PID Control - A brief introduction
Summary
TLDRThis video introduces PID control, a fundamental concept in control systems. It begins by explaining the limitations of open-loop systems and the importance of feedback control. Using a robot as an example, the video highlights how PID controllers adjust errors to achieve desired outcomes. PID stands for Proportional, Integral, and Derivative, each representing a different method for adjusting system errors. The video also touches on how different control paths can be simplified based on the design requirements. The next video will provide further examples and mathematical insights into PID control.
Takeaways
- 📋 A controller is used to adjust a system's performance to meet specific requirements by controlling the inputs and outputs.
- 🤖 Open-loop control doesn't adjust based on the system's actual performance, making it less accurate in dynamic conditions.
- 🔄 Feedback control involves measuring the system's output, comparing it to a reference value, and adjusting the inputs to reduce error.
- 📐 PID stands for Proportional, Integral, and Derivative, which are the three methods used to adjust the error signal in a system.
- ⚖️ The Proportional (P) term multiplies the error by a constant to produce an output proportional to the error size.
- 🔢 The Integral (I) term sums the error over time to eliminate small constant errors, adjusting the output accordingly.
- ⚡ The Derivative (D) term reacts to the rate of change of the error, adjusting the output based on how fast the error is changing.
- 🔧 PID controllers are highly efficient and commonly used in industrial applications due to their simplicity and effectiveness.
- 🛠️ You can create simplified versions of a PID controller by setting certain terms to zero, such as a PI controller or a P controller.
- 💡 Simple controllers are preferred for ease of implementation, tuning, and troubleshooting, especially in large projects.
Q & A
What is an open-loop system?
-An open-loop system is one in which inputs act on a plant (or system) to produce an output without any feedback mechanism to adjust based on the output's performance.
Why is open-loop control not ideal in some situations?
-Open-loop control is not ideal when accuracy is important or when the system is subject to changes. For example, if there is an external disturbance like dirt in the robot's wheels, the system cannot adjust to maintain the desired outcome.
What is feedback control?
-Feedback control is a system where the output is measured and compared to a reference signal, and any error between the two is used to adjust the input so that the system meets the desired outcome.
How does a feedback control system handle error?
-A feedback control system compares the measured output with the reference (desired value) and calculates the error. This error is then used to generate an input signal that adjusts the system, reducing the error over time.
What does PID stand for in a PID controller?
-PID stands for Proportional, Integral, and Derivative, which are the three components that determine how the controller processes the error to adjust the system.
What is the role of the proportional term in a PID controller?
-The proportional term multiplies the error by a constant (Kp). The larger the error, the larger the proportional response, which helps reduce the error.
How does the integral term in a PID controller work?
-The integral term sums the error over time and multiplies it by a constant (Ki). This helps eliminate constant errors by making gradual adjustments until the error is reduced to zero.
What does the derivative term do in a PID controller?
-The derivative term takes the rate of change of the error and multiplies it by a constant (Kd). It reacts to how quickly the error is changing, helping the system anticipate and smooth out rapid changes in the error.
Why might a simpler controller be preferable over a more complex one?
-A simpler controller is easier to implement, tune, and troubleshoot, which can save time and money, especially in large projects where different teams need to work together.
Why is PID control so widely used in industrial applications?
-PID control is widely used because it is simple, efficient, and effective in a broad range of applications. It provides a balance between accuracy and simplicity, making it easy to implement and tune while still meeting performance requirements.
Outlines
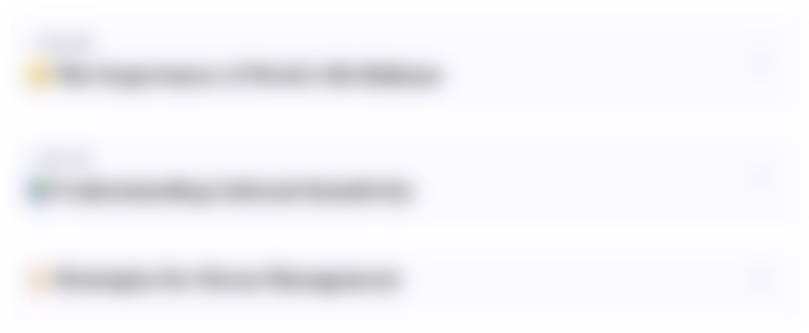
هذا القسم متوفر فقط للمشتركين. يرجى الترقية للوصول إلى هذه الميزة.
قم بالترقية الآنMindmap
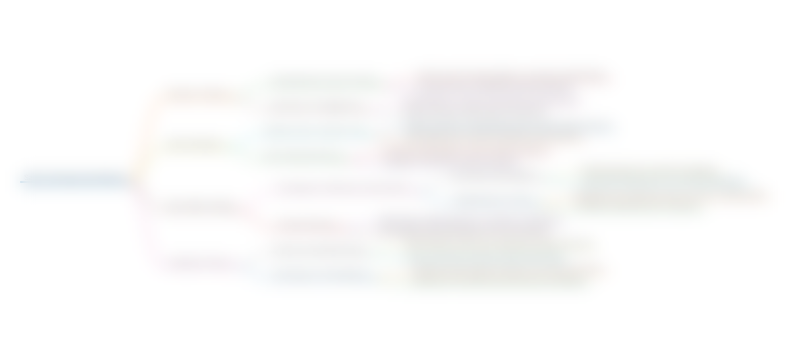
هذا القسم متوفر فقط للمشتركين. يرجى الترقية للوصول إلى هذه الميزة.
قم بالترقية الآنKeywords
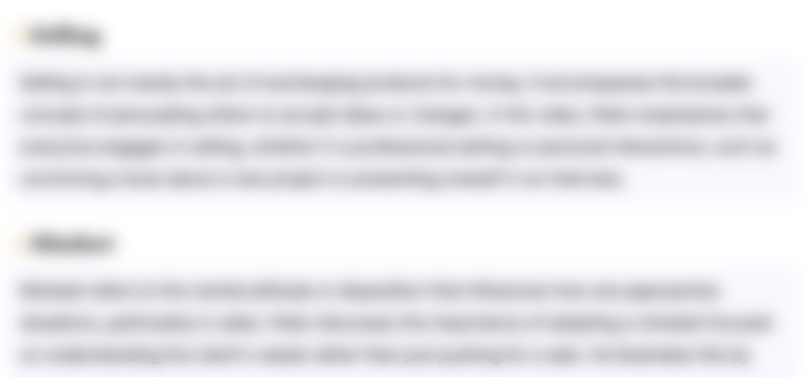
هذا القسم متوفر فقط للمشتركين. يرجى الترقية للوصول إلى هذه الميزة.
قم بالترقية الآنHighlights
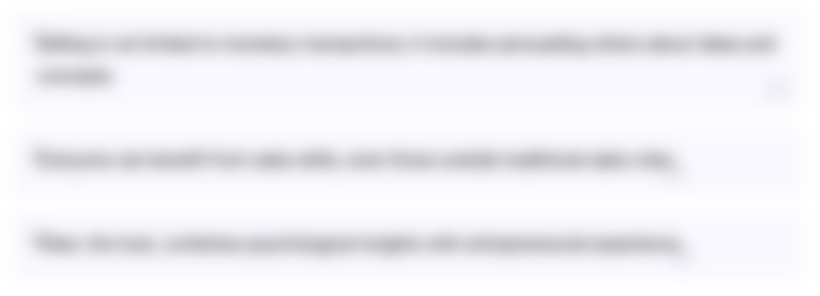
هذا القسم متوفر فقط للمشتركين. يرجى الترقية للوصول إلى هذه الميزة.
قم بالترقية الآنTranscripts
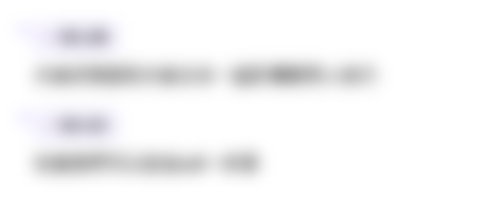
هذا القسم متوفر فقط للمشتركين. يرجى الترقية للوصول إلى هذه الميزة.
قم بالترقية الآنتصفح المزيد من مقاطع الفيديو ذات الصلة
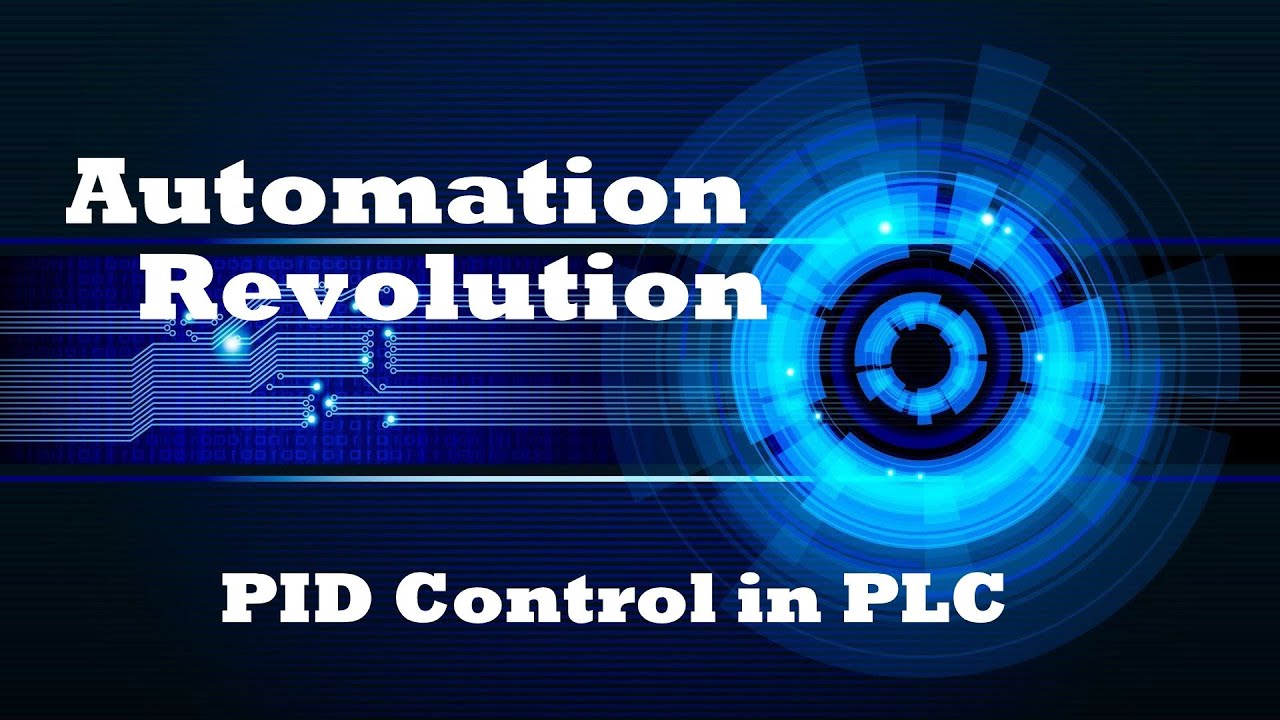
PLC Tutorial 8 : PID Control in Programmable Logic Controller (PLC)
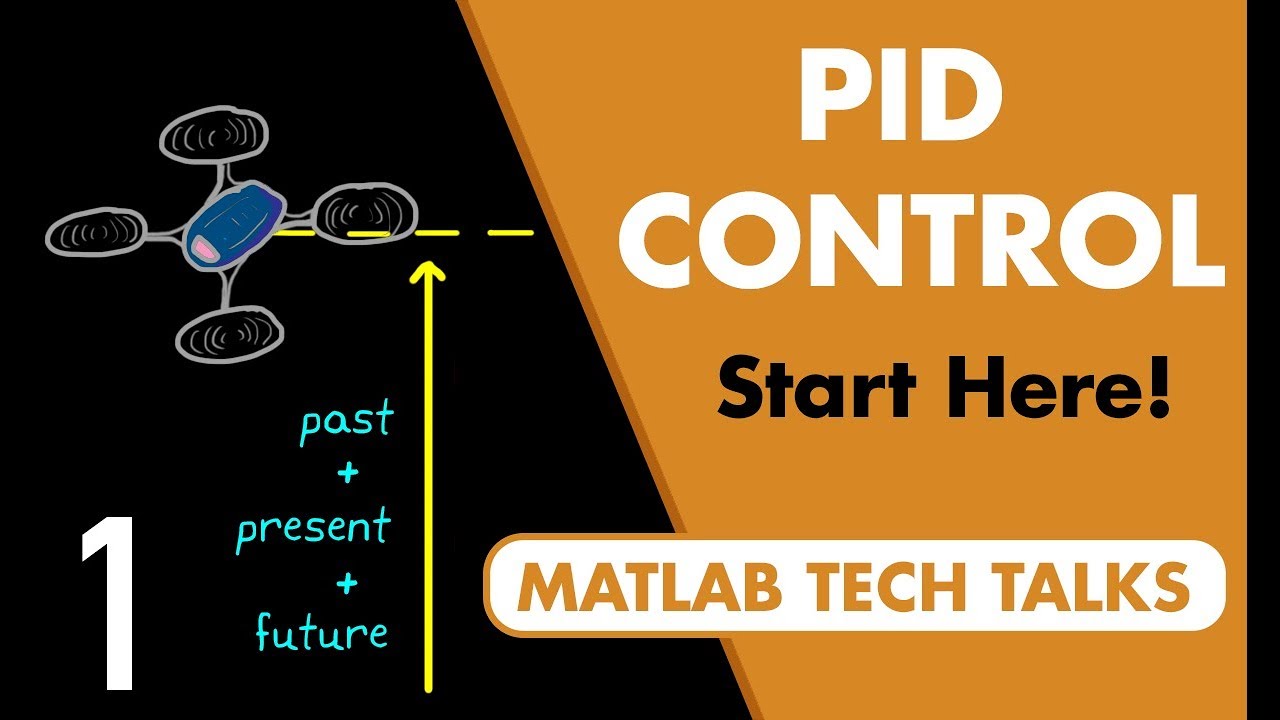
What Is PID Control? | Understanding PID Control, Part 1

Important PID Concepts | Understanding PID Control, Part 7
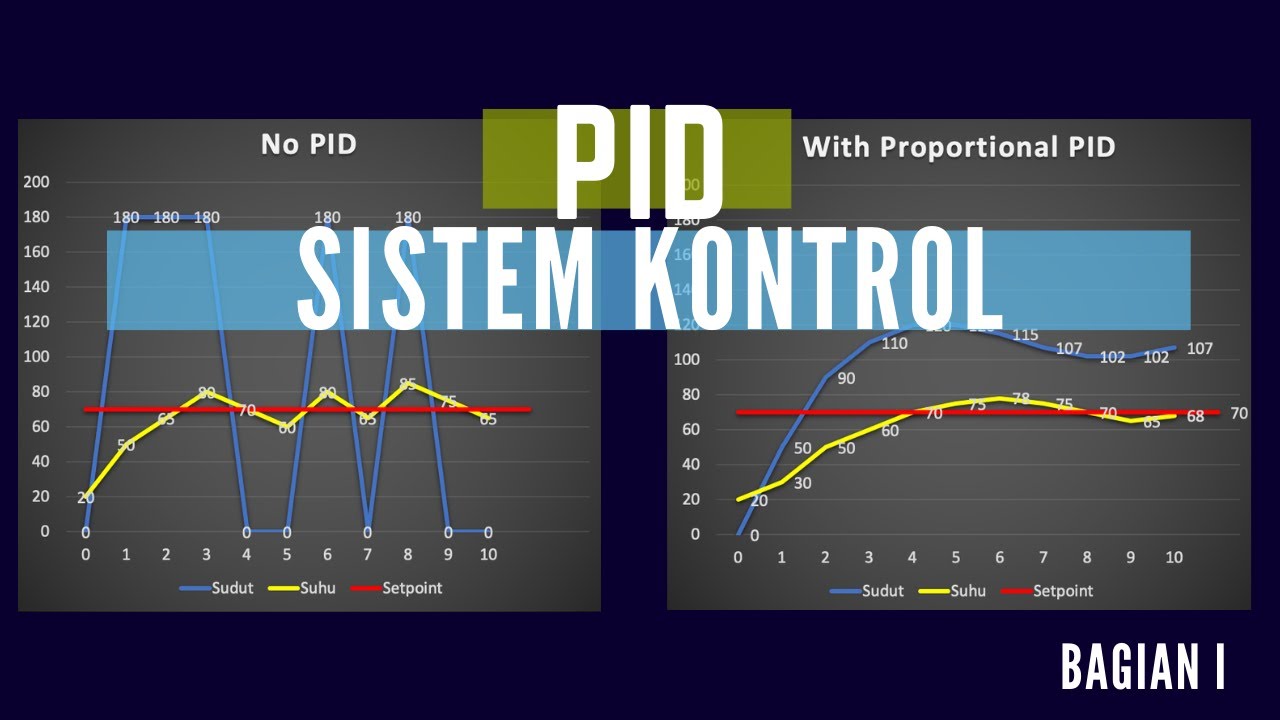
Pengenalan Sistem Kontrol PID Bagian 1
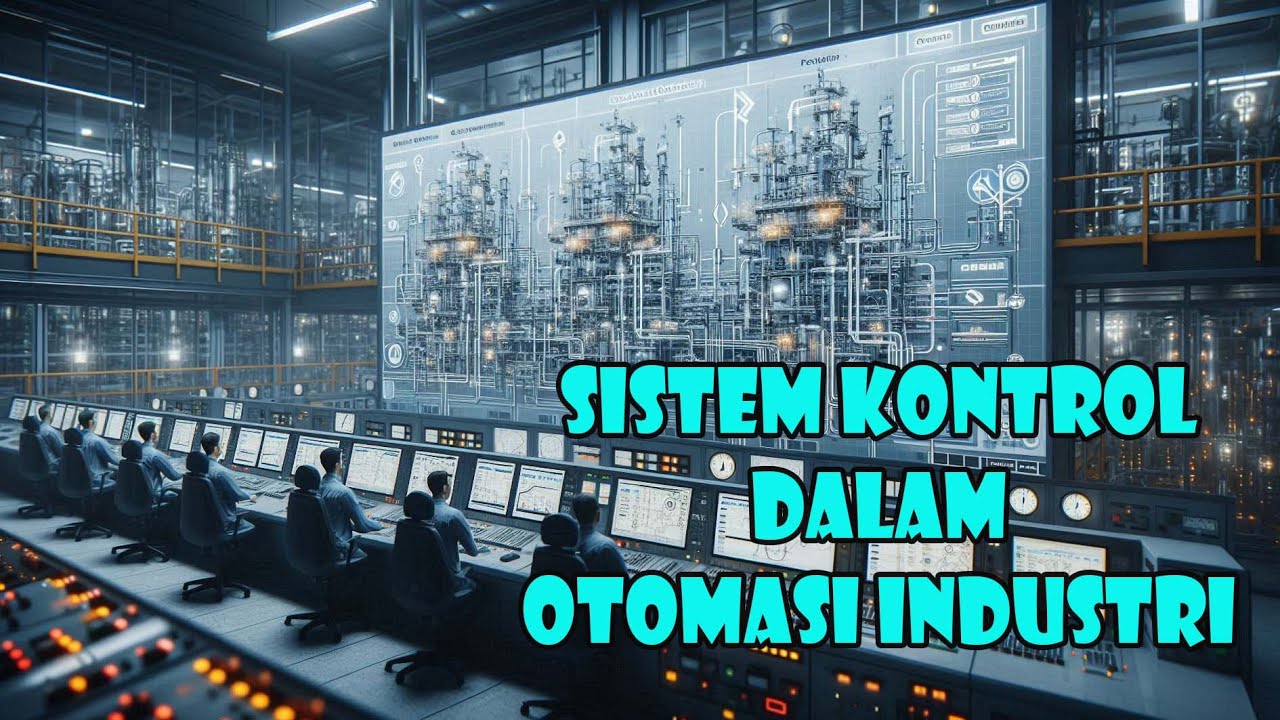
SISTEM KONTROL DALAM OTOMASI INDUSTRI
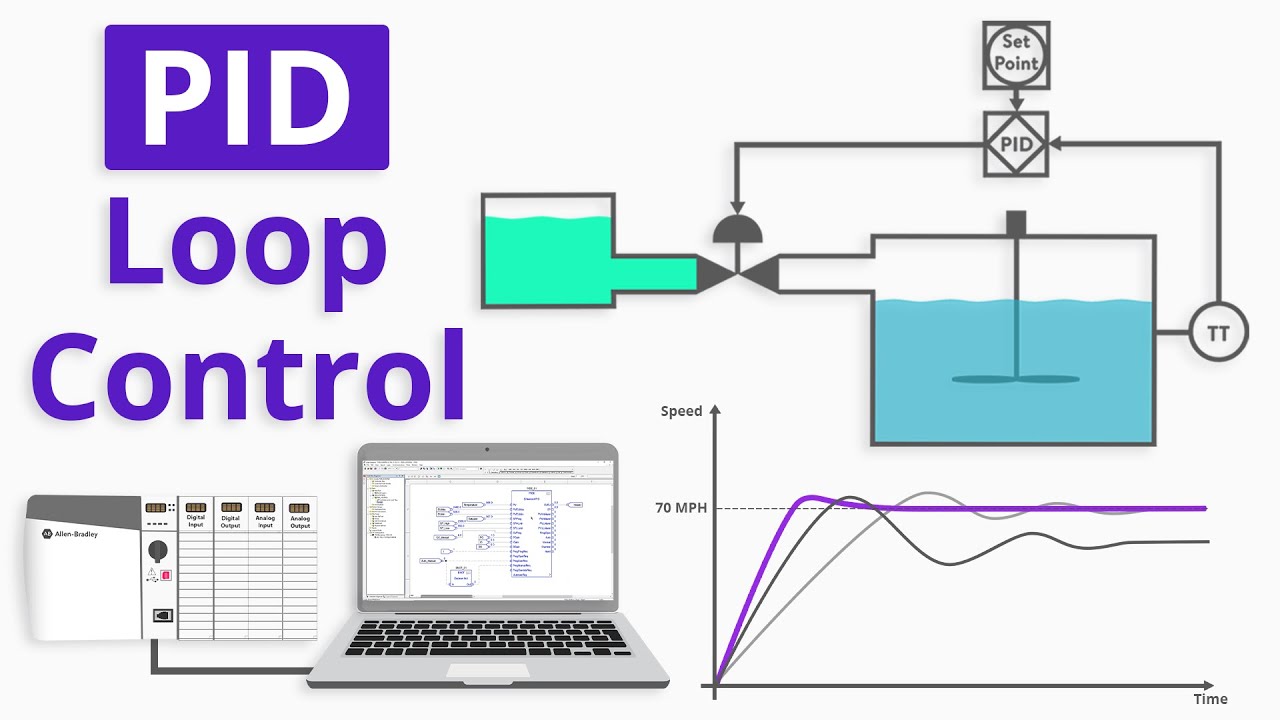
How to Program a Basic PID Loop in ControlLogix
5.0 / 5 (0 votes)