Product Costing
Summary
TLDRBob's bakery has expanded its product range, now including cakes alongside cookies. To manage costs effectively, he implements a product costing system that differentiates between direct and indirect costs. Direct costs, like flour for cookies, are easily traced, while indirect costs, such as electricity, are allocated using the plant-wide method based on machine hours. For cookies, a process costing system is used due to their mass production, whereas cakes, being unique, require individual unit costing. This system enhances Bob's decision-making for pricing and product mix, ultimately boosting the bakery's financial performance.
Takeaways
- 🍪 Bob's Bakery has a perfected cookie recipe and has expanded into cakes, necessitating a product costing system.
- 📊 Bob understands the difference between direct and indirect costs, with direct costs being easily traceable to products and indirect costs being overheads.
- ⏱️ Indirect costs like electricity bills can pose challenges due to their infrequent and delayed nature, affecting timely decision-making.
- 📈 Bob uses a conventional product costing system involving cost accumulation and cost assignment to manage his bakery's finances.
- 🔄 Cost accumulation records and aggregates costs into cost pools, which represent different types of costs.
- 🔄 Cost assignment involves allocating costs to cost objects, such as products, using methods like the plant-wide method.
- 🏭 The plant-wide method allows Bob to aggregate all indirect costs into a single cost pool and allocate them based on a chosen cost driver, like machine hours.
- 🍰 Bob uses a process costing system for cookies, which are identical and produced in large quantities, focusing on the production process rather than individual units.
- 🎂 For unique products like birthday cakes, Bob uses a product costing system where each cake is costed separately due to the different processes involved.
- 📊 Implementing a product costing system helps Bob understand the costs of making different products, aiding in better financial decisions for the bakery.
Q & A
What is Bob's current situation with his bakery?
-Bob has been running his bakery for a few months and has perfected his signature cookie recipe. He has also diversified into cakes but is unsure how to cost both products.
What does Bob understand about direct and indirect costs?
-Bob understands that direct costs can be traced directly to the cost object, like flour in cookie production, while indirect costs, also known as overheads, do not have a direct relationship to a cost object and are more difficult to assign.
Why is it challenging for Bob to assign indirect costs to his products?
-Assigning indirect costs is challenging because they do not have a direct relationship with the products and the actual costs, like electricity bills, are not known at the time of production.
What is the purpose of a product costing system for Bob's bakery?
-A product costing system helps Bob understand the costs incurred in making different products, which will assist him in making better decisions to increase the financial performance of the bakery.
What are the two basic steps involved in a conventional product costing system?
-The two basic steps are cost accumulation, which is recording and aggregating costs into cost pools, and cost assignment, which is assigning costs to cost objects like products.
What method does Bob decide to use for allocating indirect costs?
-Bob decides to use the plant-wide method for allocating indirect costs, which involves estimating all indirect costs for the year and aggregating them into a single cost pool.
How does Bob select the cost driver for allocating overheads?
-Bob selects the number of machine hours used by the products as the cost driver, as it best represents the cause and effect relationship between the use of overheads and the products made.
What formula does Bob use to calculate the overhead allocation rate?
-Bob calculates the overhead allocation rate using the formula: total budgeted overhead divided by total budgeted driver (machine hours).
How does Bob handle product costing for cookies and birthday cakes differently?
-For cookies, Bob uses a process costing system where the entire batch is costed, not individual cookies. For birthday cakes, which are unique and require different processes, costs are accumulated at the unit level and each cake is costed separately.
What is the significance of using a process costing system for cookie production?
-Using a process costing system for cookie production is significant because it allows Bob to focus on the production process rather than individual products, as cookies are made in large, identical batches.
How does the product costing system help Bob make better decisions for his bakery?
-The product costing system helps Bob by providing a clearer understanding of the costs involved in making different products, which can inform decisions on setting selling prices and determining the right product mix.
Outlines
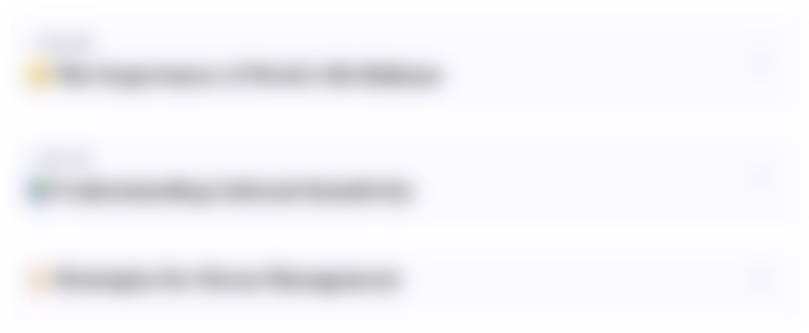
This section is available to paid users only. Please upgrade to access this part.
Upgrade NowMindmap
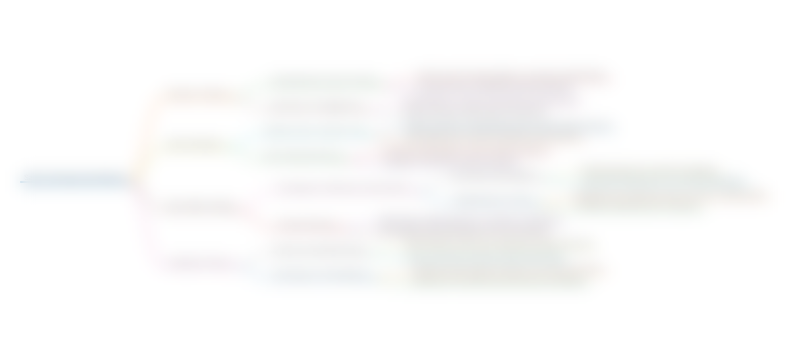
This section is available to paid users only. Please upgrade to access this part.
Upgrade NowKeywords
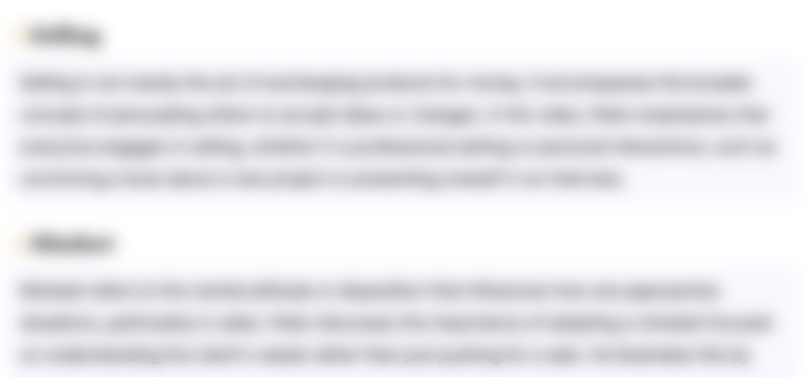
This section is available to paid users only. Please upgrade to access this part.
Upgrade NowHighlights
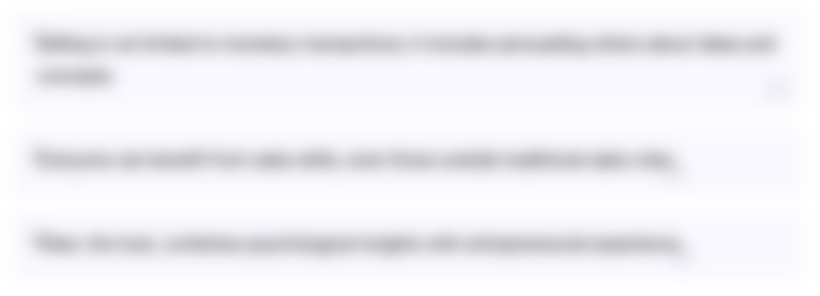
This section is available to paid users only. Please upgrade to access this part.
Upgrade NowTranscripts
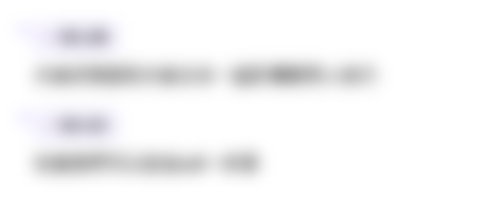
This section is available to paid users only. Please upgrade to access this part.
Upgrade NowBrowse More Related Video

Company Profile Bila Bakery

Bisnis & Wirausaha - Kisah Sukses Kios Buket

How Filipino Breads Are Made Fresh Every Morning in this Traditional Bakery in Quezon

MODAL RUMAHAN UNTUNG BELASAN JUTA SETIAP MINGGU !!! | KISAH INSPIRATIF UMKM

Cerita Mint Patisserie, dari Hobi Baking Jadi Bisnis Menguntungkan

Ferdi's Bakery | Pengusaha Muda Papua | Manokwari
5.0 / 5 (0 votes)