Materiais e Processos de Fabricação para Engenharia de Produção - Fundição - Conceito, etapas e...
Summary
TLDRThis lecture on casting processes in metalworking introduces the fundamentals of casting, emphasizing the transformation of metal from solid to liquid and back to solid through molding. It highlights the simplicity and versatility of the process, which is ideal for producing complex shapes and large pieces at a controlled cost. The lecture covers key stages like design, molding, pouring, solidifying, and post-processing, such as cleaning and deburring. It also discusses the challenges, including mechanical property limitations, the need for surface finishing, and safety concerns. Various casting techniques, particularly sand casting, and the importance of proper mold design are explored.
Takeaways
- 😀 The casting process is essential in the metal-mechanical industry, primarily used for creating metal parts by transforming metal from a solid to a liquid state, then back to solid after molding.
- 😀 Casting can be used to create both final products and preparations for further processing, making it versatile in manufacturing.
- 😀 The process involves pouring liquid metal into molds, which are then solidified to form the desired shape of the piece.
- 😀 One advantage of casting is its ability to produce complex shapes with a relatively simple process, offering cost-effective production and good control over manufacturing expenses.
- 😀 Casting is particularly useful for creating large metal parts, with molds capable of handling substantial dimensions.
- 😀 Some limitations of casting include challenges with achieving high precision in dimensions, which may require additional finishing processes like cleaning and surface treatment.
- 😀 Safety and environmental concerns are significant in casting, with risks associated with molten metal handling and potential emissions, depending on the type of mold used.
- 😀 The typical casting process involves designing the part, creating a model, making molds, pouring metal into the molds, and cleaning up the cast part after solidification.
- 😀 Molds are often made from sand, and they can be classified as either open or closed, depending on whether the mold is destroyed after use or can be reused.
- 😀 Special features in the mold, such as a core (or 'macho'), are essential for forming internal cavities in the final part, and channels are included to feed metal into the mold to prevent defects like air pockets.
- 😀 The metal is usually melted in furnaces and transferred to molds using tools like crucibles. Once the metal solidifies, the part is cleaned, excess material is removed, and the surface is finished before the part undergoes any additional treatments.
Q & A
What is the main principle behind the casting process?
-The casting process is based on the transformation of metal from a solid state to a liquid state and then back to a solid state as it cools and solidifies in a mold. This allows the creation of metal parts with complex shapes.
What are the advantages of casting in the manufacturing process?
-Casting offers several advantages, including simplicity in creating complex shapes, economic competitiveness due to reduced production steps, and the ability to produce large metal parts with a high production volume.
What are some common problems associated with casting?
-Some common issues in casting include limitations in mechanical properties of the cast part, difficulties in achieving precise dimensional accuracy, the need for post-casting cleaning and finishing, and occupational safety concerns due to the high temperatures and liquid metal involved.
What are the key stages of the casting process?
-The key stages of the casting process include designing the part, creating the model, molding the part, pouring the molten metal into the mold, allowing it to solidify, removing the mold, and performing cleaning and reworking steps like deburring.
What is the role of the 'feeding system' in casting?
-The feeding system, which includes the sprue and feeders, helps guide the molten metal into the mold cavity. It also ensures that as the metal solidifies and contracts, additional material is supplied to avoid voids or air pockets in the final piece.
Why is the design of the part important in the casting process?
-Proper part design is crucial to avoid defects like shrinkage, voids, and cracks. The design must ensure smooth transitions in the material, avoid sharp corners, and account for shrinkage during cooling to achieve a high-quality cast part.
What are the differences between expendable and permanent molds in casting?
-Expendable molds are destroyed after each casting, while permanent molds can be reused multiple times for casting. Expendable molds are typically made from materials like sand, while permanent molds are made from metals that can withstand repeated use.
How does the use of sand in casting affect the process?
-Sand molds are commonly used in casting due to their ability to withstand high temperatures and their flexibility in forming complex shapes. The sand is mixed with binding agents to create a mold that is used once and then destroyed after the casting is removed.
What is the function of the 'core' in sand casting?
-The core, often made from a more heat-resistant sand, is used to form hollow sections or voids within the cast part. It is placed within the mold to ensure specific features like internal cavities are present in the final piece.
What are some safety concerns when performing casting processes?
-Casting involves risks such as exposure to extreme temperatures, molten metal splashes, and the potential release of harmful gases during the process. Proper safety measures must be in place to protect workers, including the use of protective gear and proper ventilation.
Outlines
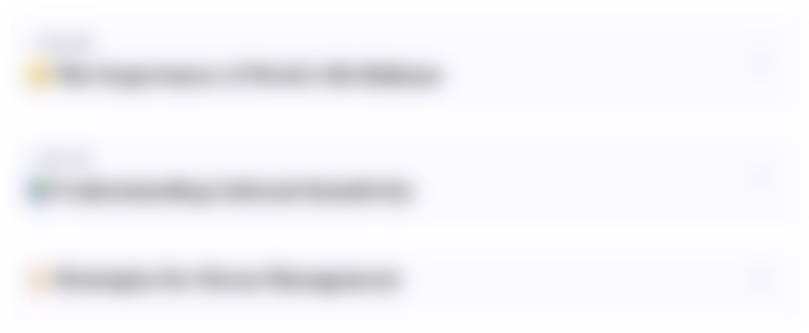
This section is available to paid users only. Please upgrade to access this part.
Upgrade NowMindmap
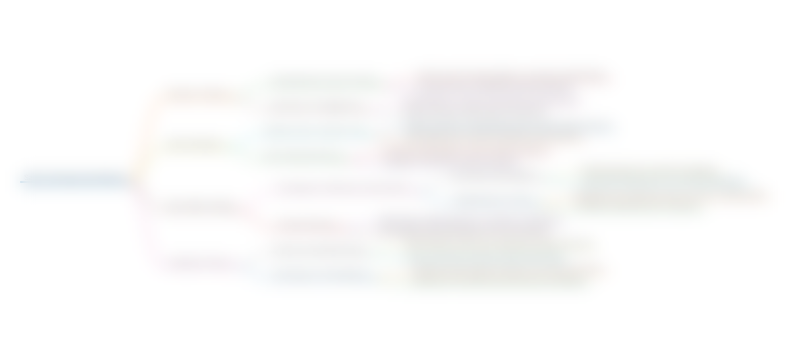
This section is available to paid users only. Please upgrade to access this part.
Upgrade NowKeywords
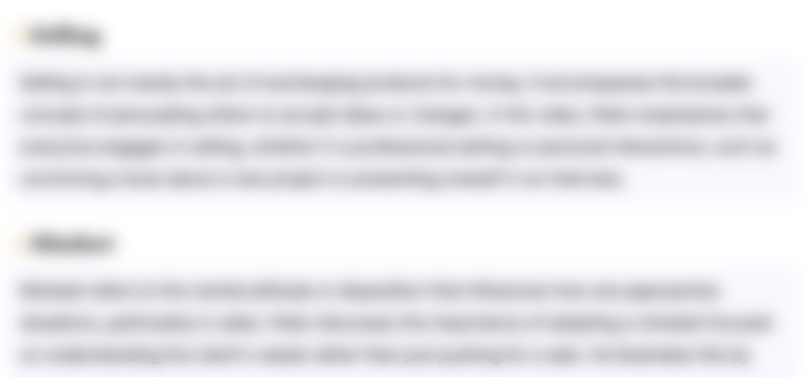
This section is available to paid users only. Please upgrade to access this part.
Upgrade NowHighlights
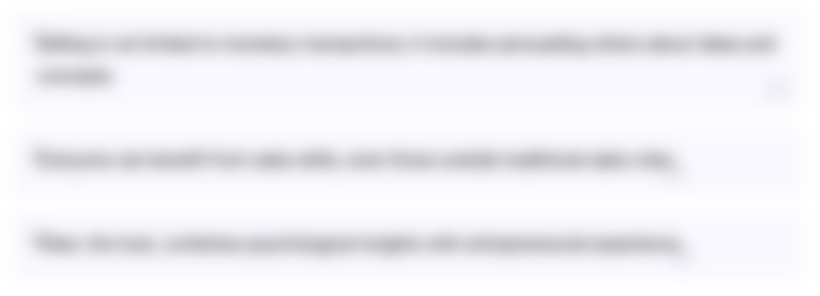
This section is available to paid users only. Please upgrade to access this part.
Upgrade NowTranscripts
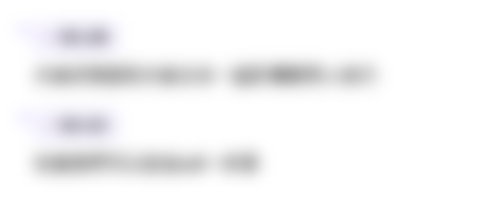
This section is available to paid users only. Please upgrade to access this part.
Upgrade NowBrowse More Related Video

PENGECORAN LOGAM | Praktikum MK Teknologi Manufaktur
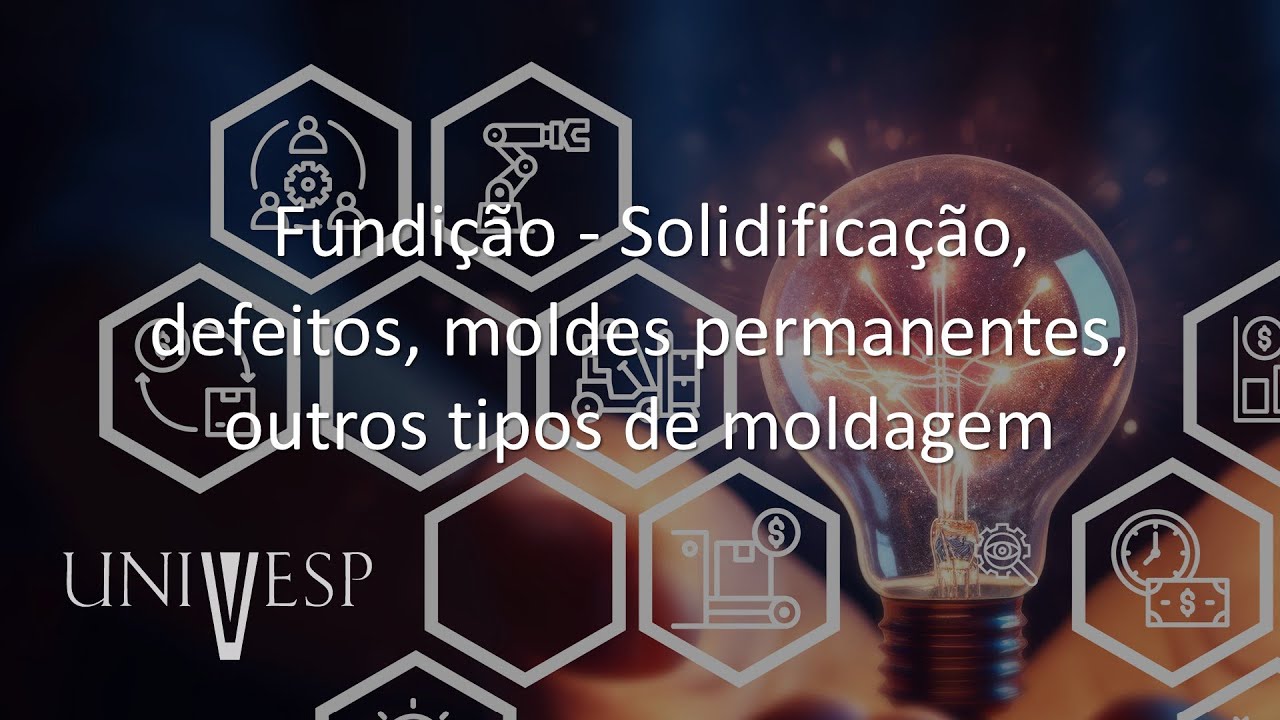
Materiais e Processos de Fabricação para Engenharia de Produção - Fundição - Solidificação, defeitos

Proses Pengecoran

Casting Allowances in Hindi || Allowances in Casting

What Is Casting? 11 Types of Casting Processes Explanation

What Are The Common Types Of Metal Casting Process In Engineering and Industry?
5.0 / 5 (0 votes)