WATER JET MACHINE PROCESS : Working of abrasive water Jet machining process (animation).
Summary
TLDRThe video script delves into the water jet machining process, a versatile non-conventional technique that utilizes high-velocity water jets for cutting materials. It can be used for both soft materials like plastic and rubber, and hard materials such as metals and granite with the addition of abrasive particles. The script covers the working principle, construction, operation, advantages, and disadvantages of water jet machining, highlighting its precision, cleanliness, and environmental friendliness. Applications range from automotive to aerospace industries, and it's also used for paint removal and stress peening. The script provides a comprehensive guide for those interested in this efficient and eco-friendly machining method.
Takeaways
- 💧 Water jet machining uses a high-velocity jet of water to cut materials, and is also known as water jet cutting.
- 🔨 For cutting harder materials, abrasive water jet machining is used, which mixes abrasive particles like garnet or aluminium oxide with water.
- 🏗️ The setup for water jet machining includes a water reservoir, hydraulic pump, intensifier, accumulator, control valve, flow regulator, mixing chamber, and nozzle.
- 🚀 The hydraulic intensifier increases water pressure from around 5 bars to 3000-4000 bars, which is crucial for the cutting process.
- 🔄 The accumulator helps to maintain a consistent high pressure by storing and supplying pressurized water as needed.
- 💦 The control valve and flow regulator manage the pressure and flow of the water jet, ensuring precision in cutting.
- 🔩 The nozzle, often made of ruby or diamond, converts the high pressure of water into a high-velocity stream for cutting.
- 🗑️ The drain and catcher system separates debris and particles from the water after machining, allowing for water reuse.
- 🛠️ Water jet machining is capable of producing complex cuts and is clean, dust-free, and has low operating costs due to the lack of moving parts.
- ♻️ It is environmentally friendly, producing no pollution or toxic byproducts, and can achieve high precision with tolerances of ±0.005 inches.
- 🚫 Disadvantages include the inability to machine very thick materials and the high initial cost of the equipment.
Q & A
What is water jet machining also known as?
-Water jet machining is also known as water jet cutting.
What type of materials can be cut using water jet machining?
-Water jet machining can cut both softer materials like plastic, rubber, or wood, and harder materials like metals or granite when an abrasive material is mixed with the water.
What is the term used when an abrasive material is mixed with water in the machining process?
-When an abrasive material is mixed with water for the machining process, it is called abrasive water jet machining.
What are the common abrasive particles used in abrasive water jet machining?
-The most commonly used abrasive particles in abrasive water jet machining are garnet and aluminium oxide, although sand and glass beads are also used.
What is the function of the abrasive particles in water jet machining?
-The function of the abrasive particles is to enhance the cutting ability of the water jet.
What are the main components of a water jet machining setup?
-The main components of a water jet machining setup include a water reservoir, hydraulic pump, booster, hydraulic intensifier, accumulator, control valve, flow regulator or valve, mixing chamber or tube, nozzle, and a drain and catcher system.
How does the hydraulic intensifier increase the pressure of water?
-The hydraulic intensifier increases the pressure of water from about four to three thousand to four thousand bar.
What is the purpose of the accumulator in water jet machining?
-The accumulator stores high pressurized water temporarily and supplies it when a large amount of pressure energy is required, helping to eliminate pressure fluctuation during the machining process.
What is the typical velocity of the water jet that comes out of the nozzle?
-The typical velocity of the water jet coming out of the nozzle is about one thousand meters per second.
What are some of the advantages of water jet machining?
-Advantages of water jet machining include the ability to produce complex cuts, a clean and dust-free machining area, low operating and maintenance costs, negligible thermal damage to the workpiece, the ability to cut a wide range of materials, being environmentally friendly, and high precision machining.
What are some of the disadvantages of water jet machining?
-Disadvantages of water jet machining include the inability to machine very thick materials and the high initial cost of the equipment.
In which industries is water jet machining commonly used?
-Water jet machining is commonly used in various industries such as mining, automotive, and aerospace for cutting, shaping, and other operations.
What are some of the materials commonly machined by water jet?
-Materials commonly machined by water jet include rubber, textiles, plastics, foam, leather, composites, tile, stone, glass, paper, and more.
What are some additional applications of high pressure water jet besides the machining process?
-Besides the machining process, high pressure water jet is used in paint removal, surgery, cleaning, and peening to remove residual stress.
Outlines
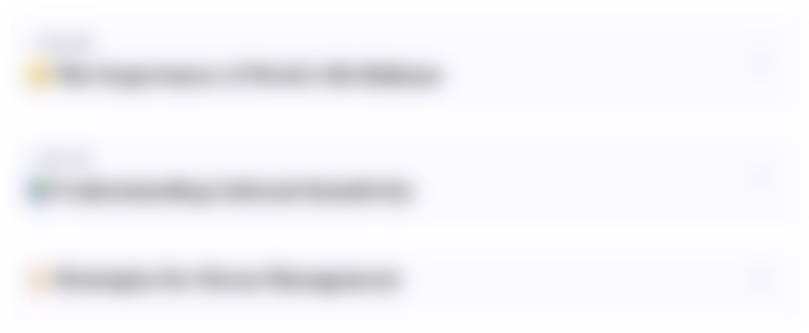
This section is available to paid users only. Please upgrade to access this part.
Upgrade NowMindmap
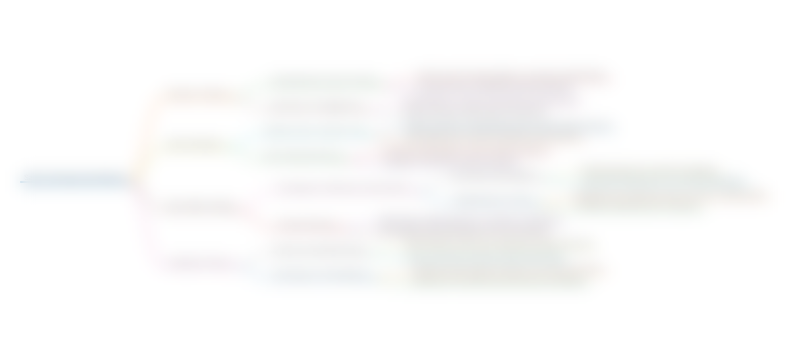
This section is available to paid users only. Please upgrade to access this part.
Upgrade NowKeywords
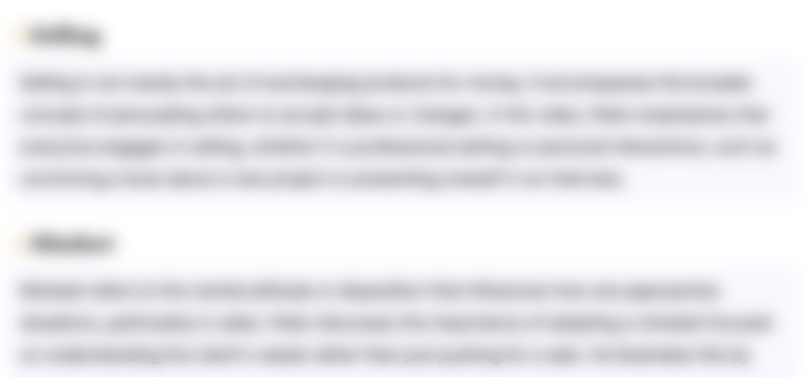
This section is available to paid users only. Please upgrade to access this part.
Upgrade NowHighlights
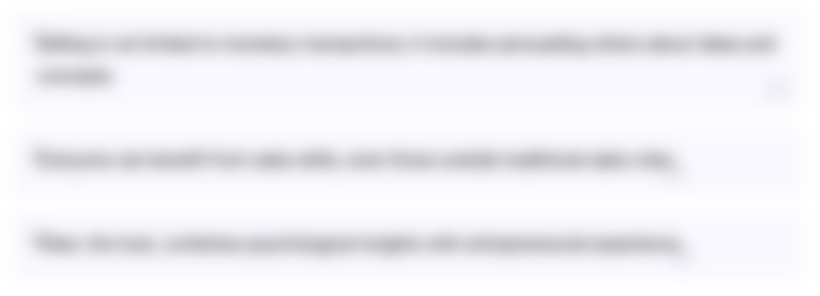
This section is available to paid users only. Please upgrade to access this part.
Upgrade NowTranscripts
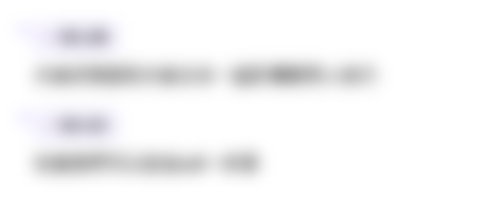
This section is available to paid users only. Please upgrade to access this part.
Upgrade NowBrowse More Related Video

Materiais e Processos de Fabricação para Engenharia de Produção: Usinagem não convencional
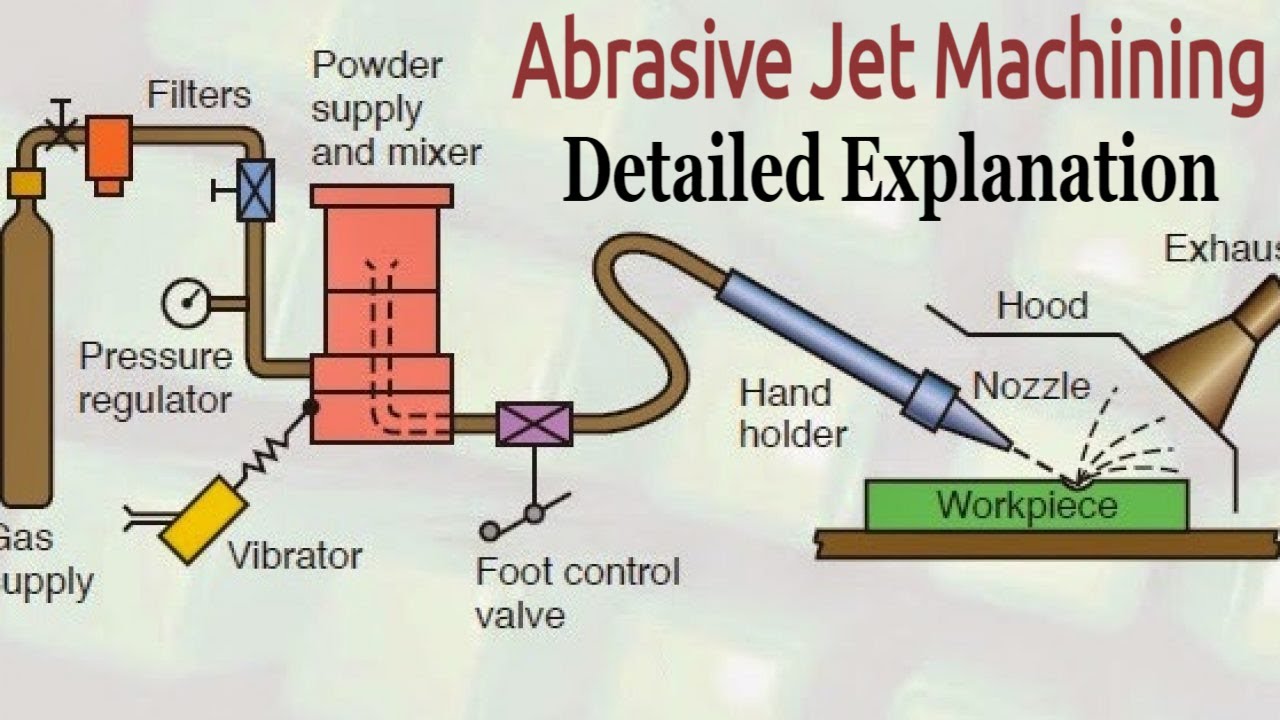
How an Abrasive Jet Machining Works?
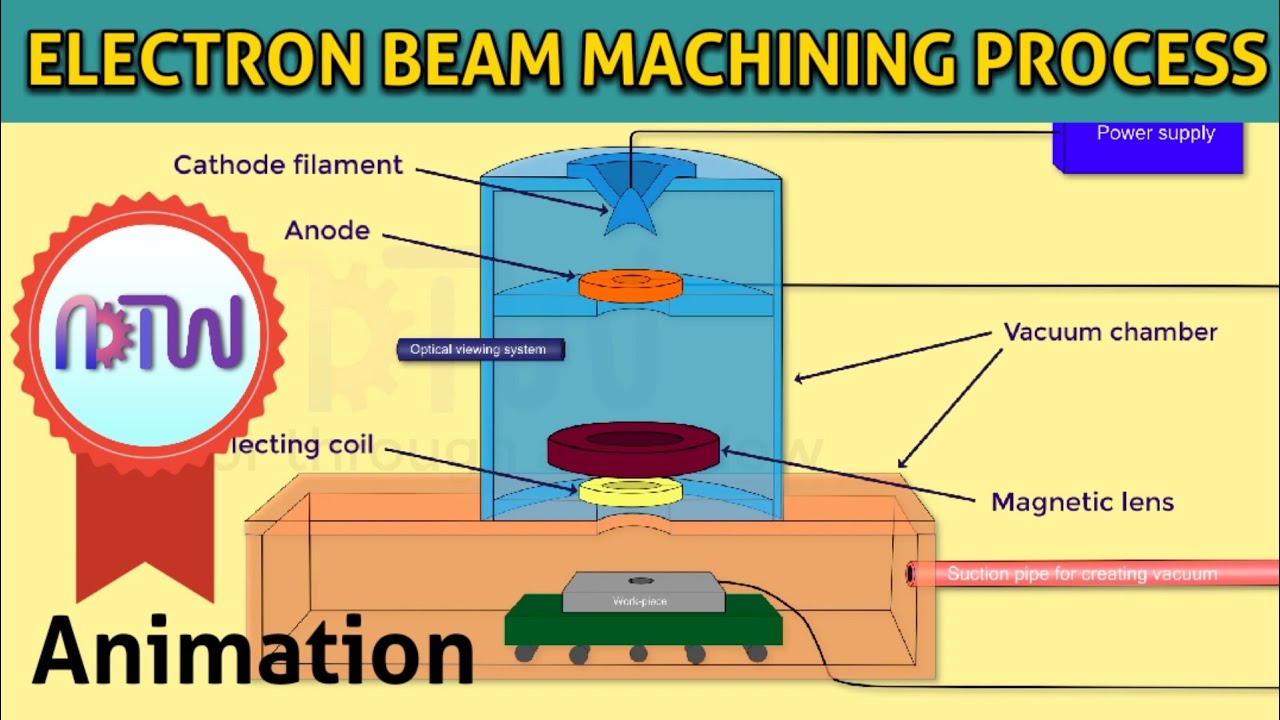
ELECTRON BEAM MACHINING PROCESS (EBM): Construction and Working of electron beam machining process.

How Does a Waterjet Work? It Slices Steel with Water!
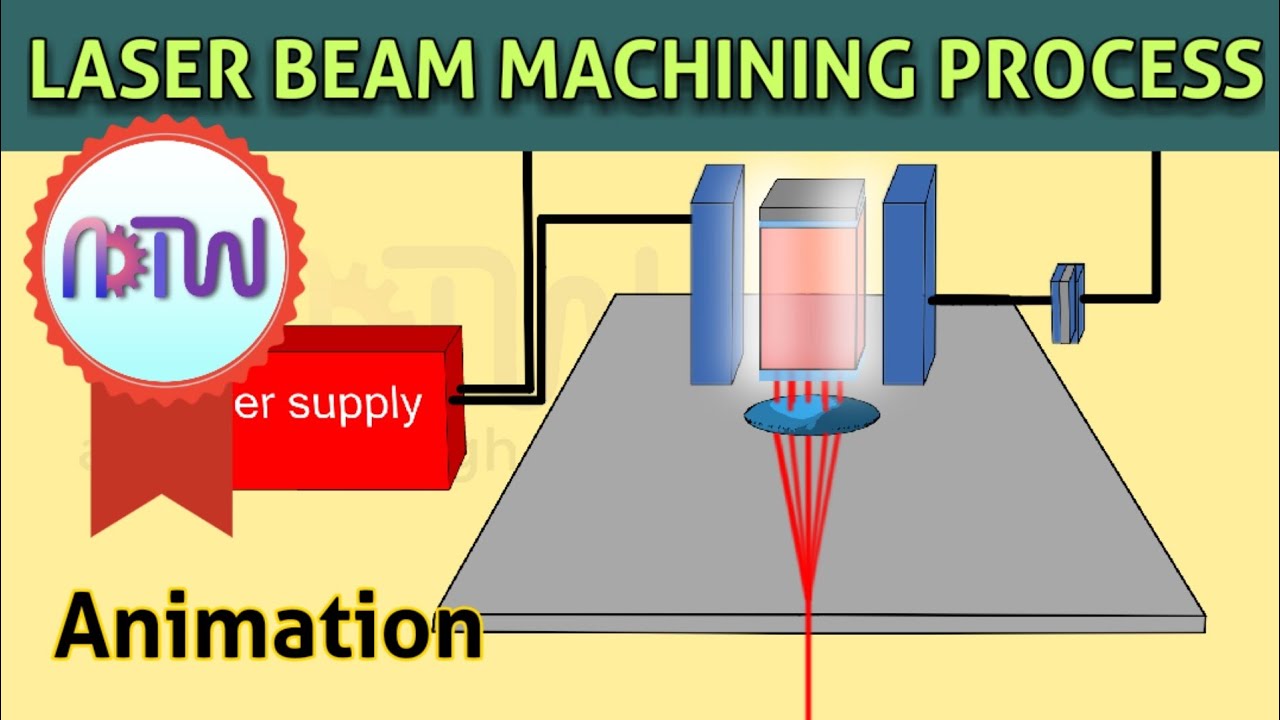
LASER BEAM MACHINING PROCESS (Animation): Working of LASER beam machining process.
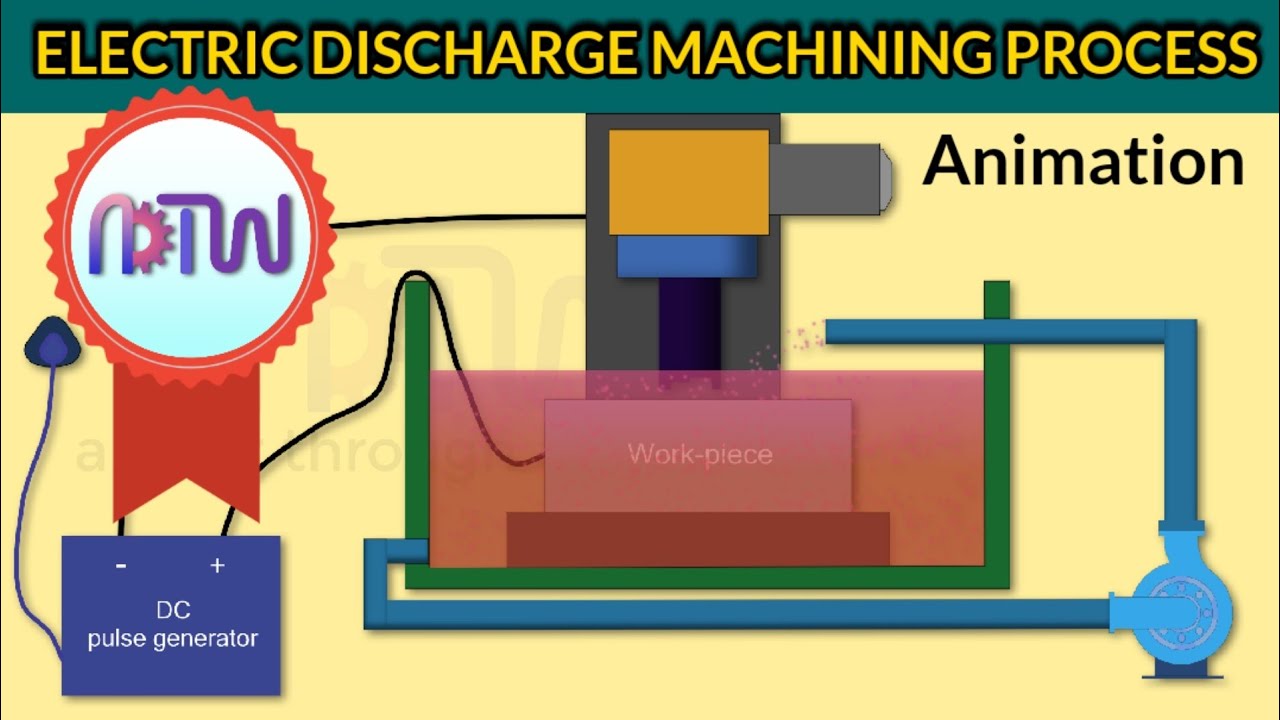
ELECTRIC DISCHARGE MACHINING PROCESS (Animation): How electric discharge maching works
5.0 / 5 (0 votes)