Hot Dip Galvanis
Summary
TLDRThis presentation discusses the hot-dip galvanizing process, a method of coating steel and iron to improve corrosion resistance. The process involves dipping the metal into molten zinc to create a durable, protective layer. The script explains the preparation steps, including cleaning the surface through mechanical and chemical methods, followed by the dipping process, which forms a multi-layered coating. The benefits of galvanizing, such as enhanced durability and corrosion resistance, are highlighted, alongside its limitations, like the requirement for simpler metal shapes and thicker coatings. The presentation also covers the various testing standards and potential risks associated with over-thick coatings.
Takeaways
- 😀 The presentation discusses the hot-dip galvanizing process, a method of coating metal (usually steel or iron) with zinc to prevent corrosion.
- 😀 Hot-dip galvanizing involves dipping metal into molten zinc, forming a metallurgically strong bond between zinc and the base metal.
- 😀 The main purpose of hot-dip galvanizing is to increase the metal's resistance to corrosion by providing a protective zinc layer.
- 😀 The zinc layer in hot-dip galvanizing provides cathodic protection, meaning it protects the underlying metal even if the coating is scratched.
- 😀 Common metals used in hot-dip galvanizing include zinc (Zn), tin (Sn), lead (Pb), and aluminum (Al).
- 😀 The galvanizing process enhances metal durability, making it resistant to weathering, rust, and other environmental factors.
- 😀 Challenges of hot-dip galvanizing include the need for a clean metal surface, the relatively thick coating produced, and the method's limitation to non-complex metal shapes.
- 😀 Surface preparation for galvanizing includes cleaning the metal to remove dirt, grease, and oxidation, which ensures a smooth, clean surface for coating.
- 😀 The process consists of several stages: surface preparation, pickling, rinsing, fluxing, and finally, dipping the metal into molten zinc.
- 😀 Post-galvanizing, the metal undergoes cooling, either by immersion in sodium chrome solution or water, to prevent oxidation and ensure durability.
Q & A
What is the hot-dip galvanizing process described in the transcript?
-Hot-dip galvanizing is a process where steel or iron is dipped into molten zinc to form a strong, metallurgically bonded coating that provides corrosion resistance. The process involves several stages, including surface preparation, cleaning, and dipping into molten zinc.
What are the main benefits of using hot-dip galvanizing for metal coating?
-The main benefits of hot-dip galvanizing are increased corrosion resistance, durability, and long-term protection for metals, especially steel and iron, making them more resistant to environmental damage.
What metals are typically used in the hot-dip galvanizing process?
-The metals typically used in the hot-dip galvanizing process include zinc (ZN), tin (SN), lead (PP), and aluminum. Zinc is the most commonly used material.
How does the galvanizing process protect the metal from corrosion?
-The zinc coating applied during hot-dip galvanizing acts as a sacrificial anode, protecting the underlying steel or iron by corroding first, thus preventing rust and corrosion of the base metal.
What are the key stages involved in the hot-dip galvanizing process?
-The key stages include surface preparation (cleaning), pre-treatment, the actual dipping process into molten zinc, cooling and drying, and post-dip inspection to ensure the coating is of high quality.
Why is surface preparation important in the galvanizing process?
-Surface preparation is crucial as it ensures the metal surface is free from contaminants such as oil, grease, and rust. This allows the zinc to bond properly, resulting in a stronger, more effective coating.
What are some of the cleaning methods used during surface preparation?
-Cleaning methods include physical cleaning (using grinding machines to smooth rough surfaces), chemical cleaning (using caustic soda solutions to remove grease and oil), and acid cleaning (using hydrochloric or sulfuric acid to remove rust and scale).
What risks are associated with excessive coating thickness in hot-dip galvanizing?
-Excessive coating thickness can lead to issues such as flaking, cracking, and delamination of the zinc coating, which can compromise the protective qualities of the galvanizing and cause premature failure of the coating.
What is the structure of the coating formed during hot-dip galvanizing?
-The coating consists of several layers, including a top layer of pure zinc (Eta), a middle layer of zinc-iron alloys (Gamma, Delta, Zeta), and a bonding layer that adheres to the steel or iron. These layers provide both mechanical strength and corrosion resistance.
How is the quality of the galvanizing coating inspected?
-The quality of the galvanizing coating is inspected by examining its uniformity, thickness, and adhesion. Tests like visual inspection, thickness measurements, and adherence checks are commonly used to ensure the coating meets standards.
Outlines
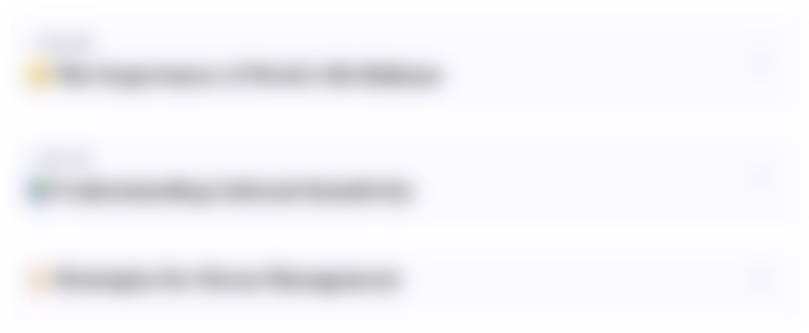
This section is available to paid users only. Please upgrade to access this part.
Upgrade NowMindmap
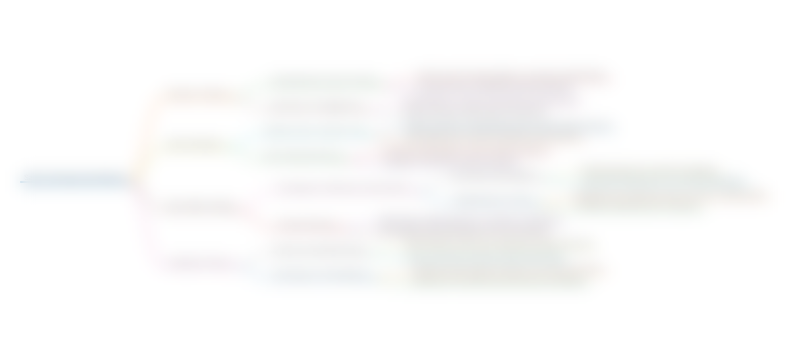
This section is available to paid users only. Please upgrade to access this part.
Upgrade NowKeywords
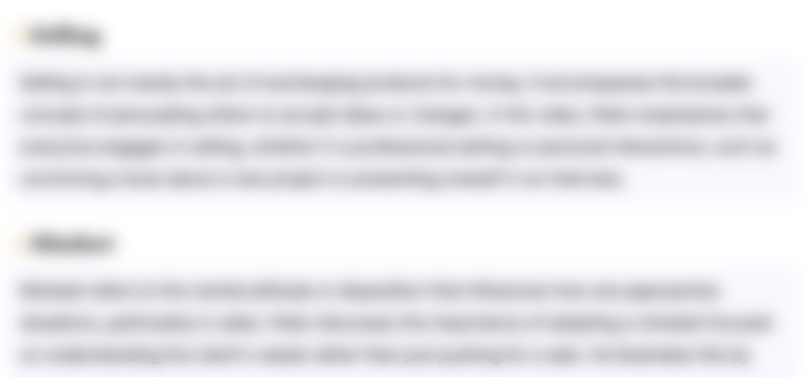
This section is available to paid users only. Please upgrade to access this part.
Upgrade NowHighlights
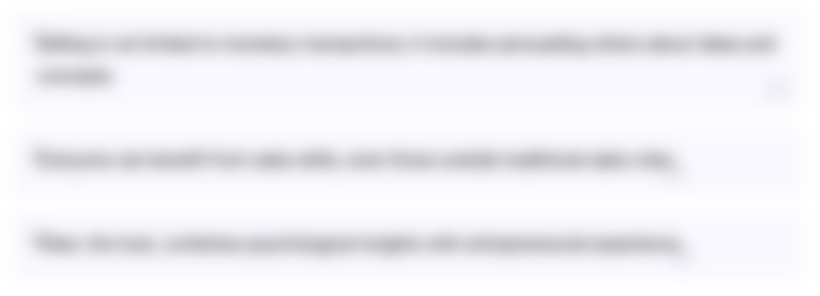
This section is available to paid users only. Please upgrade to access this part.
Upgrade NowTranscripts
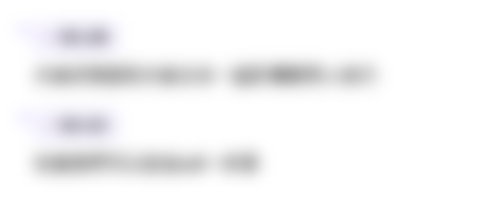
This section is available to paid users only. Please upgrade to access this part.
Upgrade Now5.0 / 5 (0 votes)