Control Modes (V/Hz, SVC, FVC)
Summary
TLDRThis video highlights key motor control methods for PowerFlex series drives, focusing on Volts per Hertz, Sensorless Vector Control, and Flux Vector Control. Volts per Hertz, the most common method, adjusts voltage and frequency to control motor speed but is less effective for high-performance or low-speed applications. Sensorless Vector Control adds slip compensation for better speed and torque control under load, while Flux Vector Control enhances performance with a current resolver and improved accuracy. The video concludes with a call to reach out for further inquiries or assistance from local specialists.
Takeaways
- 😀 Volts per Hertz (V/Hz) is the most common control method, adjusting voltage and frequency to control motor speed.
- 😀 V/Hz works well for general applications but is not ideal for high dynamic performance or low-speed motor operation.
- 😀 For torque control, V/Hz may not be the best choice in applications requiring precise torque regulation.
- 😀 Sensorless Vector Control is the default method in PowerFlex drives and adds slip compensation to improve speed control.
- 😀 Sensorless Vector Control also includes a torque current estimator for better motor performance under load.
- 😀 Unlike V/Hz, Sensorless Vector Control also manages voltage angle for improved low-speed operation and torque control.
- 😀 Flux Vector Control builds on V/Hz by adding components like a current resolver to enhance drive performance.
- 😀 The current resolver identifies flux and torque-producing currents in the motor, allowing for better regulation.
- 😀 Flux Vector Control replaces the current limit block with a current regulator for more accurate motor control.
- 😀 While V/Hz, Sensorless Vector, and Flux Vector are the most common, there are additional control methods that may suit specific applications.
Q & A
What is the most common motor control method used in PowerFlex series drives?
-The most common motor control method used in PowerFlex series drives is Volts per Hertz (V/Hz). It adjusts the voltage and frequency to control the motor's speed while maintaining a constant volts-to-hertz ratio.
What are the limitations of the Volts per Hertz control method?
-The Volts per Hertz method does not work well in applications requiring high dynamic performance, low-speed operation, or precise torque control. It is best suited for general applications.
How does Sensorless Vector Control (SVC) improve upon Volts per Hertz?
-Sensorless Vector Control (SVC) improves upon Volts per Hertz by adding slip compensation and a torque current estimator, which allows for better speed control under load and improved low-speed operation.
What is the role of the torque current estimator in Sensorless Vector Control?
-The torque current estimator in Sensorless Vector Control helps calculate an approximate torque current, improving torque control and motor speed accuracy under varying load conditions.
What advantage does Sensorless Vector Control have over Volts per Hertz at low speeds?
-Sensorless Vector Control provides better low-speed operation due to the added slip compensation and the ability to manage the motor's voltage angle, resulting in improved torque control at lower speeds.
What is Flux Vector Control and how does it differ from Sensorless Vector Control?
-Flux Vector Control builds on the Volts per Hertz method by adding additional components like a current resolver, which identifies flux and torque-producing currents. This allows for more precise motor control compared to Sensorless Vector Control, which does not include these advanced components.
What is the role of the current resolver in Flux Vector Control?
-The current resolver in Flux Vector Control helps identify the flux and torque-producing currents in the motor. This data is used by other components in the drive to improve motor control precision.
How does the current regulator in Flux Vector Control improve motor performance?
-The current regulator in Flux Vector Control replaces the current limit block, providing more accurate motor control by regulating the motor's current based on real-time data from the current resolver.
Does Flux Vector Control still rely on frequency as the output reference?
-Yes, even with the added improvements, Flux Vector Control still uses a frequency reference as the output, but it significantly enhances torque and flux control within the motor.
What are the key benefits of using Sensorless Vector and Flux Vector Control methods?
-The key benefits of Sensorless Vector and Flux Vector Control methods include improved torque control, better low-speed performance, and more precise motor speed control, especially under varying loads. These methods are ideal for applications requiring higher performance than Volts per Hertz can offer.
Outlines
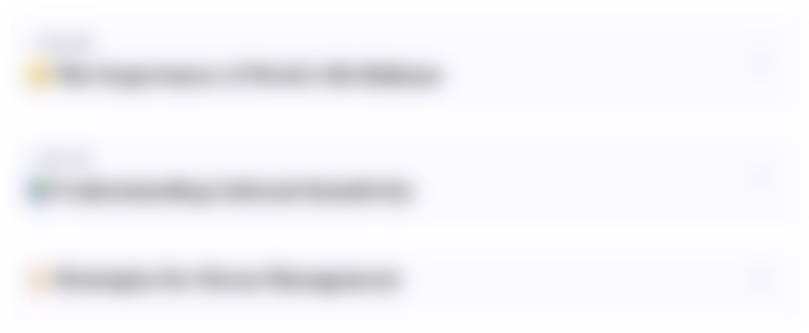
此内容仅限付费用户访问。 请升级后访问。
立即升级Mindmap
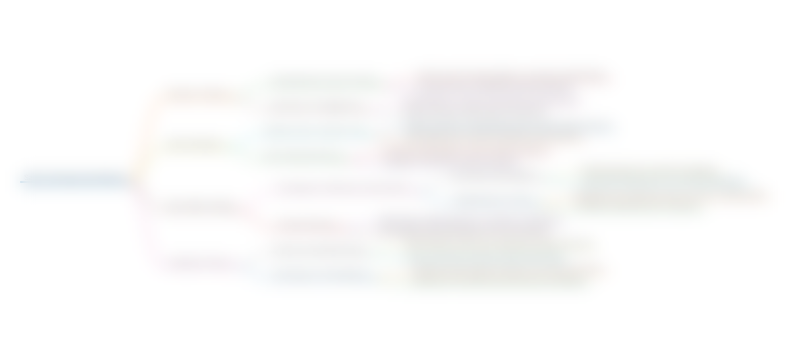
此内容仅限付费用户访问。 请升级后访问。
立即升级Keywords
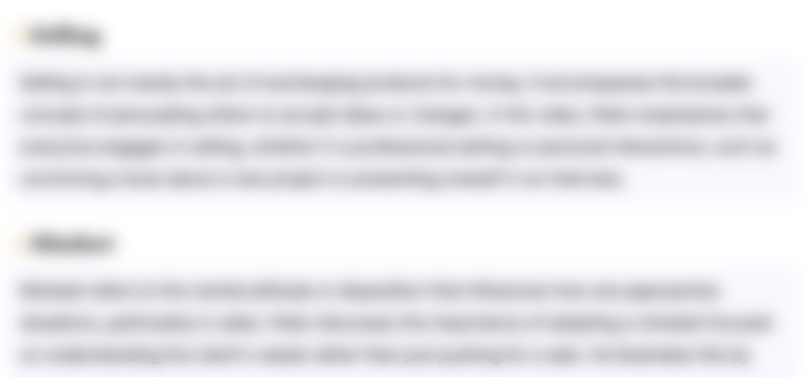
此内容仅限付费用户访问。 请升级后访问。
立即升级Highlights
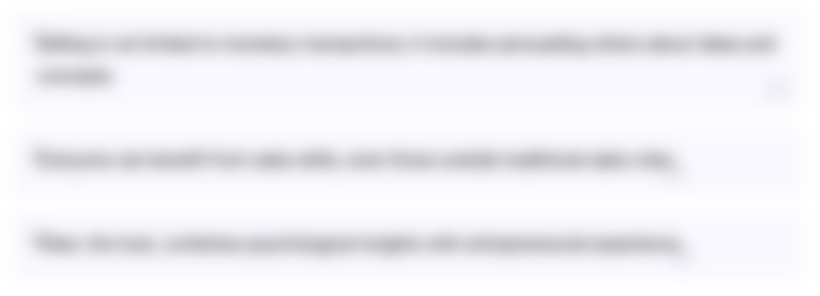
此内容仅限付费用户访问。 请升级后访问。
立即升级Transcripts
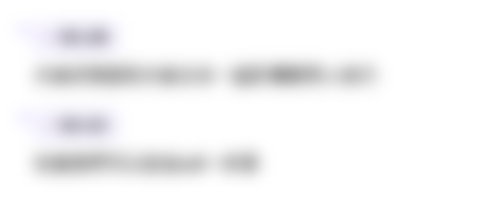
此内容仅限付费用户访问。 请升级后访问。
立即升级浏览更多相关视频
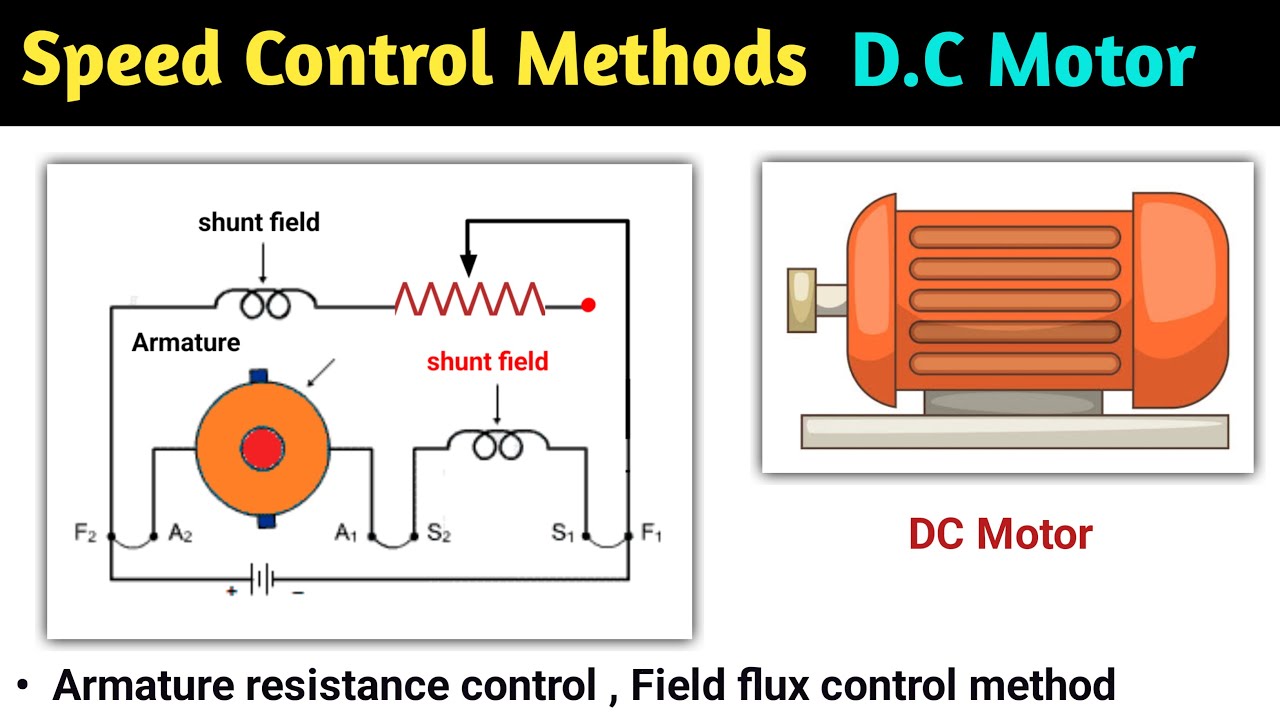
speed control of dc motor | speed control of dc shunt motor | dc motor speed control | series motor
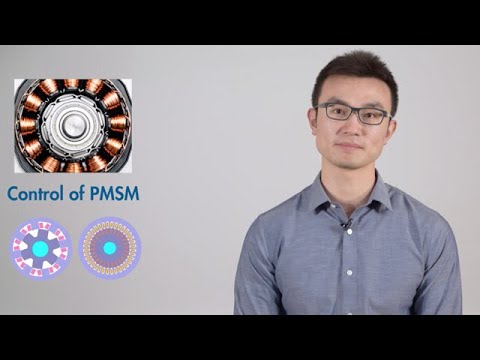
Motor Control Design with MATLAB and Simulink
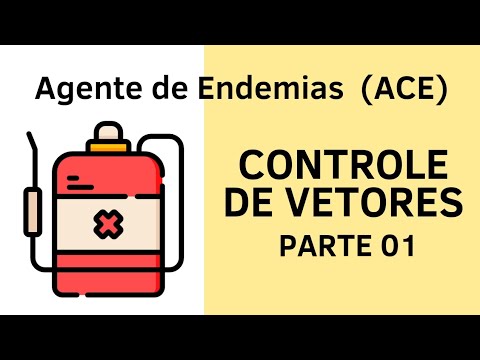
Controle de Vetores - Agente de Combate à Endemias e Agente Comunitário de Saúde - Aula 01
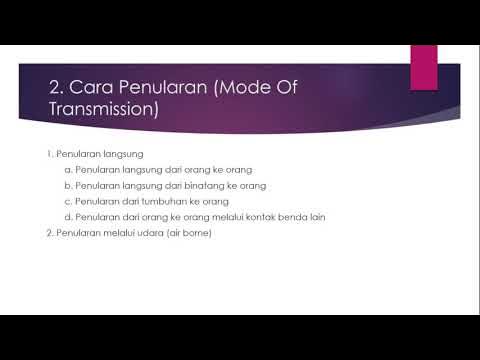
Mekanisme Penularan Penyakit dari Orang ke Orang
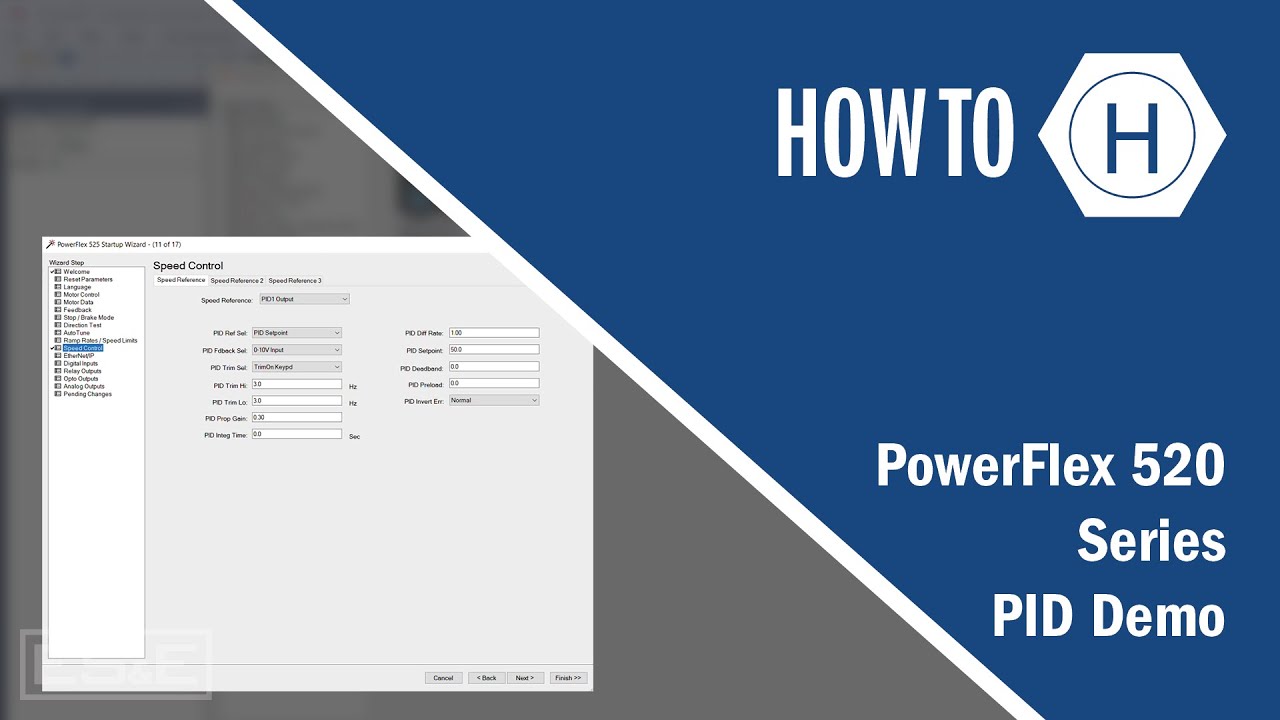
PowerFlex 520 Series PID Demo
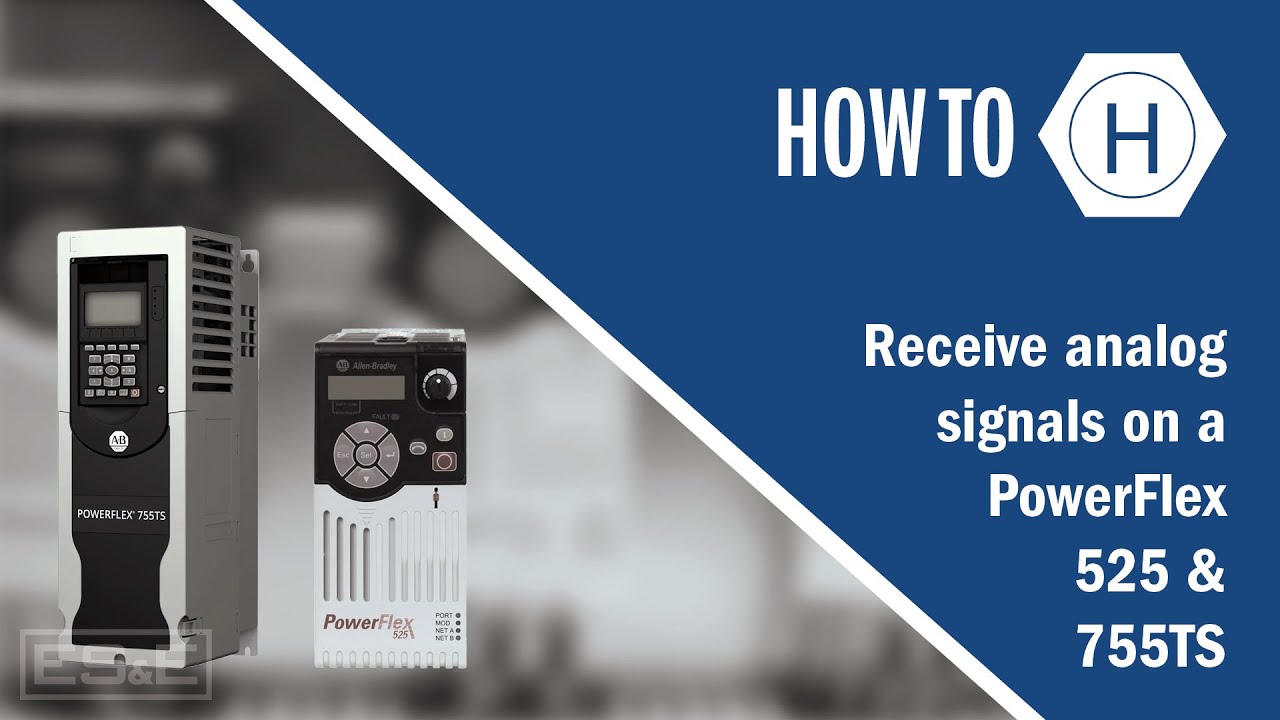
Receive Analog Signals on a PowerFlex 525 & 755TS
5.0 / 5 (0 votes)