04 - GuardLink Components
Summary
TLDRThe video script discusses the Guardmaster Safety Relay system, highlighting its capability to support up to 64 devices with a master module and two trunk lines. It covers local controls, such as device reset and special safe torque off applications, and the system's compatibility with electromechanical or solid-state devices. The script also explains the use of optical bus for Ethernet module connectivity, the importance of voltage drop calculations for long runs, and the integration with Studio 5000 for easy troubleshooting. The Guardmaster system is designed for compact logic control platforms without a safety PLC, emphasizing its diagnostic and remote reset features.
Takeaways
- π§ The master module supports 2 trunk lines and up to 64 devices, with electromechanical or solid-state safety relay options.
- βοΈ Local controls on the module allow up to 20 different functions, including single input with optional time delay and device reset capabilities.
- π‘ Connectivity is facilitated by an optical bus, enabling communication between stacked safety relays and the Ethernet module.
- π‘οΈ The device supports single-wire safety, allowing cascading of multiple safety relays for larger systems.
- π‘ The terminal layout is consistent with the GS family of safety relays, featuring indicator status lights and updatable firmware via Ethernet module.
- π Different versions of optical links are supported, with backward compatibility and passive taps for long runs or voltage drop conditions.
- π οΈ Rockwell offers a voltage drop calculator to help set up and evaluate guard link systems, ensuring safety devices receive appropriate voltage.
- π The Ethernet module provides advanced diagnostics and communication for up to six devices through the optical bus, with newer devices recommended to be placed closest to the module.
- π The system integrates with Studio 5000 for easy configuration and diagnostics, supporting compact and extended compact logics platforms without a safety PLC.
- π§© The system setup includes part numbers for various taps, passive power taps, shorting plug terminators, mounting brackets, safety relays, and Ethernet modules.
Q & A
What is the function of the master module mentioned in the script?
-The master module manages up to 64 devices and supports two trunk lines, enabling connectivity and control for various safety devices.
What types of devices does the master module support?
-The master module supports both electromechanical and solid-state devices, providing versatile options for different safety applications.
How many functions can be configured on the master module, and what is one example?
-Up to 20 different functions can be configured on the master module. An example is the ability to perform a device reset by cycling power to reset devices in a fault condition.
What connectivity feature is highlighted for the master module?
-The master module connects to the Ethernet module using an optical bus, allowing communication and diagnostic data transfer between multiple devices.
What compatibility is mentioned regarding the optical link versions?
-The system is compatible with both Optical Link 2.0 and 3.0 versions, with backward compatibility ensuring integration with older devices.
What is the purpose of passive power taps in the system?
-Passive power taps are used to address voltage drop conditions over long runs, injecting power back into the system to maintain voltage levels.
What are the key features of the taps mentioned in the transcript?
-The taps support guard locking devices, have a slim design for easy mounting, and are available in various configurations for different sensor inputs and safety applications.
How does the system ensure safety when a device or tap fails?
-The system uses a guard link circuit that sends pulse signals to the taps. If a tap drops offline or a device fails, the system detects this and sends the data back, ensuring safety integrity.
What recommendations are given for placing devices with different optical link versions?
-Newer devices using Optical Link 3.0 should be placed closer to the Ethernet module, while older or slower communication devices should be placed further away.
What software integration is mentioned for configuring the system?
-The system integrates with Studio 5000 version 20 and newer, allowing for easy setup and configuration through a single software platform, with automatic tag population and system diagnostics.
Outlines
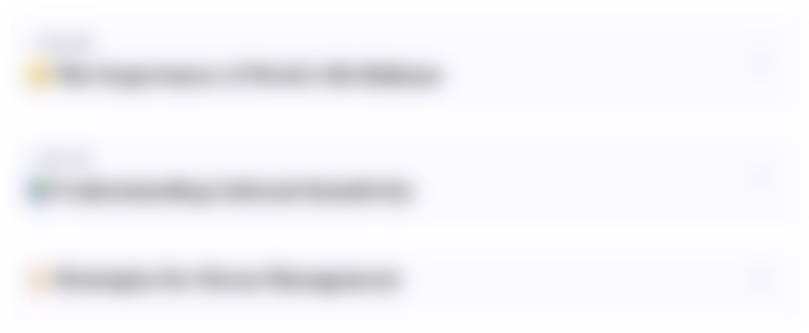
This section is available to paid users only. Please upgrade to access this part.
Upgrade NowMindmap
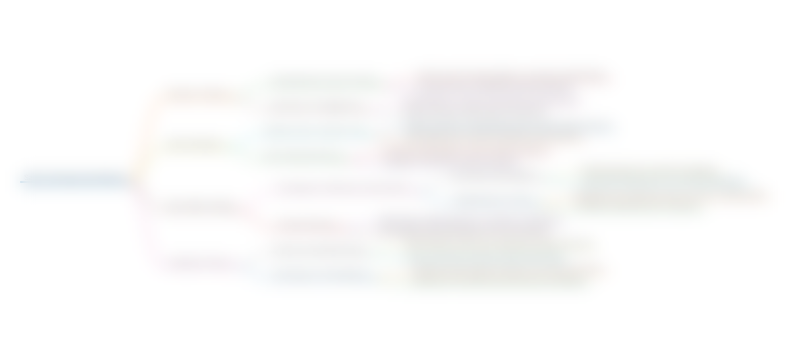
This section is available to paid users only. Please upgrade to access this part.
Upgrade NowKeywords
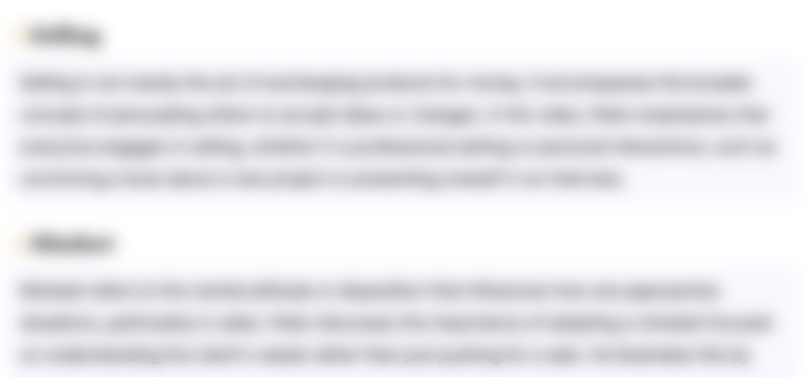
This section is available to paid users only. Please upgrade to access this part.
Upgrade NowHighlights
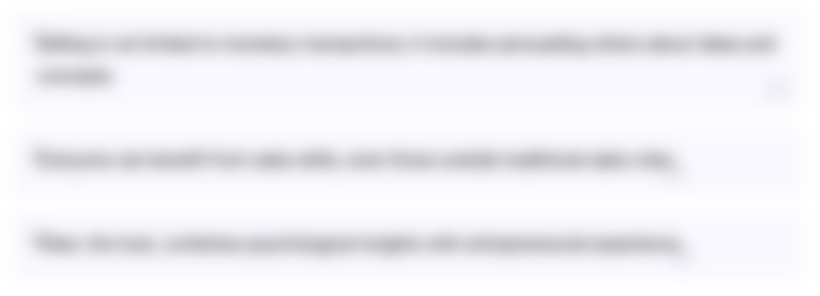
This section is available to paid users only. Please upgrade to access this part.
Upgrade NowTranscripts
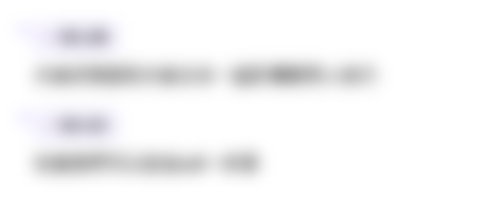
This section is available to paid users only. Please upgrade to access this part.
Upgrade NowBrowse More Related Video
5.0 / 5 (0 votes)