M3 L6 Lean Principles for Continuous Improvement
Summary
TLDRThe video script outlines a strategic approach to achieving operational excellence through the principles of lean methodology. It emphasizes the importance of understanding customer value, streamlining processes, and eliminating waste to maximize efficiency and revenue. The script introduces five core lean principles, eight types of waste, and various tools like the DMAIC framework and Kaizen for continuous improvement. It encourages leaders to delegate and empower their teams to drive cultural shifts towards operational efficiency.
Takeaways
- 📈 **Operational Excellence Journey**: Continuous improvement is essential, focusing on efficiency, effectiveness, and value-driven actions.
- 🏗️ **Building Blocks & Delegation**: Establishing operational excellence requires understanding the five guiding principles and delegating tasks to avoid overwhelming oneself.
- 🛠️ **Lean Principles**: Lean methodology is adopted from the automotive industry and is a mindset for maximizing customer value while minimizing waste, applicable across various industries.
- 🔍 **Value Identification**: The core of lean is identifying what customers truly value, which is the starting point for eliminating waste and improving processes.
- 🌐 **Value Stream Mapping**: Mapping out every step in the process to see what adds direct value to the customer, using flags to categorize activities as green (value-adding), orange (necessary but not value-adding), and red (wasteful).
- 🚀 **Cultural Shift**: Embracing change, open communication, and problem-solving are crucial for building a lean organization that thrives on clarity, efficiency, and continuous improvement.
- 🔎 **Waste Identification**: Understanding the eight types of waste (defects, overproduction, waiting, non-utilized talent, transportation, inventory, motion, and extra processing) is key to operational excellence.
- 👀 **Gemba Walks**: Leadership should regularly observe the value stream in its natural setting to identify waste and gather feedback from the team.
- 🔄 **Root Cause Analysis**: Tools like the 'five whys' and fishbone diagrams help in identifying the root cause of problems, which is essential for effective process improvement.
- 🛑 **Process Improvement**: The DMAIC (Define, Measure, Analyze, Improve, Control) framework provides a structured approach to tackle complex problems and improve processes.
- 🌱 **Kaizen Philosophy**: Kaizen, meaning 'change for the better,' encourages continuous, incremental improvements and a culture where everyone contributes to the organization's growth.
Q & A
What are the five guiding principles for operational excellence mentioned in the script?
-The script does not explicitly list the five guiding principles for operational excellence but emphasizes the importance of efficiency, effectiveness, high quality, value-driven processes, and continuous improvement.
What are the four building blocks for operational excellence?
-The script does not detail the four building blocks but suggests that they are foundational elements that, when established, should result in operational excellence.
Why is delegation important in achieving operational excellence?
-Delegation is crucial because it allows leaders to distribute tasks among teams or hire external consultants, enabling them to focus on guiding and leading the process rather than trying to fix everything themselves.
What does the script suggest as an alternative to creating standard operating procedures for everything by oneself?
-The script suggests delegating tasks to teams or hiring external consultants to assist in the process, as creating standard operating procedures for everything by oneself could overwhelm the leader and detract from their primary role.
How does the script define Lean methodology?
-The script defines Lean methodology as fundamentally about maximizing customer value while minimizing waste. It is not just a set of tools but a mindset that focuses on delivering value efficiently.
What are the five core Lean principles mentioned in the script?
-The five core Lean principles mentioned are: 1) Value - understanding what customers truly value; 2) Value Stream - mapping out every step in the process; 3) Waste Management - identifying and eliminating wasteful steps; 4) Flow - ensuring smooth progression of value-adding steps; 5) Perfection - an ongoing journey to improve and get closer to perfection.
What is the definition of waste in the context of Lean methodology?
-In the context of Lean methodology, waste is defined as anything that does not add value to the customer.
What are the eight types of waste identified in the script?
-The eight types of waste are: defects, overproduction, waiting, non-utilized talent, transportation, inventory, motion, and extra processing.
What is the purpose of a waste audit in the context of the script?
-The purpose of a waste audit is to identify different types of waste in the current operations, which can help in streamlining processes and enhancing value to customers.
How can one identify and address inefficiencies in their organization using the script's guidance?
-One can identify inefficiencies by conducting a waste audit, mapping out current processes, and comparing them to ideal processes. The script also suggests using tools like the five times why exercise, the fishbone diagram, and the Impact versus effort Matrix to address inefficiencies.
What is Kaizen and how does it relate to continuous improvement in an organization?
-Kaizen is a Japanese term meaning 'change for the better' and represents a philosophy of integrating continuous, incremental improvement into daily operations. It encourages all employees to contribute ideas for improvement, fostering a culture where everyone is responsible for enhancing the organization's processes and outcomes.
Outlines
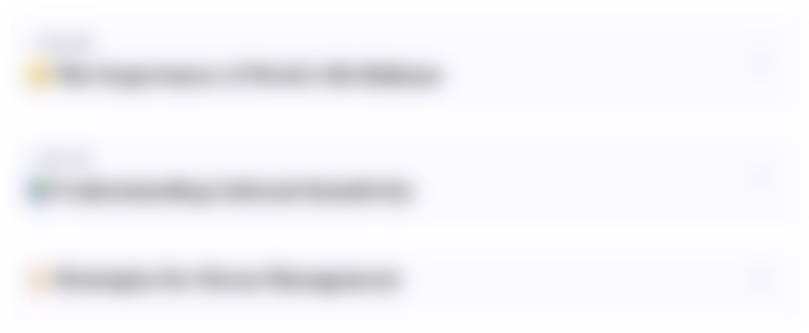
This section is available to paid users only. Please upgrade to access this part.
Upgrade NowMindmap
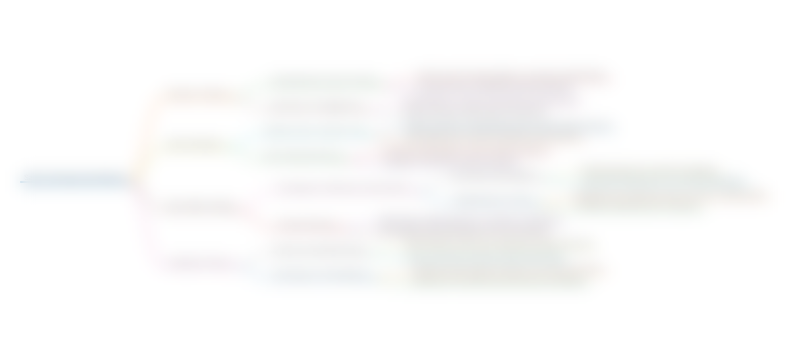
This section is available to paid users only. Please upgrade to access this part.
Upgrade NowKeywords
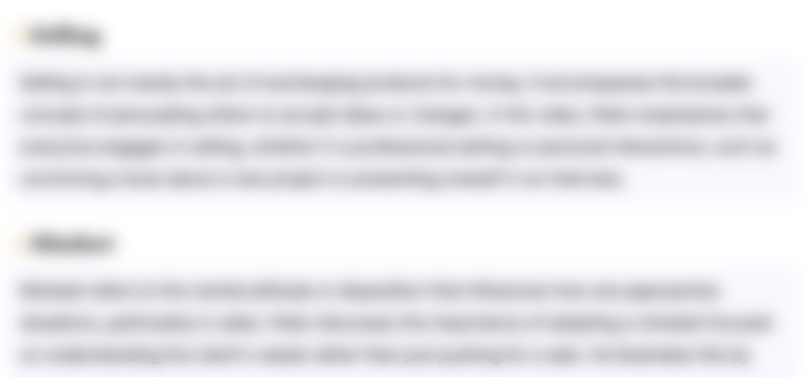
This section is available to paid users only. Please upgrade to access this part.
Upgrade NowHighlights
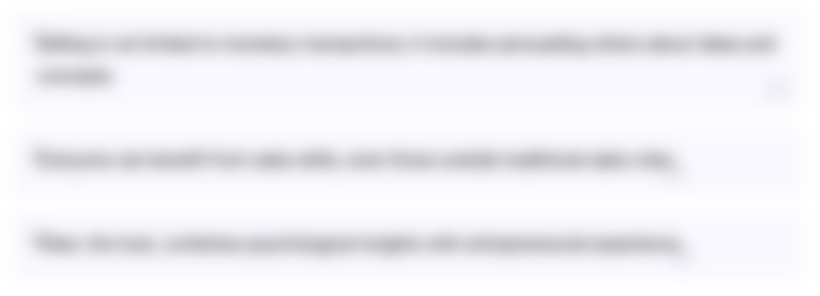
This section is available to paid users only. Please upgrade to access this part.
Upgrade NowTranscripts
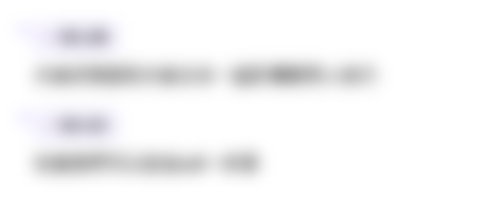
This section is available to paid users only. Please upgrade to access this part.
Upgrade Now5.0 / 5 (0 votes)