Gestão de compras - Prefeitura de Itaquaquecetuba-SP
Summary
TLDRThis video focuses on the essentials of purchasing and material management within organizations, covering both public and private sectors. It explores topics such as inventory control, supplier management, and stock optimization to enhance operational efficiency. The process of procurement is outlined, highlighting the importance of planning, minimizing costs, and ensuring materials meet the required specifications. Special attention is given to warehouse management (almoxarifado) and the need for accurate stock tracking to prevent disruptions in company operations. Ultimately, the video emphasizes maximizing resources and improving decision-making for effective material administration.
Takeaways
- 😀 Material management is crucial for both public and private organizations, ensuring smooth operations from purchase to stock management.
- 😀 The purchasing process begins with understanding the need for materials, determining quantities, and setting timeframes for procurement.
- 😀 In public organizations, purchases must adhere to legal regulations like Law 8666, which governs bidding and supplier selection.
- 😀 Private sector companies have more flexibility in their purchasing processes, handling negotiations and supplier relationships directly.
- 😀 Inventory management includes receiving materials, checking their compliance with orders, and managing stock accurately to avoid discrepancies.
- 😀 Almoxarifado refers to the physical warehouse, while estoque is the actual stock of materials within it.
- 😀 The role of inventory control is essential for maintaining stock accuracy, ensuring that the quantity and condition of items match the system records.
- 😀 Efficient material management involves optimizing resources, reducing waste, and ensuring the timely delivery of goods to avoid operational interruptions.
- 😀 Stockroom functions include verifying product quality and quantity upon delivery, accepting or rejecting goods based on compliance with orders.
- 😀 The importance of managing material obsolescence, especially for perishable goods, is critical to prevent losses and ensure resources are used optimally.
- 😀 A well-managed purchasing cycle ensures that all processes are coordinated to maintain an uninterrupted flow of materials, supporting the overall efficiency of the organization.
Q & A
What is the primary focus of the video script?
-The primary focus of the video is on the management of purchases, inventory, and the receipt of materials within the context of material administration in both public and private sectors.
Why is material management essential in organizations?
-Material management is crucial for ensuring that an organization effectively handles its resources from the purchasing stage to inventory control, ensuring smooth operations without interruptions in production or services.
What role does the purchasing process play in material management?
-The purchasing process is integral to material management as it ensures that the necessary materials are acquired at the right quantity, quality, and price to meet the organization’s needs.
What are the two main types of purchasing systems mentioned?
-The two main types of purchasing systems mentioned are centralized purchasing (where one unit buys for all others) and decentralized purchasing (where each unit buys separately).
How does inventory management contribute to the organization?
-Inventory management helps in maintaining stock at optimal levels, ensuring that the organization has the right materials available at the right time while avoiding overstocking or stockouts, thus preventing disruptions in operations.
What is the role of the inventory department in handling materials?
-The inventory or stock department is responsible for receiving, checking, and storing materials accurately, as well as managing the materials' movement, ensuring the stock aligns with the organization’s needs and system records.
How does the purchasing process differ between public and private sectors?
-In the public sector, the purchasing process must adhere to strict regulations like the Law 8666 for tenders and supplier registration. In the private sector, the process is more flexible, with companies having the freedom to negotiate directly with suppliers.
What is the importance of supplier verification in the purchasing process?
-Supplier verification is essential to ensure that the suppliers can meet the organization's needs in terms of quantity, quality, and delivery timelines, and that they comply with necessary regulatory requirements.
What is the significance of accurate inventory counts or stocktaking?
-Accurate inventory counts, or stocktaking, are crucial for ensuring that physical stock matches the recorded stock in the system. This helps prevent discrepancies, manage inventory efficiently, and track any missing or surplus items.
What is the difference between an inventory and an almoxarifado?
-An 'almoxarifado' refers to the physical space where materials are stored, while inventory refers to the actual materials or goods within that space. The almoxarifado is the storage area, and inventory is the items being managed within it.
Outlines
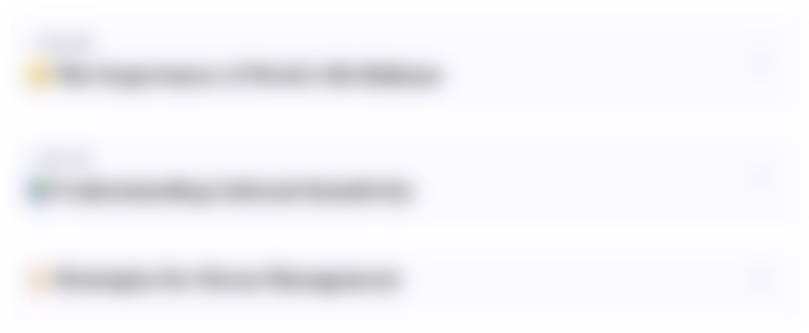
This section is available to paid users only. Please upgrade to access this part.
Upgrade NowMindmap
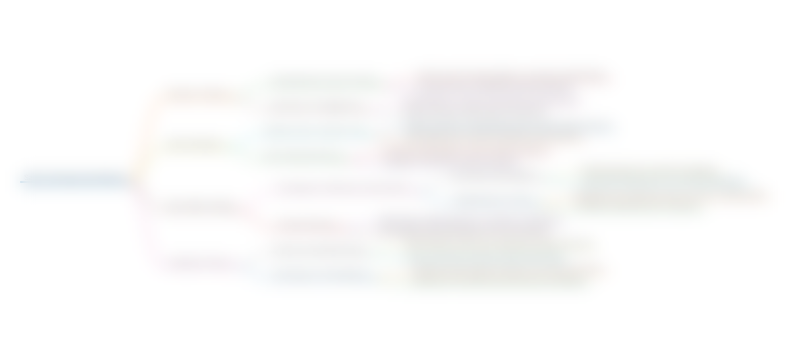
This section is available to paid users only. Please upgrade to access this part.
Upgrade NowKeywords
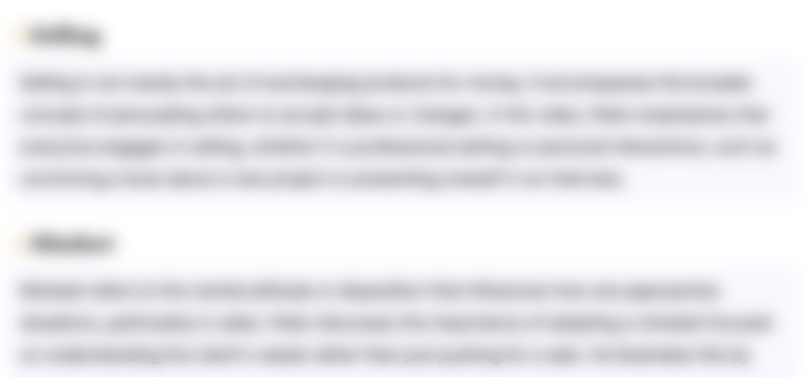
This section is available to paid users only. Please upgrade to access this part.
Upgrade NowHighlights
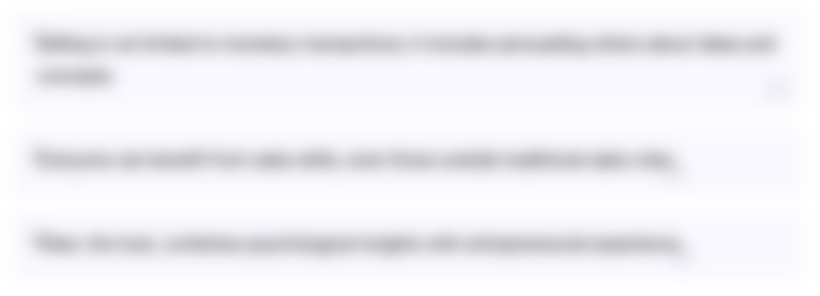
This section is available to paid users only. Please upgrade to access this part.
Upgrade NowTranscripts
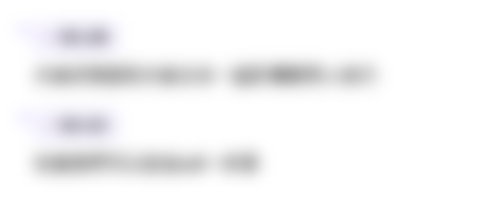
This section is available to paid users only. Please upgrade to access this part.
Upgrade NowBrowse More Related Video
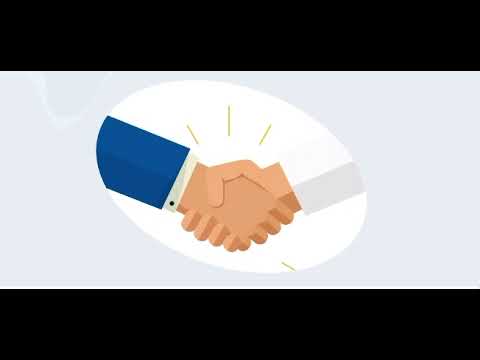
مجالات الإدارة
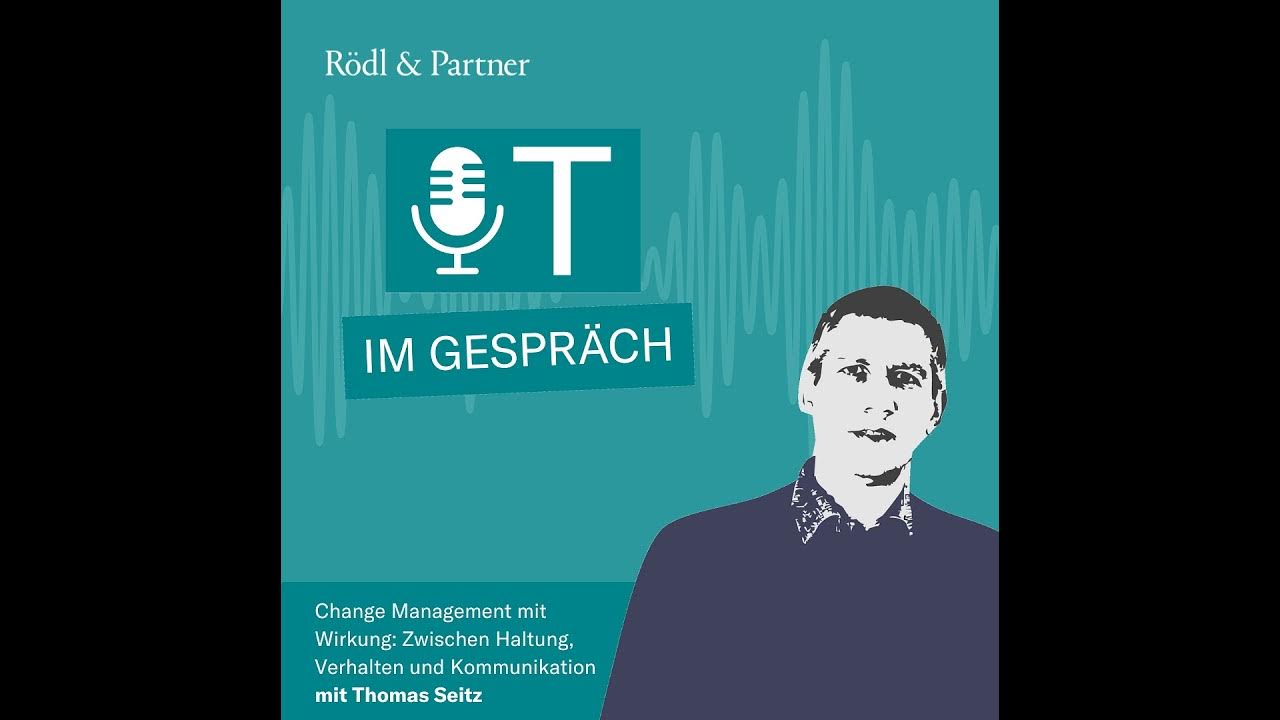
Change Management mit Wirkung: Über Haltung, Verhalten und Kommunikation

Complexity Management Course Intro

MATERI AUDIT SEKTOR PUBLIK - Gambaran Umum Audit Sektor Publik

Private & Public Sector Organisations | A-Level, IB & BTEC Business
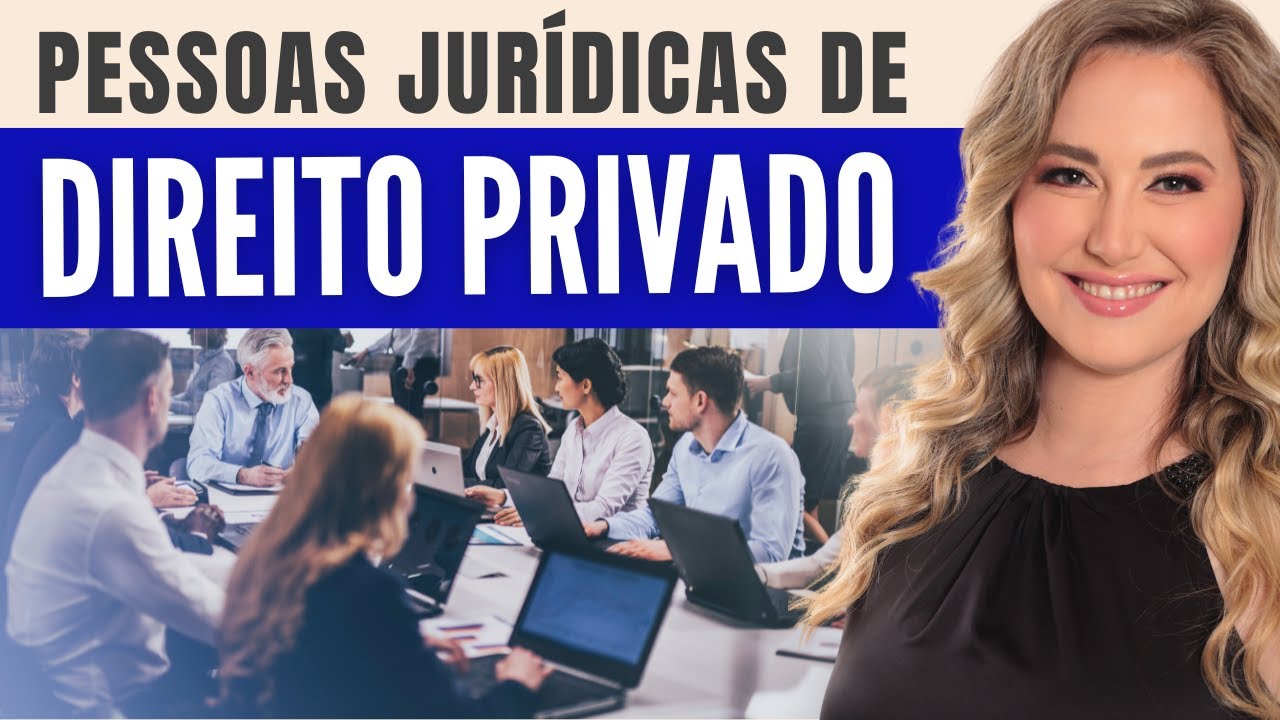
PESSOAS JURÍDICAS de Direito PRIVADO - Conceito, Exemplos e Resumo | Direito Civil
5.0 / 5 (0 votes)