ANSYS Student: Fatigue Analysis of a Formula SAE Hub
Summary
TLDRThis demonstration guides users through a fatigue analysis of a Formula SAE hub using ANSYS. The analysis focuses on determining the number of cycles the hub can withstand before fatigue failure under torque and bearing loads. The process includes setting up the material properties, applying boundary conditions, and solving the model. It covers both stress-life and strain-life fatigue methods, demonstrating how to adjust for biaxiality and various loading scenarios. The results predict the hub’s fatigue life, with a focus on real-world applications like stop-start motion and continuous operation, ultimately providing valuable insights for designing durable parts.
Takeaways
- 😀 Fatigue analysis is performed on a Formula SAE hub to determine the number of cycles before fatigue failure.
- 😀 Two types of fatigue analysis are used: stress life (for low strain, high cycle conditions) and strain life (for large strains and potential plastic deformations).
- 😀 The stress life fatigue method is based on empirical SN curves, which relate alternating stress values to the number of cycles to failure.
- 😀 Strain life fatigue analysis is used when the stresses exceed the material's yield stress, leading to plastic strains.
- 😀 The analysis uses a torque of 300 lb-ft and a dead load of 150 lbs distributed across bolt holes to simulate real-world loading conditions.
- 😀 The hub is modeled using structural steel, and a mesh is generated for analysis.
- 😀 Fixed supports are applied to the bearing surface, and a moment is applied to the face plate of the hub to simulate load conditions.
- 😀 The maximum stress occurs at the corner transition of the bearing surface, with a value of 15,000 psi, well below the yield stress of structural steel.
- 😀 The fatigue life of the part is estimated to be 3.4 × 10^5 cycles, based on fully reversed loading and the equivalent stress.
- 😀 A biaxiality indicator suggests that the loading at the corner of the hub is under shear stress, prompting the use of maximum shear stress for a more conservative fatigue life estimate.
- 😀 By adjusting the stress component to maximum shear stress, the fatigue life prediction becomes more conservative, estimating 1.6 × 10^5 cycles instead.
- 😀 Advanced loading types such as zero-based loading, ratio-based loading, and history-based loading allow for refined fatigue analysis under different operating conditions.
Q & A
What is the objective of the fatigue analysis for the Formula SAE hub in this demonstration?
-The objective is to determine the number of cycles the hub can withstand before experiencing fatigue failure, given the applied loads and constraints.
What are the two types of fatigue analysis discussed in the demonstration?
-The two types are stress life fatigue analysis and strain life fatigue analysis. Stress life is used for low-strain, high-cycle fatigue, while strain life is suited for larger strains and lower-cycle fatigue.
Which type of fatigue analysis is suitable for low strain, high cycle fatigue analysis?
-The stress life fatigue analysis is suitable for low strain, high-cycle fatigue where the stresses from a single loading event are much smaller than the yield stress of the material.
What is the main difference between stress life and strain life fatigue analysis?
-Stress life is used when the material experiences small stresses and large cycles, while strain life is used for situations where the material experiences larger strains and stresses that can exceed the yield stress.
What material properties are defined in the engineering data for this fatigue analysis?
-The material properties include the SN curve (alternating stress vs. number of cycles to failure), and strain life parameters are also defined, allowing the user to choose the appropriate fatigue method.
What is the purpose of using the fatigue strength factor in the fatigue tool?
-The fatigue strength factor adjusts the SN curve to account for differences between the experimental conditions under which the SN curve was obtained and the actual operating conditions of the part.
What does the scale factor in the fatigue tool allow you to do?
-The scale factor allows you to explore fatigue results for different loading conditions, such as applying higher or lower loads than those originally applied in the model, to see how they affect the fatigue life.
What is the predicted fatigue life of the hub based on the equivalent stress of 15,000 psi?
-The predicted fatigue life of the hub is 3.4e+5 cycles, meaning the hub can withstand that many cycles of fully reversed bearing and moment loads before failure.
Why did the analysis switch from using equivalent stress to maximum shear stress in the fatigue tool?
-The analysis switched to maximum shear stress because the hub was experiencing pure shear in the corner region due to the dominant torque load, and using maximum shear stress gives a more conservative estimate of the fatigue life.
What does the by axiality indicator in the fatigue tool tell you?
-The by axiality indicator shows whether the loading is pure uniaxial, biaxial, or pure shear. In this case, the corner of the hub is under pure shear, and the fatigue analysis was adjusted accordingly.
Outlines
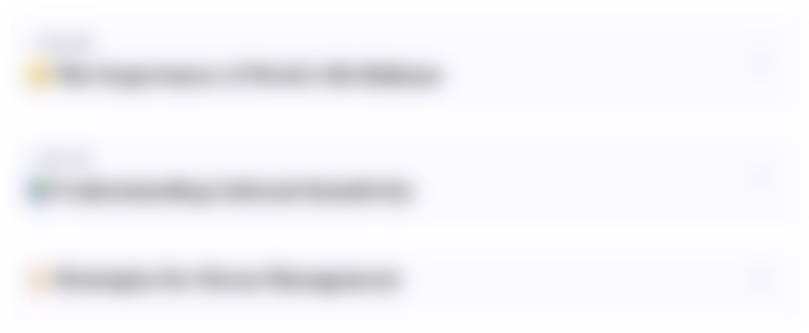
此内容仅限付费用户访问。 请升级后访问。
立即升级Mindmap
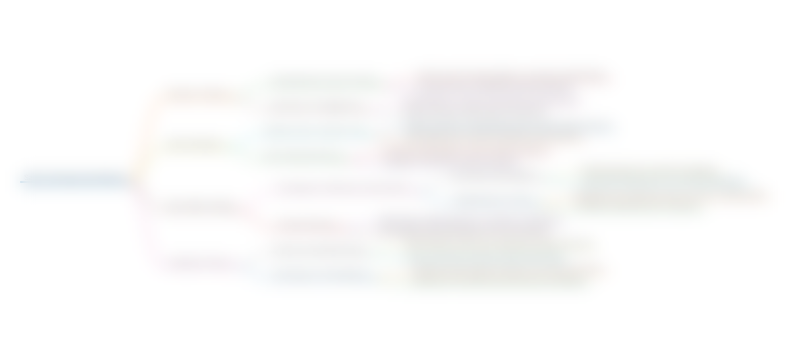
此内容仅限付费用户访问。 请升级后访问。
立即升级Keywords
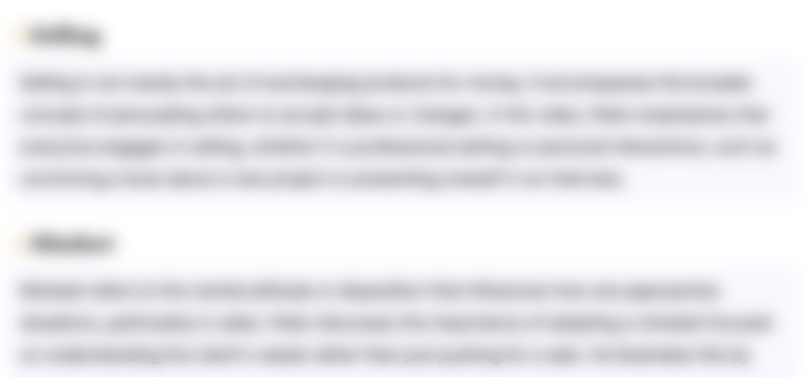
此内容仅限付费用户访问。 请升级后访问。
立即升级Highlights
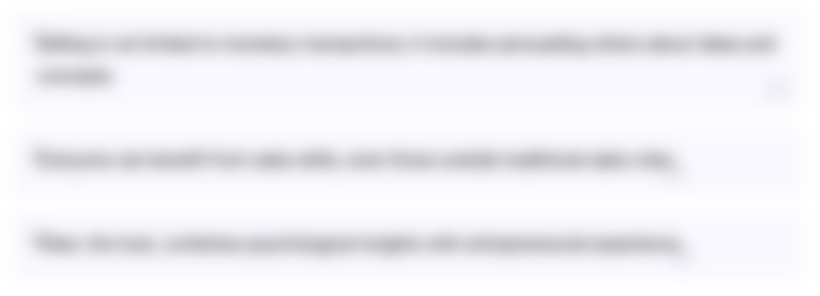
此内容仅限付费用户访问。 请升级后访问。
立即升级Transcripts
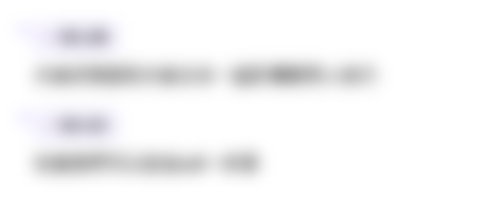
此内容仅限付费用户访问。 请升级后访问。
立即升级浏览更多相关视频
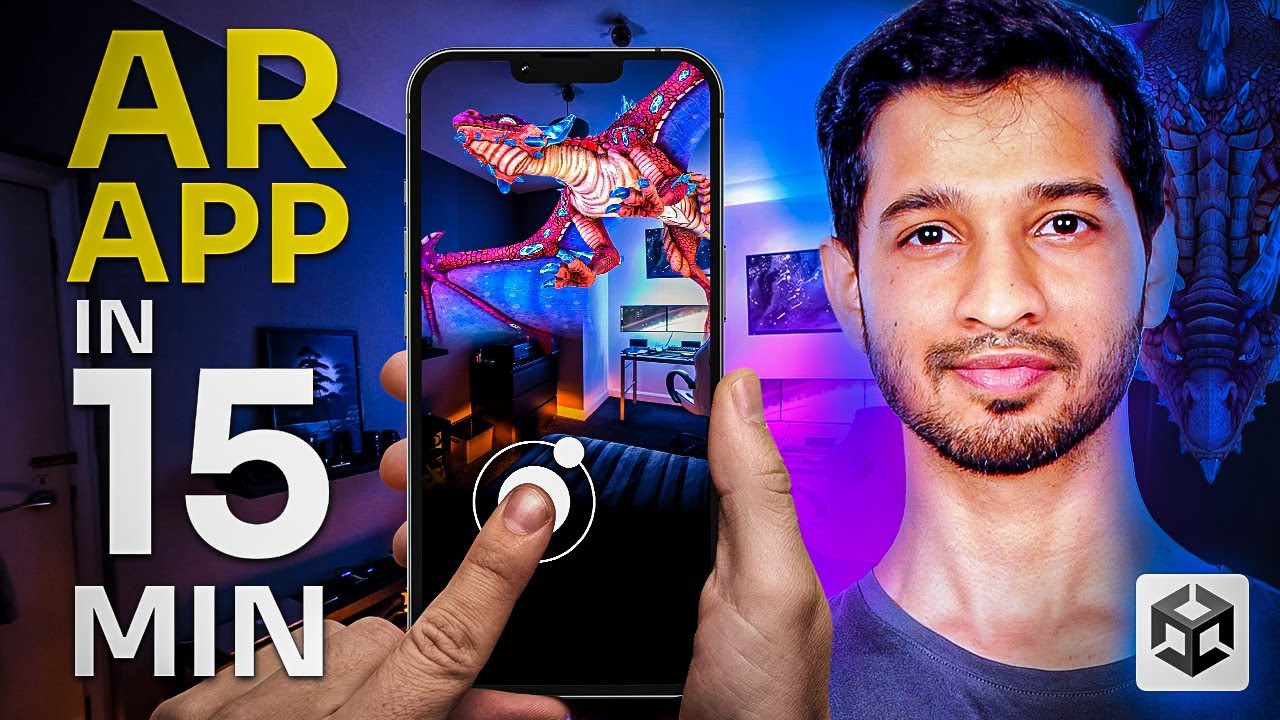
Let’s Make an AR App in 15 MINUTES!! (Beginner Friendly)

How to Specify Materials in Ansys Fluent — Lesson 4
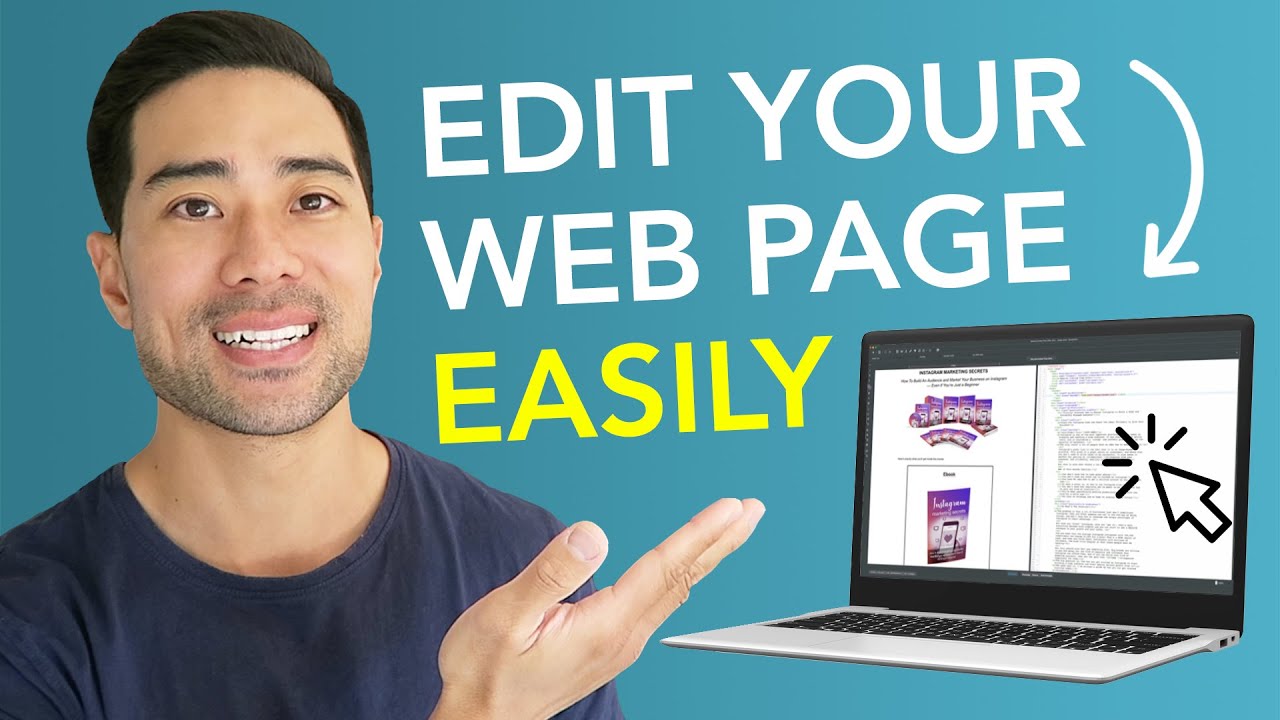
How To Edit an HTML Web Page Using BlueGriffon - PLR Tutorial
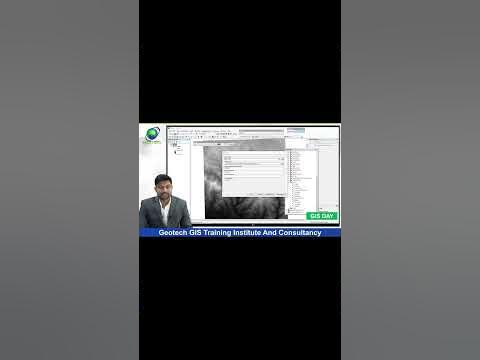
How to Prepare Slope Map from DEM #shorts #youtubeshorts #gis
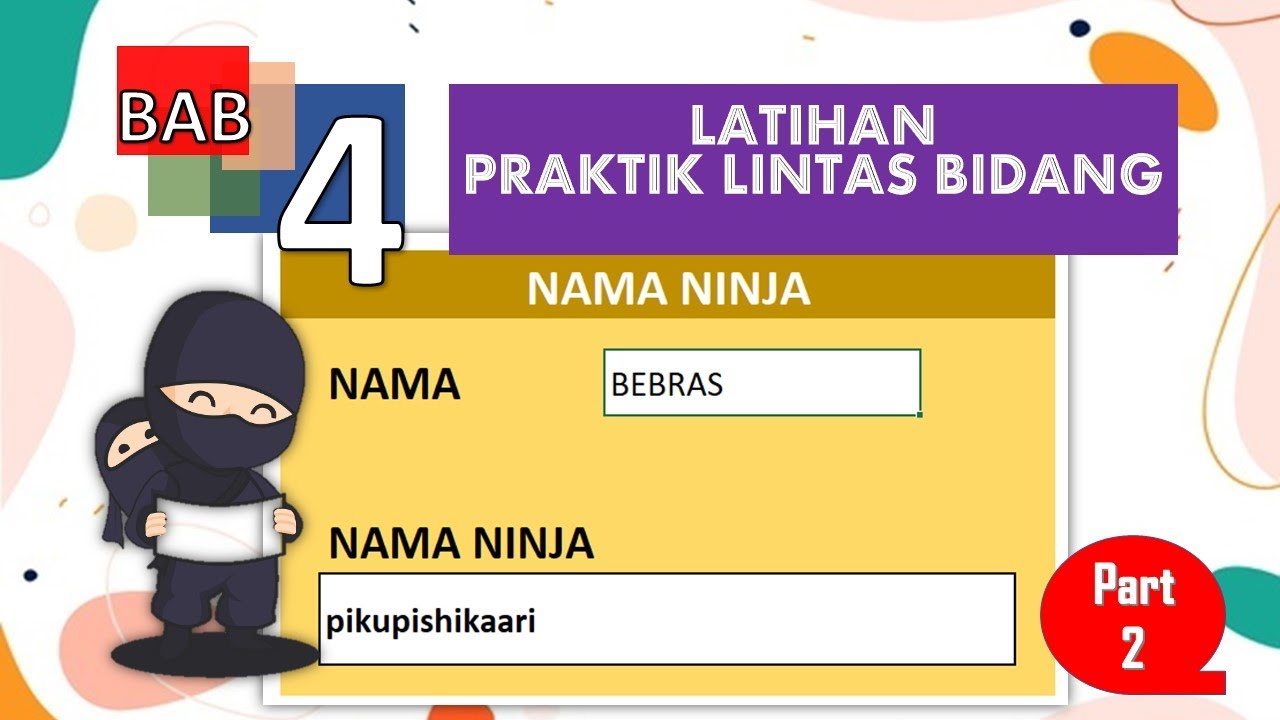
Praktik Lintas Bidang | Informatika SMA Kelas X
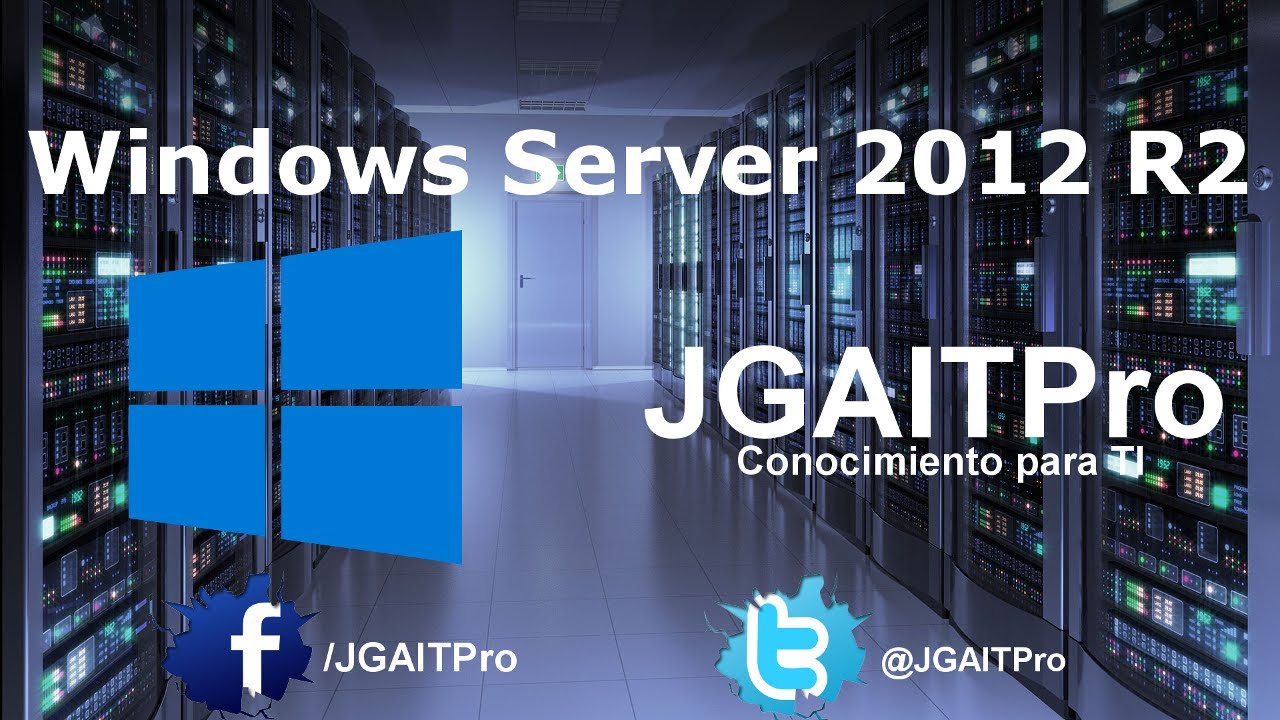
Windows Server 2012 R2 - Quitar opción Conectar o desconectar unidades de red por GPO
5.0 / 5 (0 votes)