What is GD&T? | GD&T symbols Explained with Example | for Beginners Understanding | Subscribe Us
Summary
TLDRThis video script offers an in-depth exploration of GD&T (Geometric Dimensioning and Tolerancing), a critical system in engineering for defining product geometry. It explains the symbolic language used in engineering drawings to specify allowable deviations in size, shape, and location of features on a part. The script covers various tolerance types, datum systems, and geometric characteristics like straightness, flatness, and cylindricity. It also delves into concepts like MMC, LMC, and fit allowances, essential for ensuring parts function correctly together. The video aims to educate on the importance of precise measurements and specifications in manufacturing.
Takeaways
- 📏 GD&T stands for Geometric Dimensioning and Tolerancing, a system used to define the size, shape, and location of features on a part.
- 🔍 Dimensioning is the specification of the size of features like length, angle, or location, while tolerancing defines the allowable variation in these dimensions.
- 📉 There are three types of tolerances: limit, unilateral, and bilateral, each allowing different permissible variations in feature dimensions.
- 📐 A datum is a theoretical exact feature used as a reference for measurements, with primary, secondary, and tertiary datums controlling different degrees of freedom.
- 📏 Datum features are part features that contact a datum and are denoted with capital letters in boxes, connected to the datum with a triangle.
- 🔳 The 14 standard characteristics in GD&T are categorized into form, profile, location, orientation, and run-out types, each with specific control types.
- 🔍 Characteristics like straightness, flatness, and circularity are form type controls that ensure features match their perfect form within a tolerance zone.
- 📏 Profile of a line and surface characteristics are profile type controls that ensure the profile of a feature matches a specified curve or shape.
- 🔄 Orientation type characteristics like parallelism and perpendicularity ensure the correct angular relationship between features and datums.
- 🔄 Run-out type characteristics like circular run-out and total run-out control the form of a surface or the orientation of features in relation to a datum.
- 🔢 MMC (Maximum Material Condition) and LMC (Least Material Condition) are conditions that define the maximum and minimum material states within dimensional tolerances.
Q & A
What does GD&T stand for and what is its purpose?
-GD&T stands for Geometric Dimensioning and Tolerancing. It is a system of symbols, rules, and definitions used to define the size, shape, form, orientation, and location of features on a part. It is used to define the allowable deviation of feature geometry to ensure an object functions correctly.
What are the three types of tolerances mentioned in the script?
-The three types of tolerances mentioned are limit dimension, unilateral, and bilateral. Limit dimensions show the largest and smallest values allowed, unilateral tolerance allows variation in one direction, and bilateral tolerance allows variation in both positive and negative directions.
What is a datum in the context of GD&T?
-A datum in GD&T is a theoretical exact feature from which dimensional measurement is done. It is generally chosen as an edge or feature that has the greatest influence in a specific measurement.
Can you explain the difference between primary, secondary, and tertiary datums?
-Primary datum controls three degrees of freedom, restricting rotation around x and y axes and movement along the z axis. Secondary datum controls two additional degrees of freedom, restricting rotation around the z axis and movement along the y axis. Tertiary datum controls one additional degree of freedom, restricting movement along the x axis.
What is straightness in GD&T and how is it measured?
-Straightness is a form type characteristic that controls the straightness of a feature in relation to its own perfect form. It is measured using a dial indicator by moving its plunger on the surface of the feature in a straight line, and the deflection of the dial gives the actual straightness value.
How is flatness different from straightness in GD&T?
-Flatness, like straightness, is a form type characteristic, but it controls the flatness of a surface in relation to its own perfect form. It is measured using a straight edge and a dial indicator, with the deflection of the dial indicating the actual flatness value.
What is the purpose of the MMC condition in GD&T?
-MMC, or Maximum Material Condition, describes the condition of a feature where the maximum amount of material exists within its dimensional tolerance. It is used to ensure proper fit and function of mating parts.
What does LMC stand for and what does it represent?
-LMC stands for Least Material Condition. It represents the condition of a feature where the least amount of material exists within its dimensional tolerance, which is useful for ensuring maximum clearance or minimum interference.
What is the significance of bonus tolerance in GD&T?
-Bonus tolerance is an additional tolerance for a geometric control applied to a feature of size with MMC or LMC. It allows for more flexibility in the manufacturing process while still meeting the specified tolerances.
How is the virtual condition different from the MMC and LMC conditions?
-Virtual condition is a theoretical extreme boundary condition of a feature generated by the collective effects of MMC size limit, LMC, and any applicable geometric tolerances. It represents the boundary within which any portion of a feature may possibly fall.
What is the purpose of the projected tolerance zone in GD&T?
-The projected tolerance zone is a modifier used for threaded or blind holes to ensure proper fitment of mating parts. It extends the tolerance zone beyond the surface of the part to the functional length of the mating part, controlling the perpendicularity of the hole to the extent of the projection.
Outlines
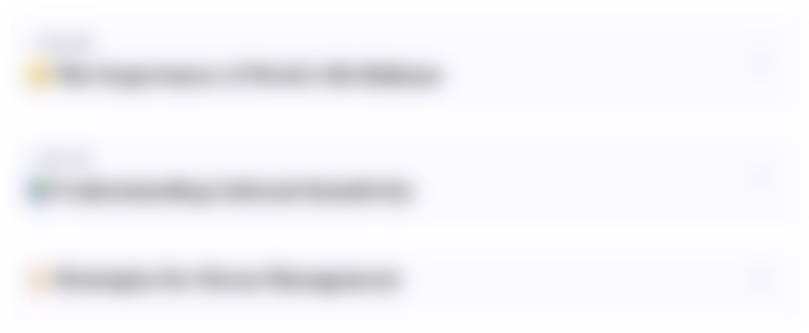
此内容仅限付费用户访问。 请升级后访问。
立即升级Mindmap
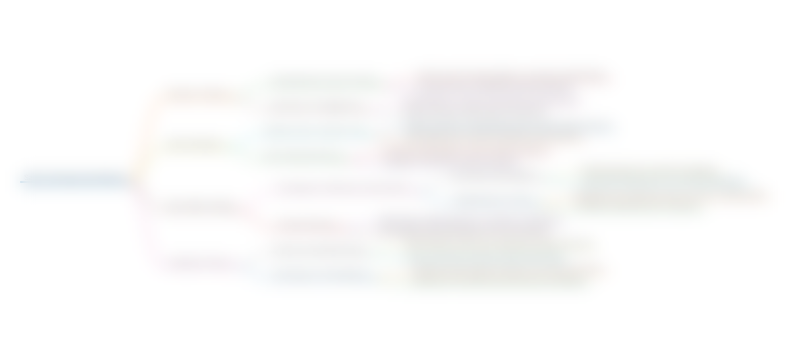
此内容仅限付费用户访问。 请升级后访问。
立即升级Keywords
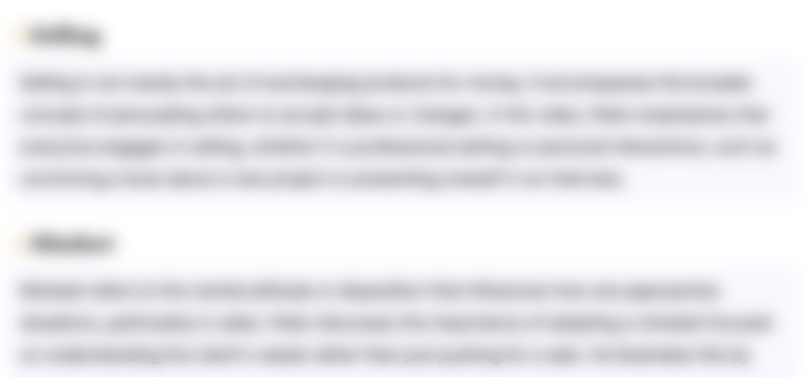
此内容仅限付费用户访问。 请升级后访问。
立即升级Highlights
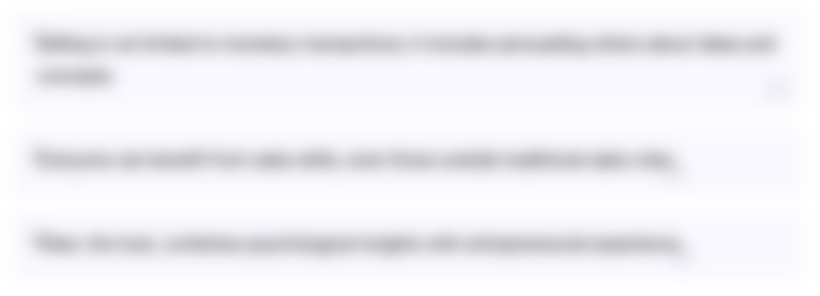
此内容仅限付费用户访问。 请升级后访问。
立即升级Transcripts
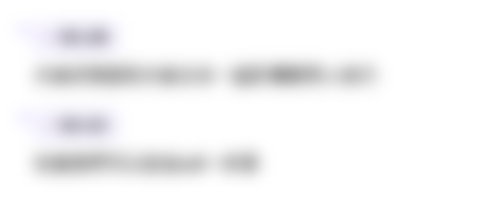
此内容仅限付费用户访问。 请升级后访问。
立即升级浏览更多相关视频
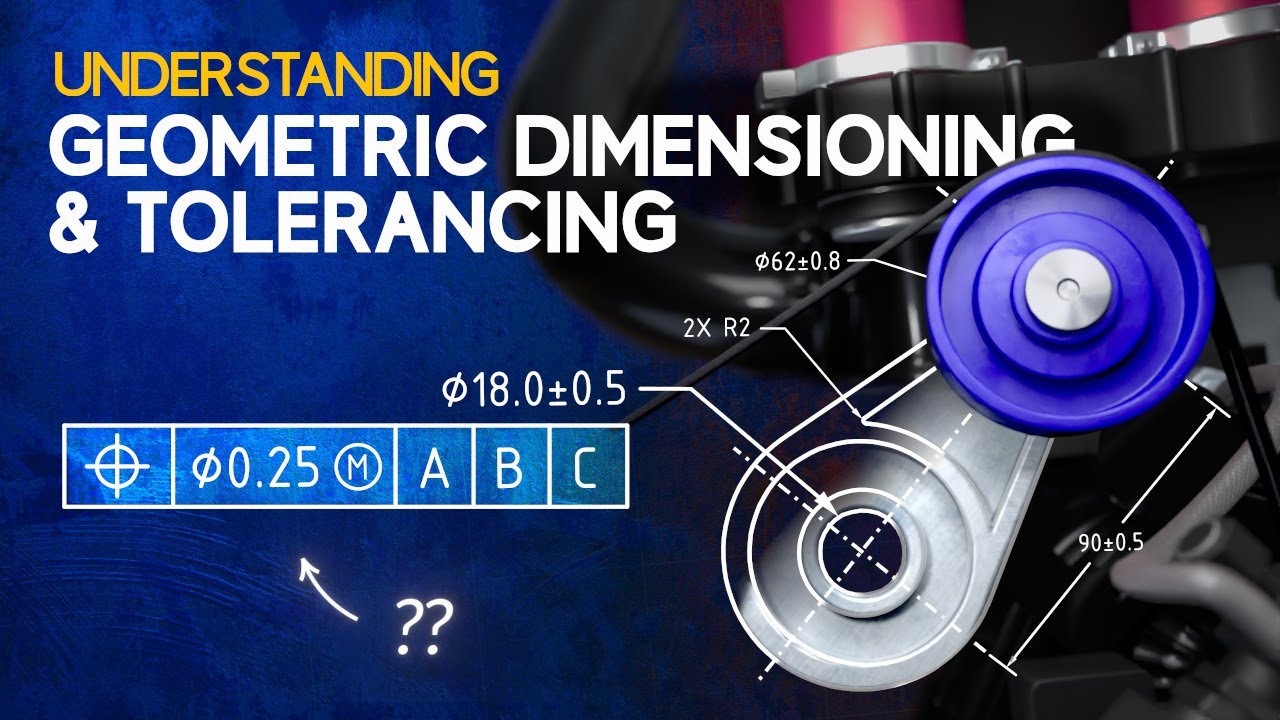
Understanding GD&T
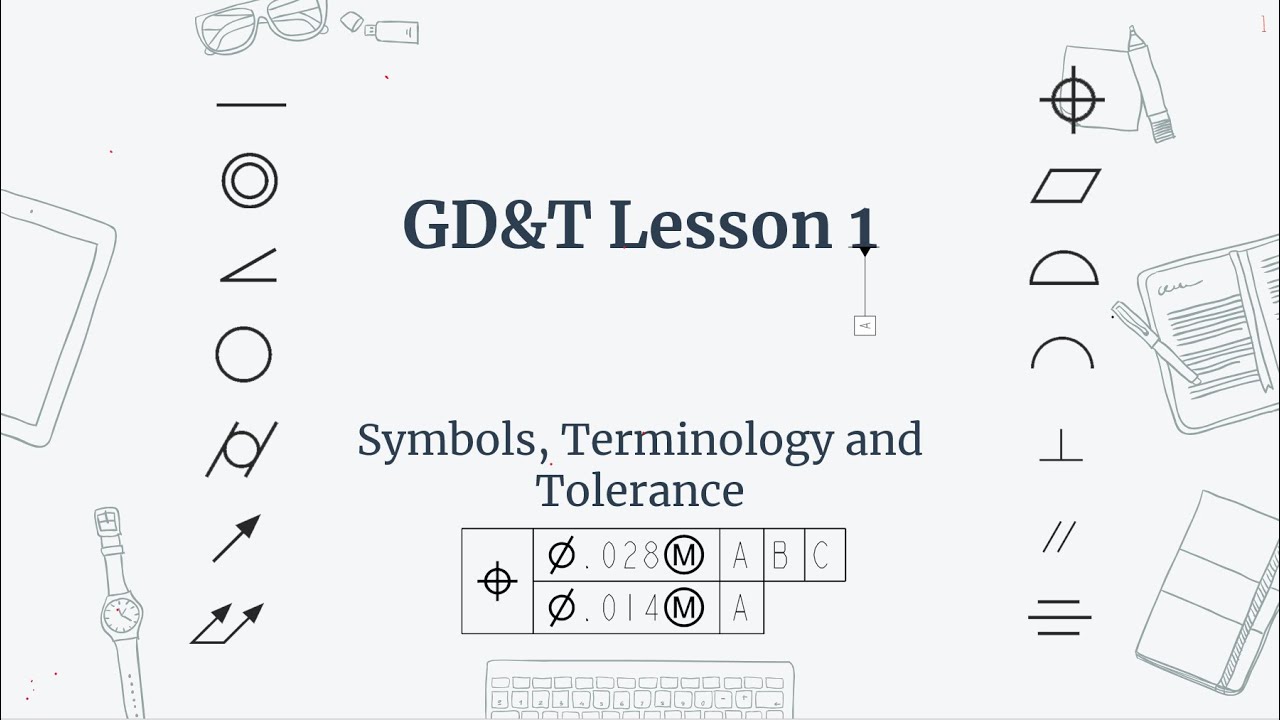
GD&T Lesson 1: Symbols, Terminology and Tolerance.

Understanding Engineering Drawings
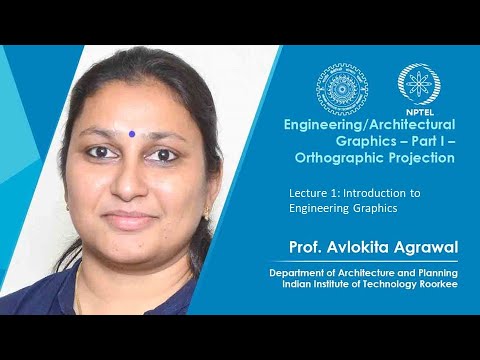
Lecture 1: Introduction to Engineering Graphics

Orthographic Projection_An Introduction_Engineering Drawing_Engineering Graphics_English
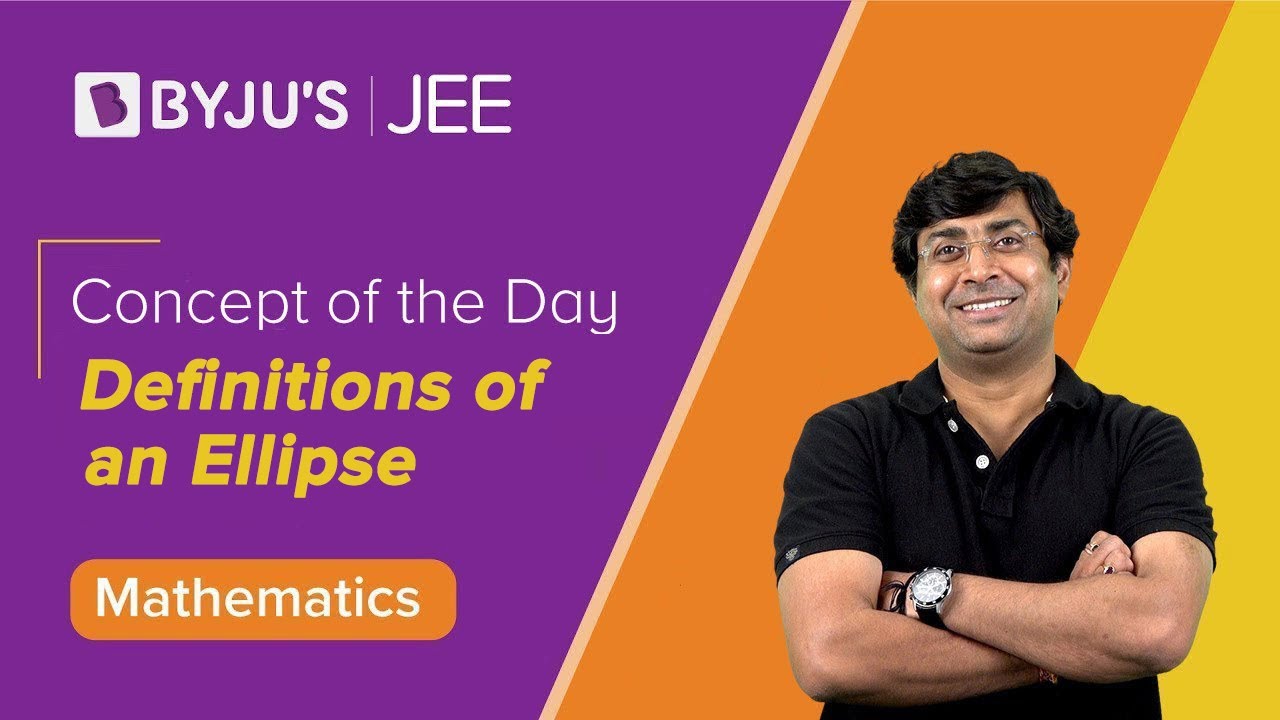
Definitions of an Ellipse | MATHS | JEE | Concept of the Day | GB Sir
5.0 / 5 (0 votes)