Processos de Fabricacao - Soldagem por resistência
Summary
TLDRThis video lesson introduces resistance welding, explaining its fundamental principle—heat generation through electrical resistance—used to fuse metal parts. The process relies on electric current, pressure, and time to create strong welds. Different methods, including seam, spot, projection, and butt welding, are explored, highlighting their versatility across various industries. The video also covers essential welding equipment, such as power sources, copper alloy electrodes, and pressure systems. Finally, the lesson emphasizes the importance of controlling welding parameters, ensuring high-quality welds. It concludes by encouraging further study and mastery of the subject through course materials.
Takeaways
- 😀 Resistance welding generates heat through electric current encountering resistance in the material, transforming electrical energy into thermal energy.
- 😀 The process relies on three key factors: electric current, heat generation, and pressure applied to the materials being welded.
- 😀 The Joule effect (resistive heating) is the fundamental principle behind resistance welding, which occurs when electric current passes through a resistant material, generating heat.
- 😀 Resistance welding is a versatile process used across various industries and includes multiple welding techniques like spot, seam, projection, butt, and flash welding.
- 😀 In resistance welding, electrodes are used to pass electric current through the materials being welded, causing localized heating at the contact points.
- 😀 Different resistance welding processes are suited for specific applications, such as seam welding for continuous joints and projection welding for multiple points of contact.
- 😀 The key to a successful weld is not only the heat generated but also the pressure exerted on the materials, which ensures a solid bond.
- 😀 The equipment for resistance welding includes a power source (transformer and rectifier), electrodes, a mechanical system for applying pressure, and a cooling system to prevent overheating.
- 😀 The welding process can be customized based on the materials, their thickness, and the required mechanical properties, making resistance welding highly adaptable.
- 😀 The operator plays a crucial role in adjusting parameters like current intensity, pressure, and time to ensure a quality weld and avoid defects.
- 😀 Resistance welding is widely used in manufacturing sectors like automotive, aerospace, and construction due to its efficiency and the precision it offers in joining metal parts.
Q & A
What is resistance welding, and how does it differ from other welding processes?
-Resistance welding is a welding process where heat is generated by the resistance to electric current passing through the workpieces. Unlike other welding processes that rely on fusion through electric arcs or gas, resistance welding uses localized heat in a small contact area to create the weld, along with applied pressure.
What is the principle behind resistance welding?
-The principle of resistance welding is based on the conversion of electrical energy into heat due to the electrical resistance of the materials. This heat, combined with pressure applied to the parts being welded, causes the materials to fuse at the interface.
What role does resistivity play in resistance welding?
-Resistivity refers to the material’s ability to resist the passage of electric current. Metals with higher resistivity, like steel, generate more heat when current passes through them, which is essential for the welding process. Conversely, metals with low resistivity, like copper, conduct current efficiently and are not typically used for welding.
Why is pressure an important factor in resistance welding?
-Pressure is crucial in resistance welding because, while heat is generated at the interface of the welded parts, the pressure ensures the parts are held together firmly to create a strong bond. Without proper pressure, the weld may not form effectively.
What types of resistance welding processes are covered in the script?
-The script discusses several resistance welding processes, including seam welding, projection welding, butt welding, and spark butt welding. Each process applies the same fundamental principle but differs in how the electrodes are used or the type of pressure applied.
What is seam welding, and how does it work?
-Seam welding involves applying electric current and pressure to the workpieces at multiple points along the joint. This process creates a continuous weld bead, similar to how a sewing machine forms a line of stitches. The electrodes used are circular.
How does projection welding differ from spot welding?
-Projection welding is similar to spot welding, but in projection welding, one of the parts has protrusions (created through stamping) that localize the welding current at specific points. This results in multiple spots welded simultaneously along the joint.
What are the key components of the equipment used in resistance welding?
-The key components include a power source (typically a transformer and rectifier), electrodes made of copper alloys (which conduct heat and electrical current), and a mechanical system to apply pressure. These components work together to generate the necessary heat and pressure for the welding process.
How does the welding equipment’s mechanical system function?
-The mechanical system is responsible for applying the necessary pressure to the parts being welded. This pressure can be applied manually, using an electric motor, or automatically, using hydraulic or pneumatic systems, to ensure proper contact between the workpieces.
What are some of the applications of resistance welding mentioned in the script?
-Applications of resistance welding include manufacturing fuel tanks, truck bodies, and other metal parts where a strong, reliable bond is needed. The versatility of resistance welding allows it to be used for various types of metal joints and components, depending on the material and welding requirements.
Outlines
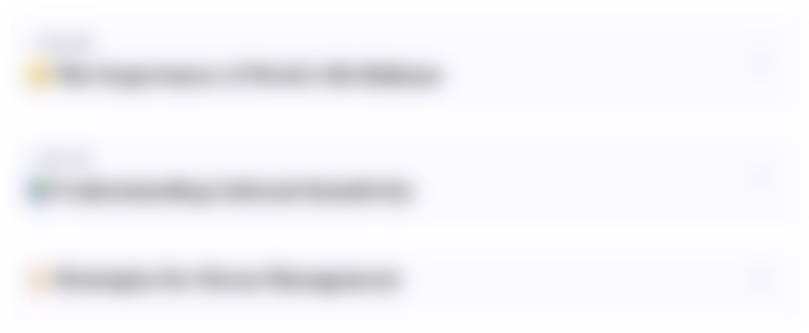
此内容仅限付费用户访问。 请升级后访问。
立即升级Mindmap
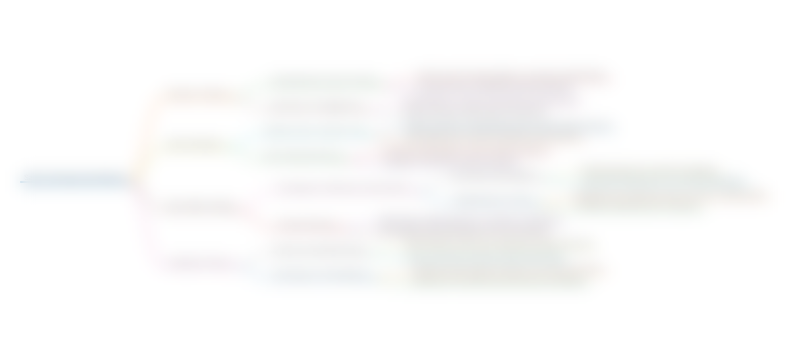
此内容仅限付费用户访问。 请升级后访问。
立即升级Keywords
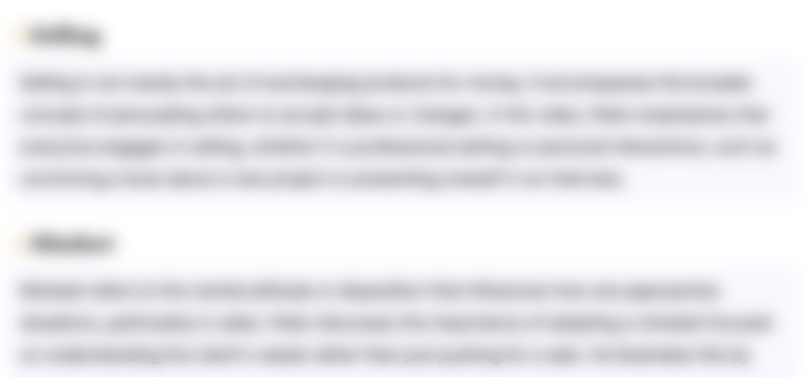
此内容仅限付费用户访问。 请升级后访问。
立即升级Highlights
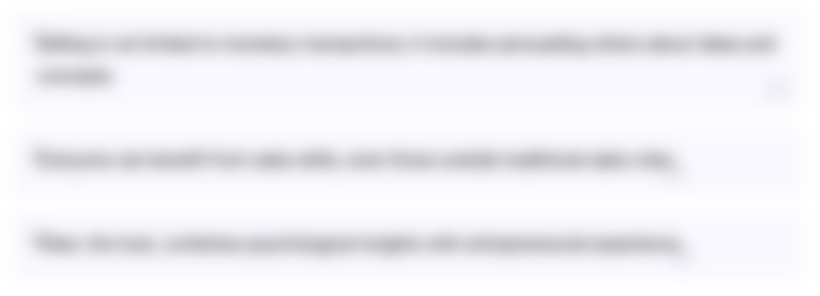
此内容仅限付费用户访问。 请升级后访问。
立即升级Transcripts
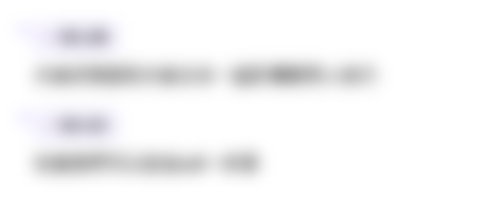
此内容仅限付费用户访问。 请升级后访问。
立即升级5.0 / 5 (0 votes)