Module 5, Video 1: Job vs Process Costing Explained
Summary
TLDRThis video explains the difference between two costing systems: job order costing and process costing. Job order costing is used for unique or low-volume products, accumulating costs for individual jobs or batches. Process costing, on the other hand, is applied to high-volume, identical products, accumulating costs by department or process. The video emphasizes the importance of cost accounting in determining product pricing, production volumes, and inventory values, which are crucial for business decisions. It also highlights how organizations may use both systems depending on the types of products they produce, whether custom or standardized.
Takeaways
- 😀 Cost accounting involves the measurement, recording, and reporting of product costs, both in total and per unit.
- 😀 Cost accounting helps organizations decide which products to produce, how much to charge, and how many units to produce.
- 😀 Job order costing is used for products with unique characteristics, such as custom homes or batches of personalized products.
- 😀 Job order costing accumulates costs per job, and if it's a batch, the per unit cost is calculated by dividing the total job cost by the number of units produced.
- 😀 Process costing is used for continuous production of identical products, where the volume is large, such as in the production of LEGO bricks.
- 😀 In process costing, costs are accumulated by process or department, and the per unit cost is determined by dividing the total processing costs by the total units produced.
- 😀 Job order costing is typically used when the volume of products is low, sometimes only one product.
- 😀 Process costing is used when the volume of products produced is very high, making it ideal for mass production industries.
- 😀 Some organizations use both costing systems, especially if they produce both unique and standardized products.
- 😀 The objective of both costing systems is to accurately calculate per unit costs, which help in pricing, inventory valuation, and cost control.
Q & A
What is cost accounting?
-Cost accounting is the measurement, recording, and reporting of product costs both in total and per unit. It helps organizations determine which products to produce, how much to charge for them, and how many units to produce.
Why is cost accounting important for an organization?
-Cost accounting is critical because it provides accurate cost information that is essential for decision-making, pricing products, and managing the number of units to produce, ultimately impacting an organization's success.
What is the difference between job order costing and process costing?
-Job order costing is used for unique or customized products with low production volume, while process costing is used for high-volume, identical products produced continuously.
What type of products is job order costing used for?
-Job order costing is used for products with unique characteristics, such as custom items or batches of similar products produced for a specific customer, like custom homes or university sweatshirts.
What is the objective of a job order costing system?
-The objective of a job order costing system is to calculate the total cost of a particular job by accumulating costs per job or batch, and then calculating the per-unit cost by dividing the total job cost by the number of units produced.
What is process costing, and when is it used?
-Process costing is used when products are produced in large volumes, continuously, and are identical, like manufacturing LEGO bricks. It accumulates costs by process or department and calculates the per-unit cost by dividing the total processing costs by the total units produced.
Can organizations use both job order costing and process costing?
-Yes, organizations can use both costing systems. For example, a company may produce both custom products (requiring job order costing) and standardized products (requiring process costing), depending on their manufacturing needs.
What is the objective of a process costing system?
-The objective of a process costing system is to accumulate costs by process or department and then calculate the cost of each unit by dividing the total costs by the total units produced.
What is a good example of a product that uses process costing?
-A good example of a product that uses process costing is LEGO bricks, which are produced in vast quantities, averaging 36 billion bricks annually, with each brick being identical.
How can organizations use costing systems to control costs?
-Organizations use costing systems to calculate per unit costs, which helps them determine product pricing, assess the value of ending inventory, and manage or control production costs moving forward.
Outlines
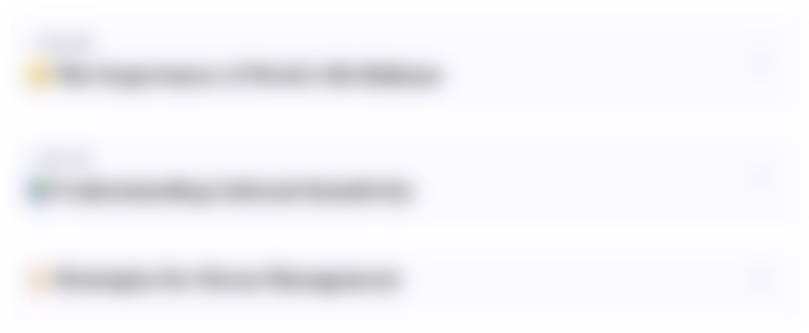
此内容仅限付费用户访问。 请升级后访问。
立即升级Mindmap
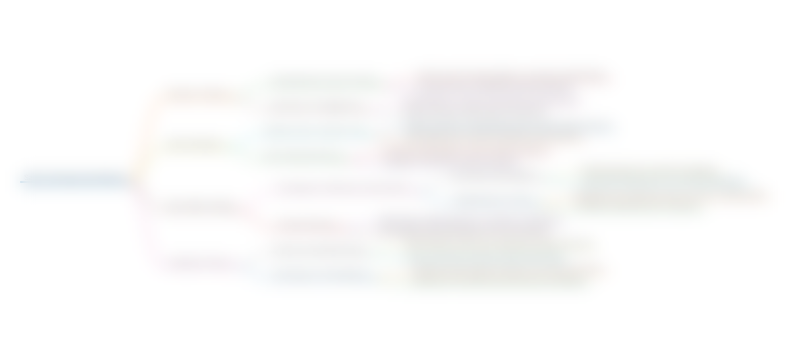
此内容仅限付费用户访问。 请升级后访问。
立即升级Keywords
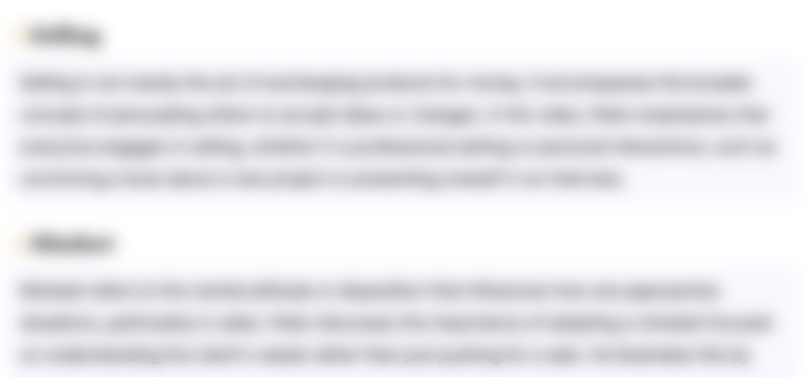
此内容仅限付费用户访问。 请升级后访问。
立即升级Highlights
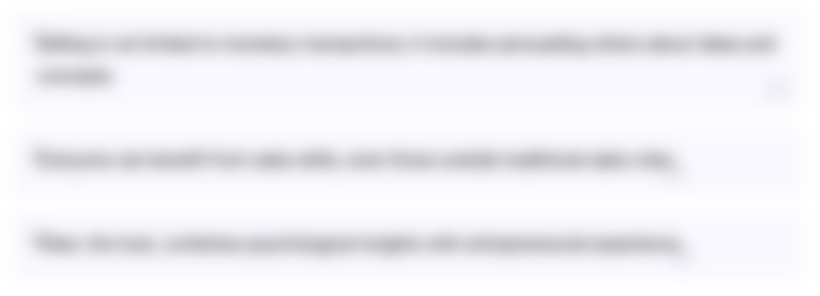
此内容仅限付费用户访问。 请升级后访问。
立即升级Transcripts
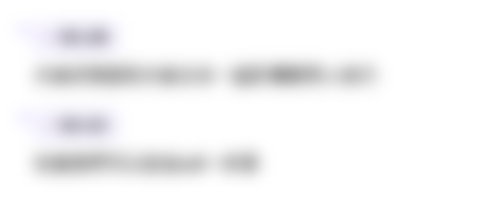
此内容仅限付费用户访问。 请升级后访问。
立即升级5.0 / 5 (0 votes)