What is Operations Management? | Rowtons Training by Laurence Gartside
Summary
TLDRLaurence Gartside from Rowtons Training demystifies operations management, highlighting its role in orchestrating the processes behind an organization's core products and services. The video explains how operations managers oversee daily activities, transforming inputs into valuable outputs across various industries. It covers key operational functions like demand forecasting, capacity planning, and performance management, emphasizing the discipline's importance in aligning operational strategy with business objectives for competitive advantage.
Takeaways
- 🔧 Operations management is the discipline that oversees the processes and activities involved in creating and delivering an organization's core products and services.
- 🛠️ Business operations encompass the daily activities necessary for an organization to create value and generate profit, functioning alongside other departments like marketing and finance.
- 🚀 Operations are about 'doing': making, helping, and delivering the real work that satisfies customer needs.
- ⛏️ Examples of operations include a coal mine extracting coal, an airline transporting passengers, a restaurant serving food, and a digital marketing agency creating content.
- 🔄 The transformation of inputs like labor, machinery, materials, and expertise into higher value outputs is a key function of operations.
- 📈 Operations management involves coordinating resources, forecasting demand, capacity planning, and demand management to ensure efficient operations.
- 📊 Scheduling is a critical part of operations management, involving planning and decision-making regarding job sequences and responding to disruptions.
- 📝 Resource requirements planning is essential for operations, akin to planning a dinner party with guests, dietary needs, shopping lists, and preparation timelines.
- 🏭 Operations management is crucial from the initial design phase of a business, including equipment, staffing, layout, and processes to meet delivery goals and quality standards.
- 📊 Performance management in operations involves setting metrics, collecting data, analyzing, and acting on it to improve and track operational efficiency.
- 🌟 Effective operations management is about creating value by designing and running systems and processes that are both effective and efficient.
Q & A
What is operations management?
-Operations management is the discipline of managing the activities and processes that create and deliver an organization's core products and services.
Who is Laurence Gartside and what does he do?
-Laurence Gartside is a professional who provides online training and consultation in business operations management through his site, Rowtons Training.
What are business operations?
-Business operations are the core daily activities that an organization performs to create value and earn a profit, alongside other primary functions like marketing or finance.
How do operations transform inputs into outputs?
-Operations transform inputs such as labor, machinery, materials, energy, and expertise into higher value outputs, such as coal from a mine or passengers transported by an airline.
What are the fundamental challenges faced by operations managers?
-Operations managers face challenges like designing, planning, running, and improving systems, coordinating input resources, forecasting demand, capacity planning, demand management, scheduling, and resource requirements planning.
What is capacity planning in operations management?
-Capacity planning is the act of making long-term decisions about what the organization wants to be capable of delivering in terms of products or services, both in the short term and far into the future.
How does demand management differ from other aspects of operations management?
-Demand management involves actively influencing and shaping demand to keep it within the organization's capabilities, ensuring a regular flow of work that can be efficiently delivered.
What is the role of scheduling in operations management?
-Scheduling in operations management involves making plans and decisions about when and in what sequence jobs should be done, addressing daily disruptions and urgent changes, as well as strategic decisions for delivery objectives.
Why is resource requirements planning important?
-Resource requirements planning is crucial for ensuring that all necessary resources, such as staff, materials, and equipment, are available and ready when needed to meet operational demands.
How does operations management contribute to the strategic alignment of a business?
-Operations management contributes to strategic alignment by ensuring that the operations strategy supports the overall business strategy, potentially offering a competitive edge through lowest cost, fastest delivery, or highest level of customization.
What is performance management in the context of operations management?
-Performance management in operations management involves designing metrics, collecting data, analyzing, and acting on it to understand what is working well and identify areas for improvement, tracking progress over time.
Outlines
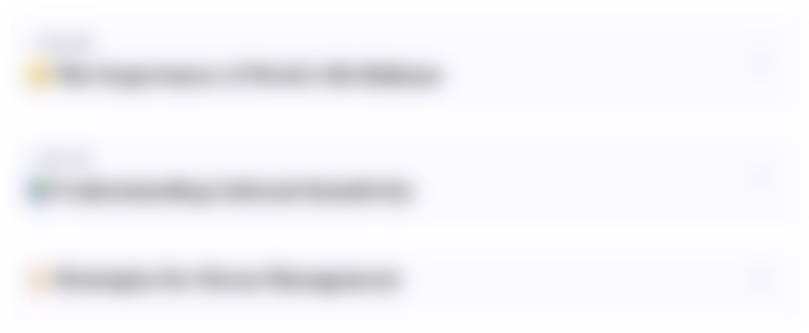
This section is available to paid users only. Please upgrade to access this part.
Upgrade NowMindmap
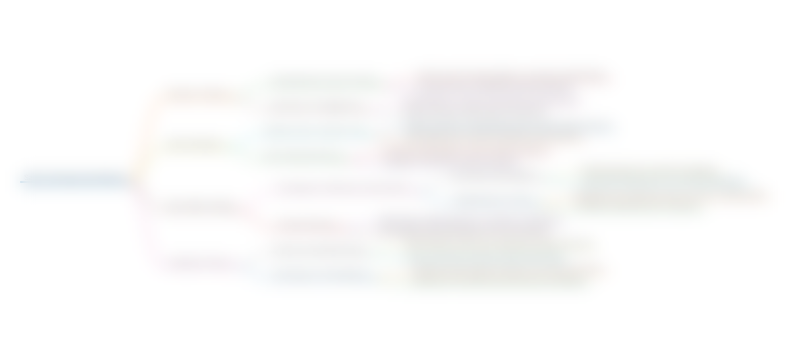
This section is available to paid users only. Please upgrade to access this part.
Upgrade NowKeywords
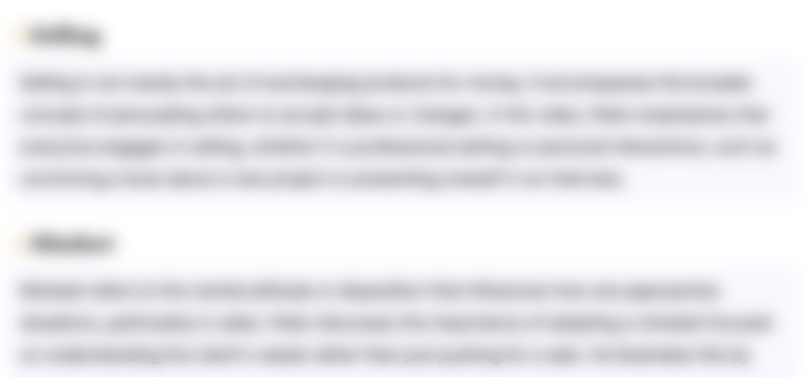
This section is available to paid users only. Please upgrade to access this part.
Upgrade NowHighlights
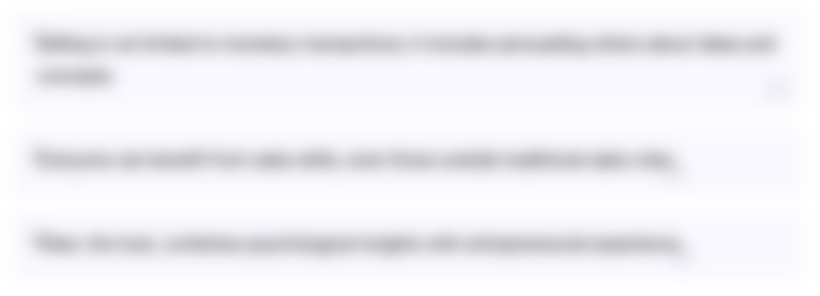
This section is available to paid users only. Please upgrade to access this part.
Upgrade NowTranscripts
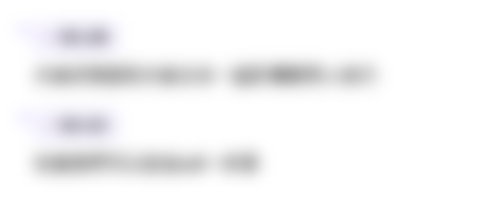
This section is available to paid users only. Please upgrade to access this part.
Upgrade NowBrowse More Related Video
5.0 / 5 (0 votes)