Inventory management
Summary
TLDRThis script explores the importance of inventory management across various industries, emphasizing the need for balance between having sufficient stock and minimizing costs. It highlights the role of trust among departments like sourcing, manufacturing, and warehousing in achieving inventory management excellence, and underscores the impact of inventory on financial statements.
Takeaways
- 📦 **Inventory Management Definition**: It's about having the right inventory, at the right time, in the right place, with a focus on recordkeeping and the flow of goods.
- 🔄 **Involvement Across Departments**: All departments, including sourcing, manufacturing, warehousing, marketing, sales, finance, accounting, and legal, have a stake in inventory management.
- 🛒 **Bulk Buying Strategy**: The sourcing department often prefers to buy in bulk to get volume discounts, affecting inventory levels.
- 🏭 **Efficiency in Manufacturing**: Manufacturing prefers long production runs for efficiency and cost-effectiveness, which can lead to higher inventory.
- 📏 **Warehouse Space Constraints**: Warehousing is concerned about space and the physical presence of inventory, highlighting the challenge of storage capacity.
- 💰 **Financial Impact**: Inventory management is crucial for cash flow management and avoiding obsolescence, which can lead to financial losses.
- 📋 **Legal Considerations**: Contracts may specify delivery requirements and penalties, emphasizing the importance of inventory availability for legal compliance.
- 🗳️ **Inventory Decision-Making**: There's often a conflict between departments favoring more inventory for various reasons and those advocating for less to save on costs.
- 🔢 **Financial Dominance**: The finance department's preference for lower inventory often prevails due to its significant impact on financial decisions and outcomes.
- 💼 **Financial Statements Connection**: Inventory appears on the balance sheet as an asset and affects the income statement and cash flow statement, influencing company financials.
- 🔗 **Trust as the Foundation**: Trust among departments is essential for inventory management excellence, allowing for optimized inventory levels and reduced costs.
- 🛠️ **Investment in Systems and Processes**: To achieve excellence in inventory management, companies must invest in systems, processes, data, and human actions, which typically yield significant returns.
- 🌐 **Learning Through Observation**: Gaining practical insights by observing inventory management in action at companies with complex supply chains can provide valuable learning experiences.
Q & A
What is the fundamental concept of inventory management?
-The fundamental concept of inventory management is to have the right inventory, at the right time, in the right place, which includes both recordkeeping and the flow of goods from suppliers to customers.
Why is inventory management important for different departments within a company?
-Inventory management is important for different departments because it impacts sourcing, manufacturing, warehousing, marketing, sales, finance, accounting, and legal aspects of a company, each with its own perspective and stakes in maintaining optimal inventory levels.
What does the sourcing department typically propose regarding inventory?
-The sourcing department typically proposes buying in bulk from suppliers to get maximum volume discounts, which can affect inventory levels.
What is the manufacturing department's view on production runs?
-The manufacturing department prefers to make big production runs of the same product before changing over to produce another product for maximum efficiency and lowest cost per unit.
Why might warehousing be resistant to holding more inventory?
-Warehousing might be resistant to holding more inventory due to space limitations, as warehouses can fill up quickly, similar to storage space in a house.
How does marketing and sales view inventory in relation to customer orders?
-Marketing and sales view inventory as essential to have plenty available when a customer order comes in to meet demand and ensure customer satisfaction.
What are the financial and accounting department's main priorities in inventory management?
-The financial and accounting department's main priorities in inventory management are to manage cash flow and avoid inventory obsolescence, which can impact the company's financial health.
Why would the legal department have an opinion on inventory management?
-The legal department may have an opinion on inventory management due to contractual obligations, such as the need to deliver critical spare parts within a specified time frame to avoid financial penalties.
How does inventory show up in a company's financial statements?
-Inventory shows up as one of the assets on a company's balance sheet. It affects the balance between assets and liabilities, and can influence cash flow and profitability.
What is the role of trust in achieving inventory management excellence?
-Trust is the basis for inventory management excellence as it connects all departments and ensures that commitments are delivered upon, allowing for optimized inventory levels and efficient operations.
Why is it important for a company to invest in systems and processes for inventory management?
-Investing in systems and processes for inventory management is important because it helps to build trust, reduce errors, optimize operations, and ultimately leads to significant payoffs in terms of cost savings and operational efficiency.
Outlines
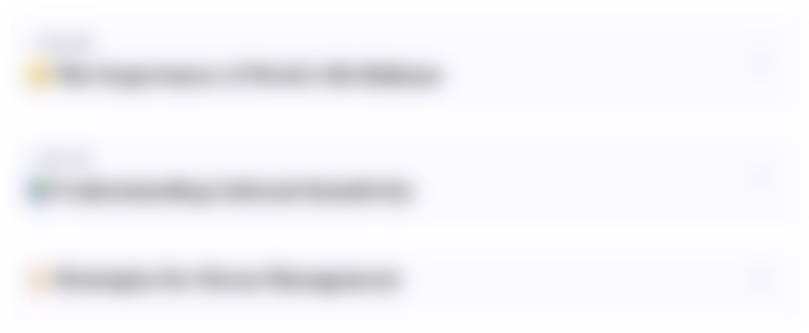
This section is available to paid users only. Please upgrade to access this part.
Upgrade NowMindmap
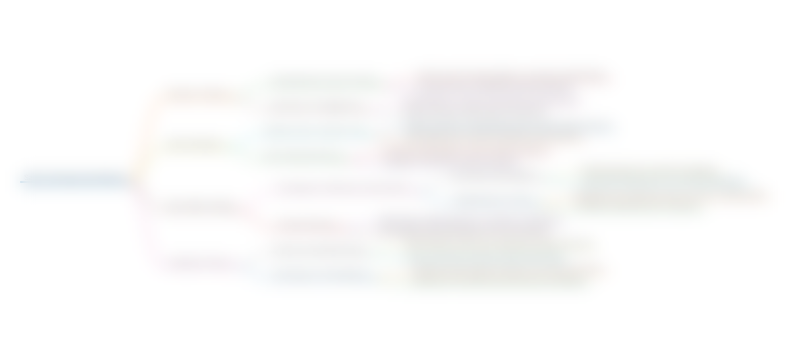
This section is available to paid users only. Please upgrade to access this part.
Upgrade NowKeywords
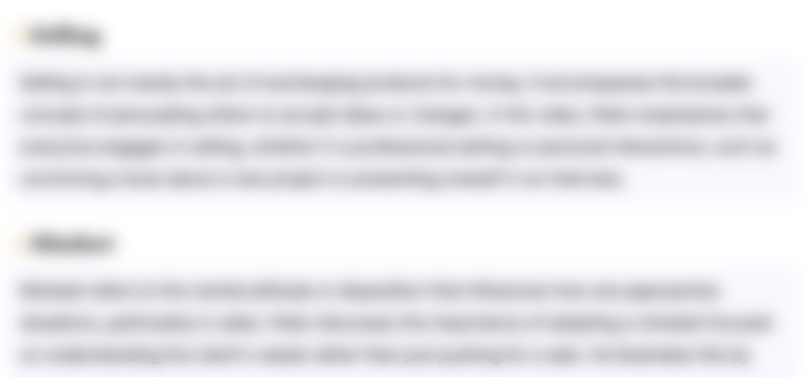
This section is available to paid users only. Please upgrade to access this part.
Upgrade NowHighlights
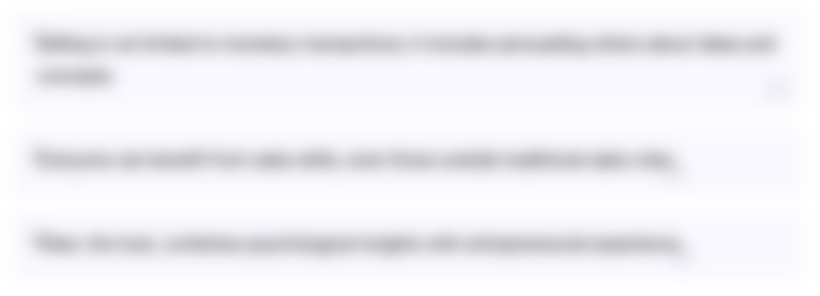
This section is available to paid users only. Please upgrade to access this part.
Upgrade NowTranscripts
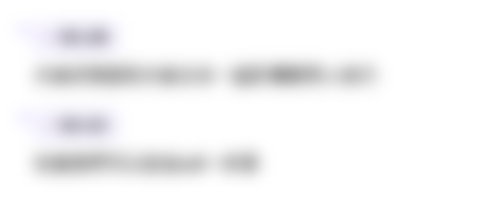
This section is available to paid users only. Please upgrade to access this part.
Upgrade NowBrowse More Related Video

Manajemen Persediaan (Inventory)
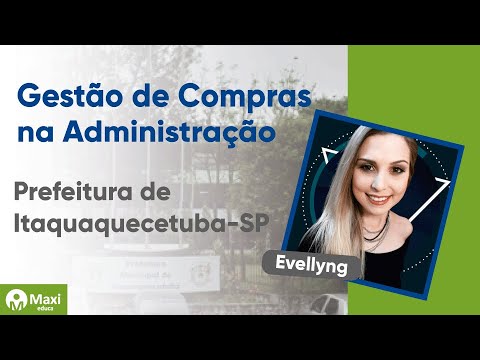
Gestão de compras - Prefeitura de Itaquaquecetuba-SP

Managing Your Assets 05 - The Parts You Need, When You Need Them

Chap 1 1 Operations Management at Frito Lay
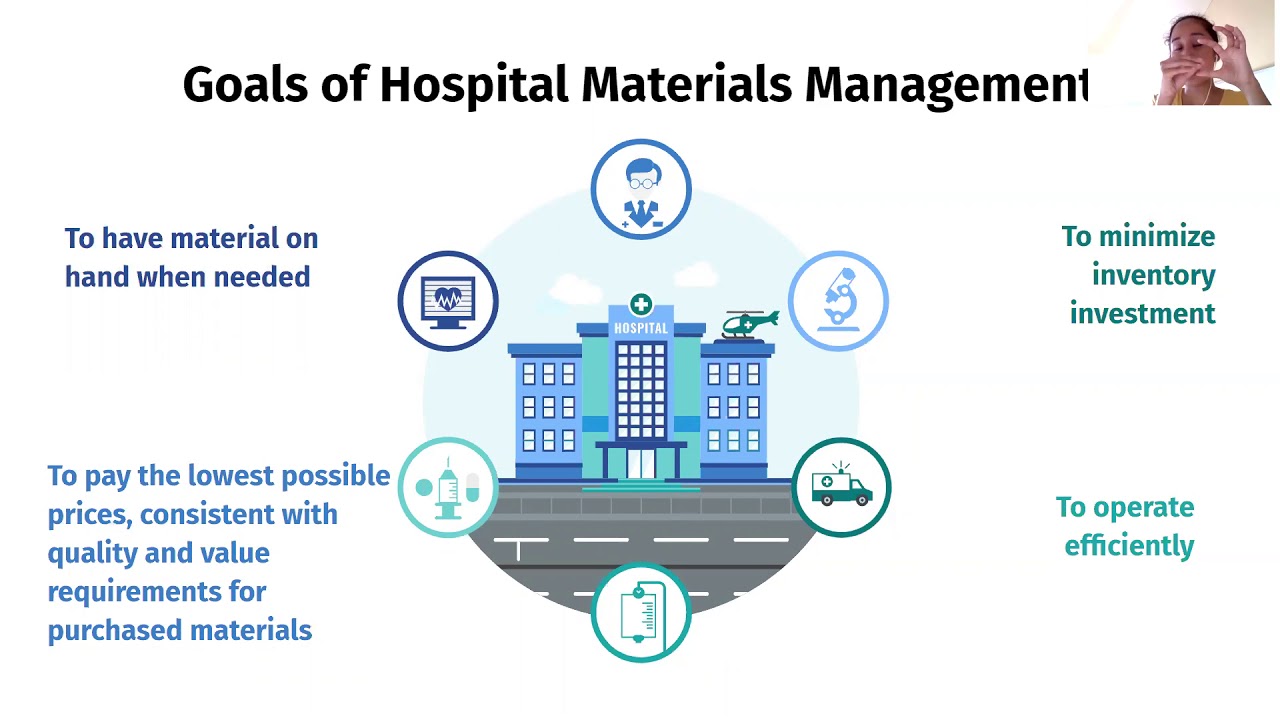
12 Hospital Materials Management -Health Information System for Medical Technologists (FILIPINO)
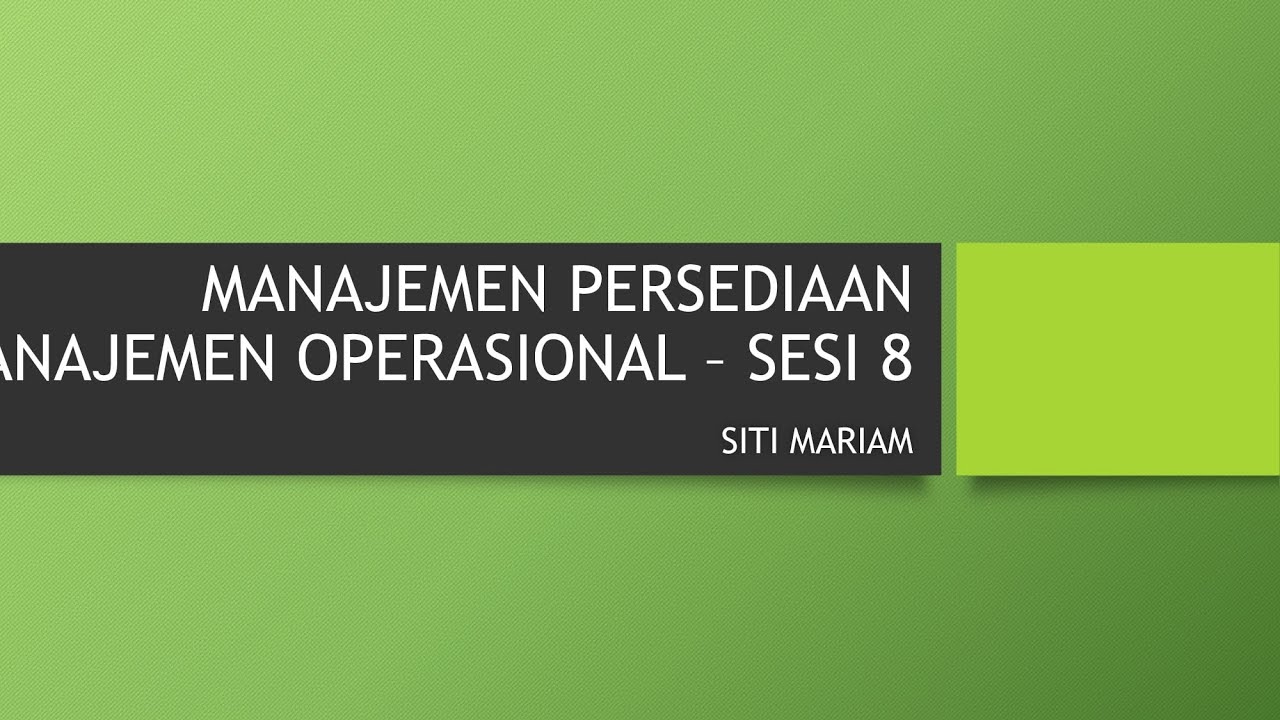
E learning : Manajemen Operasional - Sesi 8, Manajemen Persediaan | by Siti Mariam
5.0 / 5 (0 votes)