Lezione 4D - CREAZIONE VSM - Parte 4 di 4 - Lean Thinking e Toyota Producition System - Zero sprechi
Summary
TLDRThe transcript discusses a methodical approach to improving production processes by analyzing cycle times and lead times to meet customer demand. It emphasizes the importance of aligning production capacity with customer orders and identifying bottlenecks. The speaker introduces the concept of Value Stream Mapping (VSM) to visualize and streamline the production process, reduce waste, and improve efficiency. Strategies such as Just-In-Time production, Heijunka, and the implementation of 5S and 7 Muda are explored to achieve a more responsive and customer-focused manufacturing system.
Takeaways
- 🕒 The 'process cycle efficiency' is calculated by dividing the total cycle time by the total lead time, which helps to understand production capacity in relation to customer demand.
- 🏭 Launching production with 'distro g' is crucial to highlight whether production capacity can meet the top time required by the customer.
- 🔍 Analyzing the 'tac time' (time available for production) against the customer's daily demand helps to determine if current machinery and departments can meet the required output.
- 📈 A visual representation of process times on a graph can reveal if the current process can meet customer demand, and if not, where the bottlenecks are in the production line.
- 🔧 Implementing additional techniques such as extra shifts or machinery may be necessary to address bottlenecks and increase production capacity.
- 🗓️ The 'future state' in the value stream map is defined by identifying and eliminating waste, with the aim of improving the current state to meet future goals.
- 🚀 The 'future state' should focus on reducing lead times and improving responsiveness to customer demand, moving from production based on forecasts to production based on actual customer orders.
- 🔎 A thorough analysis of waste, including known and consultant-identified waste, is essential for improving the production process.
- 📝 The '5S' and '7 Muda' principles are applied to identify areas for improvement and to streamline the production process.
- 👥 Establishing a 'Kaizen event' with dedicated teams to tackle identified issues is a structured approach to continuous improvement.
- ✅ Defining a standard procedure as a result of each improvement activity ensures that changes are sustainable and can be replicated across the organization.
Q & A
What is the final result of the process cycle efficiency?
-The final result of the process cycle efficiency is the total cycle time, which is the sum of all cycle times and lead times, allowing one to calculate the process cycle efficiency by dividing the total cycle time by the total lead time.
Why is it important to launch production with a 'distro g'?
-Launching production with a 'distro g' is important because it highlights whether the production capacity can sustain the top time required by the customer's demand, ensuring that each machine or department can meet the daily production target.
How does the script define the takt time in the context of customer demand?
-The takt time is defined as the time available to produce one unit of a product, calculated by dividing the available working time by the customer's daily demand. For example, if the customer requires 265 pieces per day and the working time is 8 hours, the takt time would be 8 hours * 60 minutes * 60 seconds / 265 pieces.
What does the script suggest to do if the production process cannot meet the customer's demand?
-If the production process cannot meet the customer's demand, the script suggests implementing additional techniques such as adding another shift, using more machines, or addressing bottlenecks to increase production capacity.
What is the purpose of identifying waste in the production process?
-The purpose of identifying waste in the production process is to define the future state of the business by eliminating inefficiencies and improving the overall process, which can lead to better customer satisfaction and reduced lead times.
How does the script suggest improving the production process?
-The script suggests improving the production process by identifying and eliminating waste, applying 5S methodology, and implementing continuous flow and pull systems where applicable to reduce lead times and increase efficiency.
What is the significance of the 'visual stream map' in the context of the script?
-The 'visual stream map' is a tool used to analyze the current state of the production process and define the future state by identifying areas for improvement and implementing corrective actions.
Why is it necessary to involve leadership in the process improvement activities described in the script?
-Involving leadership is necessary because their engagement and belief in the process can motivate the team and ensure that improvements are sustained and integrated into the company's culture.
What are some common types of waste identified in the script?
-Common types of waste identified in the script include overproduction, waiting, transportation, process, inventory, motion, and defects, which are areas where inefficiencies can be reduced to improve the production process.
How does the script propose to handle the issue of excess workload or overburdening employees?
-The script proposes to handle excess workload by implementing lean principles such as reducing batch sizes, leveling production, and improving the layout to create a more efficient and less stressful work environment.
What are the potential pitfalls in designing a visual stream map as mentioned in the script?
-Potential pitfalls in designing a visual stream map include unmotivated teams, incomplete or uncertain data, lack of follow-through on improvement actions, and a lack of ongoing management support and commitment to the process.
Outlines
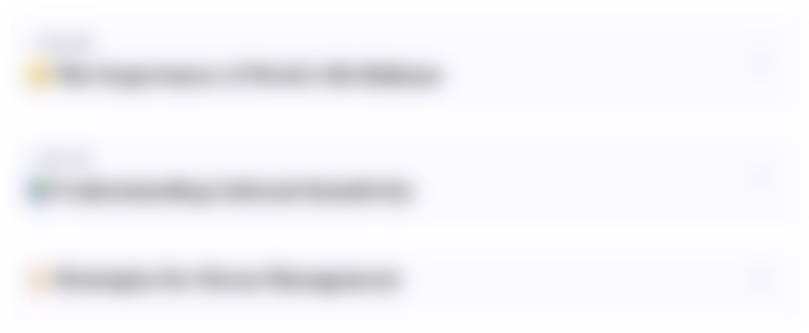
此内容仅限付费用户访问。 请升级后访问。
立即升级Mindmap
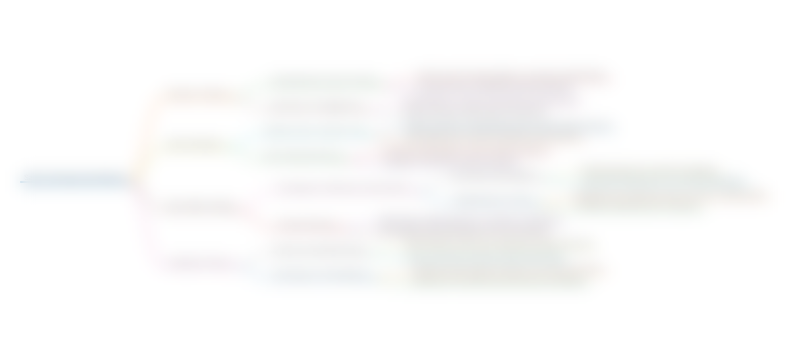
此内容仅限付费用户访问。 请升级后访问。
立即升级Keywords
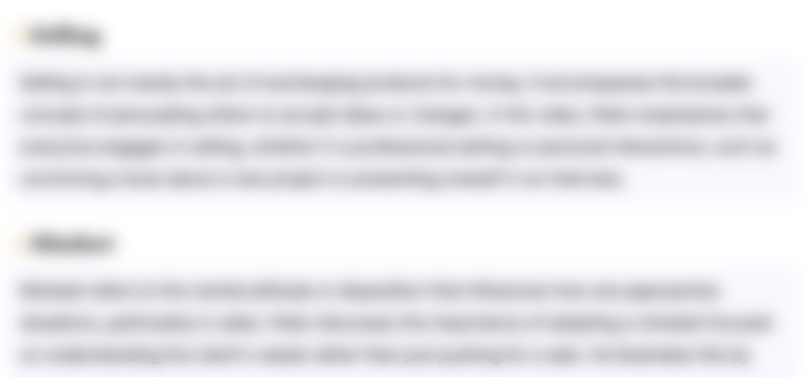
此内容仅限付费用户访问。 请升级后访问。
立即升级Highlights
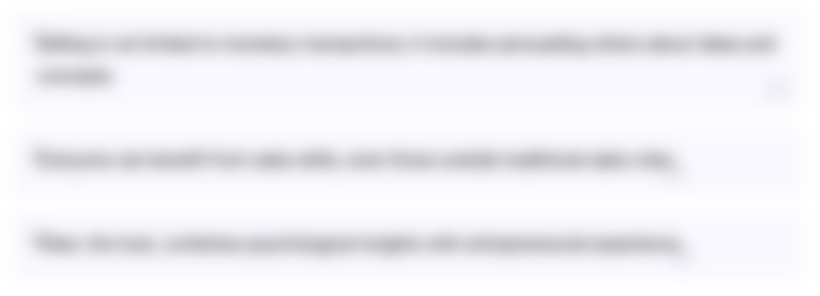
此内容仅限付费用户访问。 请升级后访问。
立即升级Transcripts
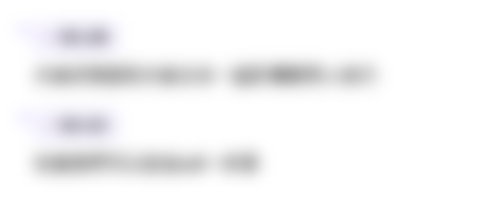
此内容仅限付费用户访问。 请升级后访问。
立即升级5.0 / 5 (0 votes)