We make our own body panels for a Lada
Summary
TLDRIn this episode, the host introduces a vacuum forming machine, central to creating custom car parts. They announce new merchandise discounts, including hoodies, and demonstrate the machine's process of molding ABS plastic into panels. Challenges arise with power limitations and uneven plastic stretching, but the team successfully creates durable fenders. The video explores the cost-effectiveness of plastic parts versus metal, inviting viewers to share ideas for further applications.
Takeaways
- 🛍️ The video introduces new merchandise available on their website, including signature hoodies and other items like t-shirts, baseball caps, mugs, and document holders.
- 💰 A 25% discount is offered to the first 25 people who order the signature hoodies, with additional discounts on the entire product lineup.
- 🎁 With every order, a free sticker is included as a bonus.
- 🛠️ The main focus of the episode is a vacuum forming machine, which is used to mold plastic into various shapes for car parts like bumpers and fender flares.
- 🔨 The machine consists of a bench, frame, and uses a heating process with lamps to soften the plastic, followed by vacuum molding over a form or mold.
- ⚡️ The machine requires a significant amount of power, but the team finds a workaround by using a smaller configuration to accommodate the facility's power limitations.
- 🔧 The process involves placing a sheet of plastic onto the frame, heating it, and then molding it over a form while applying vacuum to achieve the desired shape.
- 🚗 The team attempts to replicate a car door panel and front fenders using the vacuum forming machine, experimenting with different materials and thicknesses of plastic.
- 🔄 They encounter challenges such as uneven plastic distribution and vacuum leaks, but manage to produce usable plastic panels despite these issues.
- 💡 The video highlights the cost-effectiveness of using plastic for car parts compared to metal, with significant savings on materials and production costs.
- 📈 The vacuum forming machine is a valuable tool for custom part production, especially for those with experience in the field, and the team invites viewers to share their ideas and suggestions.
Q & A
What is the main focus of the episode described in the transcript?
-The main focus of the episode is the introduction and demonstration of a vacuum forming machine used for creating various plastic parts such as bumpers, fender flares, and other panels.
What kind of merchandise is being promoted in the video?
-The merchandise being promoted includes signature hoodies, t-shirts, baseball caps, mugs, document holders, and stickers, all available with discounts on the website.
What special offer is made for the first 25 customers who order the signature hoodies?
-The first 25 customers to order the signature hoodies are offered a 25% discount on their purchase.
What material is commonly used with the vacuum forming machine for creating plastic parts?
-ABS plastic is commonly used with the vacuum forming machine for creating plastic parts due to its workability with this type of equipment.
What is the issue with the power requirements of the vacuum forming machine?
-The vacuum forming machine requires 48 kilowatts of power, but the facility has a limitation of approximately 30 kilowatts, which restricts the use of all 48 lamps simultaneously.
How is the plastic sheet secured in place on the frame before the molding process begins?
-The plastic sheet is secured in place on the frame using silicone seals that tightly press against the sheet, and it is pinched all around to lock it in place.
What is the purpose of the vacuum pump and reservoirs in the vacuum forming machine?
-The vacuum pump and reservoirs are used to create a vacuum that sucks down the hot plastic and wraps it tightly around the mold on the tabletop, forming the desired shape.
What was the initial problem encountered when trying to mold a door panel?
-The initial problem was that the vacuum leaked out, preventing the plastic from stretching out evenly and resulting in a puffy and half-baked appearance in some areas.
How did the team improve the molding process for the front fenders?
-The team improved the molding process by honing their skills, using one mil thick ABS plastic and HDPE plastic, and ensuring a proper fit and vacuum application.
What is the advantage of using plastic panels over metal parts in certain applications?
-Plastic panels are advantageous in applications like drift cars where aesthetics are less critical because they are cheaper to make, lighter, and can be easily replaced if damaged.
What was the cost of the vacuum forming machine mentioned in the transcript?
-The vacuum forming machine cost a bit under 300,000 rubles, or approximately four thousand US dollars, including shipping.
Outlines
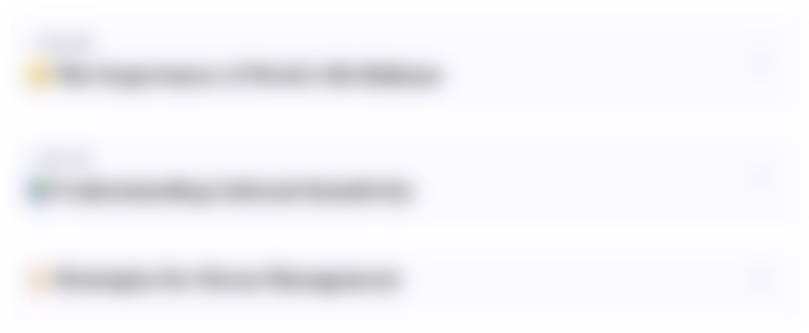
This section is available to paid users only. Please upgrade to access this part.
Upgrade NowMindmap
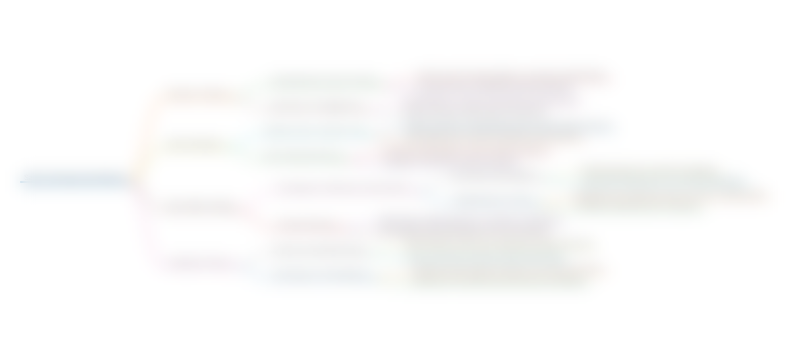
This section is available to paid users only. Please upgrade to access this part.
Upgrade NowKeywords
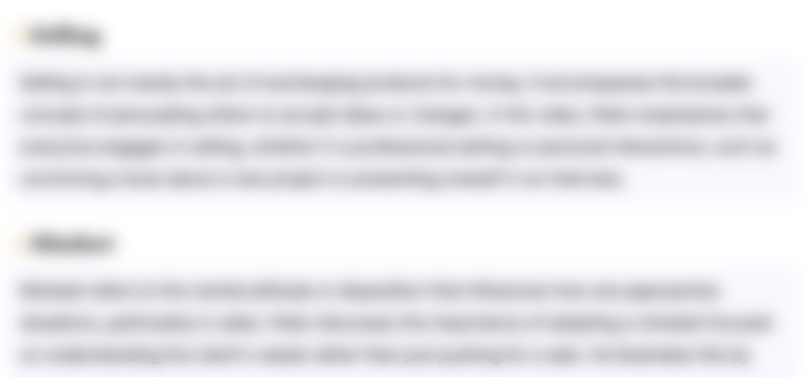
This section is available to paid users only. Please upgrade to access this part.
Upgrade NowHighlights
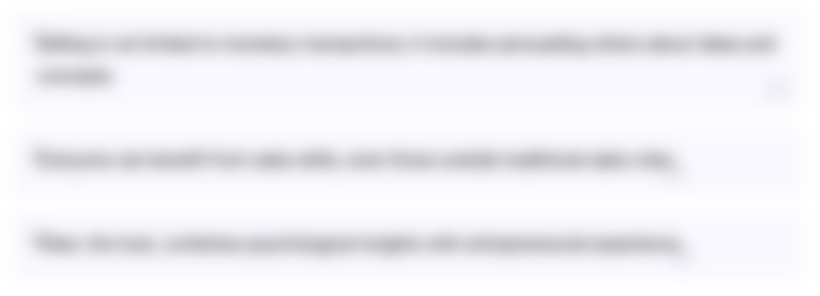
This section is available to paid users only. Please upgrade to access this part.
Upgrade NowTranscripts
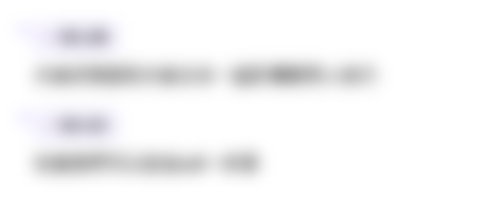
This section is available to paid users only. Please upgrade to access this part.
Upgrade NowBrowse More Related Video

I Taught a YouTuber How to Make $1 Billion

直管『VT250Z』金属バットで作ったマフラーの音が超害悪すぎるw

PAINTING My Rat Rod Honda-Stang!? ("Masutangu" Rebuild Pt.5)
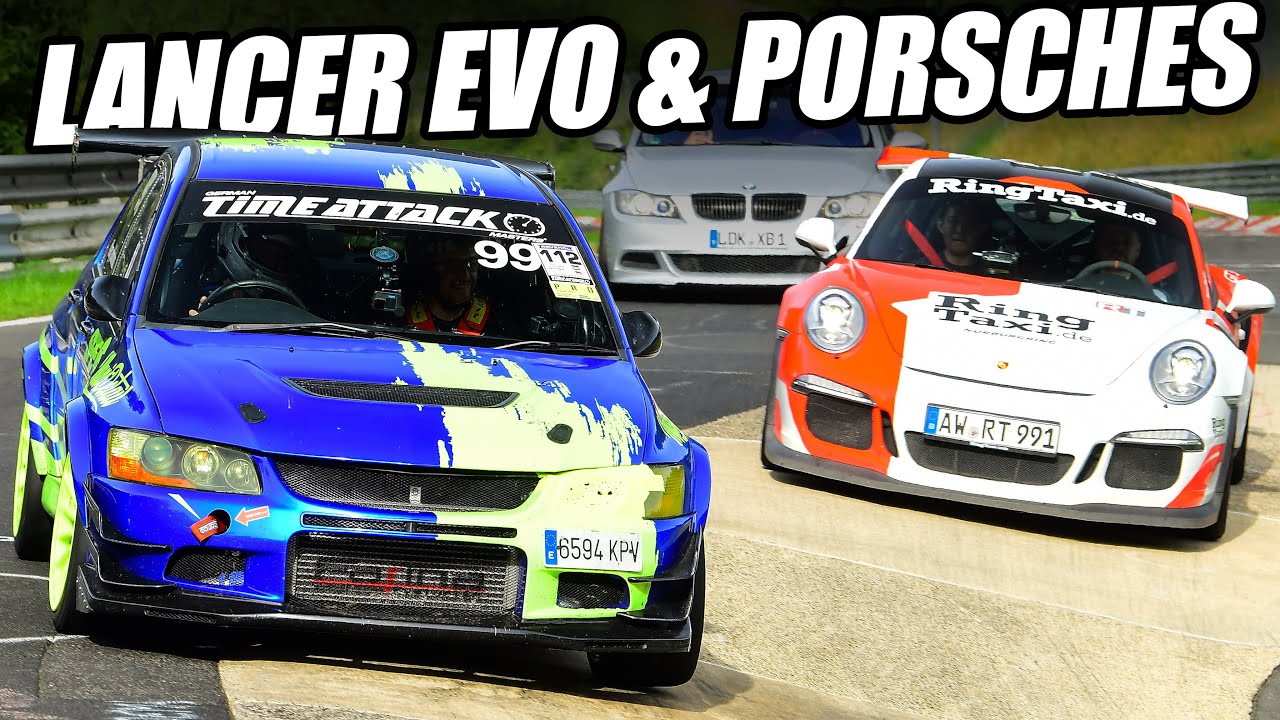
TIME ATTACK Lancer EVO 8 & Porsches 😏 // Nürburgring!
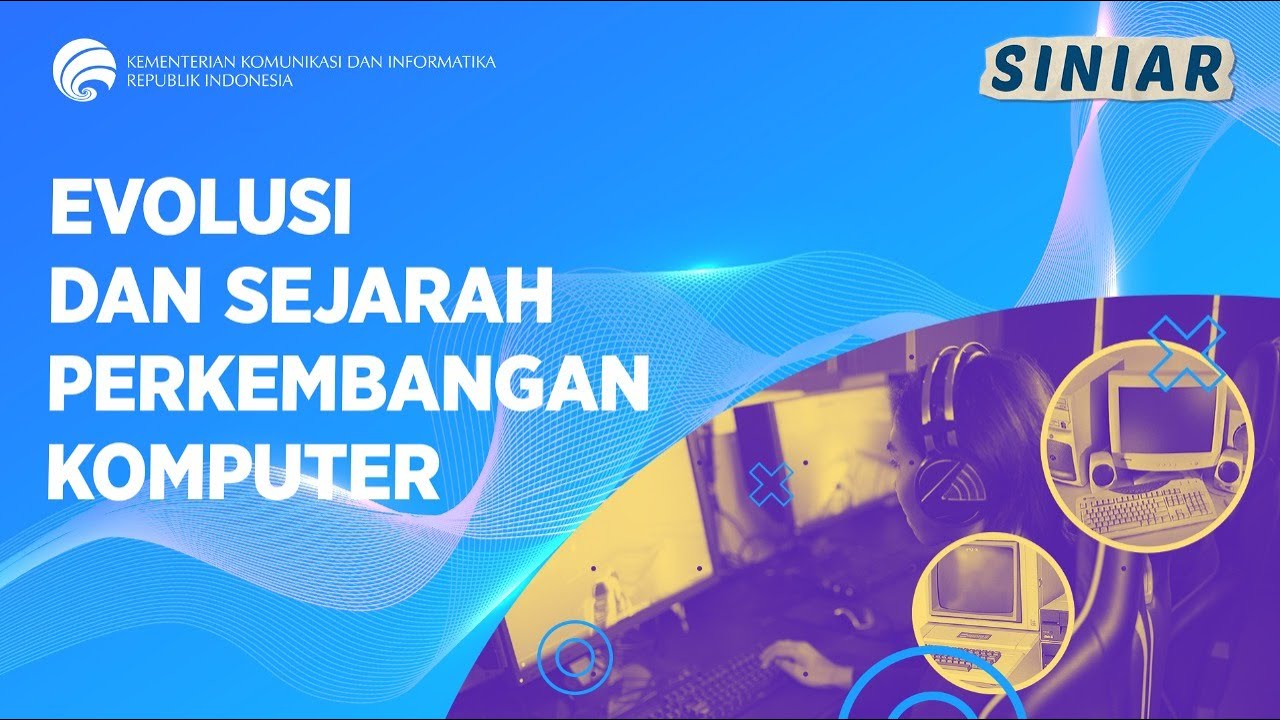
EVOLUSI DAN SEJARAH PERKEMBANGAN KOMPUTER - SINIAR
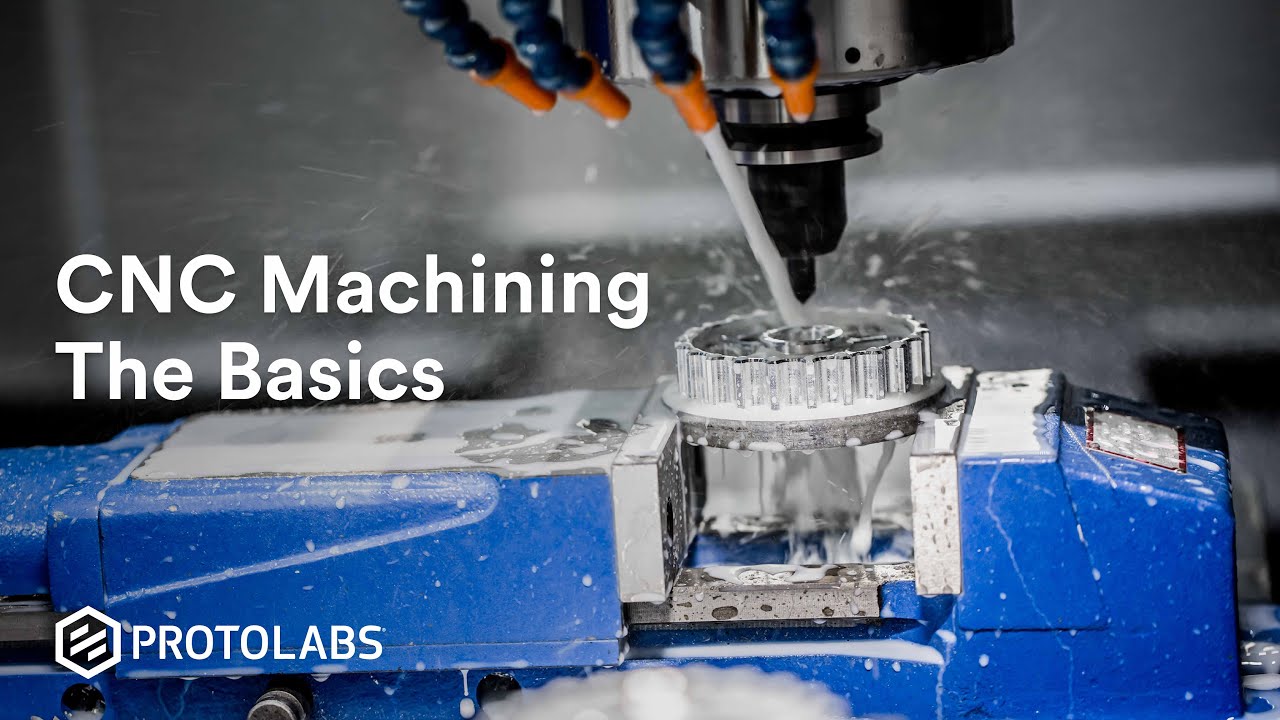
CNC machining - What is it and How Does it Work? (Must Know Basics)
5.0 / 5 (0 votes)