Slip ring Induction Motor, How it works?
Summary
TLDRThe video script delves into the workings of induction motors, highlighting the difference between squirrel cage and slip ring rotor designs. It explains how squirrel cage motors, with their low starting torque, are unsuitable for applications requiring high initial force, such as in hoists. In contrast, slip ring induction motors are favored for their ability to generate high starting torque, achieved by reducing the phase difference between induced EMF and current through external resistance. This makes them ideal for heavy-duty industrial applications like elevators and cranes.
Takeaways
- ๐ Induction motors are a staple in the industrial world for many decades due to their reliability and performance.
- ๐ง There are two types of rotors in induction motors: slip ring rotors, used in lifting hoists for their high starting torque, and squirrel cage rotors, which are simpler and used in most other applications.
- ๐ซ Squirrel cage induction motors have a low starting torque, which can be problematic for certain applications that require a high initial force.
- ๐ The working of an induction motor involves a rotating magnetic field (RMF) produced by the stator winding, which induces an electromotive force (EMF) in the rotor bars, leading to motion.
- ๐ง Faraday's law of electromagnetic induction and Lorentz's law are fundamental to understanding how induction motors generate motion.
- ๐ The concept of inductance is crucial in induction motors, as it influences the phase difference between the applied voltage and the current, affecting motor performance.
- ๐ In a simple circuit with a resistor and an inductor, the phase difference between the applied voltage and the current is due to inductive reactance, which increases with frequency.
- ๐ The rotor's resistance and inductive reactance cause a phase-lag phenomenon, which affects the torque produced by the motor.
- ๐ Induction motors produce maximum torque when the current induced in the rotor is near the maximum magnetic flux, aligning with the 'maximum torque condition'.
- ๐ At startup, the high frequency of the induced EMF in the rotor due to zero speed results in a large phase difference, leading to the low starting torque of normal induction motors.
- ๐ Slip ring induction motors overcome the low starting torque issue by using external resistance to reduce the phase difference between the induced EMF and the current, allowing for high torque even at startup.
- ๐ The use of external resistance in slip ring motors at startup helps the current induced to approach the maximum torque condition, resulting in higher starting torque compared to squirrel cage motors.
- ๐๏ธ Slip ring induction motors are particularly important in applications requiring high starting torque, such as elevators, cranes, hoists, and industrial machinery like printing presses.
Q & A
What is the main difference between squirrel cage and slip ring rotors in induction motors?
-The main difference lies in the rotor construction. Squirrel cage rotors are simpler, with bars short-circuited by end rings, while slip ring rotors use three windings and can incorporate external resistance to reduce phase difference and produce high starting torque.
Why do induction motors with squirrel cage rotors produce low starting torque?
-At startup, the rotor speed is zero, leading to a high rate of magnetic field cutting through the rotor, which results in a high frequency of induced EMF and a large phase difference, causing low starting torque.
How does the slip ring induction motor overcome the issue of low starting torque?
-The slip ring induction motor uses external resistance connected to the rotor windings via slip rings. By increasing the resistance at startup, it reduces the phase difference, allowing the current induced to approach the maximum torque condition.
What is the significance of inductance in the operation of an induction motor?
-Inductance, along with resistance in the rotor, causes a phase difference between the applied voltage and the current. This phase difference affects the torque produced by the motor, with maximum torque occurring when the induced current aligns with the maximum magnetic flux.
How does the slip ring induction motor adjust the phase difference during startup?
-By increasing the external resistance connected to the rotor windings at startup, the slip ring induction motor reduces the phase difference between the induced EMF and the current, enabling it to produce high torque from the beginning.
What is the role of Faraday's law of electromagnetic induction in the operation of an induction motor?
-Faraday's law states that an electromotive force is induced in a conductor when it cuts through a magnetic field. In an induction motor, this law is responsible for inducing EMF in the rotor bars, which in turn generates the current that causes the rotor to turn.
What is Lorentz's law, and how does it relate to the operation of an induction motor?
-Lorentz's law describes the force experienced by a current-carrying conductor placed in a magnetic field. In an induction motor, this force acts on the current in the rotor bars, causing the rotor to rotate.
Why is the slip ring induction motor preferred for applications requiring high starting torque?
-Slip ring induction motors are preferred because they can produce high starting torque by reducing the phase difference between the induced EMF and the current through the use of external resistance, making them suitable for applications like elevators, cranes, and hoists.
What are some advantages of slip ring induction motors besides high starting torque?
-Besides high starting torque, slip ring induction motors offer the ability to control speed and torque more precisely through external resistance adjustments, making them versatile for various industrial applications.
What are the disadvantages of slip ring induction motors compared to squirrel cage motors?
-While the script does not explicitly mention the disadvantages, slip ring induction motors are generally more complex, more expensive to manufacture and maintain due to the presence of slip rings and brushes, and may have lower efficiency due to additional resistance.
How does the concept of maximum torque condition relate to the performance of an induction motor?
-The maximum torque condition is when the induced current in the rotor is near the maximum magnetic flux. An induction motor produces the most torque under this condition, which is crucial for understanding motor performance and optimizing its operation.
Outlines
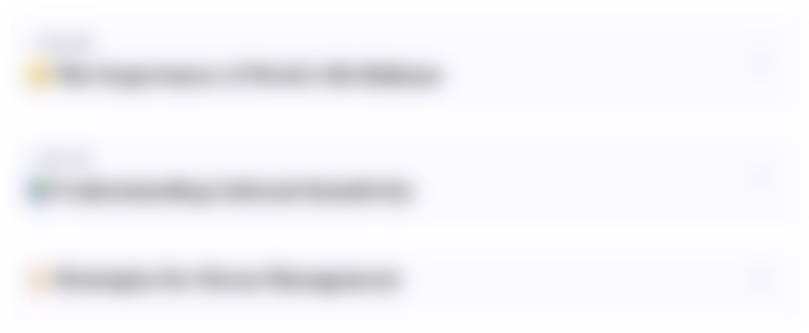
This section is available to paid users only. Please upgrade to access this part.
Upgrade NowMindmap
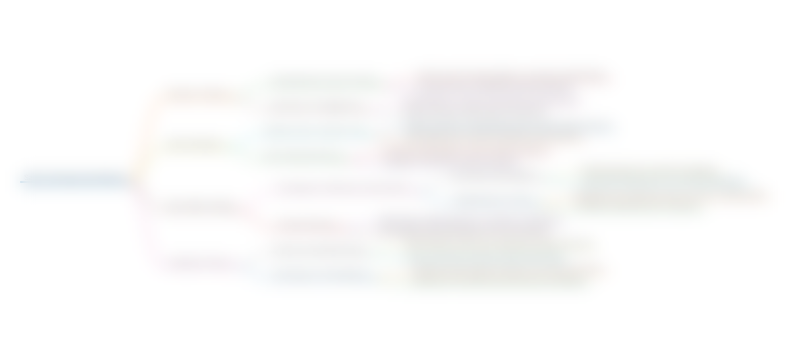
This section is available to paid users only. Please upgrade to access this part.
Upgrade NowKeywords
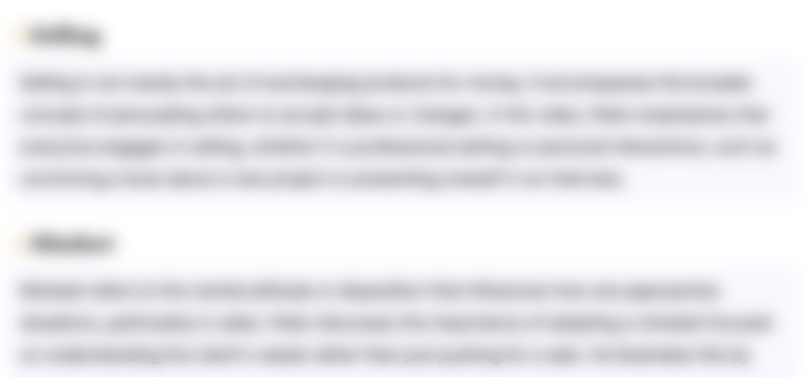
This section is available to paid users only. Please upgrade to access this part.
Upgrade NowHighlights
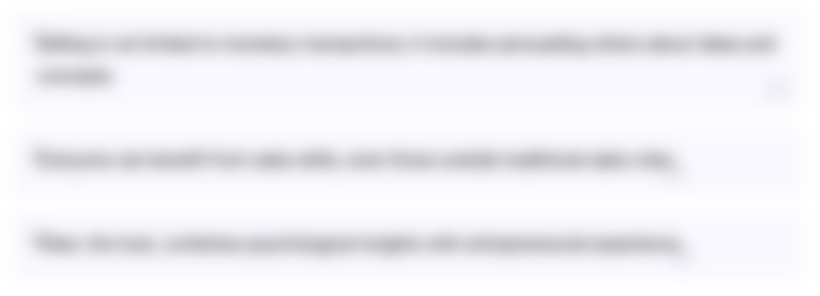
This section is available to paid users only. Please upgrade to access this part.
Upgrade NowTranscripts
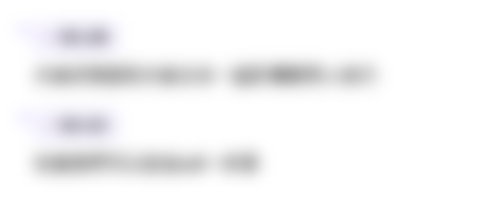
This section is available to paid users only. Please upgrade to access this part.
Upgrade NowBrowse More Related Video

Squirrel Cage Rotor and Slip Ring Rotor - Squirrel Cage vs Wound Rotor
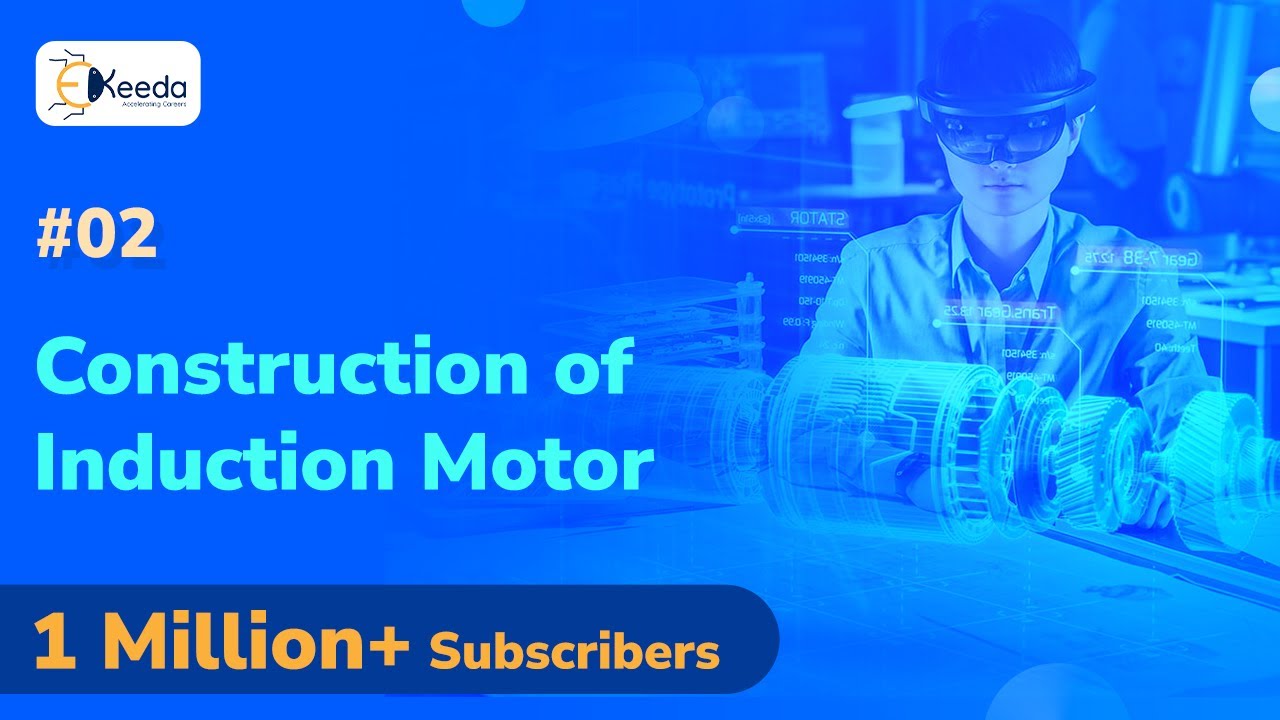
Construction of Three Phase Induction Motor - Three Phase Induction Motor - Electrical Machines 3

How alternating current motors work?
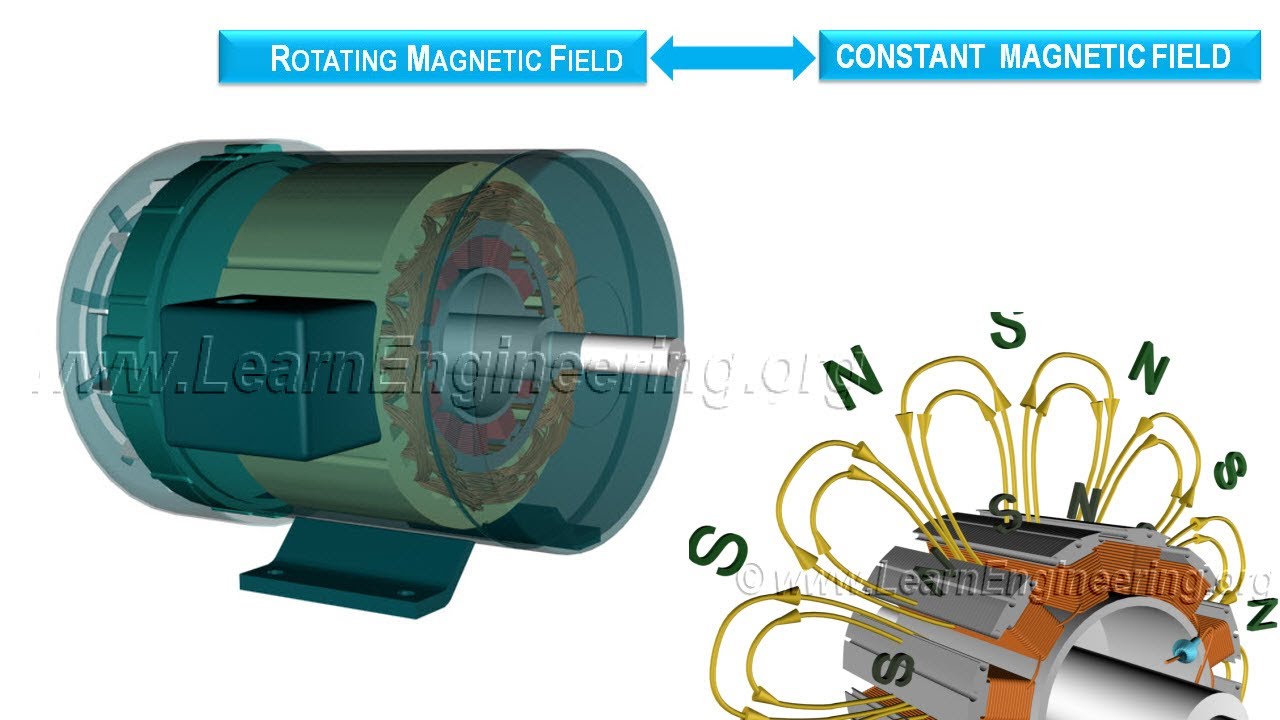
Working of Synchronous Motor
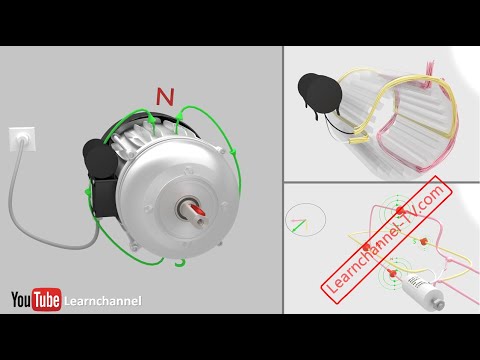
Single Phase Induction Motor (Capacitor Induction Motor or AC Motor) explained
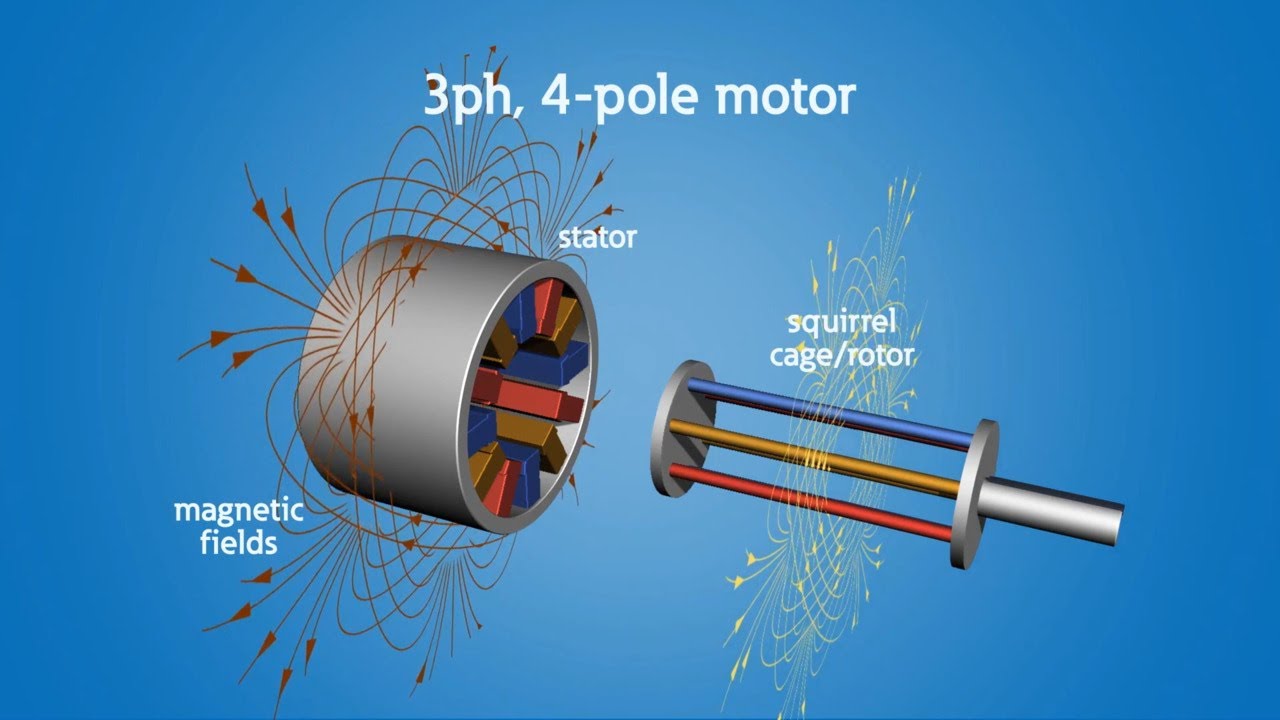
Motors 101
5.0 / 5 (0 votes)