Automation Migration Strategy.
Summary
TLDRThe video explains a common strategy companies use to introduce new products quickly while managing competitive pressures. It describes a phased automation migration strategy, starting with manual production, moving to automated single-station cells, and eventually to fully integrated automated systems. This approach allows companies to adapt their manufacturing processes as product demand increases, reducing costs and risks by gradually introducing automation. The strategy helps avoid premature investment in high-level automation and ensures that production meets growing demand while allowing time for design improvements.
Takeaways
- 🚀 A company often needs to introduce new products quickly due to competitive pressures.
- 🛠️ The easiest and least expensive method to achieve this is by designing a manual production system using independent workstations.
- ⚙️ Tooling for manual production can be fabricated quickly and at low cost, which allows for rapid product introduction.
- 🔄 If demand increases, manual workstations can be replicated to produce sufficient quantities.
- 📈 As demand grows and high future demand is anticipated, companies often transition to automation.
- 🏗️ Many companies adopt an automation migration strategy to evolve their manufacturing systems as product demand rises.
- 📊 Phase 1 of the strategy involves manual production using single independent manual workstations, which allows for quick and low-cost startup.
- 🤖 Phase 2 introduces automation to single stations, but work units are still moved between stations manually.
- 🔗 Phase 3 integrates the automated single stations into a fully automated multi-station system with automated transfer of work units between stations.
- ✔️ This phased approach allows companies to gradually introduce automation and avoid committing to full automation prematurely, minimizing risk.
Q & A
What is the main reason a company might need to introduce a new product quickly?
-Competitive pressures in the marketplace often push companies to introduce new products in the shortest possible time.
What is the simplest and least expensive method for starting new product production?
-The simplest and least expensive way is to design a manual production method using a sequence of independent workstations.
Why might a company replicate manual cells during production?
-If more than a single set of workstations is needed to meet demand, companies replicate the manual cell to produce the product in sufficient quantities.
What triggers a company to consider automating production?
-If a product is successful and high demand is anticipated, it makes sense for the company to automate production to reduce labor and increase production rate.
What are the three phases of a typical automation migration strategy?
-The three phases are: 1) Manual production using single-station manned cells; 2) Automated production with single-station automated cells; 3) Automated integrated production with multi-station automated systems.
Why is manual production often used in phase 1 of the automation migration strategy?
-Manual production is used in phase 1 because it allows quick and low-cost tooling, enabling fast introduction of the new product.
What happens in phase 2 of the automation migration strategy?
-In phase 2, the single workstations are automated to reduce labor and increase production rate, but work units are still moved manually between stations.
At what point does a company move to phase 3 in the automation migration strategy?
-A company moves to phase 3 when it is certain that the product will be produced in mass quantities for several years, justifying the integration of automated cells into a multi-station automated system.
What are the advantages of following an automation migration strategy?
-The advantages include quick product introduction, gradual automation as demand grows, the ability to make engineering changes, and avoiding premature investment in full automation.
How does the automation migration strategy reduce risks for companies?
-It avoids the risk of committing to a high level of automation from the start, which may not be justified if demand for the product doesn't grow as expected.
Outlines
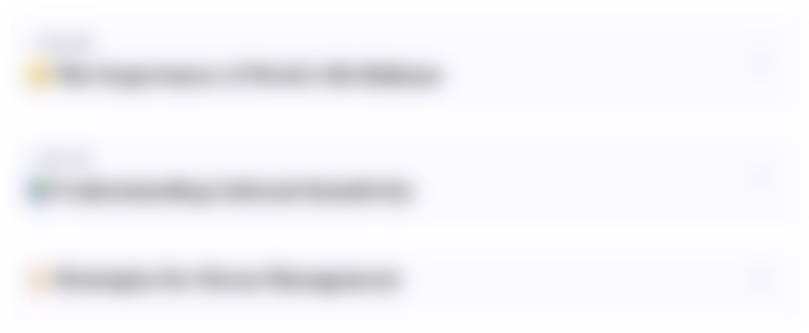
此内容仅限付费用户访问。 请升级后访问。
立即升级Mindmap
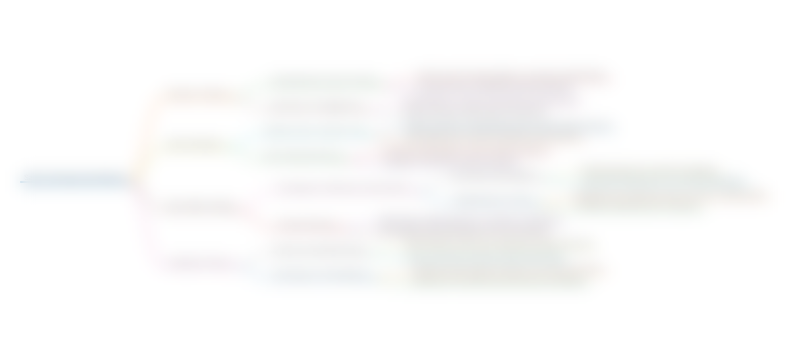
此内容仅限付费用户访问。 请升级后访问。
立即升级Keywords
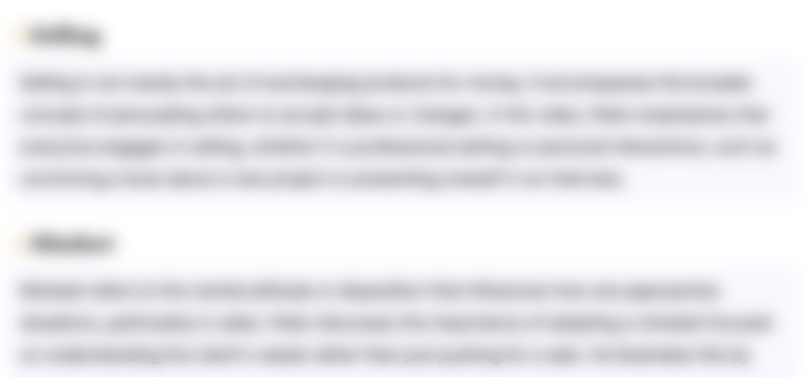
此内容仅限付费用户访问。 请升级后访问。
立即升级Highlights
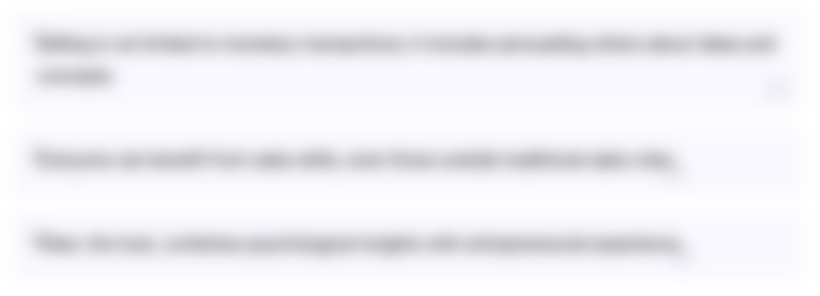
此内容仅限付费用户访问。 请升级后访问。
立即升级Transcripts
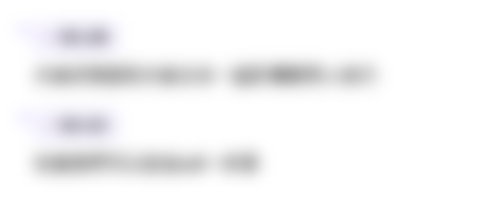
此内容仅限付费用户访问。 请升级后访问。
立即升级5.0 / 5 (0 votes)