Toughening up composites: Damage mechanisms and fracture
Summary
TLDRProfessor Kostas Cities from the University of Munster discusses toughened composites in aerospace engineering at the first virtual European conference on fracture. He highlights the benefits of composites, such as weight reduction and high strength, and delves into damage mechanisms and the development of mathematical models for predicting and optimizing composite behavior. The talk also explores innovative solutions like hybrid structures, graphene nano-modification, and 3D weaving for enhancing damage tolerance and performance in dynamic events.
Takeaways
- 🎓 Kostas Tsitouras, a professor of aerospace engineering at the University of Munster, presented at the first virtual European Conference on Fracture, highlighting the significance of composite materials in various industries.
- 🛠 Composite materials, particularly carbon fiber reinforced polymers (CFRPs), are valued for their lightweight, high strength, and stiffness, as well as their ability to be tailored for specific applications.
- 🚀 The aerospace and defense industries utilize CFRPs extensively for their performance benefits, such as reduced weight, improved fatigue resistance, and the potential for embedded functionality like damage sensing and self-healing.
- 🏗️ Composites have been adopted in various sectors including energy, marine, construction, and transportation due to their versatility and performance advantages over traditional materials.
- 📈 The history of CFRPs spans nearly 60 years, with significant milestones such as the introduction of the first commercial product by Dunlop in 1983 and the use of CFRPs in Formula One cars by McLaren in 1995.
- 🔍 Despite their benefits, composites can suffer damage under both static and dynamic loading, leading to issues like transverse cracking and delamination, which necessitate advanced modeling for damage prediction and management.
- 📚 Mathematical models are crucial for calculating stresses, predicting damage, and estimating the long-term performance of composite structures, enabling optimization of material properties and structural design.
- 🛡️ The development of damage-tolerant and toughened composites involves creating materials that can absorb energy without catastrophic failure, such as through the use of hybrid layered structures combining metals and composites.
- 🔬 Innovative techniques like 3D weaving and the incorporation of thermoplastic interlayers can enhance the damage resistance and tolerance of composites, making them more robust against impact and fatigue.
- 📈 The use of graphene in composites presents a promising avenue for improving mechanical properties, thermal conductivity, and electrical conductivity, offering multifunctional benefits.
- 💡 Challenges in the composites field include reducing production costs, increasing manufacturing speed and volume, and developing reliable models for structural integrity assessment, which are critical for the advancement and adoption of composite materials.
Q & A
Who is the speaker in the provided transcript and what is their field of expertise?
-The speaker is Kostas D. Soutis, a professor of aerospace engineering from the University of Manchester.
What is the significance of the first virtual European conference on fracture?
-The conference is significant as it is the first of its kind to be held virtually, focusing on the topic of fracture, and it represents a platform for experts like Professor Soutis to present their research.
Which university is recognized as Britain's first University of the Industrial Age with strong research in advanced materials?
-The University of Manchester is recognized as Britain's first University of the Industrial Age with strong research in advanced materials.
What are the benefits of using composite materials in aerospace engineering?
-Composite materials offer benefits such as weight reduction, high strength and stiffness, tailorable mechanical properties, complex shape and contour creation, reduced part count compared to metallic equivalents, less machining, corrosion resistance in aggressive environments, and good fatigue resistance with potential for embedded functionality like damage sensing and self-healing.
What is the history of commercial applications of carbon fiber composites?
-Carbon fiber composites have been around for almost 60 years, with the first commercial product appearing in 1983 when Dunlop produced their first carbon fiber tennis racket. In 1995, McLaren used carbon fiber composites for a Formula One car.
How do composite materials contribute to the design and performance of the Airbus A350?
-The Airbus A350 features an entire section made out of carbon fiber, with more than 52 percent of the aircraft's structure composed of carbon fiber composites, contributing to its lightweight and high-strength design.
What are the challenges associated with the fatigue behavior of carbon fiber composites?
-Fatigue in carbon fiber composites can lead to damage accumulation in the form of transverse cracking, delamination at the crack tip, and split tensile cracking in the 90-degree layers, which can eventually trigger fiber breakage.
What role do mathematical models play in understanding and optimizing composite materials?
-Mathematical models are crucial for calculating stresses in composite configurations, considering damage mechanisms, estimating the effect of damage on stiffness and strength, and predicting long-term performance, which aids in optimizing composite properties and design.
What is the significance of fiber micro buckling in the context of composite materials?
-Fiber micro buckling is a critical damage mode in composite materials, which is very brittle in nature. When it reaches a critical length, it can become unstable, leading to catastrophic fracture. Identifying these cracks non-destructively before they become unstable is a significant challenge.
How can hybrid layered structures improve the toughness and damage tolerance of composite materials?
-Hybrid layered structures, which combine metal and composite layers, can optimize strength, stiffness, and toughness properties. They can absorb energy during impact events without perforation, demonstrating damage tolerance and the ability to accommodate extensive damage without loss of structural integrity.
What is the potential of graphene in enhancing the properties of composite materials?
-Graphene, a two-dimensional material with exceptional mechanical, electrical, and thermal properties, can be used to nano-modify epoxy resins in composites, improving their thermal conductivity, impact resistance, fatigue life, and providing strain sensing capabilities, among other enhancements.
What are some of the current challenges in the manufacturing and application of polymer composites?
-Current challenges include increasing the supply of raw materials, reducing material and finished part costs, increasing the speed and volume of manufacturing, addressing the challenges of machining, drilling, assembly, joining, and repairing polymer composites, and developing non-destructive evaluation techniques and real-time structural health monitoring methods.
Outlines
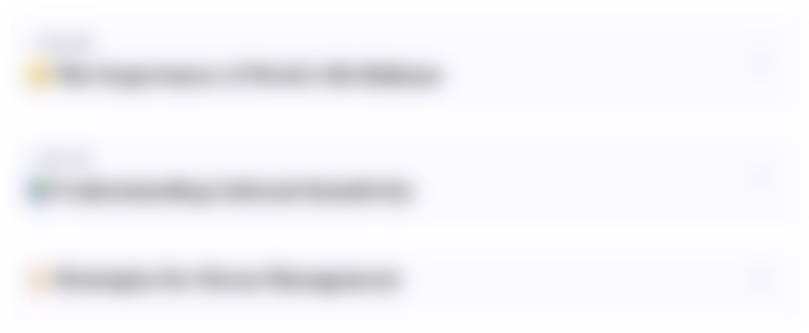
This section is available to paid users only. Please upgrade to access this part.
Upgrade NowMindmap
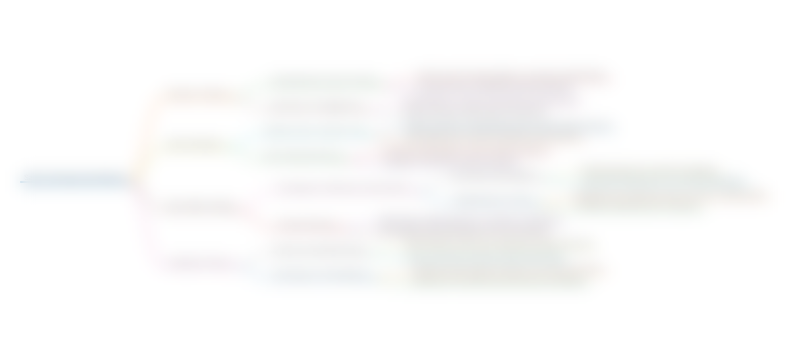
This section is available to paid users only. Please upgrade to access this part.
Upgrade NowKeywords
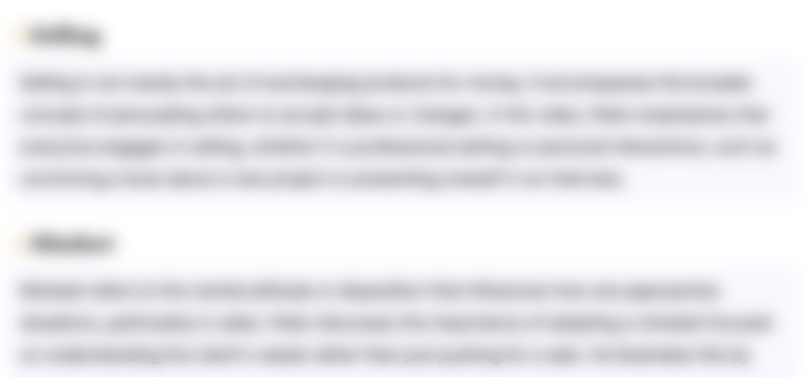
This section is available to paid users only. Please upgrade to access this part.
Upgrade NowHighlights
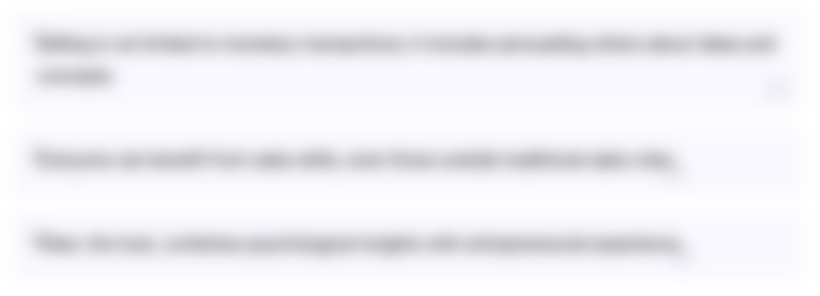
This section is available to paid users only. Please upgrade to access this part.
Upgrade NowTranscripts
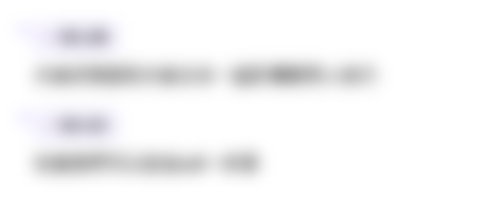
This section is available to paid users only. Please upgrade to access this part.
Upgrade NowBrowse More Related Video
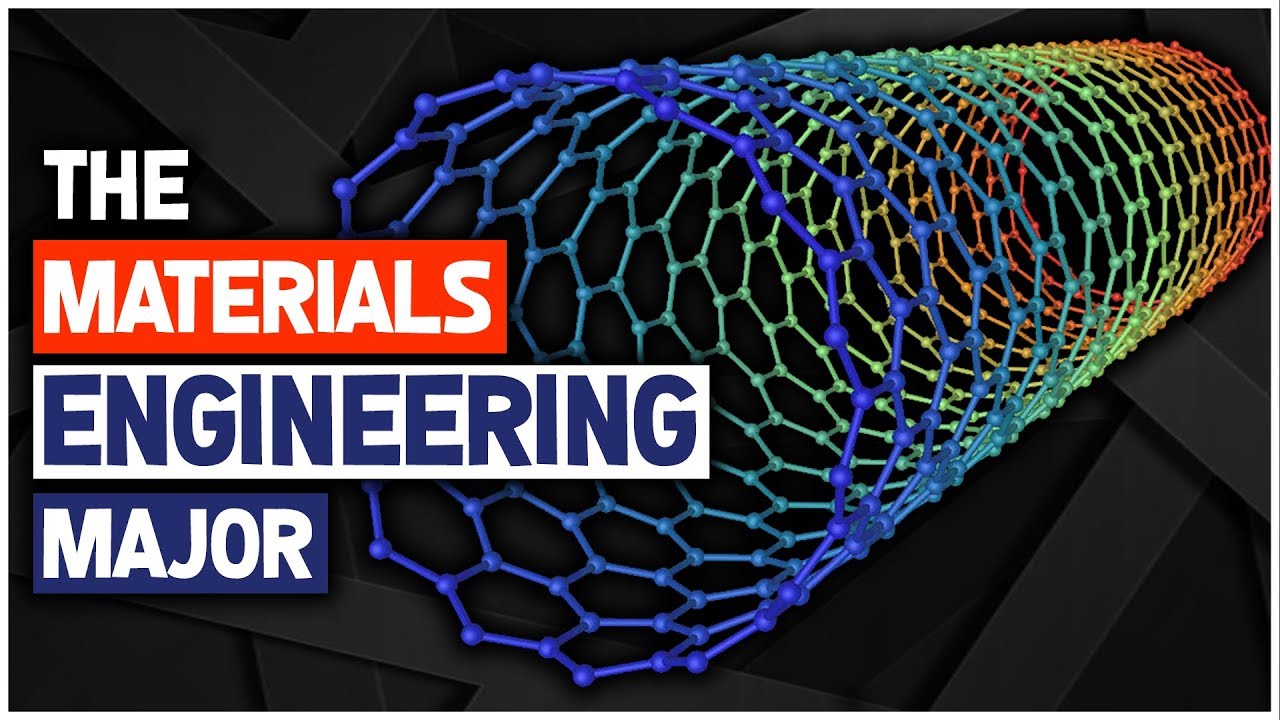
What is Materials Engineering?
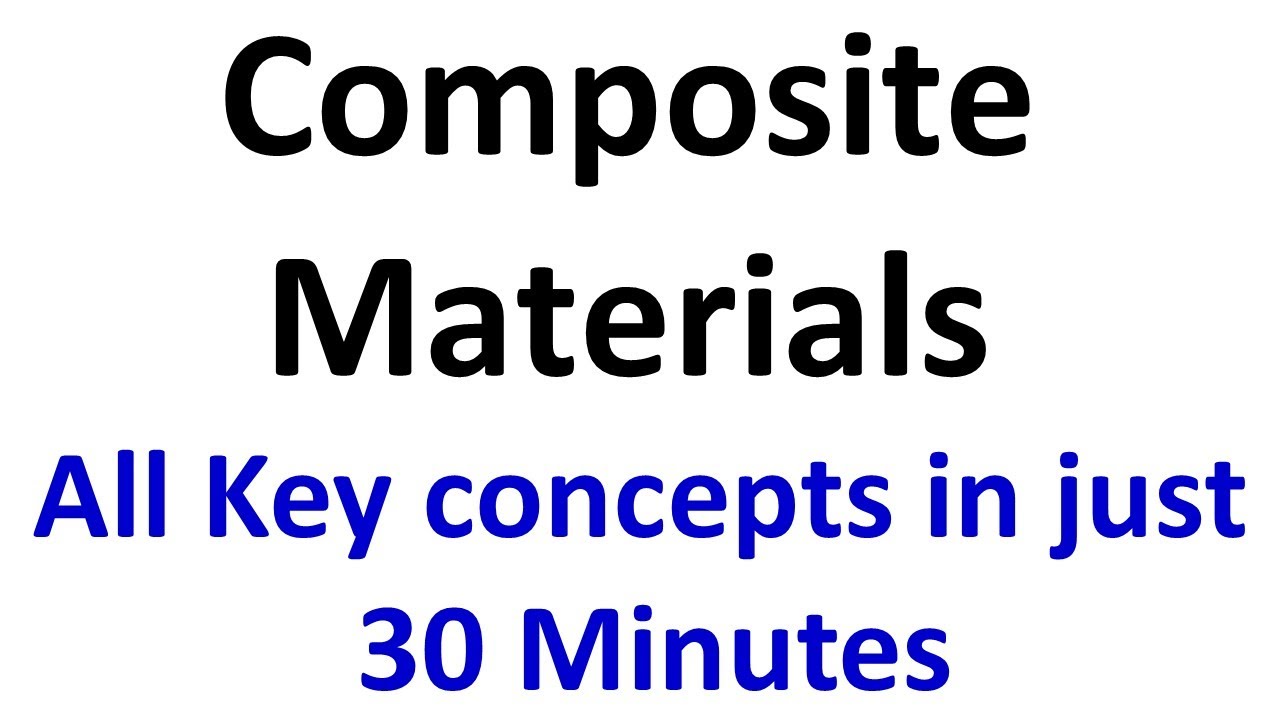
Lecture # 40-41 | Composite Materials | All Key concepts in just 30 Minutes
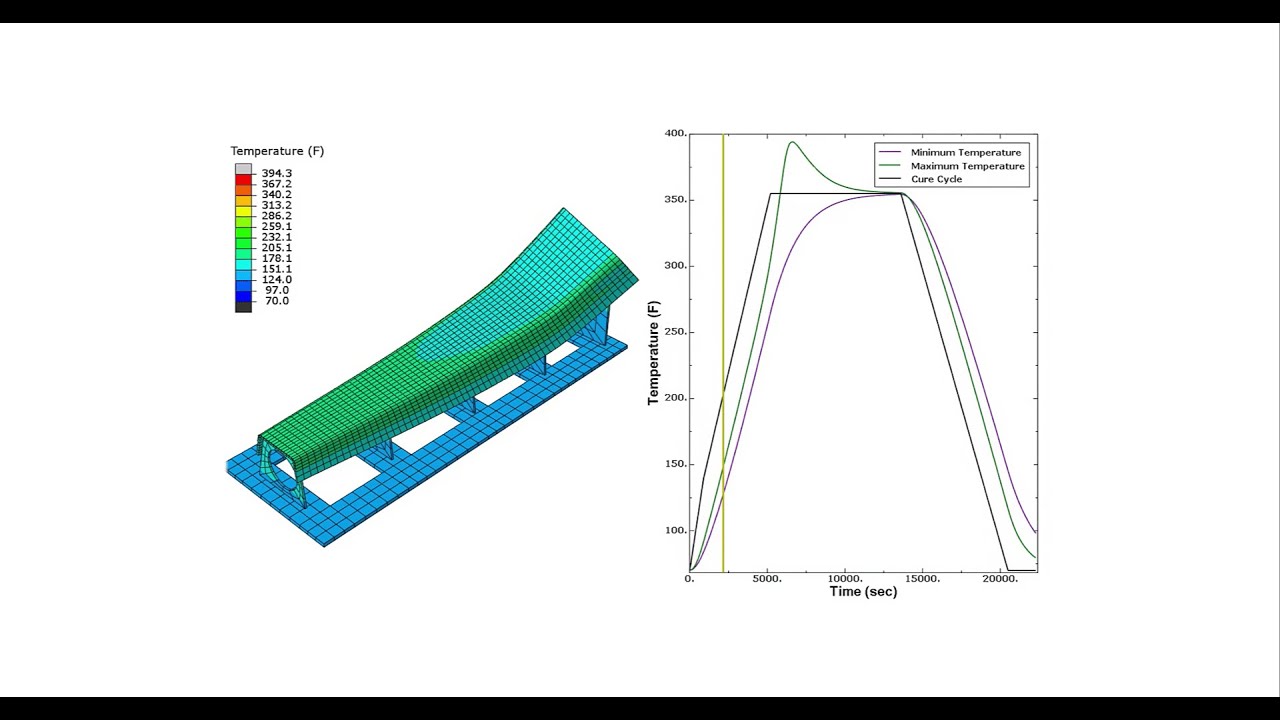
Simulation based Engineering of Composite Materials

Topic 6: Fracture Mechanisms Lecture 4
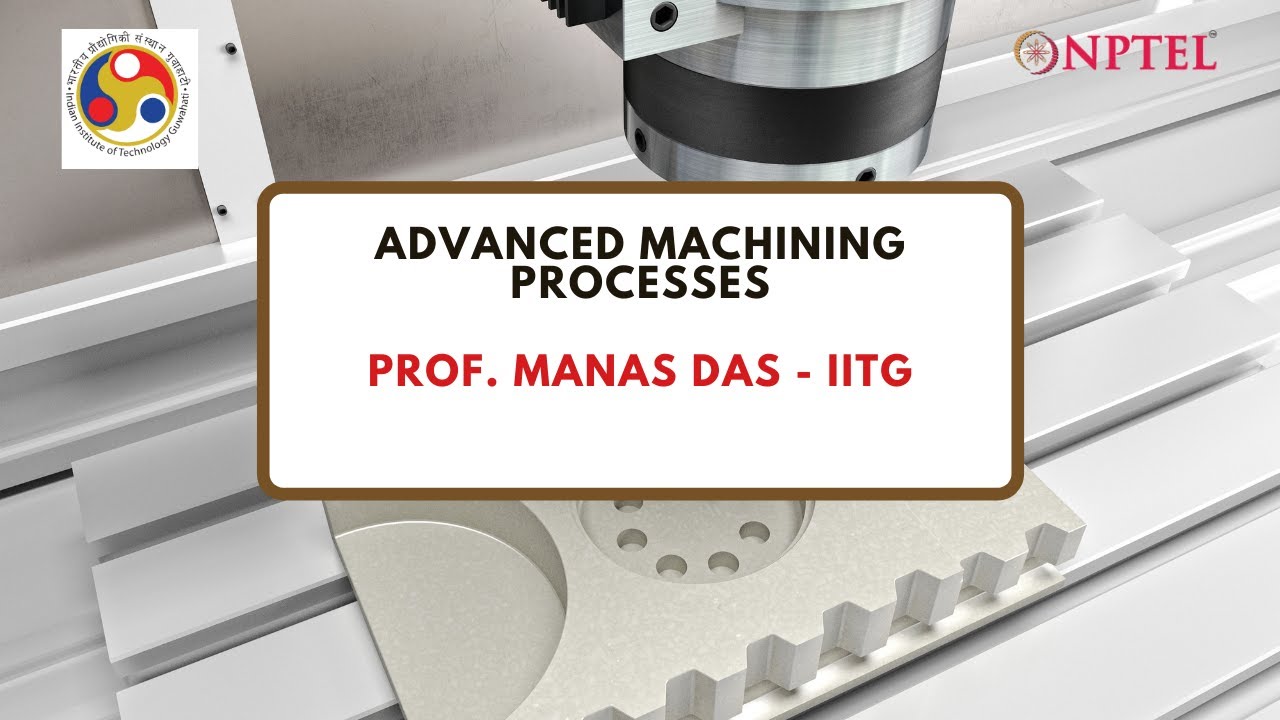
Introduction: Advanced Machining Processes
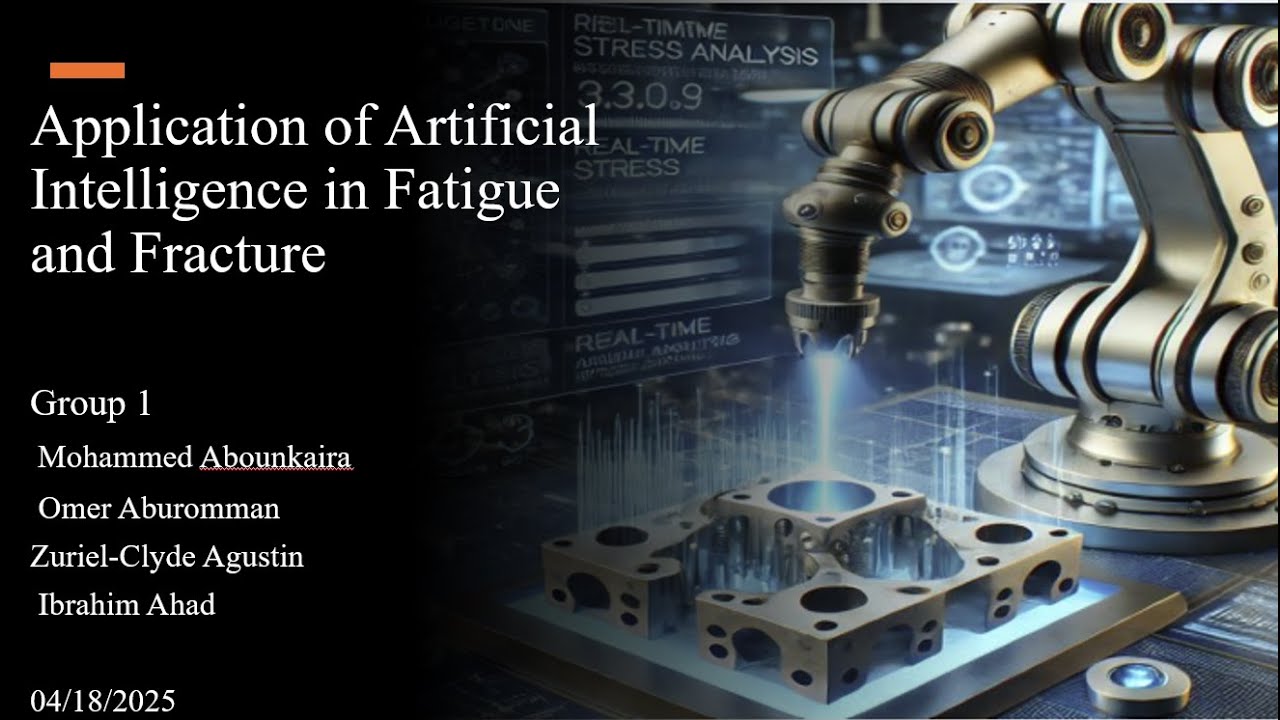
ME401 Group1 Application of Artificial Intelligence In Fatigue and Fracture
5.0 / 5 (0 votes)