Just in Time by Toyota: The Smartest Production System in The World
Summary
TLDRIn this episode of 'Selling Breakdowns,' Alex Berman explores Toyota's innovative 'Just In Time' (JIT) production system, which emerged in post-war Japan. The JIT system, developed by Taiichi Ohno, optimizes production by minimizing inventory and wait times, focusing on adding value at each stage. It leverages Japan's small size for efficient, on-time deliveries from suppliers, reducing costs and emphasizing quality over quantity. The JIT philosophy challenges traditional 'Just In Case' approaches, promoting efficiency, quality, and trust in staff, making it applicable to various business areas.
Takeaways
- 🏭 Just In Time (JIT) is a production system created by Toyota post-World War II to optimize efficiency and minimize waste.
- 🌏 Post-war Japan's scarcity of cash and resources led to the innovative JIT approach, turning limitations into strategic advantages.
- 🔧 JIT philosophy focuses on producing only what is needed, reducing wait times, and minimizing inventory to save on warehousing costs.
- 🚚 The system relies on frequent, timely deliveries from suppliers, which is feasible in Japan due to its relatively small size.
- ❌ Risks in JIT include supply chain disruptions that can halt production if suppliers fail to deliver on time.
- 🔍 JIT encourages continuous improvement by questioning each production step's value addition and eliminating non-value-adding activities.
- 💡 The JIT approach can be applied to various business areas, promoting efficiency, quality, and cost savings.
- 🛠️ JIT demands high-quality control and perfect functioning to avoid the need for spare parts or extra time buffers.
- 🤝 The philosophy can boost morale by entrusting staff with consistent performance, fostering a culture of respect and trust.
- 📈 JIT contrasts with the 'Just In Case' approach, which involves maintaining buffers to mitigate risks, potentially leading to wasted resources.
Q & A
What is the main focus of the video 'Selling Breakdowns' by Alex Berman?
-The main focus is to explore the Just In Time (JIT) production system created by Toyota in post-war Japan, explaining how it works and how its philosophy and practices can be applied to various areas of business.
What challenges did Japan face after World War 2 that influenced the development of Just In Time?
-Japan faced a lack of cash, scarce resources, and limited land for factory expansion, which led Taiichi Ohno at Toyota to develop the Just In Time system to overcome these challenges.
How did Taiichi Ohno turn Japan's post-war problems into advantages for Toyota?
-Taiichi Ohno managed to turn the problems into advantages by gradually creating the Just In Time system, which focused on minimizing waste and maximizing efficiency in production.
What is the core principle of the Just In Time production system?
-The core principle of JIT is to produce only what is needed, when it is needed, and in the amount needed, thereby minimizing wait times and inventory costs.
How does Just In Time reduce the need for inventory?
-Just In Time reduces inventory by ordering parts and materials as soon as they are needed rather than keeping a stockpile, which eliminates the costs associated with warehousing.
What is the potential risk associated with the Just In Time system?
-The potential risk is that any disruption in the supply chain can shut down the entire production system since there are no spare parts or buffer stock to fall back on.
How did Toyota use Japan's geographical size to its advantage in the Just In Time system?
-Toyota leveraged Japan's relatively small size to ensure suppliers could deliver parts on time due to short travel distances, which was crucial for the JIT system's success.
How does Just In Time influence the quality of production?
-Just In Time forces a focus on quality to maintain efficiency, as there is no room for errors or faulty parts, which would disrupt the production process.
What is the difference between the 'Just In Time' and 'Just In Case' approaches?
-Just In Time focuses on minimizing waste and risk by producing or ordering only what is needed, while Just In Case involves maintaining buffers such as extra stock or staff to handle potential issues.
How can the Just In Time philosophy improve morale among staff?
-The JIT philosophy can improve morale by showing trust in staff to perform consistently without the need for excessive buffers or safety nets, which can be motivating and foster a sense of responsibility.
What are some ways businesses can apply the Just In Time philosophy beyond manufacturing?
-Businesses can apply JIT by focusing on efficiency in all areas, such as improving communication between departments, enhancing quality control to reduce the need for backups, and streamlining services to minimize resource waste.
Outlines
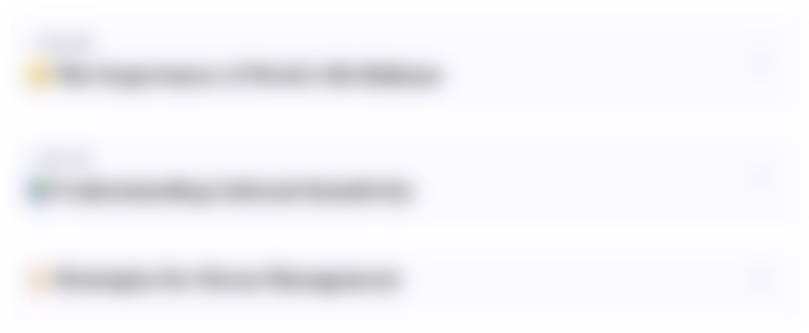
هذا القسم متوفر فقط للمشتركين. يرجى الترقية للوصول إلى هذه الميزة.
قم بالترقية الآنMindmap
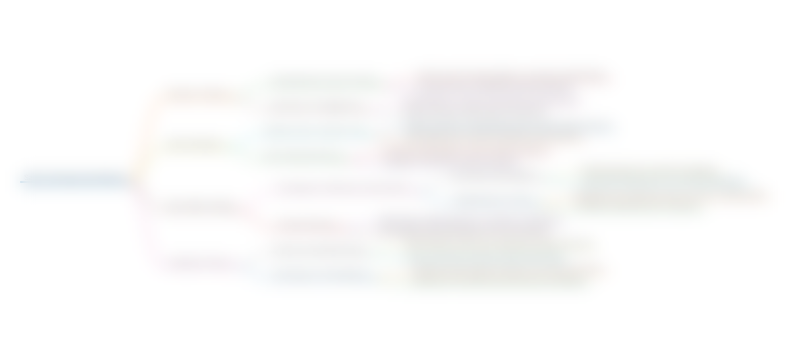
هذا القسم متوفر فقط للمشتركين. يرجى الترقية للوصول إلى هذه الميزة.
قم بالترقية الآنKeywords
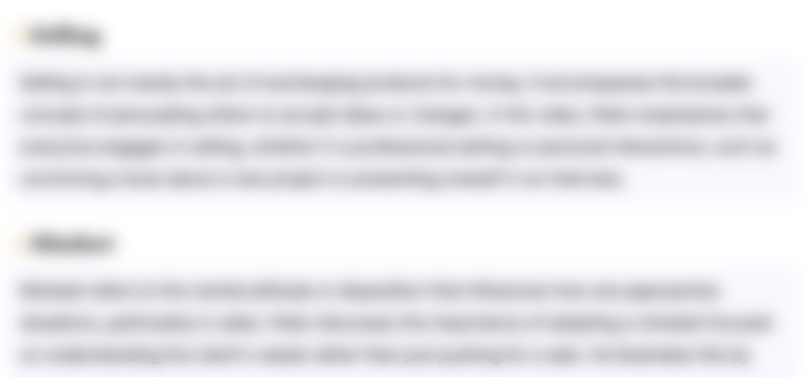
هذا القسم متوفر فقط للمشتركين. يرجى الترقية للوصول إلى هذه الميزة.
قم بالترقية الآنHighlights
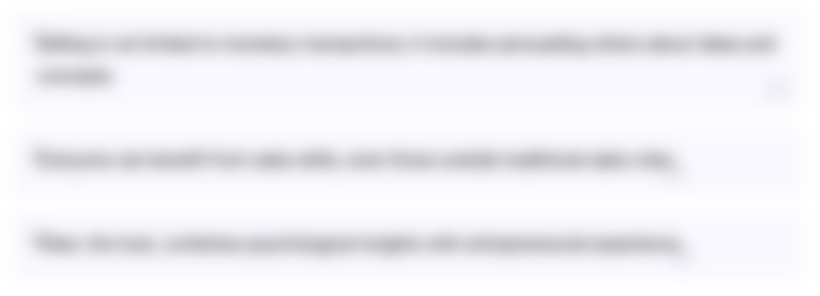
هذا القسم متوفر فقط للمشتركين. يرجى الترقية للوصول إلى هذه الميزة.
قم بالترقية الآنTranscripts
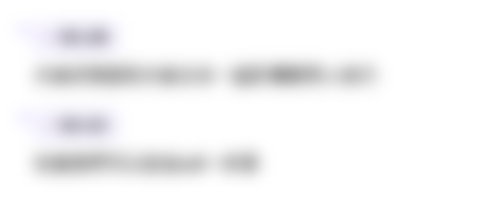
هذا القسم متوفر فقط للمشتركين. يرجى الترقية للوصول إلى هذه الميزة.
قم بالترقية الآنتصفح المزيد من مقاطع الفيديو ذات الصلة

Modelo Toyota de Produção - Just In Time & Kanban
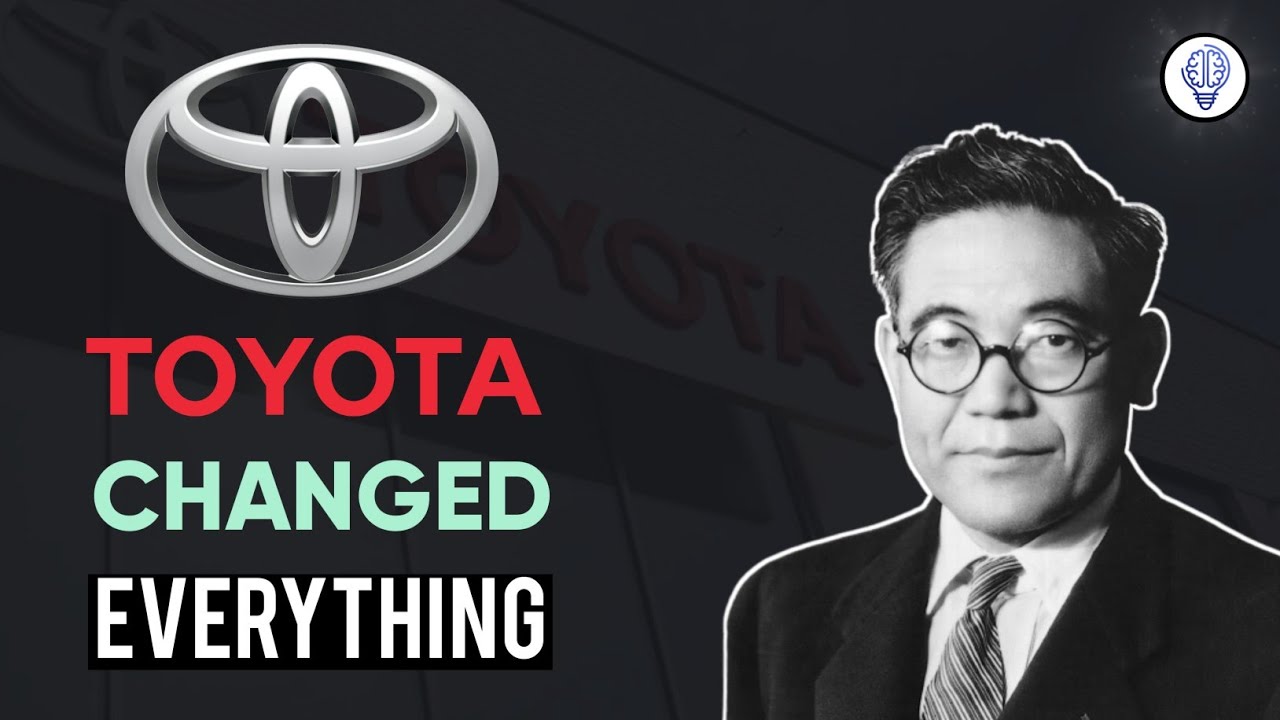
How did Toyota beat FORD & GM using its GENIUS Supply Chain Model?
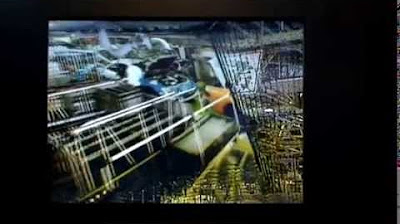
History of the Toyota Production System (TPS)

Just In Time JIT Definition Investopedia

English Learning Podcast Conversation | Episode 47: Just In Time Strategy
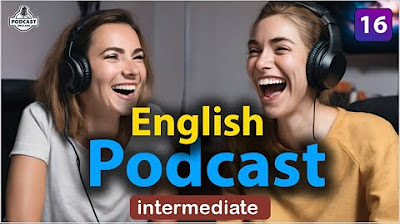
Powerful Podcasts for English Fluency | Episode 16
5.0 / 5 (0 votes)