Total Quality Management (TQM) overview, including Six Sigma, Benchmarking & Just-in-Time concepts
Summary
TLDRThis video covers the core principles of Total Quality Management (TQM), focusing on seven key concepts: Continuous Improvement, Six Sigma, Employee Empowerment, Benchmarking, Just-in-Time (JIT), Taguchi Concepts (skipped for simplicity), and Seven Quality Control Tools. It explores the importance of process enhancement, statistical and programmatic quality management, employee involvement, and learning from the best practices of other industries. Additionally, it highlights how reducing inventory with JIT can expose process issues, ultimately leading to better quality and lower costs. The video also touches on the challenge of measuring service quality, emphasizing both tangible and intangible factors.
Takeaways
- 😀 Continuous Improvement is a core principle of TQM, aiming for ongoing refinement of processes without a fixed endpoint, using models like PDCA and PDSA to guide incremental gains.
- 😀 Six Sigma focuses on reducing defects to no more than 3.4 per million opportunities, using a structured program combined with statistical methods to improve quality and reduce variation.
- 😀 DMAIC (Define, Measure, Analyze, Improve, Control) is a key methodology within Six Sigma for systematic process improvement.
- 😀 Employee Empowerment encourages organizations to involve employees in identifying and solving quality problems, with a focus on improving processes rather than blaming individuals.
- 😀 Benchmarking involves comparing an organization's practices with the best in the industry, even outside of the organization's field, to identify opportunities for improvement.
- 😀 Just-in-Time (JIT) reduces inventory to expose process problems, enabling more efficient problem-solving and improving both quality and cost-efficiency.
- 😀 The Seven Quality Control Tools are essential for generating ideas, organizing data, and identifying problems. These tools will be explored further in a separate video.
- 😀 Service quality is harder to measure than product quality due to the varying perceptions of customers regarding both tangible (physical) and intangible (experience-based) aspects.
- 😀 Both tangible and intangible components of service quality impact customer perceptions. For example, a well-done job may be overshadowed by poor customer service or mistakes made during the service.
- 😀 TQM is not a one-time process but a continuous journey of process optimization and customer satisfaction, requiring a commitment to systematic improvements and feedback loops.
Q & A
What is Total Quality Management (TQM)?
-Total Quality Management (TQM) is a management approach that involves managing the entire organization to excel in all aspects of products and services that are important to the customer. It focuses on continuous improvement, employee involvement, and using data-driven tools and techniques to achieve quality goals.
What are the seven concepts of TQM discussed in the video?
-The seven concepts of TQM discussed in the video are: Continuous Improvement, Six Sigma, Employee Empowerment, Benchmarking, Just-in-Time (JIT), Taguchi Concepts (not covered in detail), and Knowledge of TQM Tools.
What is Continuous Improvement, and how is it applied in TQM?
-Continuous Improvement is the ongoing effort to improve processes incrementally, using methods such as the PDCA (Plan-Do-Check-Act) or PDSA (Plan-Do-Study-Act) models. It involves analyzing and improving all areas surrounding operations, from suppliers to customer interactions, to optimize quality and efficiency.
What is the statistical definition of Six Sigma?
-The statistical definition of Six Sigma refers to a process that has no more than 3.4 defects per million opportunities (DPMO). It signifies a very high level of process quality, where defects are extremely rare.
What are the two meanings of Six Sigma in the context of TQM?
-Six Sigma has two meanings: 1) As a **statistical standard**, it refers to achieving no more than 3.4 defects per million opportunities. 2) As a **program**, it is a structured approach to process improvement aimed at reducing defects and enhancing customer satisfaction, often using tools such as lean methodologies.
What is the DMAIC methodology, and how is it related to Six Sigma?
-DMAIC stands for Define, Measure, Analyze, Improve, and Control. It is a methodology used in Six Sigma to systematically improve processes by first defining the problem, measuring current performance, analyzing the causes of defects, improving the process, and controlling the improved process to maintain the gains.
Why is employee empowerment important in TQM?
-Employee empowerment is crucial because it involves engaging employees in decision-making and quality improvement processes. Employees on the front lines often have valuable insights into process inefficiencies and potential solutions. Empowered employees are more likely to contribute to a culture of quality and process improvement.
What is benchmarking, and how does it help organizations improve quality?
-Benchmarking is the practice of comparing an organization’s processes, products, or services to those of industry leaders or other organizations (often in different industries). The goal is to identify best practices that can be adapted and implemented to improve the organization's own quality, efficiency, and competitiveness.
How does Just-in-Time (JIT) contribute to quality management?
-Just-in-Time (JIT) is a philosophy that aims to reduce inventory and improve process efficiency. By reducing inventory, JIT exposes hidden problems in the process, such as slow setups or supplier issues, that might otherwise be masked by excess stock. These problems can then be addressed to improve overall quality and reduce costs.
What is the importance of understanding both tangible and intangible aspects of service quality?
-In service quality, both tangible and intangible components play a significant role in customer perception. Tangible aspects, like the quality of the service provided (e.g., clean carpets), are measurable. Intangible aspects, such as customer service and attitudes (e.g., the technician's punctuality and behavior), also significantly influence how customers perceive the overall quality of the service.
Outlines
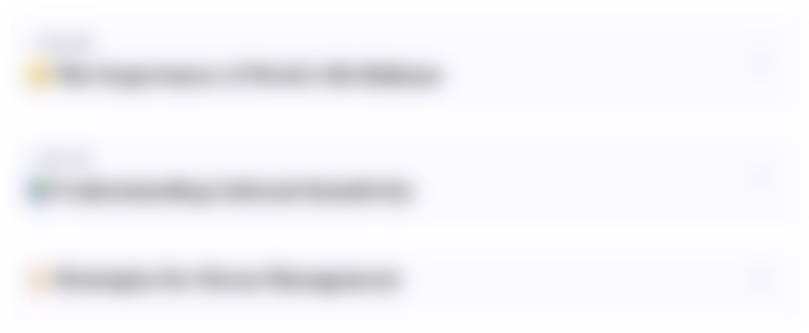
此内容仅限付费用户访问。 请升级后访问。
立即升级Mindmap
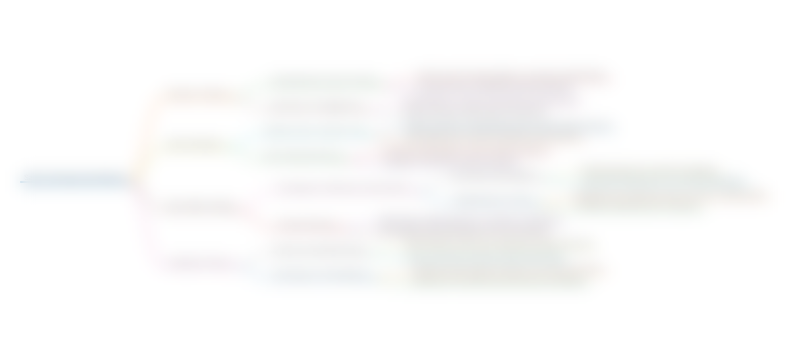
此内容仅限付费用户访问。 请升级后访问。
立即升级Keywords
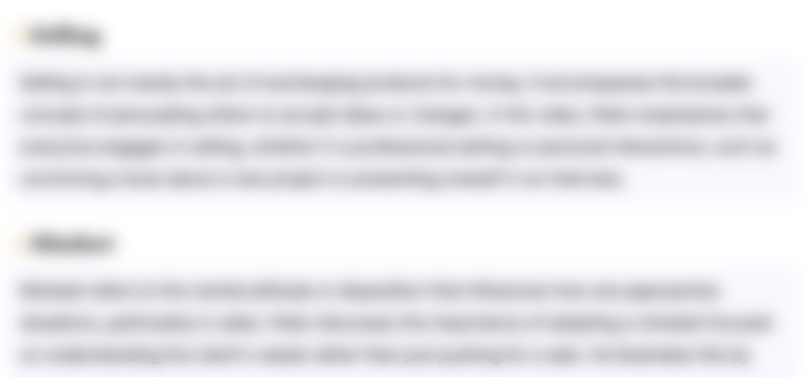
此内容仅限付费用户访问。 请升级后访问。
立即升级Highlights
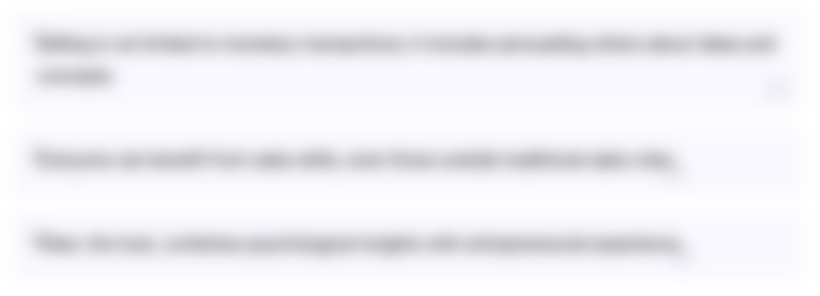
此内容仅限付费用户访问。 请升级后访问。
立即升级Transcripts
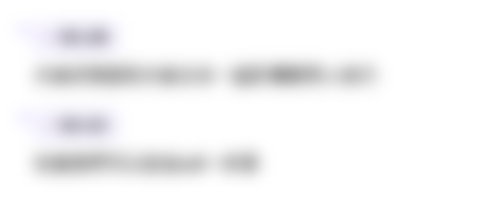
此内容仅限付费用户访问。 请升级后访问。
立即升级浏览更多相关视频
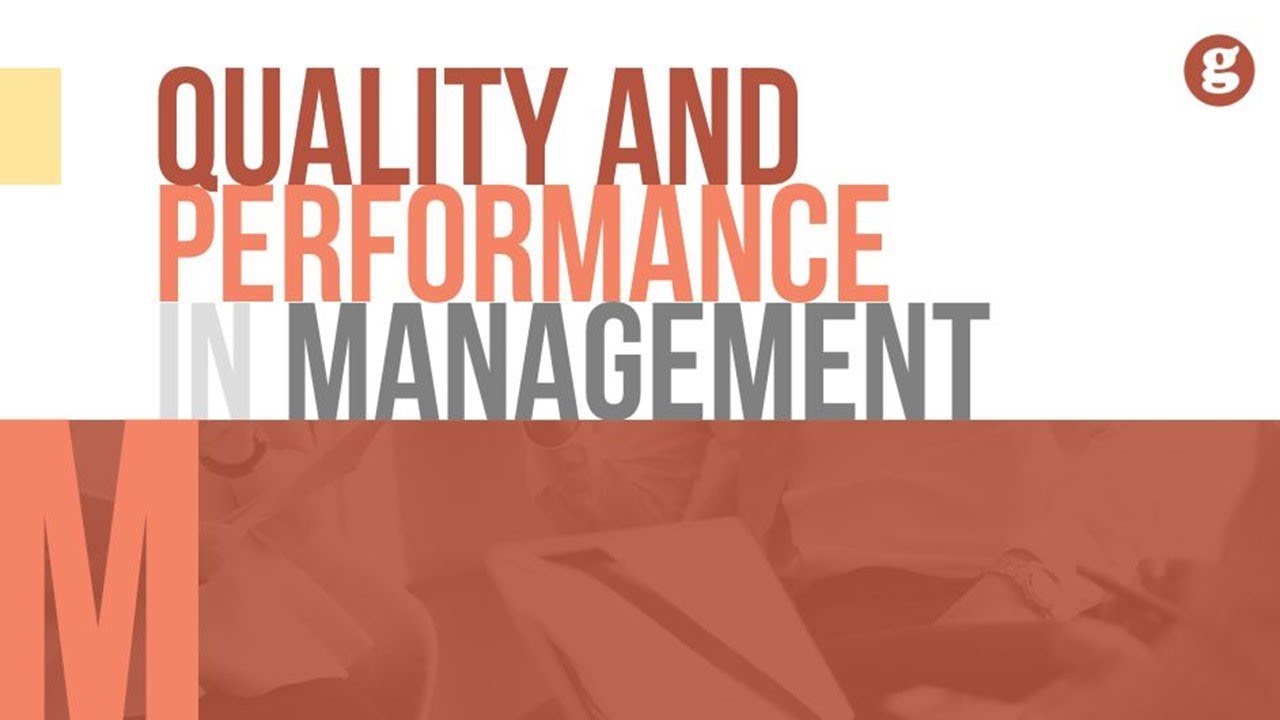
Quality and Performance in Management
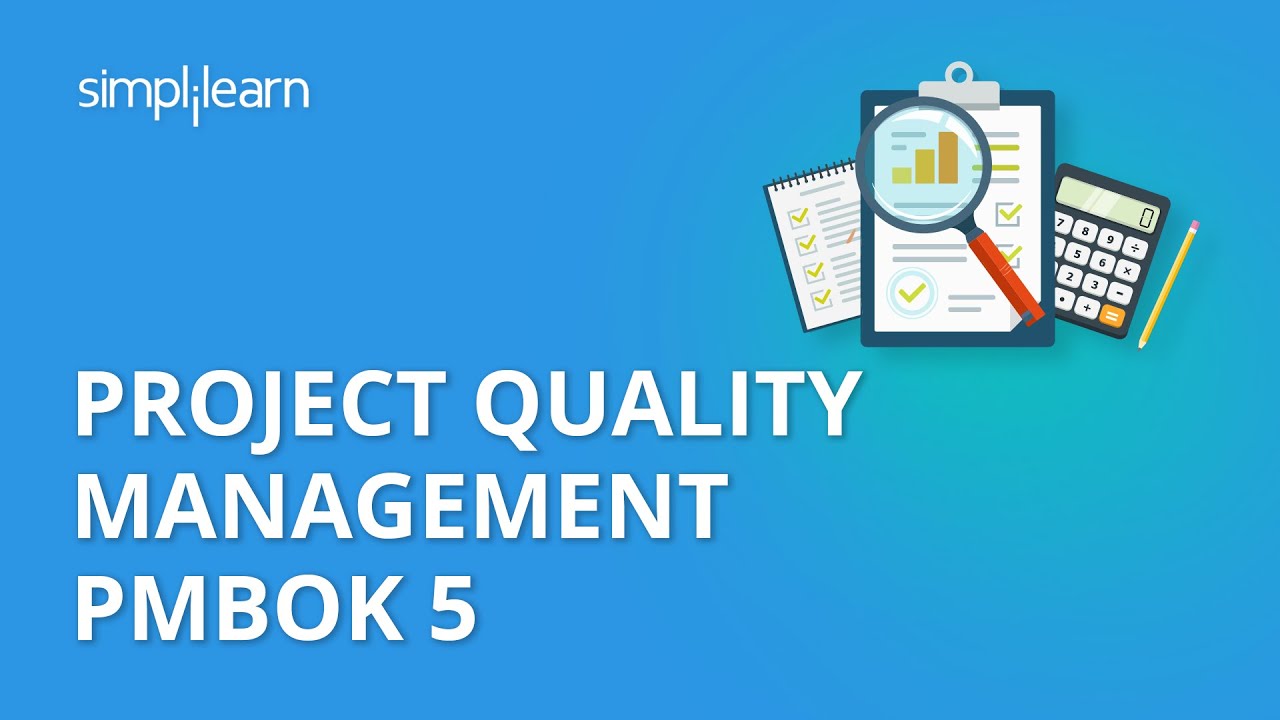
Project Quality Management PMBOK 5 | PMP® Training Videos | Project Management Tutorial |Simplilearn
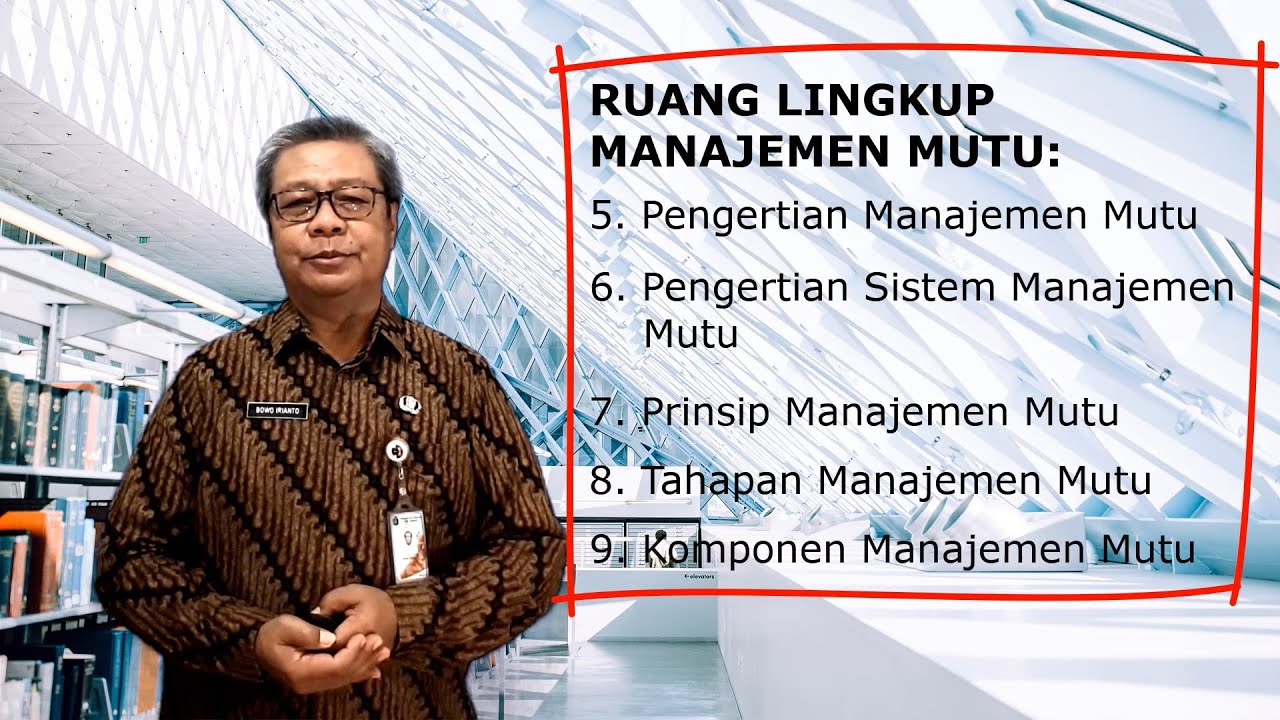
MANAJEMEN MUTU 02 - Pengertian, Sistem, Prinsip, Tahapan dan Komponen Manajemen Mutu - Bowo Irianto

CBME 1 | Lesson 1 | Part 2/3

What is Total Quality management (TQM)? | 7 Principles of Total Quality Management
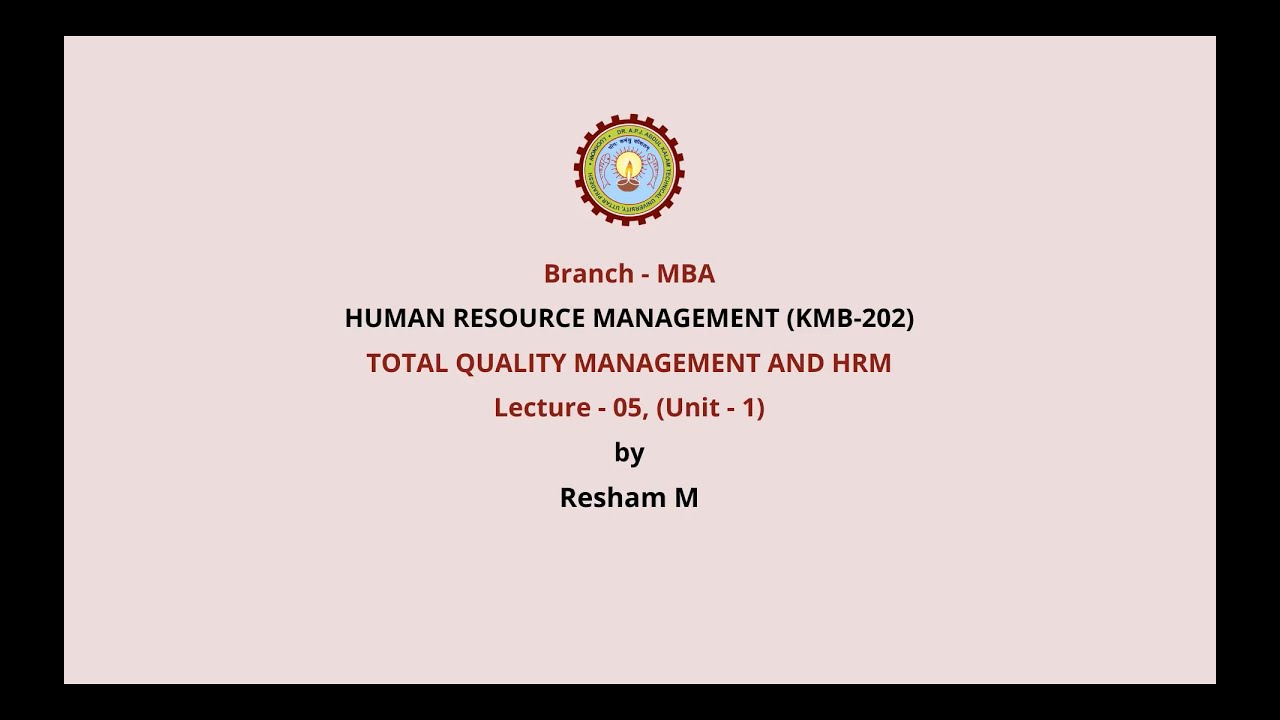
Human Resource Management | Total Quality Management and HRM | AKTU Digital Education
5.0 / 5 (0 votes)