Explicación MRP
Summary
TLDRThe transcript discusses Material Requirements Planning (MRP), a systematic approach essential for managing production materials and optimizing inventory. It covers the MRP process, including creating a Master Production Schedule (MPS), determining material needs, and ensuring production efficiency. The video highlights the importance of accurate planning and the role of ERP systems in automating these processes. Challenges such as capacity constraints, defects, and fluctuating lead times are addressed, stressing the need for flexibility in planning. Despite limitations, MRP remains crucial for streamlining production and ensuring that products meet customer demands.
Takeaways
- 😀 MRP (Material Requirements Planning) is a systematic process for managing material inventories and production schedules.
- 😀 The main objective of MRP is to ensure that the right materials are available at the right time, avoiding production delays.
- 😀 MRP helps optimize production by ensuring the correct amount of materials are produced to meet demand efficiently.
- 😀 The process involves creating a master production schedule and breaking it down into required materials for each product.
- 😀 A key feature of MRP is determining the right quantity of components needed for production and the time frame for each step.
- 😀 MRP requires careful consideration of factors such as inventory levels, defect rates, and actual production capacity.
- 😀 One limitation of MRP is that it often assumes fixed production times, which may not align with real-world delays or defects.
- 😀 MRP involves collaboration between different departments, including accounting, HR, and finance, to ensure optimal planning.
- 😀 The process distinguishes between independent and dependent demand, helping tailor material procurement strategies.
- 😀 While MRP can significantly improve production efficiency, it faces challenges due to human resistance to change and integration complexities.
- 😀 Technological tools, such as specialized software, can enhance the accuracy and efficiency of MRP processes, automating much of the planning work.
Q & A
What is the primary purpose of Material Requirements Planning (MRP)?
-The primary purpose of MRP is to ensure that the required materials are available for production at the right time, in the right quantity, and to optimize the production process while maintaining inventory control.
How does MRP help manage inventory in a manufacturing environment?
-MRP helps manage inventory by ensuring that the right materials are ordered based on production schedules and demand, preventing excess stock or shortages, and optimizing storage costs.
What are the main components that MRP takes into account when determining material requirements?
-MRP considers factors like the master production schedule, lead times, inventory levels, and bill of materials to determine the material requirements for production.
What is the difference between independent and dependent demand in the context of MRP?
-Independent demand refers to demand for finished goods, driven by external factors like customer orders, while dependent demand is based on the need for components or raw materials driven by the production of finished goods.
What are the common challenges organizations face when implementing MRP systems?
-Challenges include inaccurate data, lack of integration with other systems, capacity constraints, and dealing with unexpected production delays or defects in materials.
How does MRP handle production schedules and capacity planning?
-MRP integrates production schedules with capacity planning, ensuring that materials are available as needed while considering available resources and labor to avoid overburdening production capacity.
Why is the integration of technology important in MRP systems?
-Technology integration allows for automation, reducing human error and improving efficiency in tracking material requirements, production schedules, and inventory levels. It also provides real-time data for better decision-making.
What role does the master production schedule (MPS) play in MRP?
-The master production schedule (MPS) defines what products need to be produced and when, serving as the foundation for determining material requirements and production planning in MRP.
What are the limitations of MRP mentioned in the script?
-Limitations include the inability to account for capacity constraints, the potential neglect of material defects, and the challenge of maintaining up-to-date and accurate data, especially if manual processes are involved.
How does MRP contribute to customer service and overall productivity?
-MRP improves customer service by ensuring on-time delivery through better material management and production scheduling. It also enhances productivity by reducing downtime and optimizing the use of resources and materials.
Outlines
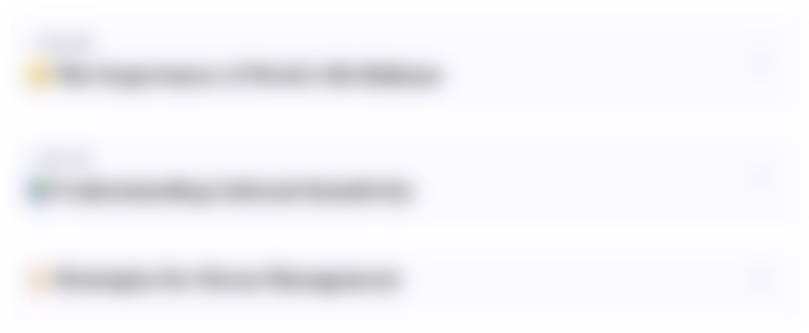
This section is available to paid users only. Please upgrade to access this part.
Upgrade NowMindmap
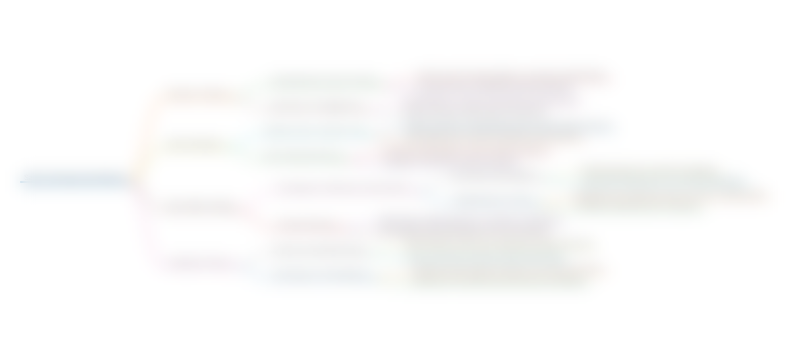
This section is available to paid users only. Please upgrade to access this part.
Upgrade NowKeywords
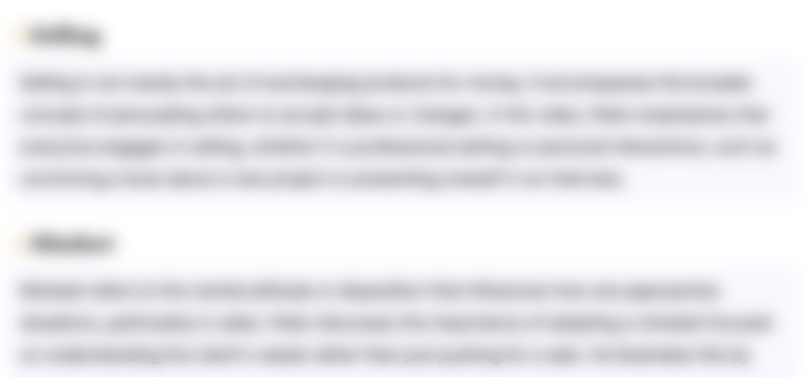
This section is available to paid users only. Please upgrade to access this part.
Upgrade NowHighlights
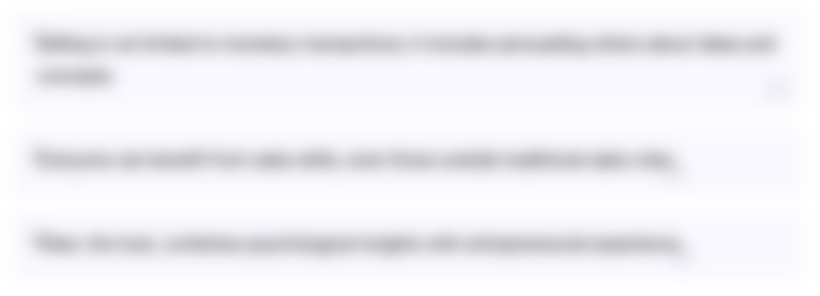
This section is available to paid users only. Please upgrade to access this part.
Upgrade NowTranscripts
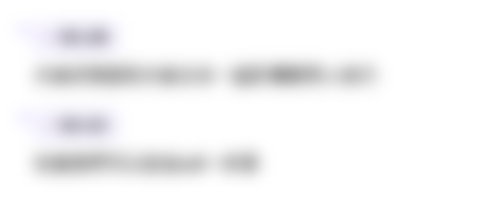
This section is available to paid users only. Please upgrade to access this part.
Upgrade NowBrowse More Related Video
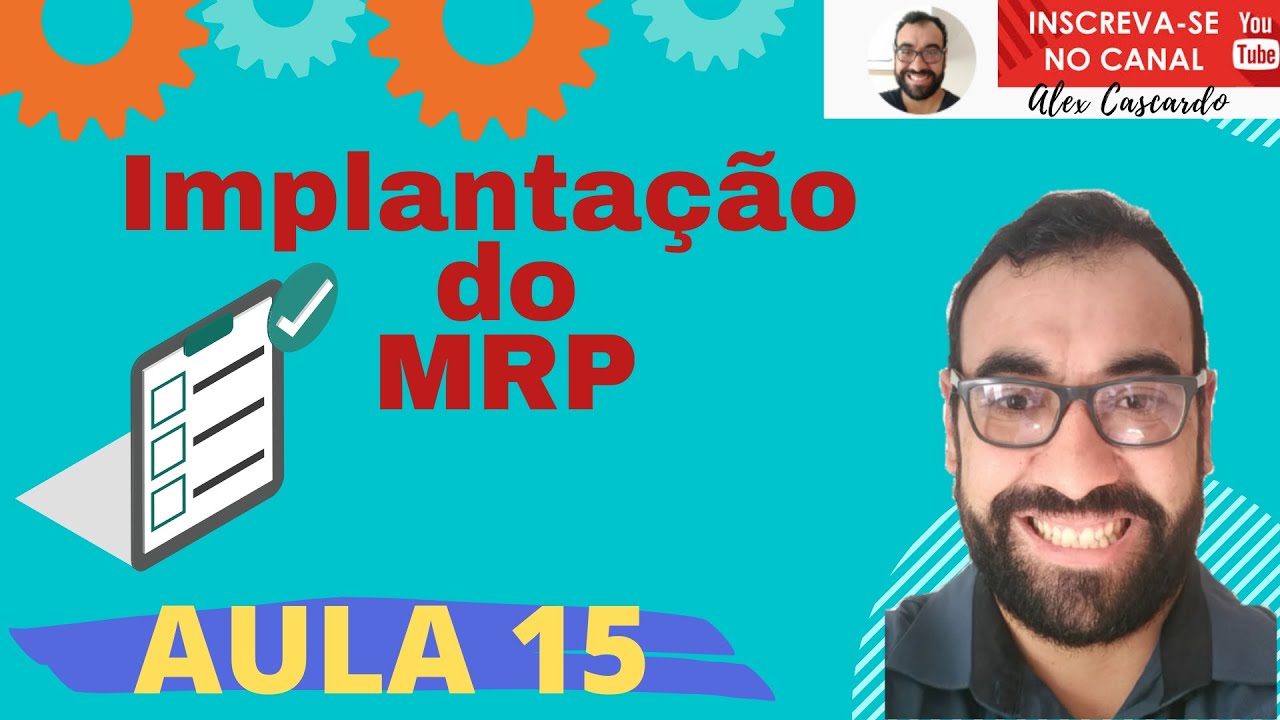
Planejamento e Controle da Produção # 15 – Implantação do MRP

What is the Material Requirement planning (MRP)? | MRP Process
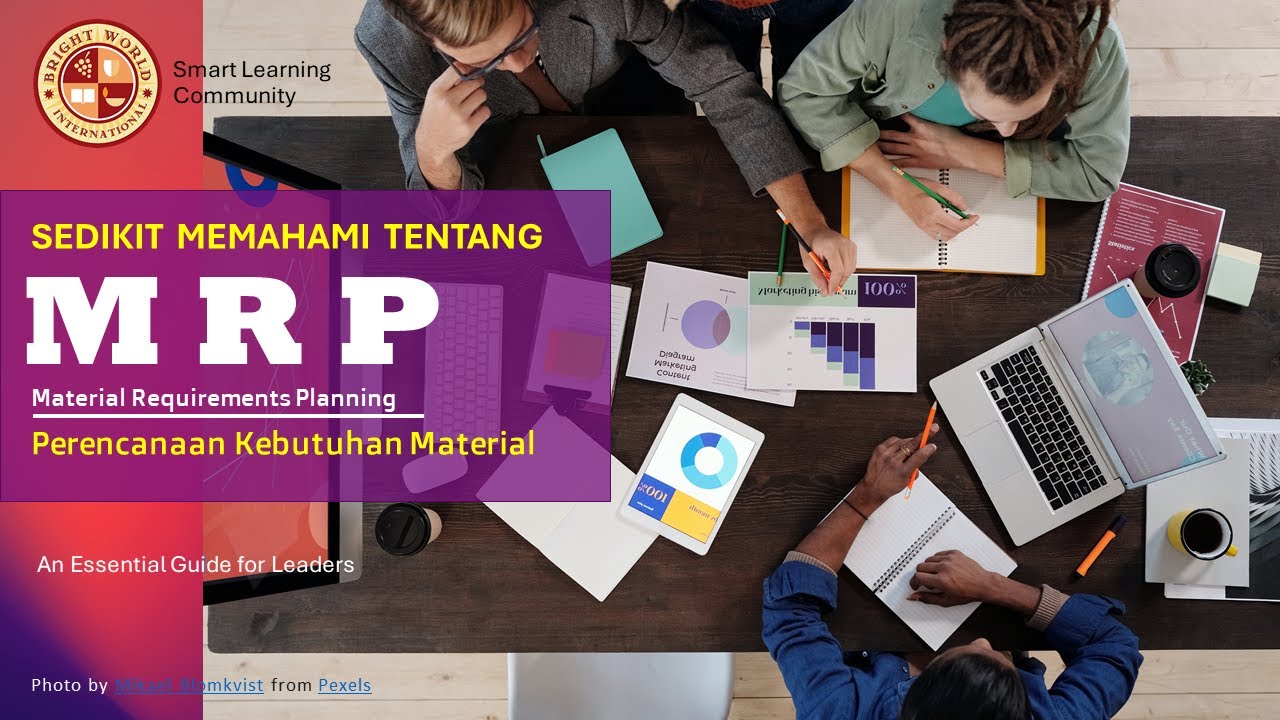
Memahami Perencanaan Kebutuhan Material untuk proses produksi ...
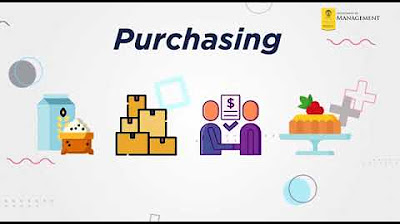
Pengantar Bisnis Sesi 11 Produksi dan Manajemen Operasi

operasi bisnis week #12 master schedule

SAP PP Training for Beginners: A Complete Guide | Proexcellency
5.0 / 5 (0 votes)