How does a Stepper Motor work?
Summary
TLDRThis video script delves into the intricacies of stepper motors, crucial for precise movements in manufacturing. It explains the variable reluctance stepper motor, highlighting its 30-degree step size and half-stepping technique for finer control. The script then transitions to the hybrid stepper motor, emphasizing its 1.8-degree step size and the role of rotor and stator teeth alignment for high accuracy. Ideal for applications requiring exact movements, stepper motors are showcased as the backbone of automated systems in manufacturing.
Takeaways
- 🤖 Stepper motors are critical in manufacturing for precise and repeatable movements in robotic arms and automated milling machines.
- 🔄 The stepper motor's unique ability to control the angular position of the rotor without a closed feedback loop makes it simple, accurate, and an open-loop system.
- 🧲 Variable reluctance stepper motors are the simplest type, with a rotor made of steel laminations and stator teeth designed to create a specific reluctance for rotor positioning.
- 🔧 The rotor's teeth are intentionally different in number from the stator's to ensure that only one pair of rotor teeth aligns with the stator at a time, facilitating precise movement.
- 🔗 The step size of a basic variable reluctance stepper motor is 30 degrees, derived from the geometric arrangement of the stator and rotor teeth.
- 🎭 Half-stepping can be employed to improve the accuracy of stepper motors by energizing coils in a specific sequence, reducing the step size to 15 degrees.
- 🧭 Hybrid stepper motors are more versatile and commonly used due to their magnetized rotor with toothed steel caps, offering higher precision.
- 🌐 The hybrid motor's rotor has 50 teeth, while the stator has 48 teeth, arranged in a way that allows for a 1.8-degree step size due to the clever arrangement of rotor and stator teeth.
- 🔌 The stator coils in a hybrid stepper motor are connected to form two independent sets, which when energized, create a magnetic pattern that aligns with the rotor's poles.
- 🔁 By alternating the energizing of the stator coils and their polarity, the rotor is made to move in precise 1.8-degree increments, achieving highly accurate motion control.
- 🛠️ Half-stepping can also be applied to hybrid stepper motors to further enhance the step angle resolution, providing even finer control over the motor's movement.
Q & A
How does a stepper motor enable precise control in manufacturing processes?
-Stepper motors enable precise control by allowing the angular position of the rotor to be controlled without a closed feedback loop, making them simple, accurate, and part of an open-loop system.
What is the significance of the rotor's angular position in a stepper motor?
-The angular position of the rotor is significant because it determines the exact movement of the motor, allowing for precise and controlled motion in applications such as robotic arms and milling machines.
How does the variable reluctance type of stepper motor work?
-The variable reluctance stepper motor works by energizing different coils to create a magnetic field that attracts the rotor to the position of least reluctance, resulting in a stepwise movement of the rotor.
What is the step size of a variable reluctance stepper motor with six stator teeth and three energizable coils?
-The step size of this motor is 30 degrees, as the rotor moves to align with the stator teeth when the coils are energized in sequence.
How can the accuracy of a variable reluctance stepper motor be improved?
-The accuracy can be improved to 15 degrees by using a technique called half-stepping, where two coils are energized simultaneously, causing the rotor to move to a position between the full steps.
What is the difference between a variable reluctance motor and a hybrid stepper motor?
-A variable reluctance motor relies on the magnetic reluctance to move the rotor, while a hybrid stepper motor has a rotor with actual magnets and toothed steel caps, providing higher accuracy and versatility.
How does the rotor's tooth arrangement in a hybrid stepper motor contribute to its accuracy?
-The rotor's tooth arrangement, along with the stator teeth arrangement, ensures that the rotor can align with the stator in a way that minimizes the magnetic reluctance, resulting in precise and controlled motion.
What is the step size of a hybrid stepper motor with a 1.8-degree step size?
-The step size of a hybrid stepper motor with a 1.8-degree step size is 1.8 degrees, which is achieved by the rotor moving to align with the magnetic field created by the energized stator coils.
How does half-stepping improve the step angle resolution of a hybrid stepper motor?
-Half-stepping improves the step angle resolution by energizing the stator coils in a way that the rotor moves to intermediate positions between the full steps, effectively halving the step size and increasing the resolution.
Why are hybrid stepper motors ideal for applications requiring precise movements and simple control?
-Hybrid stepper motors are ideal for such applications because they offer high accuracy, consistent performance, and the ability to control the motor's position with simple open-loop control systems.
How does the arrangement of the north and south end caps in a hybrid stepper motor affect its operation?
-The arrangement of the north and south end caps ensures that the rotor's magnetic poles are correctly aligned with the stator's magnetic field, which is crucial for the motor's precise and controlled movement.
Outlines
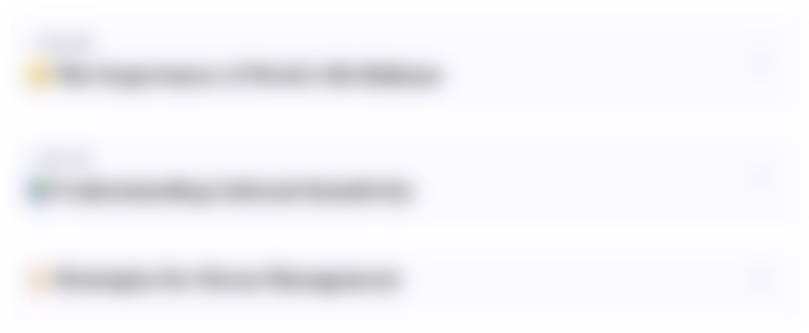
هذا القسم متوفر فقط للمشتركين. يرجى الترقية للوصول إلى هذه الميزة.
قم بالترقية الآنMindmap
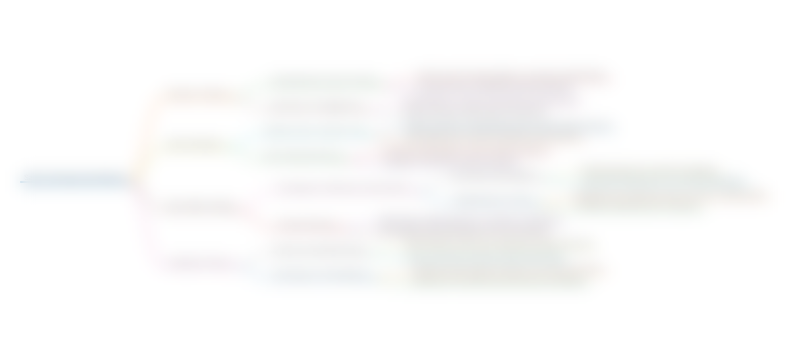
هذا القسم متوفر فقط للمشتركين. يرجى الترقية للوصول إلى هذه الميزة.
قم بالترقية الآنKeywords
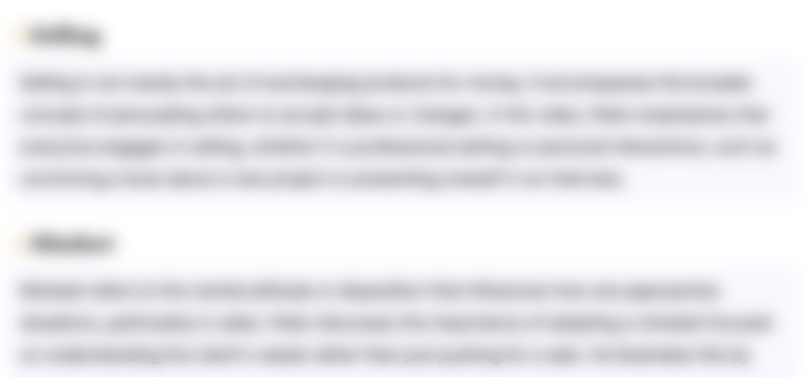
هذا القسم متوفر فقط للمشتركين. يرجى الترقية للوصول إلى هذه الميزة.
قم بالترقية الآنHighlights
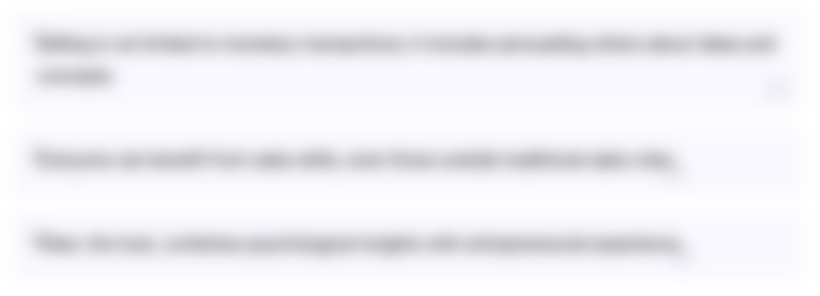
هذا القسم متوفر فقط للمشتركين. يرجى الترقية للوصول إلى هذه الميزة.
قم بالترقية الآنTranscripts
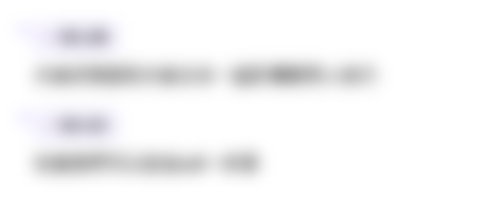
هذا القسم متوفر فقط للمشتركين. يرجى الترقية للوصول إلى هذه الميزة.
قم بالترقية الآن5.0 / 5 (0 votes)