Hydraulic Training Series - Chapter 7 - Hydrostatic Transmissions
Summary
TLDRThis video explains the principles and components of hydrostatic transmissions, highlighting how pumps and motors work in tandem to control fluid flow and mechanical movement. It covers the different types of piston pumps—radial, bent axis, and swash plate—and details how displacement adjustments influence motor speed and torque. The system’s ability to vary speed, reverse direction, and operate smoothly under load without damage is emphasized. The video also discusses the use of relief valves, check valves, and other components that ensure efficiency and prevent damage, making hydrostatic transmissions ideal for variable-speed, high-torque applications.
Takeaways
- 😀 Hydrostatic transmissions rely on pumps and motors to convert hydraulic energy into mechanical power.
- 😀 Piston pumps are the most common in hydrostatic transmissions due to their high efficiency and pressure capabilities.
- 😀 There are three basic types of piston units: radial, bent-axis, and swash plate piston pumps, each with different displacement control mechanisms.
- 😀 A variable displacement pump allows for changes in the amount of fluid moved, providing more control over motor speed and direction.
- 😀 The displacement of a swash plate piston pump is controlled by the angle of the swash plate, which can be adjusted to vary fluid flow.
- 😀 Piston motors operate in reverse compared to pumps, using hydraulic fluid to rotate the motor shaft and generate mechanical work.
- 😀 Fixed displacement motors provide constant torque, regardless of speed, making them ideal for certain applications.
- 😀 Hydrostatic transmission systems are often closed-loop, meaning the oil circulating between the pump and motor returns to the pump, creating potential for internal leakage.
- 😀 Additional components like a small reservoir pump and relief valves help maintain system efficiency by replenishing leaked fluid and protecting against overloading.
- 😀 Relief valves prevent system damage by diverting excess fluid during overload conditions, though energy loss through these valves generates heat.
- 😀 Hydrostatic transmissions offer advantages like high power density, smooth control, fast starting and stopping, and durability under varying load conditions.
Q & A
What are the main types of pumps used in hydrostatic transmissions?
-The main types of pumps used in hydrostatic transmissions are vein, piston, and gear pumps. Piston units are the most common due to their high efficiency, pressure capabilities, and availability in both fixed and variable displacement models.
How does the displacement of a piston pump get determined in a bent axis pump?
-In a bent axis pump, displacement is determined by the angle of the cylinder block relative to the drive shaft. The pistons at the top are pulled outwards, and those at the bottom are pushed in. The stroke length and displacement depend on the relative positions of these pistons.
What is the role of the swash plate in piston pumps?
-The swash plate in piston pumps determines both the stroke of the pistons and the pump's displacement. The angle of the swash plate controls the distance the pistons travel, thereby influencing the pump’s displacement and flow.
What is the difference between a pump and a motor in a hydrostatic transmission system?
-In a pump, the shaft drives the cylinder block, causing the pistons to move in and out, taking in and discharging fluid. In contrast, in a motor, fluid is pumped into the cylinder bores, forcing the pistons to move against a swashplate, which causes the motor's cylinder block and output shaft to rotate.
How does a fixed displacement motor differ from a variable displacement motor?
-A fixed displacement motor provides constant torque regardless of speed, whereas a variable displacement motor adjusts its displacement based on system requirements, leading to variable torque and speed characteristics.
What purpose do the replenishing check valves serve in a hydrostatic transmission system?
-Replenishing check valves are used to ensure the system has enough fluid despite some internal leakage in both the pump and motor. They enable the closed-loop system to function smoothly by adding fluid to compensate for losses.
What is the function of the cross-line relief valves in the hydrostatic transmission system?
-Cross-line relief valves protect the system from overloads by diverting excess pump flow back to the inlet during overload conditions, preventing system damage. However, oil flowing through these valves is wasted energy, which can lead to heat generation.
Why should stalling in a hydrostatic transmission be avoided?
-Stalling for extended periods should be avoided because it generates wasted energy, leading to excessive heat within the system. Since there is no way to dissipate this heat in a closed-loop system, prolonged stalling can damage the components.
How does the control lever impact the motor’s speed and direction in a hydrostatic transmission system?
-The control lever moves the pump's swash plate to adjust the amount and direction of pump flow, which in turn controls the speed and direction of the motor. Moving the lever off-center causes the motor to rotate, and crossing the center reverses the motor’s direction.
How does the size of the hydraulic motor affect its performance in the system?
-The size of the hydraulic motor influences the motor's torque and speed. A larger motor provides more torque but runs at a slower top speed, as it requires more fluid per revolution. A smaller motor runs faster but delivers less torque.
Outlines
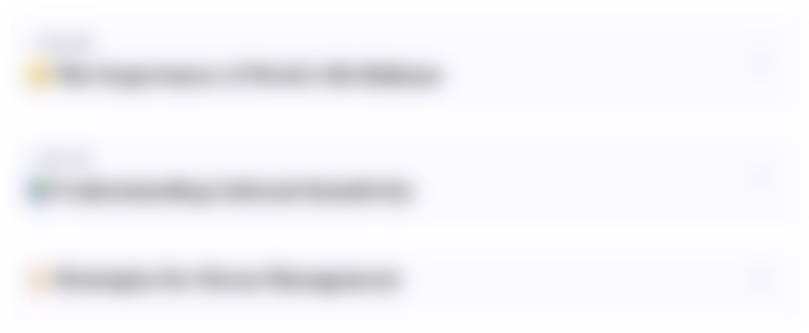
此内容仅限付费用户访问。 请升级后访问。
立即升级Mindmap
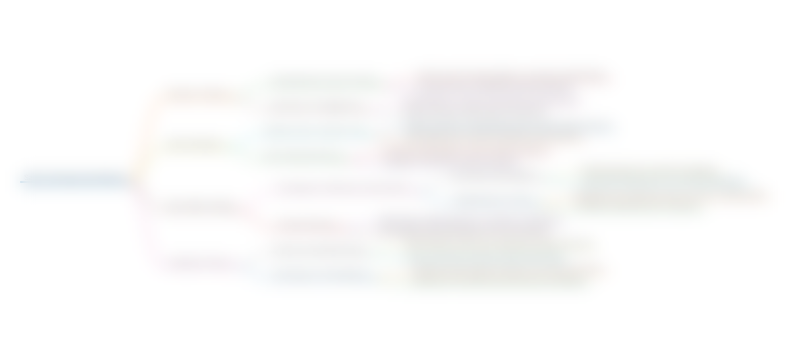
此内容仅限付费用户访问。 请升级后访问。
立即升级Keywords
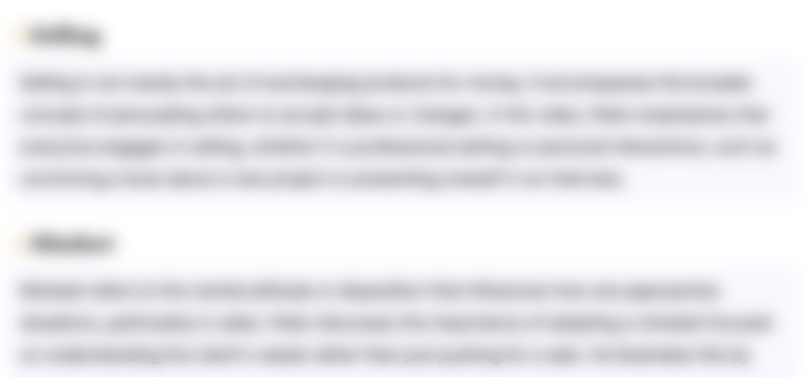
此内容仅限付费用户访问。 请升级后访问。
立即升级Highlights
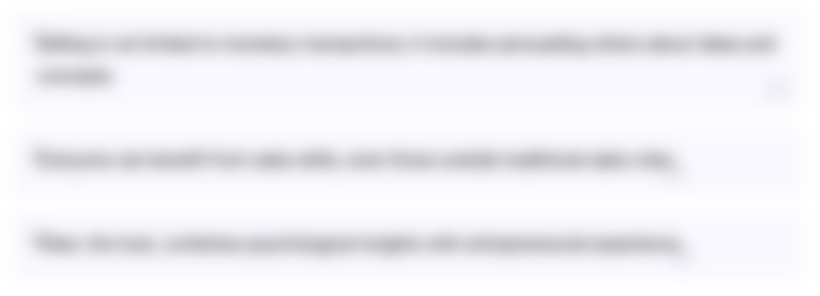
此内容仅限付费用户访问。 请升级后访问。
立即升级Transcripts
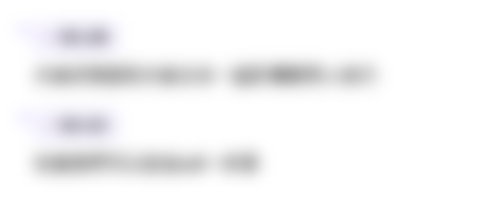
此内容仅限付费用户访问。 请升级后访问。
立即升级浏览更多相关视频
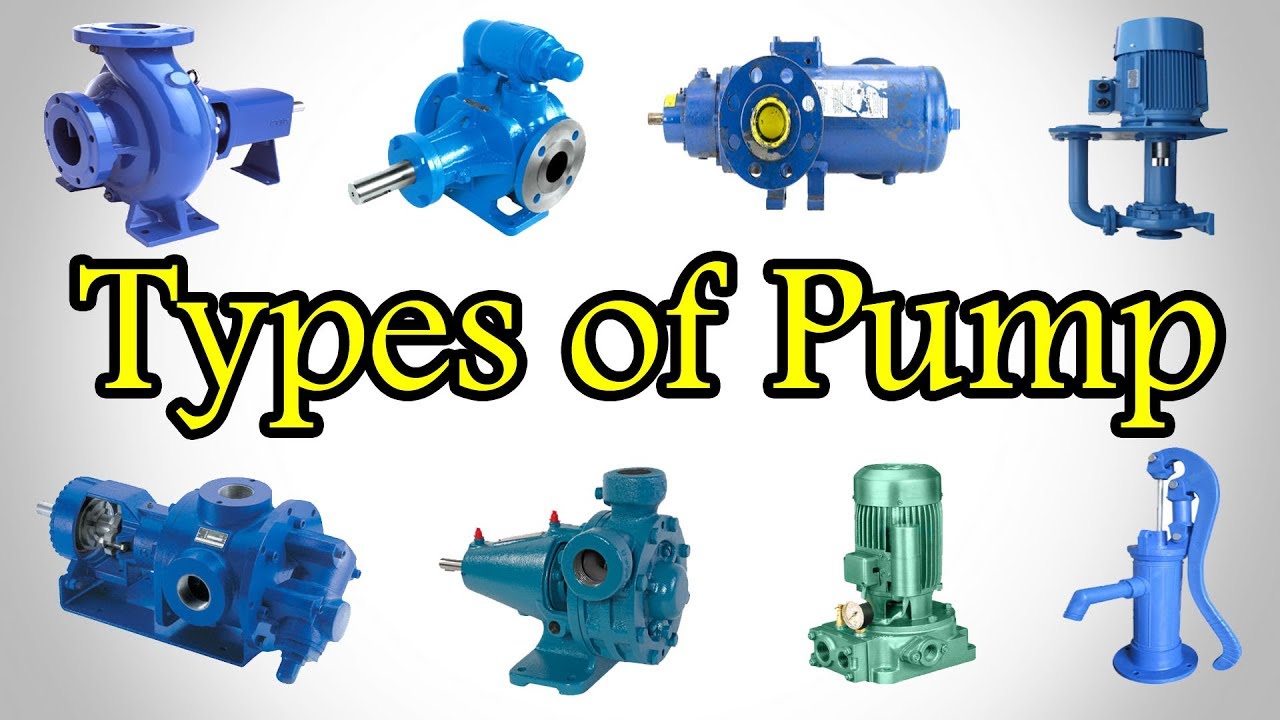
Pumps Types - Types of Pump - Classification of Pumps - Different Types of Pump

Cara kerja pompa piston variabel aliran aksial

Types of pump | Working methods
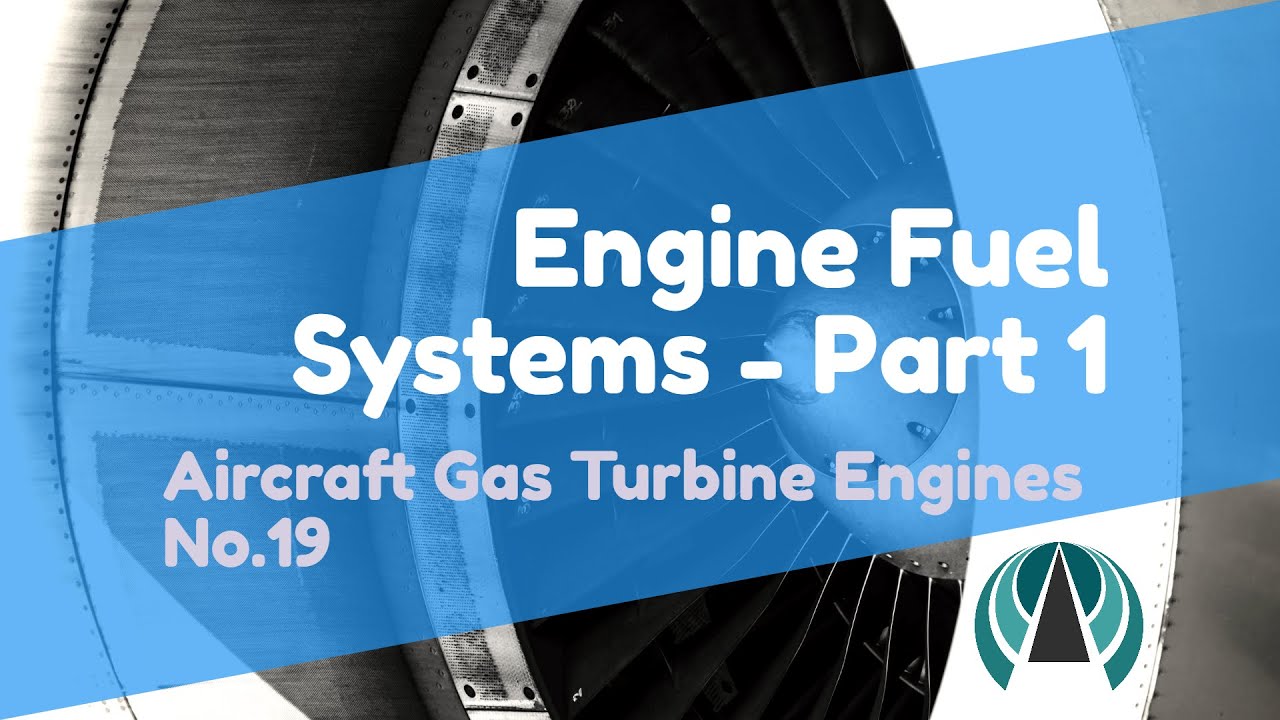
Engine Fuel Systems Part 1 - Aircraft Gas Turbine Engines #19
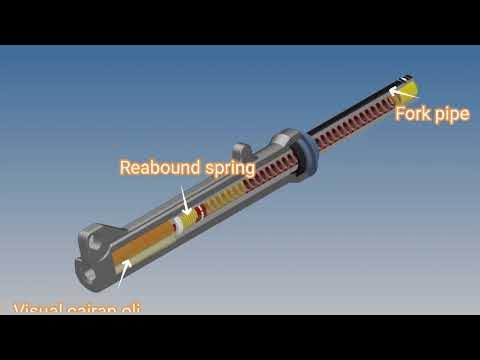
Shock depan motor 3D ( cara kerja )
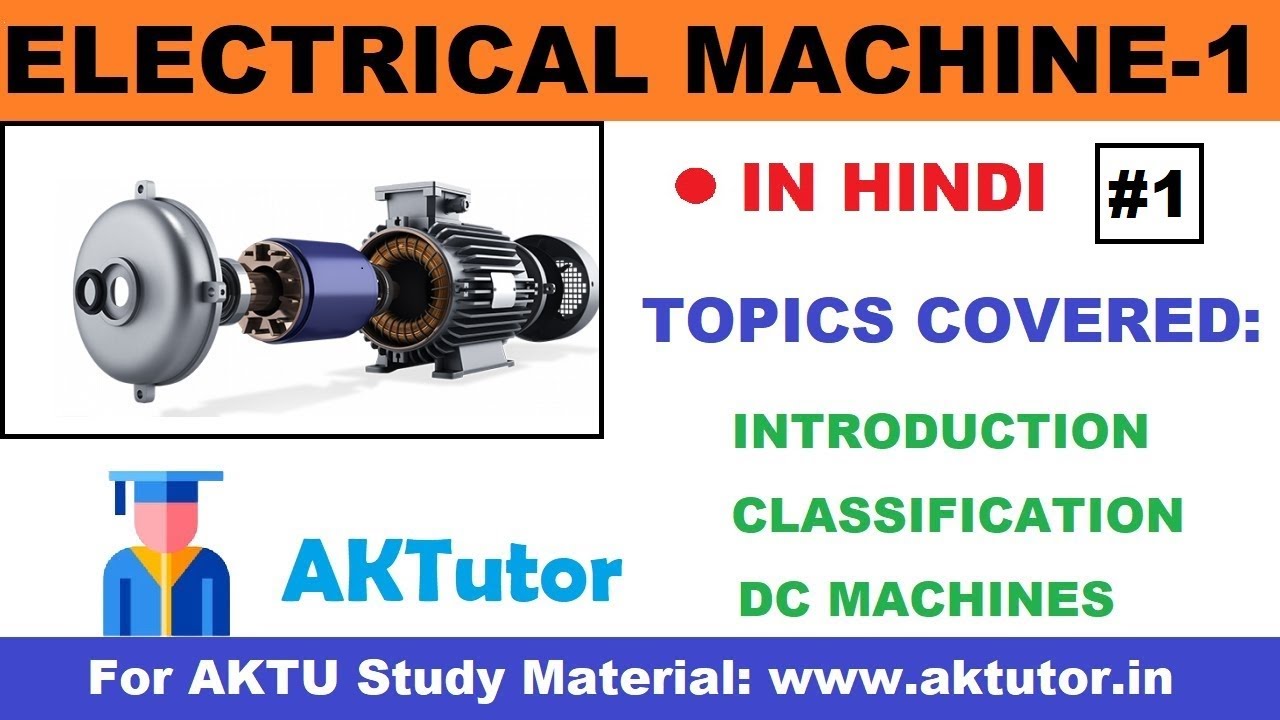
Electrical Machine 1 | Introduction | B.Tech 2nd Year | Abdul Kalam Technical University | AKTutor
5.0 / 5 (0 votes)