Four Principles – Lean Manufacturing & TPM
Summary
TLDRThis video introduces Total Productive Maintenance (TPM), a proactive strategy for enhancing manufacturing processes by integrating preventive maintenance, quality control, and employee engagement. It highlights the pitfalls of reactive maintenance, which leads to increased downtime and costly repairs. TPM focuses on building comprehensive equipment databases, standardizing maintenance processes, providing employee training, and fostering a culture of cleanliness and continuous improvement. By implementing TPM, companies can reduce breakdowns, improve operational efficiency, and create a collaborative environment where every employee contributes to equipment maintenance.
Takeaways
- 😀 TPM (Total Productive Maintenance) is crucial for avoiding equipment breakdowns and minimizing downtime.
- 🔧 Preventive maintenance combined with total quality control enhances the manufacturing process.
- 📊 Understanding equipment history helps in proactive maintenance rather than reactive repairs.
- 🛠️ A database for each piece of equipment should be established based on supplier recommendations and operating conditions.
- 📅 Standardizing processes and scheduling routine maintenance is vital for optimal machine performance.
- 🌟 Each team member plays a role in maintaining a clean and safe work environment, which helps prevent equipment failure.
- 🔍 Regular cleaning can identify potential issues early, avoiding sudden breakdowns.
- 📦 Analyzing spare parts usage ensures that frequently worn parts are always in stock for quick replacements.
- 🚀 Implementing a pit-stop approach helps in analyzing operations and making necessary improvements.
- 📈 Continuous monitoring of key process indicators is essential for ongoing improvement in the TPM system.
Q & A
What is Total Productive Maintenance (TPM)?
-TPM is a lean approach to improving the manufacturing process, combining preventive maintenance, total quality control, and total employee involvement to eliminate equipment-related losses.
What are the consequences of neglecting routine maintenance?
-Neglecting routine maintenance can lead to increased downtime, larger repair costs, and more significant operational disruptions when equipment breaks down.
How does TPM differ from traditional maintenance programs?
-Unlike traditional maintenance programs, which often focus only on repairs after breakdowns, TPM emphasizes proactive maintenance, quality control, and employee involvement across the organization.
What are the key components of implementing TPM?
-Implementing TPM involves building a database for equipment history, standardizing processes, training employees, scheduling planned maintenance, and continuously monitoring key performance indicators.
Why is having an equipment history database important?
-An equipment history database helps teams understand how equipment functions, anticipate maintenance needs, and eliminate guesswork in managing maintenance tasks.
What role do employees play in the TPM approach?
-Employees are actively involved in maintaining a clean and safe work environment, understanding equipment maintenance needs, and participating in the continuous improvement process.
What are the seven pillars of TPM?
-The seven pillars of TPM include focused improvement, autonomous maintenance, planned maintenance, quality maintenance, training and education, early equipment management, and safety, health, and environment.
How does planned maintenance benefit machine performance?
-Planned maintenance improves machine performance by scheduling routine maintenance actions at recommended intervals, which helps prevent sudden breakdowns and enhances overall efficiency.
What is the 'pit-stop approach' mentioned in the script?
-The 'pit-stop approach' refers to trialing standard operating procedures and analyzing what works and what doesn't, allowing for adjustments to continuously improve processes.
How can TPM lead to reduced breakdowns and quality issues?
-By establishing a structured maintenance and improvement process, TPM helps identify and resolve potential issues early, thereby reducing equipment breakdowns and maintaining consistent product quality.
Outlines
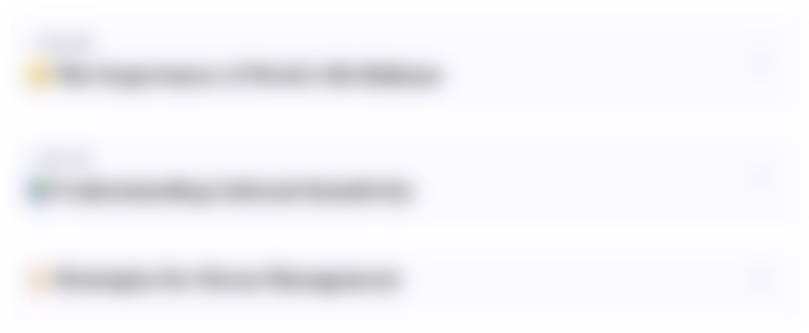
此内容仅限付费用户访问。 请升级后访问。
立即升级Mindmap
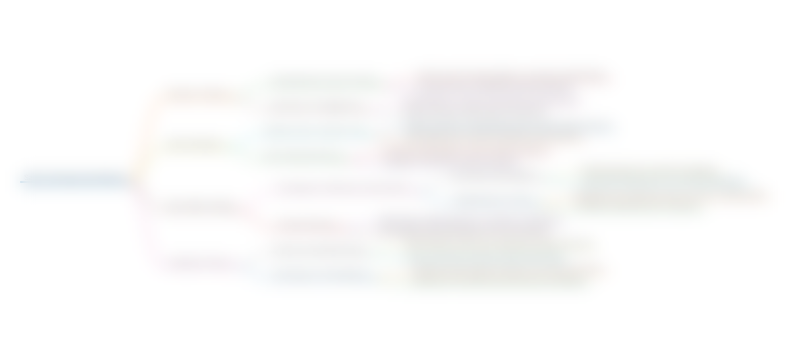
此内容仅限付费用户访问。 请升级后访问。
立即升级Keywords
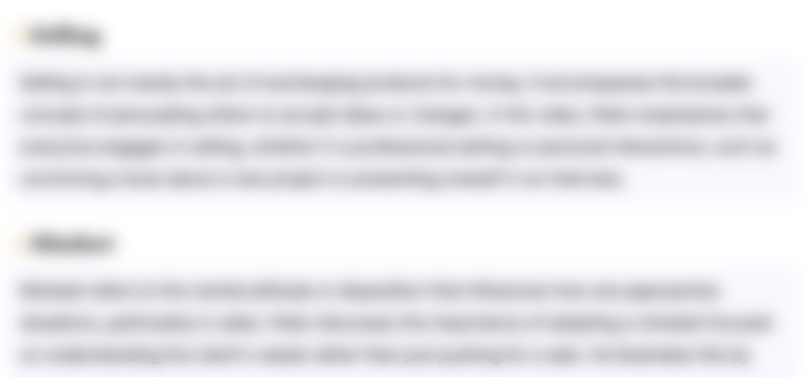
此内容仅限付费用户访问。 请升级后访问。
立即升级Highlights
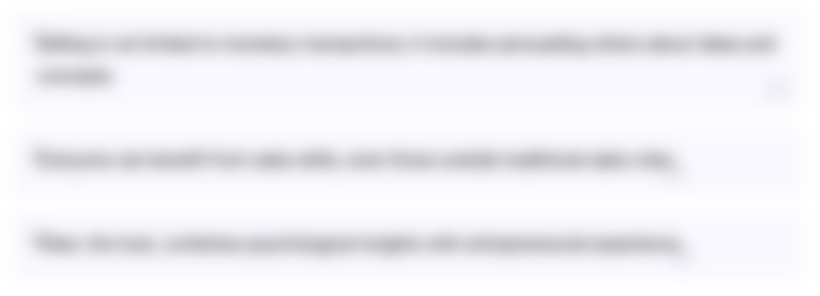
此内容仅限付费用户访问。 请升级后访问。
立即升级Transcripts
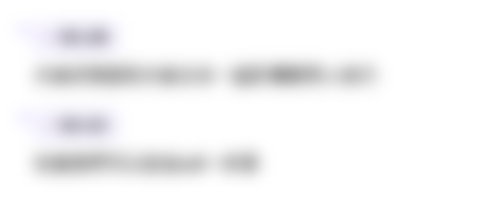
此内容仅限付费用户访问。 请升级后访问。
立即升级浏览更多相关视频
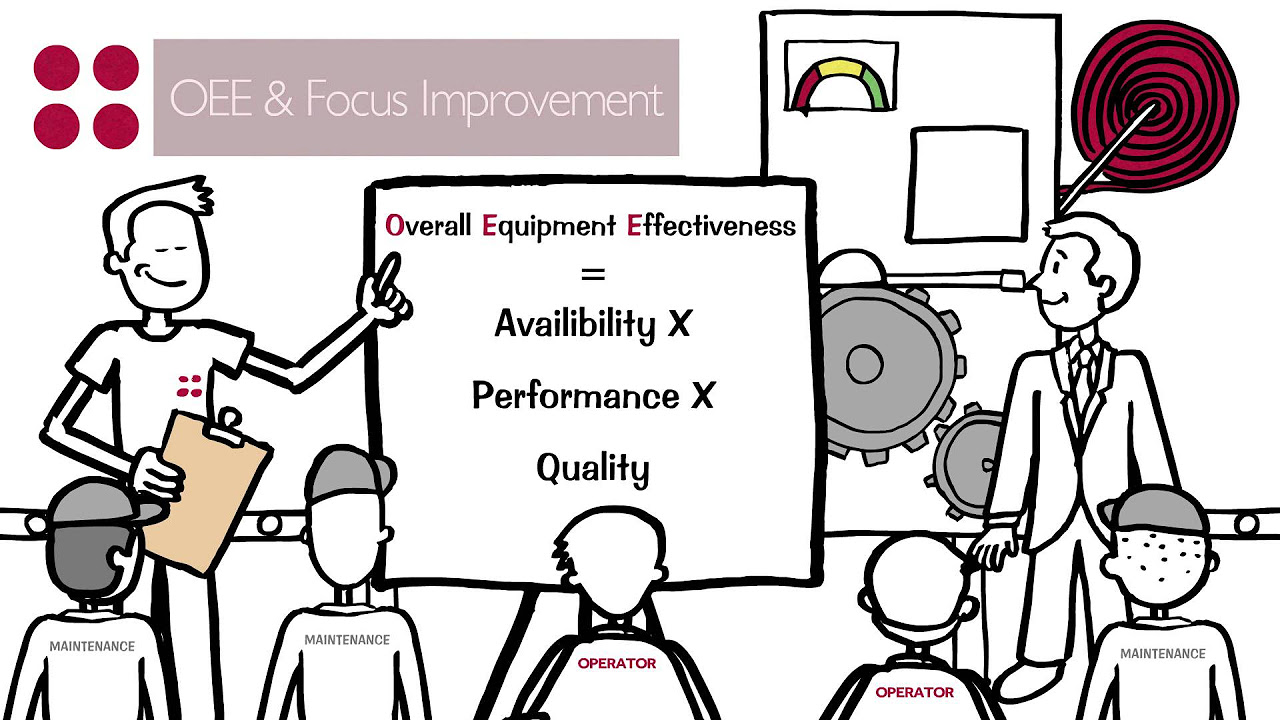
Four Principles TPM

What is TPM -Total Productive Maintenance ? | 8 TPM pillars Total Productive Maintenance

How 7 Companies Mastered TPM (Total Productive Maintenance)
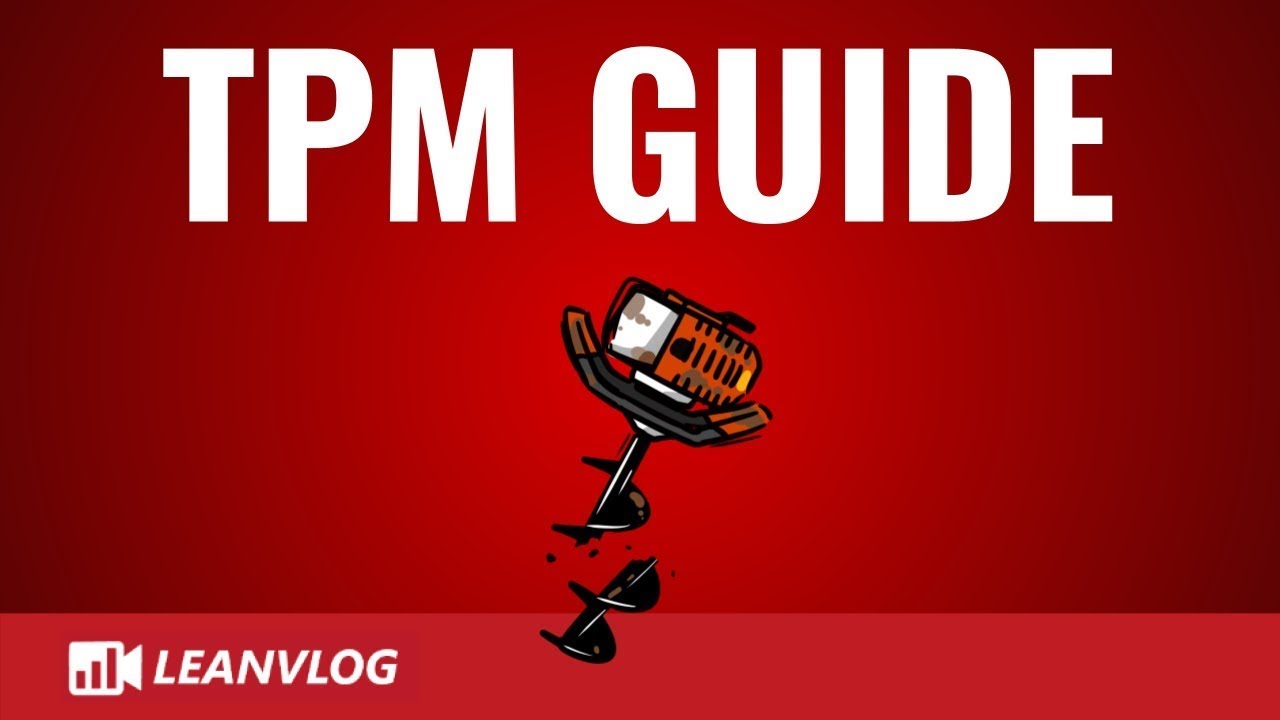
What is Total Productive Maintenance | 8 Pillars of TPM | 6 Big Losses | Type of Maintenance
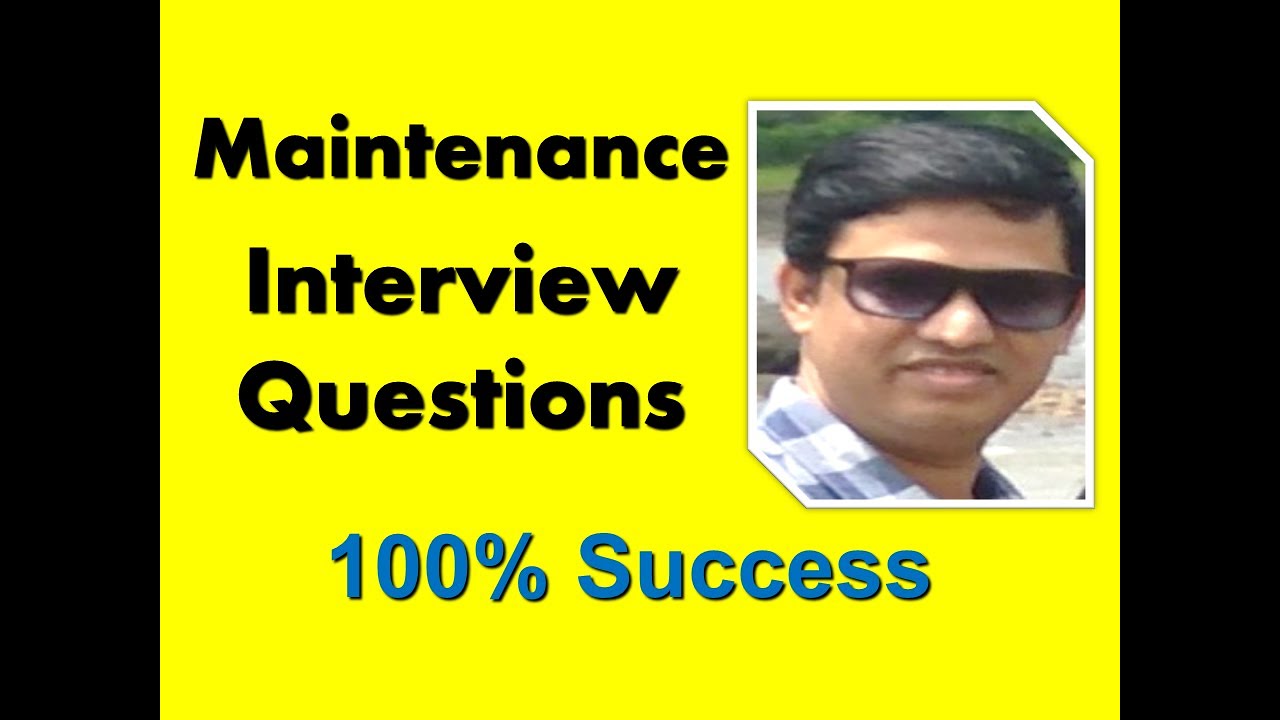
Interview Questions for Maintenance Engineers
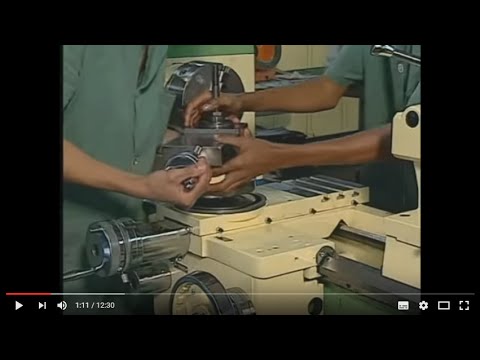
Telecurso 2000 Manutenção 01 Introdução a manutenção
5.0 / 5 (0 votes)