were sustainable, and if continuous improvement was truly continuous.
What was the main issue Tilo Schwartz identified with their continuous improvement approach at Festool?
-The main issue was that continuous improvement was primarily driven through workshops and a handful of experts, while the rest of the organization was mainly concerned with daily business, leading to a disconnect and lack of sustainability in the improvement process.
What is the significance of the letter written by Robert Falcon Scott in the context of strategy implementation?
-The letter highlights the common excuses and misunderstandings about the reasons for strategic failures. It emphasizes the importance of focusing on the three key factors necessary for successful strategy implementation: ability, self-motivation, and a common direction.
What core ability was missing in Scott's team that led to their expedition's failure?
-The core ability missing was effective problem handling. Scott's team lacked the ability to deeply investigate and address the root causes of the problems they encountered, leading to unsustainable solutions and ultimately, the failure of their expedition.
How does the Improvement Kata aim to change behaviors and habits for continuous improvement?
-The Improvement Kata aims to change behaviors and habits by coding desired behaviors into a structured pattern (Kata) and training them until they become habitual. This involves focusing on vital behaviors, reducing professional tasks to a simple sequence of steps, and consistently applying a management pattern that supports and reinforces these behaviors.
What are the four key behaviors that the Improvement Kata seeks to instill in individuals for effective continuous improvement?
-The four key behaviors are striving for a challenge, being fact-based, being root cause-oriented, and conducting quick experiments and validations.
How does the coaching kata support the implementation of the Improvement Kata in an organization?
-The coaching kata supports the implementation by providing a consistent management pattern that encourages and guides individuals towards the desired behaviors. It involves asking specific questions that prompt reflection and action towards continuous improvement, and it is applied on every management level on a daily basis.
What is the role of management in creating and maintaining a continuous improvement culture?
-Management plays a crucial role in creating and maintaining a continuous improvement culture by establishing and applying a consistent management pattern that reinforces the desired behaviors. They need to support and request a certain way of behavior that aligns with the continuous improvement mindset.
Why is it important to focus on process targets rather than result targets when striving for continuous improvement?
-Focusing on process targets is important because they encourage the establishment of a continuous improvement behavior that does not become obsolete and does not rely on external factors. Process targets promote a systematic approach to improvement that is sustainable and adaptable, unlike result targets which may lead to short-term solutions and are often dependent on factors beyond control.
How can an organization ensure that continuous improvement becomes a part of daily work?
-An organization can ensure continuous improvement becomes part of daily work by defining and training the desired behavior patterns until they become habits for each individual. This involves using a management pattern that consistently reinforces these behaviors at all levels of the organization.
Outlines
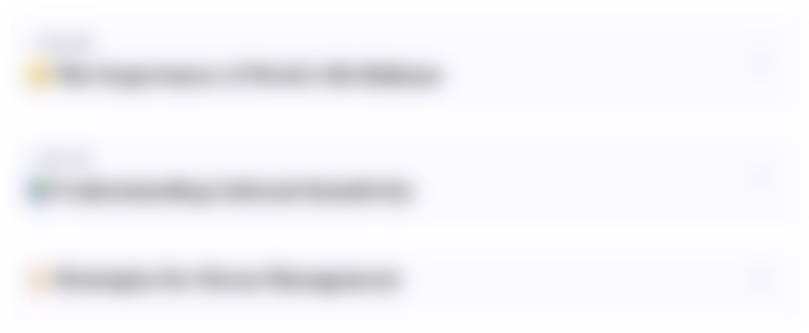
This section is available to paid users only. Please upgrade to access this part.
Upgrade NowMindmap
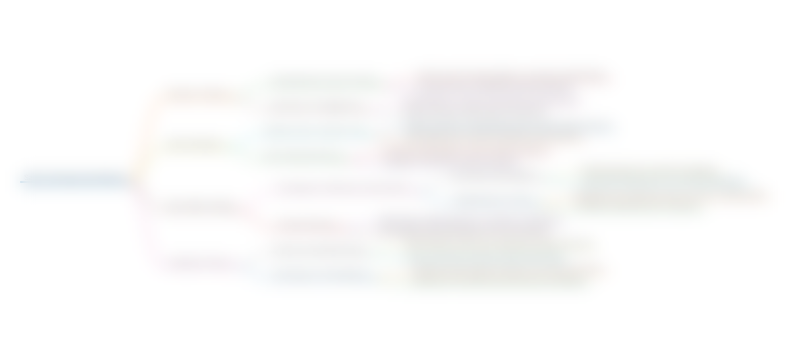
This section is available to paid users only. Please upgrade to access this part.
Upgrade NowKeywords
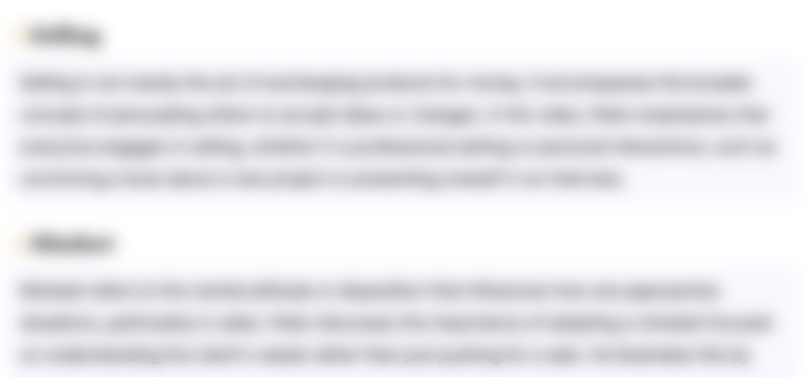
This section is available to paid users only. Please upgrade to access this part.
Upgrade NowHighlights
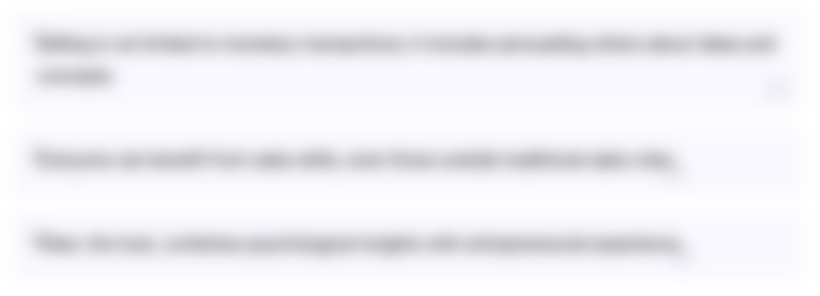
This section is available to paid users only. Please upgrade to access this part.
Upgrade NowTranscripts
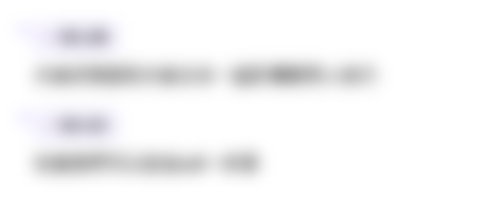
This section is available to paid users only. Please upgrade to access this part.
Upgrade NowBrowse More Related Video
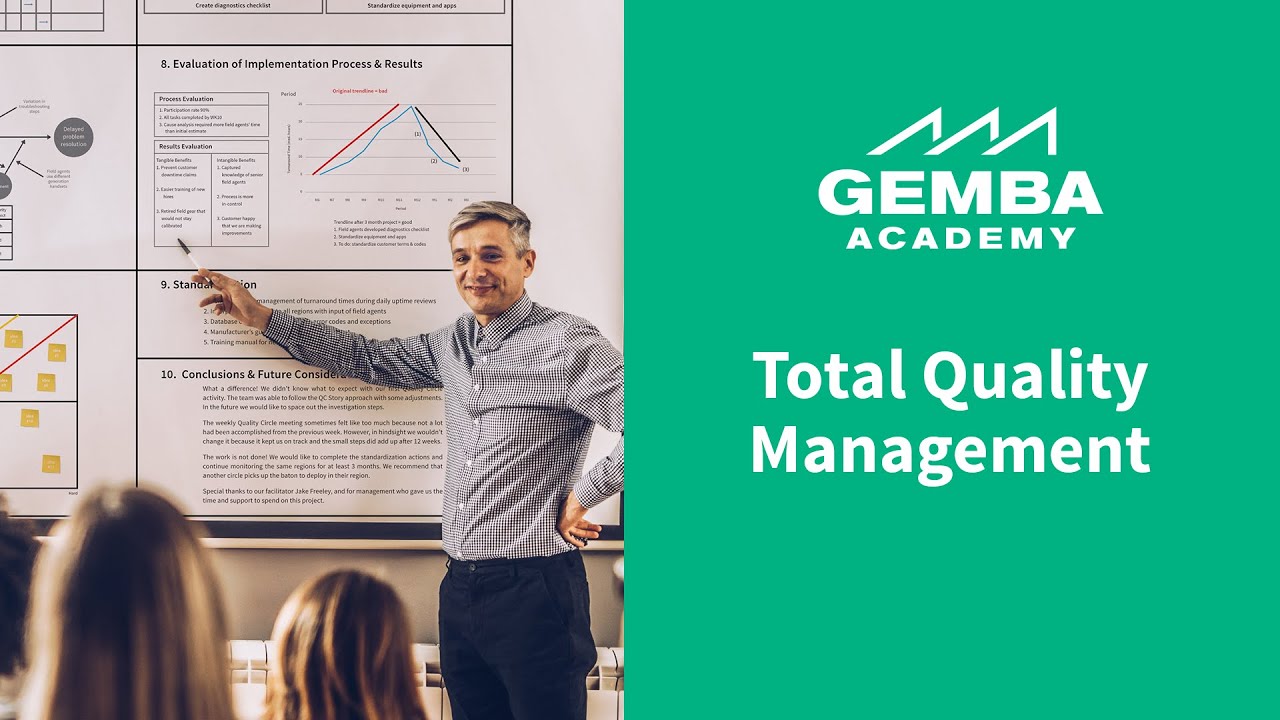
What is Total Quality Management - TQM
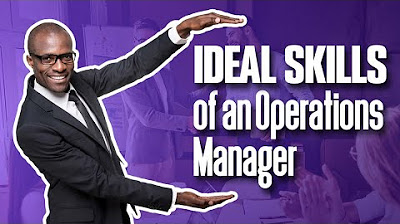
Ideal Skills of an Operations Manager | Simplicity Consultancy

Comment adapter ses placements Γ la baisse des taux et au grand ralentissement ?

Root Cause Analysis Techniques | Root Cause Analysis | Invensis Learning

What does a continuous improvement manager do?
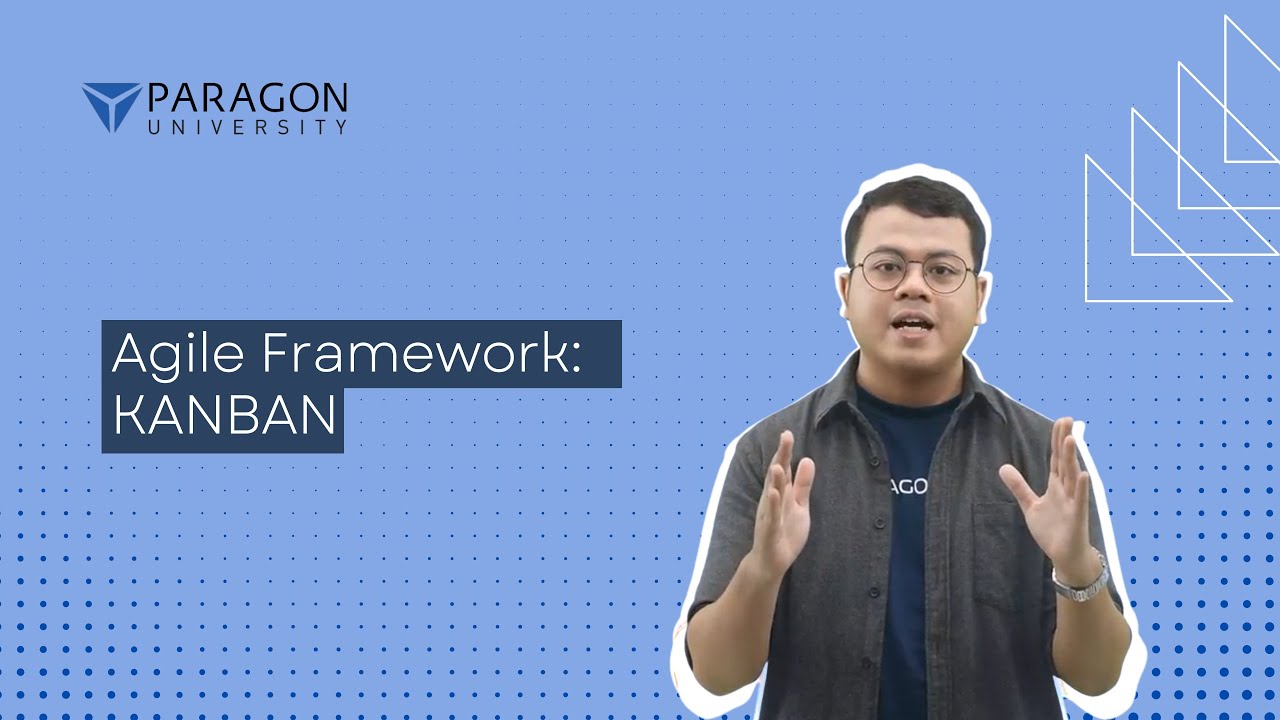
Project Management Part 10: Agile Framework - Kanban
5.0 / 5 (0 votes)