Should you Balance Capacity with Demand? | Rowtons Training by Laurence Gartside
Summary
TLDRLaurence Gartside explains why perfectly balancing capacity with demand in operations management is often a flawed strategy. Despite a cashier's capacity to serve 60 customers per hour matching the average demand, variations in both customer arrivals and service times lead to perpetual queues. Aiming for 100% utilization exacerbates the issue, causing waiting times to increase drastically. Instead, businesses should accept some idle time to maintain efficient service.
Takeaways
- 🧐 Balancing capacity with demand might seem efficient but often leads to long queues and customer dissatisfaction.
- 😤 Customers get frustrated when they encounter long waiting times, even if the business appears to have the right number of staff.
- 🛒 Supermarkets and other businesses face challenges in predicting customer arrival patterns and matching them with cashier availability.
- ⏰ Demand varies throughout the day, leading to periods of inactivity for cashiers and periods of queue growth.
- 📉 Lost capacity, such as when no customers arrive during a cashier's available minute, cannot be recouped.
- 📈 Queues can grow indefinitely if demand consistently outpaces capacity, especially in businesses operating 24/7.
- 💼 Operations managers must consider the impact of aiming for 100% utilization when there is variability in both demand and capacity.
- 🔍 Reducing variability in demand or capacity is challenging, especially in customer-facing businesses like supermarkets.
- 🏢 The decision on how much capacity to provide is crucial and involves balancing the cost of additional staff or equipment against customer wait times.
- 📊 Queue times increase significantly when utilization rates exceed 70-80%, depending on the level of variability.
- 🔗 It's important for businesses to plan capacity utilization carefully to avoid excessive waiting times and potential loss of customers.
Q & A
Why is balancing capacity with demand often a bad idea?
-Balancing capacity with demand can lead to long queues and customer dissatisfaction because of the inevitable variation in both demand and capacity. When demand and capacity rates match, the system can never catch up, leading to a perpetual queue that grows throughout the day.
What is the example given in the script to illustrate the problem with balancing capacity and demand?
-The script uses the example of a convenience store with one cashier who can serve 60 people per hour and historical demand data showing an average of 60 customers per hour. Despite this seeming balance, the reality is that the queue would continue to grow due to the variability in customer arrival times and service times.
How does the variation in customer arrival times affect the queue length?
-Variation in customer arrival times causes the queue to grow because when no customers arrive, the cashier's capacity is wasted, and when multiple customers arrive at once, the cashier can only serve one at a time, causing the queue to build up.
What is the role of capacity variation in the supermarket cashier scenario?
-Capacity variation, such as the cashier sometimes taking longer to serve a customer, contributes to the problem of queues. It adds to the unpredictability and can cause the queue to grow faster than if there was no variation.
Why can't the cashier catch up with the queue?
-The cashier can't catch up with the queue because the losses in capacity when no customers arrive cannot be recouped, and when two or more customers arrive at once, the cashier can only serve one, leaving the other to wait, thus the queue persists.
What is the impact of aiming for 100% utilization on queue times?
-Aiming for 100% utilization exacerbates the problem because any variation in demand leads to increased queue times. This is because there is no buffer to handle fluctuations in customer arrivals, leading to longer waiting times.
How does the concept of capacity utilization relate to different types of businesses?
-Capacity utilization is a critical concept across various businesses, including car factories, doctor's surgeries, call centers, and restaurant kitchens. It involves deciding how much capacity to have relative to the expected demand and understanding the trade-offs between underutilization and queue times.
What is the recommended level of utilization to avoid drastic increases in queue times?
-The script suggests that queue times start to increase drastically when utilization goes above 70 to 80 percent, depending on the level of variation. This implies that businesses should aim for less than 100% utilization to manage queue times effectively.
What are some strategies to reduce the variation of demand and capacity?
-Strategies to reduce variation include improving service time consistency, such as cashier training, and managing customer expectations, such as through预约系统 or peak-time pricing. However, these strategies may not always be feasible or desirable depending on the business model.
Why is it not practical to make customers book appointments with the cashier?
-Making customers book appointments with the cashier is not practical for supermarkets because it goes against the spontaneous nature of grocery shopping and would likely deter customers, leading to a loss of business.
What is the final advice given by Laurence Gartside regarding capacity management?
-Laurence Gartside advises that while it's tempting to aim for 100% capacity utilization to take on more work, businesses should be wary of the resulting increase in waiting times and queues. He suggests getting comfortable with some unused capacity to ensure better customer service.
Outlines
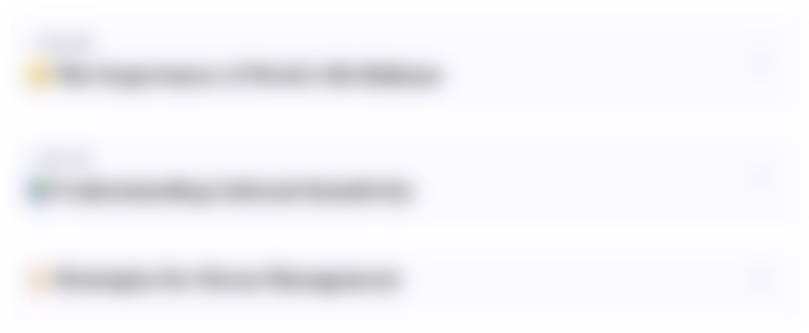
此内容仅限付费用户访问。 请升级后访问。
立即升级Mindmap
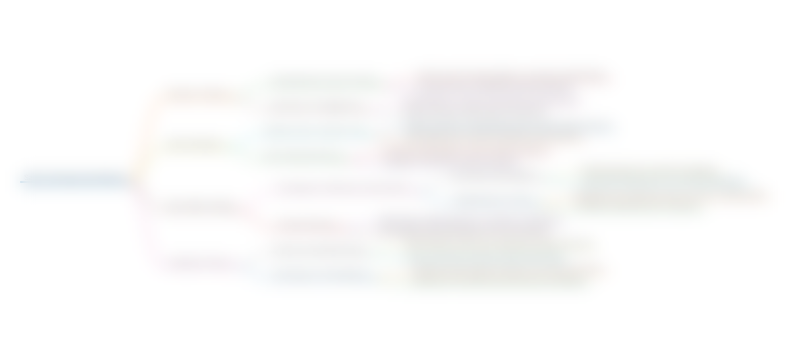
此内容仅限付费用户访问。 请升级后访问。
立即升级Keywords
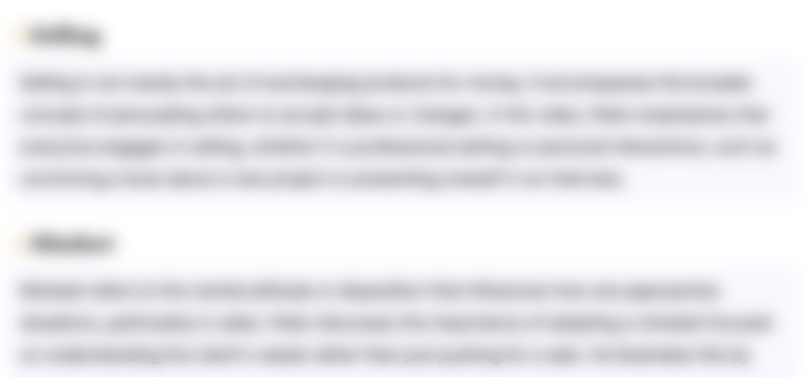
此内容仅限付费用户访问。 请升级后访问。
立即升级Highlights
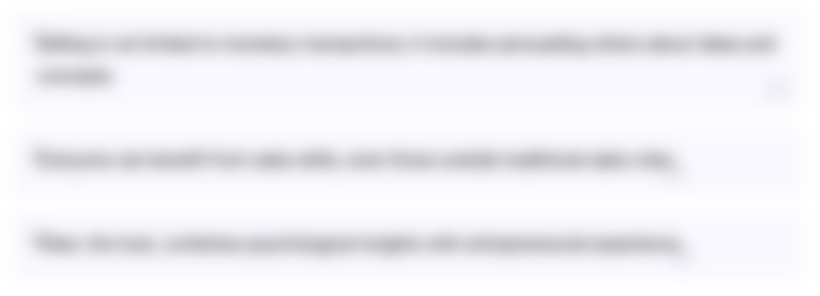
此内容仅限付费用户访问。 请升级后访问。
立即升级Transcripts
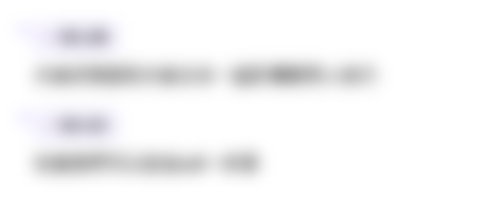
此内容仅限付费用户访问。 请升级后访问。
立即升级浏览更多相关视频
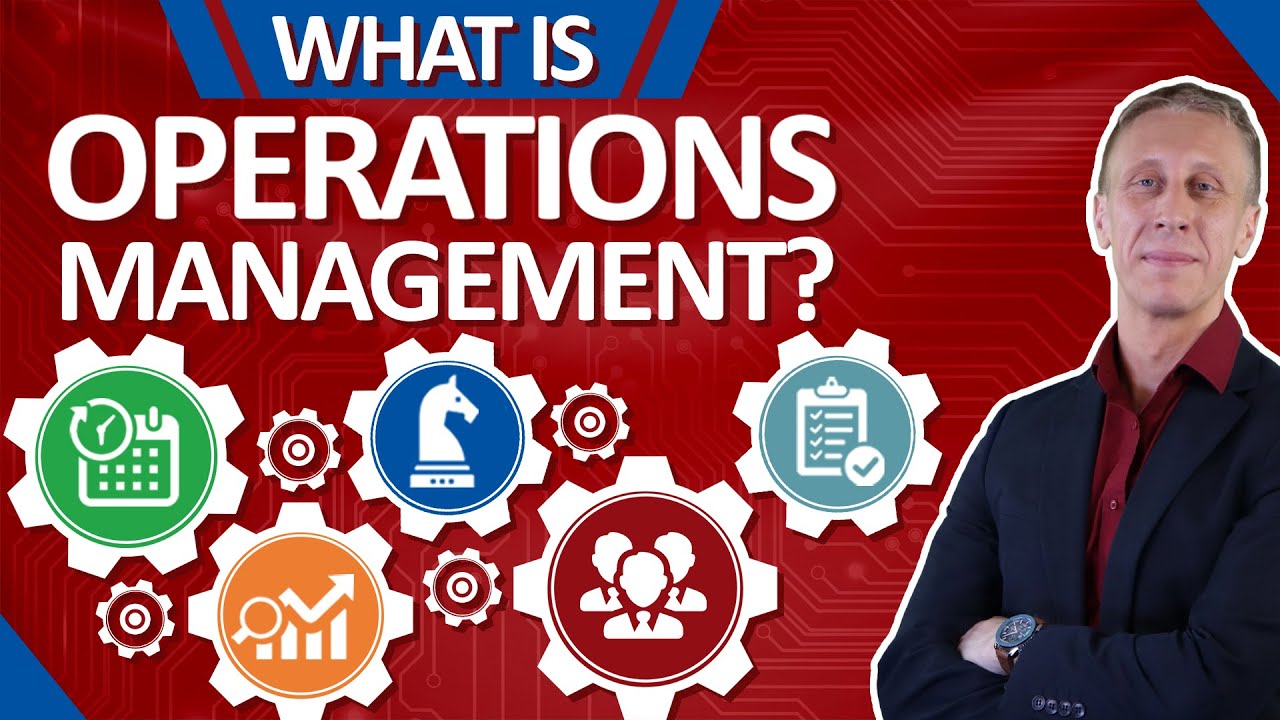
What is Operations Management? | Rowtons Training by Laurence Gartside

Capacity Management (No Background Music)

Storage capacity of Distribution Reservoir | Mass Curve Method

Liane Okdinawati: Strategic Capacity (Part 2)

Lecture 9: Managing productive capacity and customer demand

What is Demand Management?
5.0 / 5 (0 votes)