ELECTRON BEAM MACHINING PROCESS (EBM): Construction and Working of electron beam machining process.
Summary
TLDRElectron Beam Machining (EBM) is a high-tech, non-conventional process for shaping hard and brittle materials. It operates by converting electron kinetic energy into heat, vaporizing material from the workpiece surface. The process requires a vacuum to prevent energy loss and utilizes advanced components like an electron gun, magnetic lenses, and a deflecting coil for precision. EBM excels in micro-machining, creating small holes, and working with materials of low thermal conductivity and high melting points. Despite its advantages, such as good surface finish and no tool wear, it has limitations, including a low metal removal rate and high equipment costs.
Takeaways
- ⚙️ Electron beam machining (EBM) is a non-conventional process for machining very hard and brittle materials.
- 💡 The process involves converting the kinetic energy of electrons into heat energy to vaporize the workpiece surface.
- 📽️ EBM is similar to laser beam machining but uses an electron beam instead of a laser.
- 🔬 EBM works on the principle of converting electron kinetic energy into heat energy when electrons impinge on the workpiece.
- ⚡ The process requires a vacuum to prevent electrons from colliding with air particles and losing energy.
- 🛠️ EBM equipment is similar to electron beam welding machines, utilizing high voltage to accelerate electrons to a significant fraction of the speed of light.
- 🔧 Key components include the electron gun, cathode filament made of tungsten, anode, magnetic lenses, deflecting coil, and workpiece holding device.
- 🔍 EBM is used for micro-machining operations like drilling, perforating, slotting, and scribing on thin materials.
- 📏 Advantages of EBM include machining very hard materials, achieving close dimensional tolerance, good surface finish, minimal heat-affected zone, and no physical contact between tool and workpiece.
- ⚠️ Disadvantages include low metal removal rate, vacuum requirement limiting workpiece size, suitability for small cuts only, and high equipment cost.
Q & A
What is Electron Beam Machining (EBM)?
-Electron Beam Machining (EBM) is a non-conventional machining process used for machining very hard and brittle materials that cannot be machined by conventional methods. It works by converting the kinetic energy of electrons into heat energy, which evaporates the workpiece surface.
How does the electron beam machining process work?
-In EBM, the kinetic energy of electrons is converted into heat energy by impinging fast-moving electrons on the workpiece surface. This heat energy vaporizes the workpiece surface, similar to laser beam machining.
Why is a vacuum necessary for EBM?
-A vacuum is required for EBM because electrons will collide with particles in the air and lose their energy if conducted in a non-vacuum environment.
What is the role of the electron gun in EBM?
-The electron gun is a cathode ray tube that generates electrons, accelerates them at a very high speed, and focuses them on the required spot on the workpiece.
What material is typically used for the cathode filament in the electron gun?
-The cathode filament is made up of tungsten, which is heated to about 2500 degrees Celsius to accelerate electron emission by thermionic reaction.
How do magnetic lenses contribute to the EBM process?
-Magnetic lenses reduce the divergence of the electron beam and allow only a convergent beam to pass to the next stage, thus obtaining a highly focused beam of electrons.
What is the purpose of the deflecting coil in EBM?
-The deflecting coil prevents the beam from deflecting, thus forming a high-intensity beam that is focused on the workpiece.
What are the typical applications of EBM?
-EBM is mainly used for micro machining operations on thin materials, such as drilling, perforating, slotting, and scribing. It is also used for making fine gas orifices in space nuclear reactors and gas turbines, and for producing very small diameter holes.
What are some advantages of using EBM?
-Advantages of EBM include the ability to machine very hard and heat-resistant materials, achieving close dimensional tolerances, producing a good surface finish, and having a minimal heat-affected zone. Additionally, there is no physical contact between the tool and the workpiece.
What are some disadvantages of EBM?
-Disadvantages of EBM include a low metal removal rate (MRR), the requirement for a vacuum which limits the size of the workpiece, the ability to only make small cuts, and the high cost of equipment.
How does EBM compare to laser beam machining in terms of process?
-Both EBM and laser beam machining involve the conversion of energy to vaporize the workpiece surface, but EBM uses a high-energy electron beam instead of a laser.
Outlines
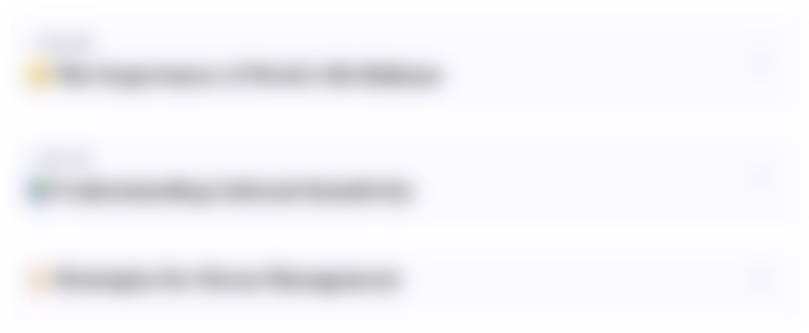
此内容仅限付费用户访问。 请升级后访问。
立即升级Mindmap
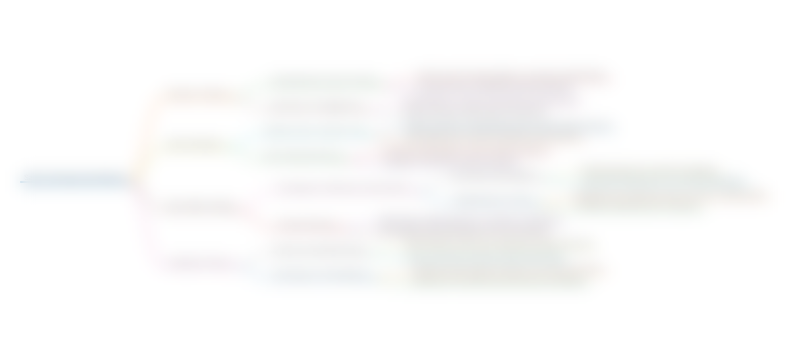
此内容仅限付费用户访问。 请升级后访问。
立即升级Keywords
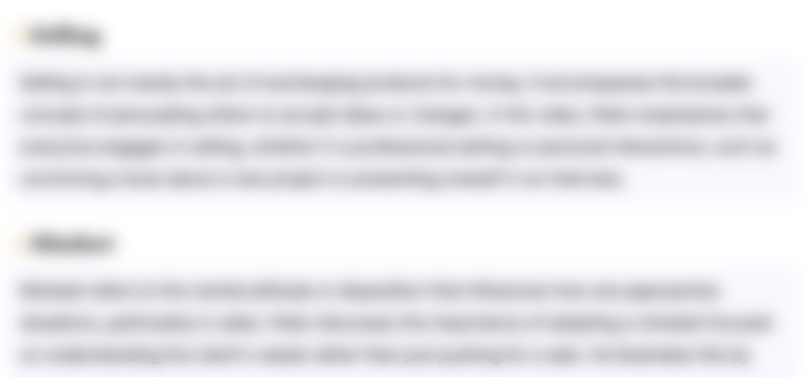
此内容仅限付费用户访问。 请升级后访问。
立即升级Highlights
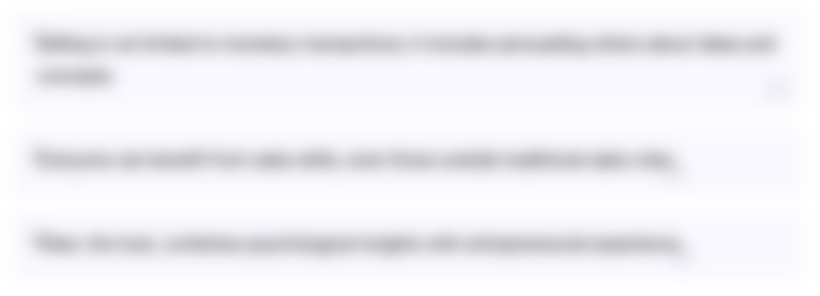
此内容仅限付费用户访问。 请升级后访问。
立即升级Transcripts
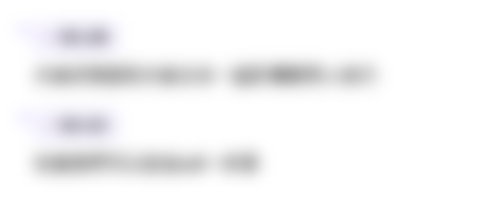
此内容仅限付费用户访问。 请升级后访问。
立即升级浏览更多相关视频
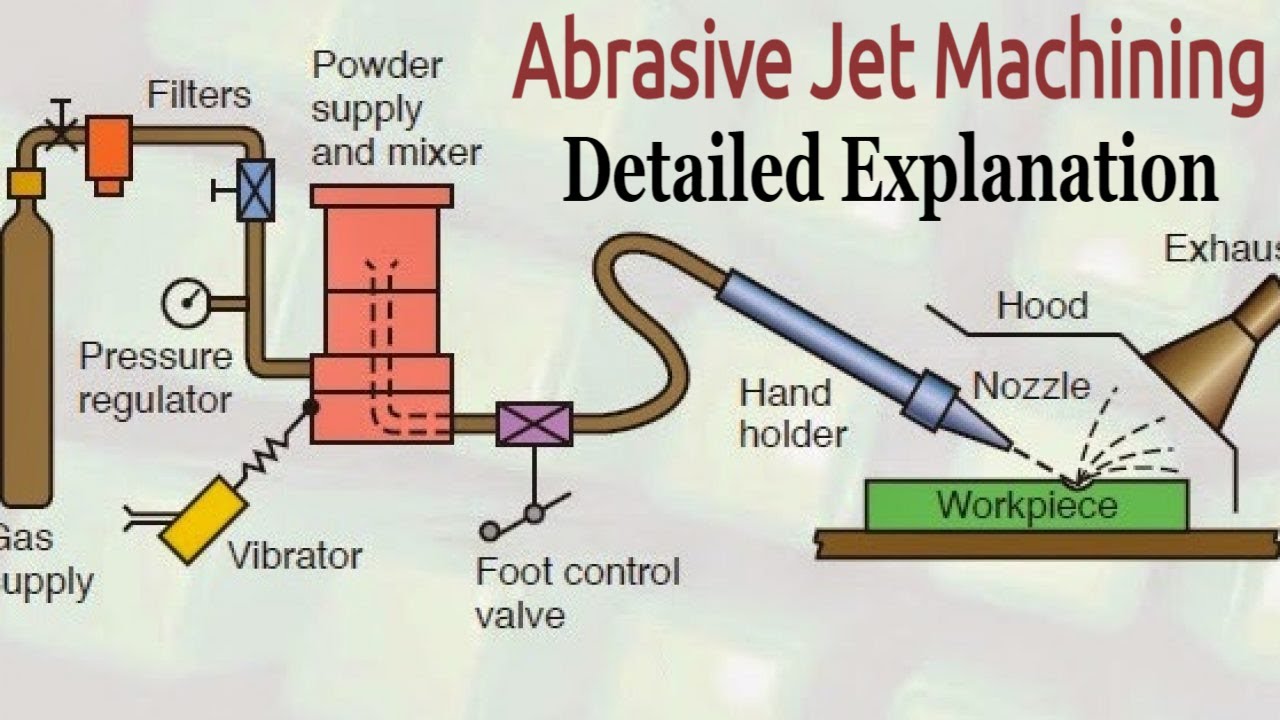
How an Abrasive Jet Machining Works?
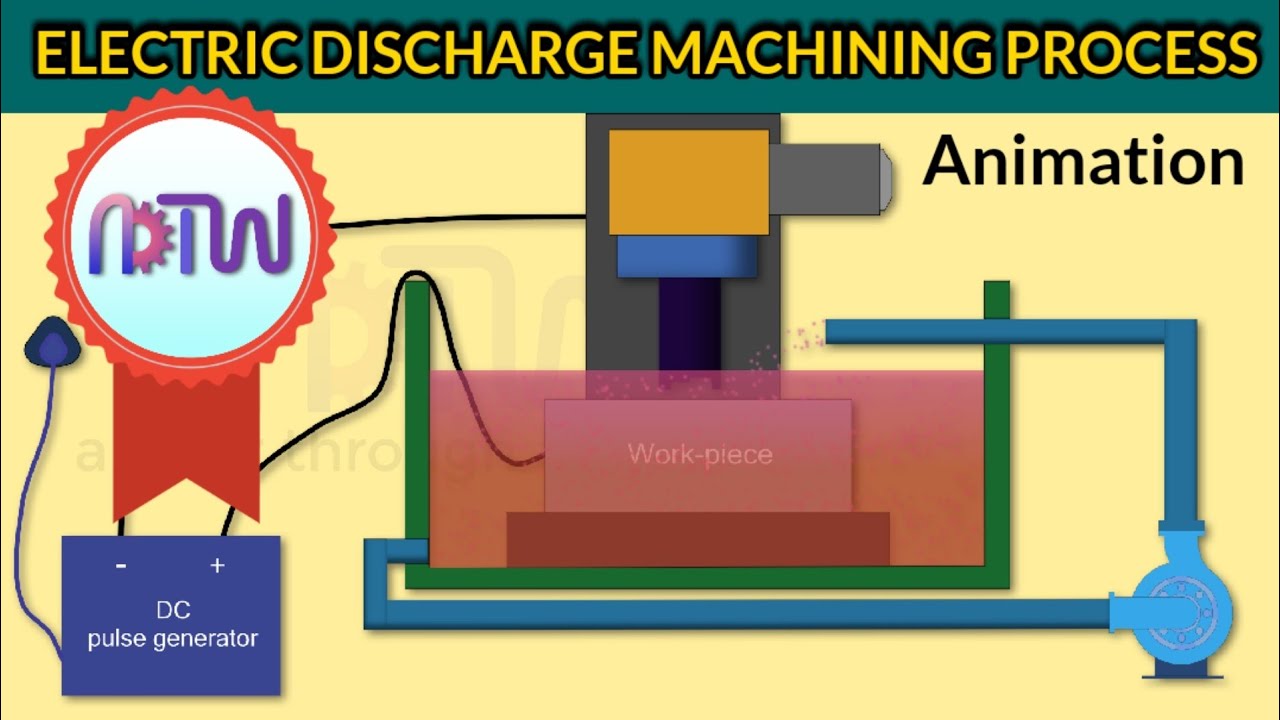
ELECTRIC DISCHARGE MACHINING PROCESS (Animation): How electric discharge maching works

WATER JET MACHINE PROCESS : Working of abrasive water Jet machining process (animation).
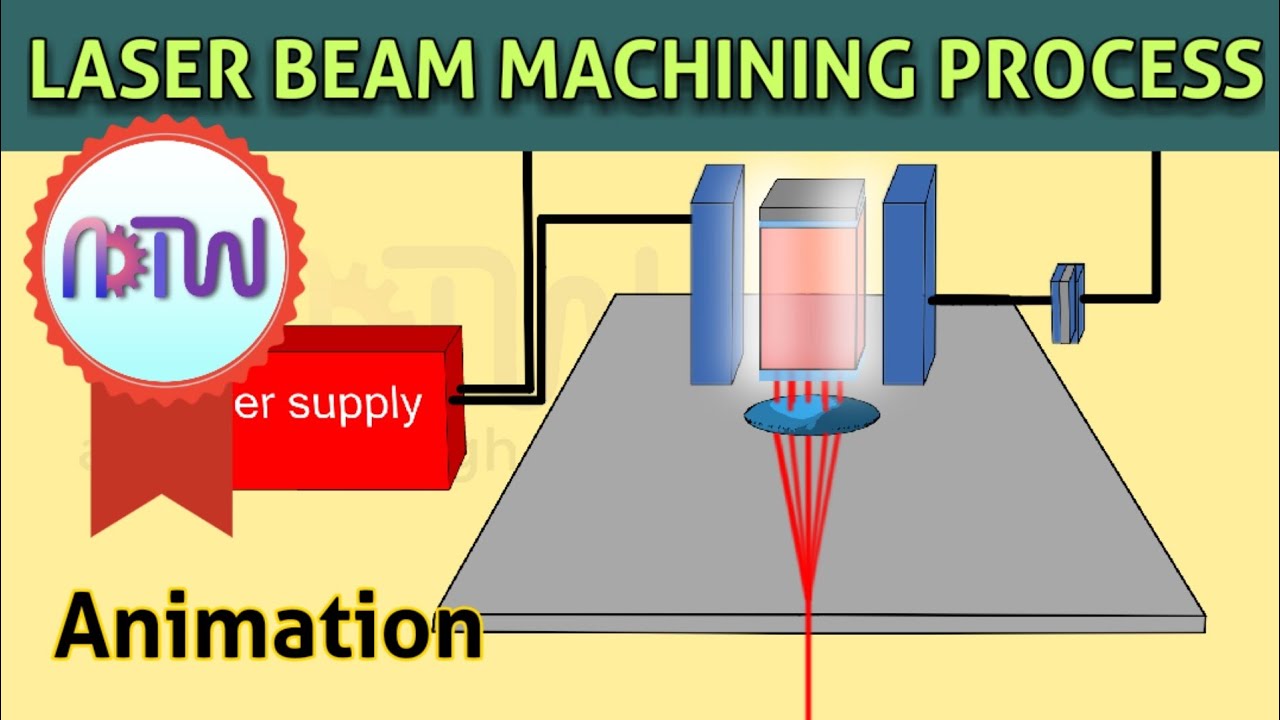
LASER BEAM MACHINING PROCESS (Animation): Working of LASER beam machining process.
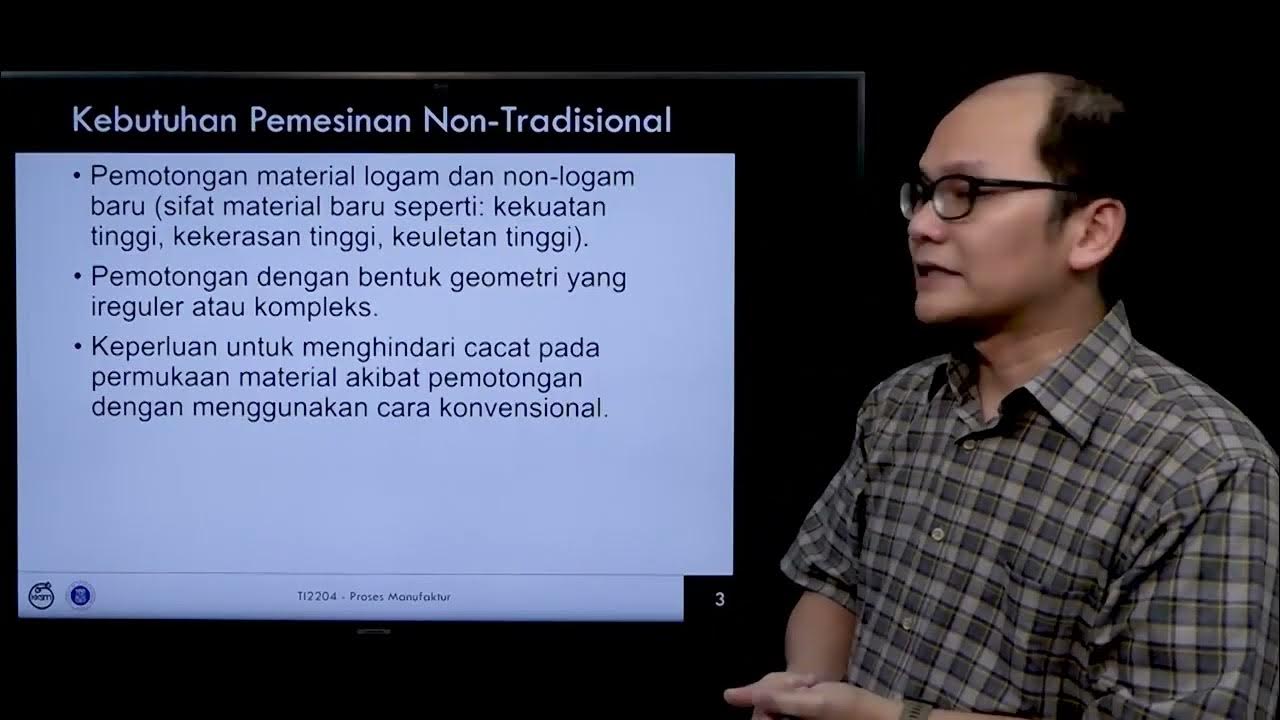
Proses Pemesinan Non Tradisional part 1
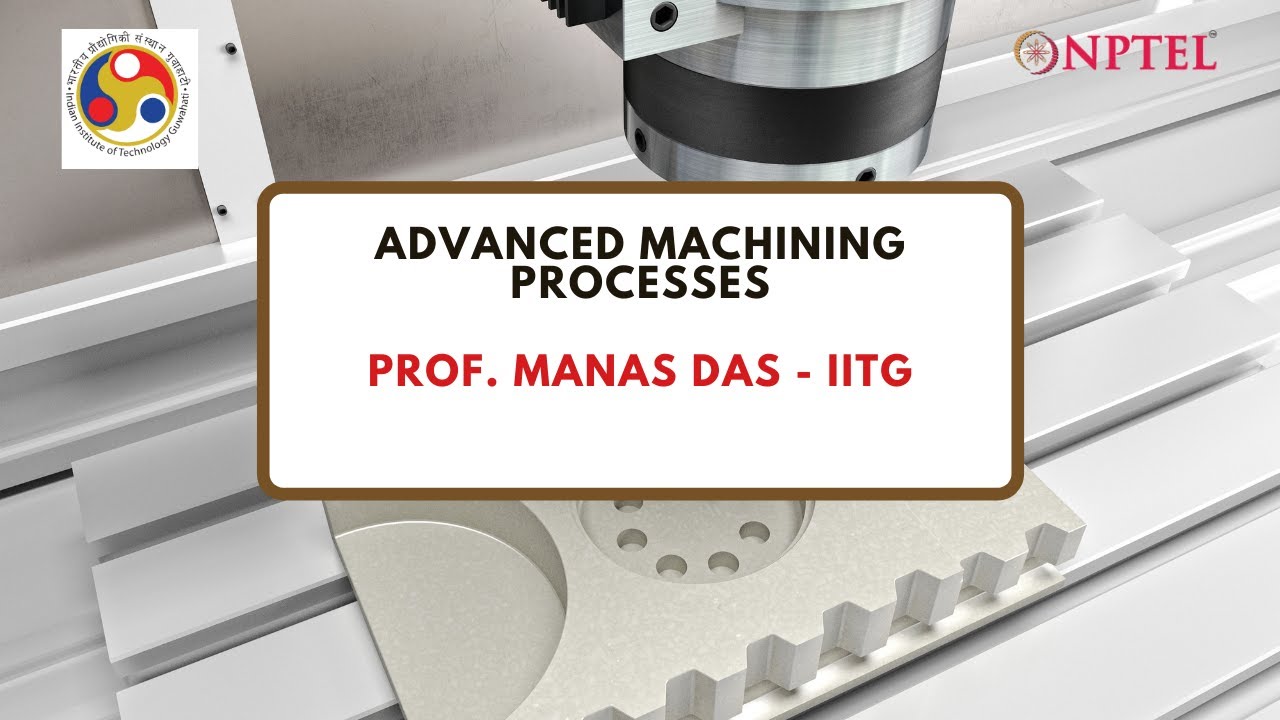
Introduction: Advanced Machining Processes
5.0 / 5 (0 votes)