Sistema de costos por procesos
Summary
TLDRThe video script discusses the process costing system, used in manufacturing to accumulate production costs by department. It highlights objectives like determining total manufacturing costs and calculating unit costs. The script also covers advantages like standardized production and ecological processing, and disadvantages such as difficulty in identifying direct cost elements per unit. Industries like chemical and pharmaceutical are mentioned as potential users of this system.
Takeaways
- 📘 The process costing system is a method for accumulating production costs by department or cost center.
- 🏭 A department is the main functional division in a factory where manufacturing processes are carried out.
- 🔢 Costs for raw materials, direct labor, and manufacturing overhead are accumulated in the product cost accounts.
- 🎯 The primary objective of direct labor costs is to work out the total cost to determine the income.
- 🔁 The production in a process costing system is continuous and uniform, with the unit cost being an average result.
- 🌐 Advantages of continuous production include standardized costs, more ecological processing, and streamlined administration.
- 🚫 Disadvantages include the inability to identify direct cost elements in each finished unit, rigid production conditions, and the need to quantify production.
- 🏷️ The importance of the process costing system lies in determining how production costs incurred during the period will be assigned to each department.
- 🔑 It is used in industries that transform raw materials or materials, such as chemical and pharmaceutical companies.
- 📊 The system must be compatible with the nature of the business and understand the stages of the production process.
- 🔄 The cost flow begins with costs and factors entering the first process and is transferred through to finished goods and then to cost of sales.
Q & A
What is the process costing system?
-The process costing system is a method of accumulating production costs by department or cost center. It involves tracking costs associated with raw materials, direct labor, and manufacturing overhead as they move through various stages of production.
What are the main objectives of using process costing in manufacturing?
-The main objectives of process costing include determining total manufacturing costs, identifying direct labor costs, and ultimately calculating the total cost of production to determine profit margins.
How does the production process in a continuous system differ from other types of production?
-In a continuous production system, the production is uniform and ongoing, which allows for standardized costs and more ecological processing. This contrasts with batch or job production methods where each unit is produced separately.
What are the advantages of continuous production in terms of cost management?
-Advantages of continuous production include standardized costs, which can lead to more predictable and manageable expenses, and more ecological processing due to the uniform nature of the production process.
What are the disadvantages of using process costing in a manufacturing setting?
-Disadvantages include the difficulty in identifying direct cost elements in each finished unit and the rigidity of production conditions, which may require precise quantification of production and processes.
Why is it important to determine how costs are assigned in the process costing system?
-Determining how costs are assigned is crucial because it affects how production costs incurred during a period are allocated to each department, which in turn impacts financial reporting and decision-making.
In which types of industries is the process costing system commonly used?
-The process costing system is commonly used in industries that involve the transformation of raw materials or materials, such as chemical and pharmaceutical industries.
What is the nature of the process costing system and how does it need to be compatible with the business?
-The process costing system must be compatible with the nature of the business and its production stages. It functions effectively when there are well-defined stages in the production process, facilitating the tracking of costs as they move through each stage.
How does the cost flow in the process costing system?
-The cost flow in the process costing system begins when costs and factors enter the first process, are transferred from process one to process two, and eventually move to the finished goods warehouse and then to the cost of sales.
What are the key characteristics of a production process that would benefit from using the process costing system?
-Key characteristics include continuous and uniform production, which allows for the averaging of unit costs and the tracking of costs through various stages of production.
How does the process costing system help in managing administrative tasks in manufacturing?
-The process costing system aids in managing administrative tasks by providing a clear and systematic way to track and allocate costs, which can streamline financial management and decision-making processes in manufacturing.
Outlines
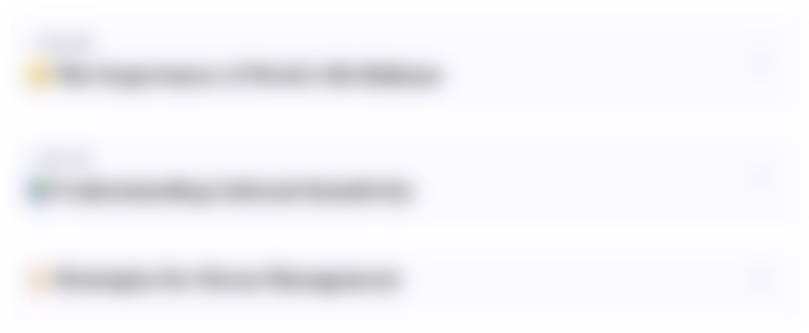
This section is available to paid users only. Please upgrade to access this part.
Upgrade NowMindmap
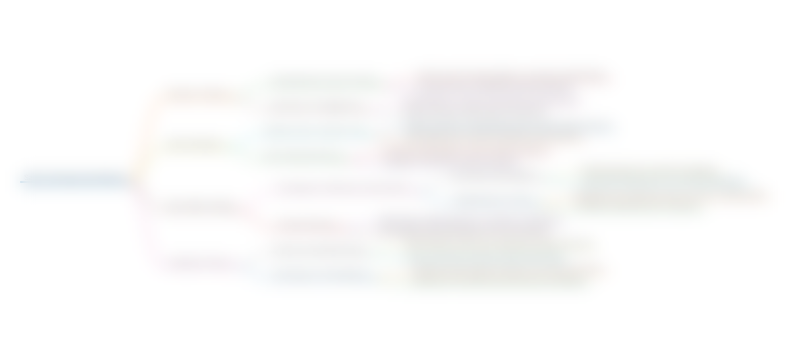
This section is available to paid users only. Please upgrade to access this part.
Upgrade NowKeywords
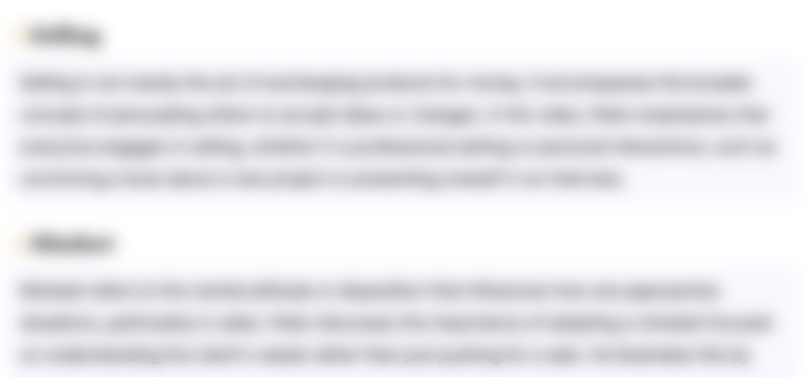
This section is available to paid users only. Please upgrade to access this part.
Upgrade NowHighlights
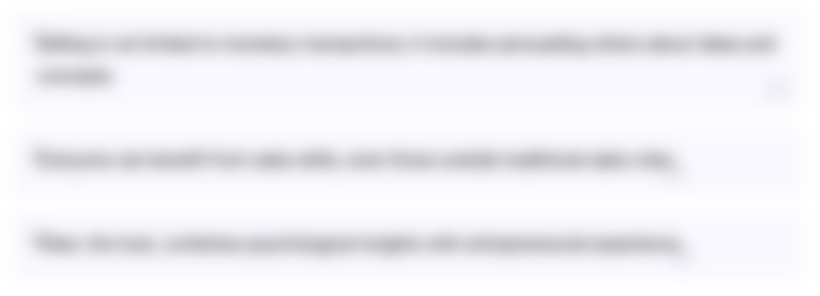
This section is available to paid users only. Please upgrade to access this part.
Upgrade NowTranscripts
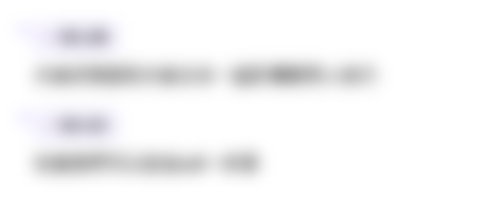
This section is available to paid users only. Please upgrade to access this part.
Upgrade NowBrowse More Related Video
5.0 / 5 (0 votes)