Chap 1 1 Operations Management at Frito Lay
Summary
TLDRIn this Pearson's onlocation video, Jay Heiser and Barry Render, authors of the textbook on operations management, discuss the 10 key decisions faced by Fredo, a PepsiCo subsidiary and global snack producer. The company excels in product innovation, quality control, and green manufacturing, emphasizing sustainability. Fredo's operations are characterized by a product-focused strategy, efficient layout, and just-in-time inventory system, minimizing costs and maximizing productivity. The video highlights the importance of these decisions for all industries, emphasizing the need for innovation and operational excellence.
Takeaways
- 📘 The video is an educational series by Pearson focusing on operations management principles as applied to the fictional company Fredo, a subsidiary of PepsiCo.
- 🌐 Fredo is a global snack food manufacturer with a diverse product range and a commitment to innovation, introducing new products to stay competitive in the industry.
- 🔍 Fredo places a strong emphasis on quality control, with extensive inspections of raw materials and a quality focus team that meets regularly to maintain high standards.
- 🏭 The company employs statistical process control and has a product-focused strategy, optimizing production processes for high-volume, low-variety products.
- 🌿 Fredo is dedicated to green manufacturing and sustainability, including initiatives like solar power, recycling, and selling byproducts for animal feed.
- 📍 Plant locations are strategically chosen to be close to raw materials and customers, ensuring freshness and reducing the time products spend in transit.
- 🔄 Fredo operates a just-in-time inventory system, turning over inventory 200 times a year, which is significantly higher than the industry average.
- 👥 The company has one of the lowest personnel turnovers in the industry, attributing this to competitive wages, benefits, and a respectful work environment.
- 🚚 Fredo's supply chain is integral to its success, with a focus on efficient movement from raw materials to finished goods, sometimes requiring ownership of farms and control over transportation.
- 📊 Demand planning at Fredo is comprehensive, taking into account historical sales, new product introductions, production innovations, promotions, and local demand forecasts.
- 🛠 Maintenance is crucial for Fredo's operations, as even a 1% downtime can result in significant financial losses, highlighting the importance of equipment reliability.
Q & A
What is the main topic of the Pearson's onlocation video series?
-The main topic of the video series is an overview of the 10 decisions of operations management as they relate to an international company, Fredo, a subsidiary of PepsiCo.
What are the 10 major operations management decisions mentioned in the script?
-The 10 major operations management decisions are design of goods and services, quality, process strategy, location, layout, human resources, supply chain management, inventory, schedule, and maintenance.
What is Fredo's position in the snack industry?
-Fredo is a multi-billion dollar snack producer and the world's largest, with over 40 different product lines, including seven with sales of over a billion dollars each.
How does Fredo ensure the quality of its products?
-Fredo ensures product quality through extensive inspections of all raw materials, additional inspection points during the production process, and the use of statistical process control. The quality focus team meets weekly, and the company consistently scores well above the passing mark on the American Institute of Baking's unannounced inspections.
What is a product-focused strategy according to the script?
-A product-focused strategy builds processes for specific types of products, such as steel, glass, beer, and commercial baked goods. These are high volume, low variety products, and organizations using this strategy tend to invest heavily in technology and sequence equipment to rapidly process the product.
How does Fredo approach green manufacturing and sustainability?
-Fredo places great emphasis on green manufacturing and sustainability by converting to solar power to reduce electricity use, increasing the recycling of cardboard boxes, and selling byproducts like potato peels for animal feed.
Why are plant locations for food products like Fredo's chips chosen with proximity to raw materials and customers?
-Plant locations are chosen for proximity to raw materials and customers to ensure products have a short shelf life and can be on the shelf as quickly as possible, sometimes within 24 hours of picking potatoes in the field.
What is the layout strategy used by Fredo for producing potato chips?
-Fredo uses a product-oriented layout for producing potato chips, where raw potatoes get washed, peeled, sliced, cooked, seasoned, and bagged in a single assembly line over a few hours.
How does Fredo manage its inventory to minimize costs?
-Fredo manages its inventory with a just-in-time inventory system, turning it over 200 times a year, which is significantly higher than other manufacturing firms. This involves delivering raw materials like potatoes 10 times a day and monitoring delivery truck locations by GPS.
What factors contribute to Fredo's low personnel turnover in the industry?
-Fredo's low personnel turnover is attributed to competitive wages and benefits, concern for ergonomics and safety, treating all employees with respect from packers to plant executives, and providing uniforms and shoes for all staff.
How does Fredo's supply chain contribute to the company's success?
-Fredo's supply chain is integral to its success, taking products from farm-fresh raw materials to finished goods in a very short time. This sometimes requires owning their own farms, controlling transportation trucks, warehousing, distribution, and delivery.
How does Fredo plan for total demand by product?
-Fredo planners prepare a total demand by product using historical sales data, new product introductions, production innovations, promotions, and dynamic local demand forecasts. Final schedules may be adjusted for known local events unique to the region served by the plant.
What is the significance of maintenance in Fredo's operations?
-Maintenance is crucial in Fredo's operations as every 1% of downtime means a loss of $200,000 at the Florida plant. Despite not being the newest in the Fredo family, the plant still has utilization at world-class levels, highlighting the importance of effective maintenance.
Outlines
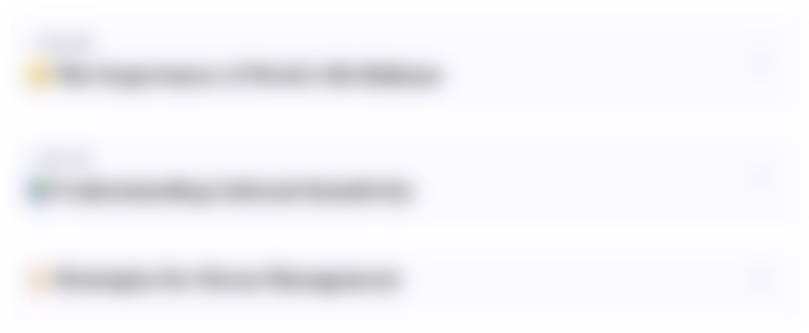
This section is available to paid users only. Please upgrade to access this part.
Upgrade NowMindmap
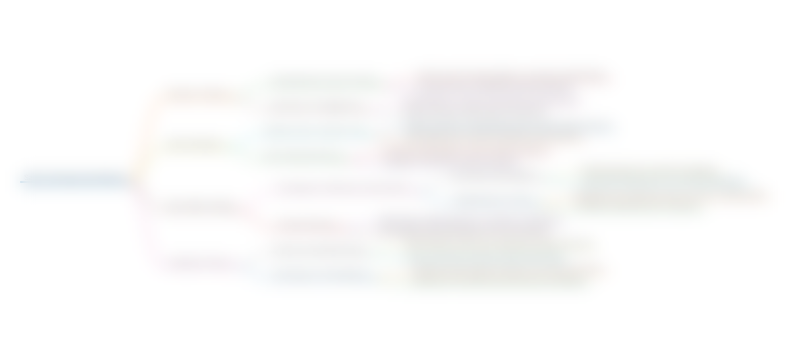
This section is available to paid users only. Please upgrade to access this part.
Upgrade NowKeywords
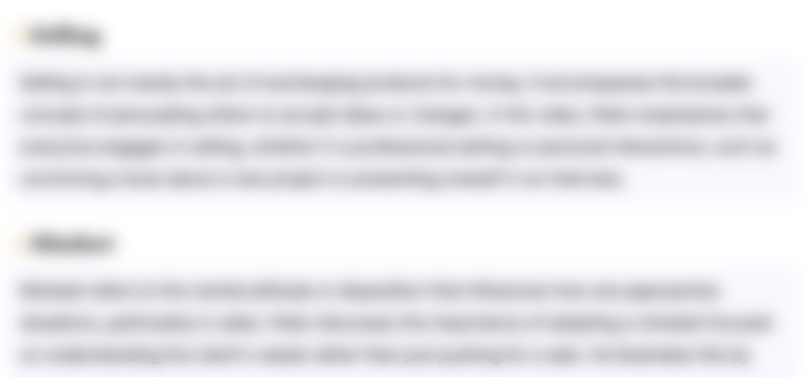
This section is available to paid users only. Please upgrade to access this part.
Upgrade NowHighlights
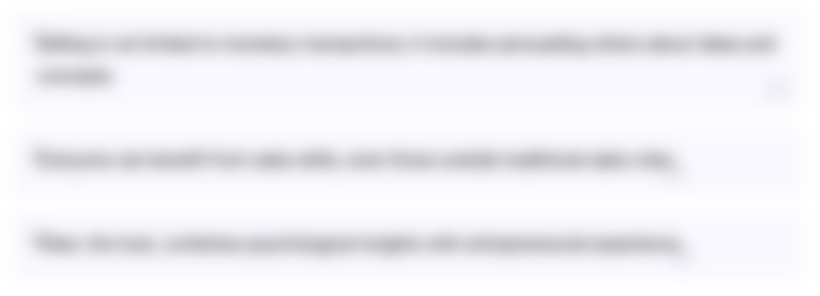
This section is available to paid users only. Please upgrade to access this part.
Upgrade NowTranscripts
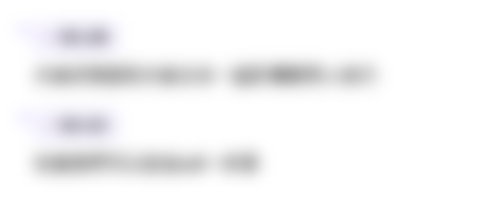
This section is available to paid users only. Please upgrade to access this part.
Upgrade NowBrowse More Related Video

Staffing Strategy in International Busines | From a Business Professor

Global production and supply chain management

10 Biggest Mining Operations in The World

This Indian Brand is Destroying Lays and Kurkure 🔥
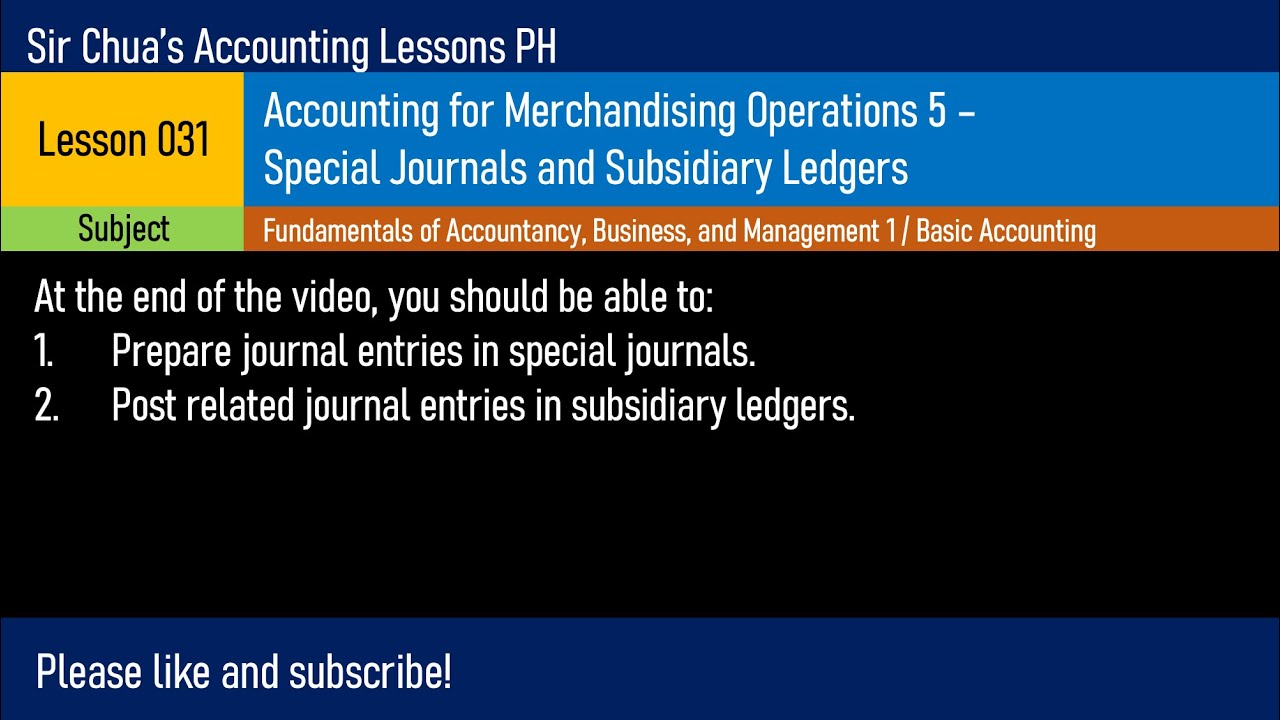
Lesson 031 - Accounting for Merchandising Operations 5: Special Journals and Subsidiary Ledgers
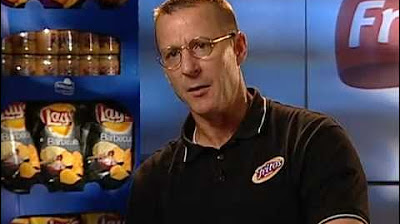
Green Manufacturing and Sustainability at Frito Lay
5.0 / 5 (0 votes)