Die forging process(open and closed die)
Summary
TLDRForging is a metalworking process that shapes metal through compressive forces, using tools like hammers or presses to apply high-velocity impacts or controlled pressures. Dating back to 8,000 BC, it refines metal's structure, improves grain flow, and eliminates imperfections. Open die forging deforms metal between flat or shaped dies, making large, simple parts. Impression die forging involves forming metal in heated cavities with multiple strokes for complex shapes. Flash forms during the process, which is later trimmed. Forging produces stronger, more durable parts compared to casting, benefiting industries requiring high-performance materials.
Takeaways
- 😀 Forging is a metalworking process that uses compressive forces, such as hammer impacts or press forces, to shape metal.
- 😀 The process of forging dates back to around 8,000 BC and is still widely used in metalworking today.
- 😀 Forging helps reduce cross-section, improve metallurgical microstructure, and provide directional grain flow in metals.
- 😀 The mechanical performance of forged materials is typically superior to cast metals due to better microstructure and grain flow.
- 😀 Open die forging involves deforming a workpiece between flat or shaped dies, without fully restricting metal flow.
- 😀 Open die forging can produce items from a few centimeters to 30 meters in length and weigh up to several hundred thousand kilograms.
- 😀 Complex shapes can be made with open die forging, but most are simple solids or hollows that require additional machining.
- 😀 Various tools, such as saddles, blocks, rings, mandrels, and punches, are used in open die forging, made from hot work tool steels or medium carbon alloy steels.
- 😀 Impression die forging (closed die forging) uses cavities or impressions to shape metal, typically involving multiple strokes to form complex shapes.
- 😀 Flash, a thin layer of excess metal, is formed during impression die forging and is later removed during trimming after the forging is complete.
Q & A
What is forging in metalworking?
-Forging is the controlled deformation of metal into specific shapes using compressive forces. These forces are applied through tools and dies, typically driven by hammers or presses.
How is forging typically performed?
-Forging is typically performed using hammers, which deform the workpiece with high-velocity impacts, or presses, which use controlled high pressures to deform the metal.
What are the key benefits of forging in metalworking?
-Forging reduces cross-section, improves the metallurgical microstructure, provides directional grain flow, and eliminates porosity found in cast ingots, improving the mechanical performance of the material.
What is the difference between open die forging and impression die forging?
-Open die forging involves deforming the metal between flat or shaped dies without fully restricting metal flow, whereas impression die forging involves deforming the metal inside one or more cavities, creating more precise shapes.
What materials are used to withstand the conditions during forging?
-Tools and dies used in forging are typically made of hot work tool steels or medium carbon alloy steels to withstand high temperatures, abrasion, and impact.
Can complex shapes be made using open die forging?
-Although open die forging can produce fairly complex shapes, most forgings are relatively simple solids or hollows that require significant machining to achieve the final shape.
What is the purpose of flash in impression die forging?
-Flash is the thin layer of metal that flows out between the dies at the parting plane during forging. It helps increase pressure within the impression, assisting metal flow and ensuring the details of the forged part are formed properly.
How does impression die forging differ from simple shaping techniques?
-Impression die forging uses multiple press strokes with dies having several impressions for pre-forming and finish forging, while simple shaping techniques may only involve a single press stroke for less complex shapes.
What is the role of preform forming operations in impression die forging?
-Preform forming operations, such as edging, blocking, and finish forging, refine the shape of the workpiece before the final forging operation to ensure the desired dimensions and features are achieved.
What is the size range of parts that can be made using open die forging?
-Open die forging can create parts ranging from a few centimeters to 30 meters in length, and they can weigh from a few kilograms up to several hundred thousand kilograms.
Outlines
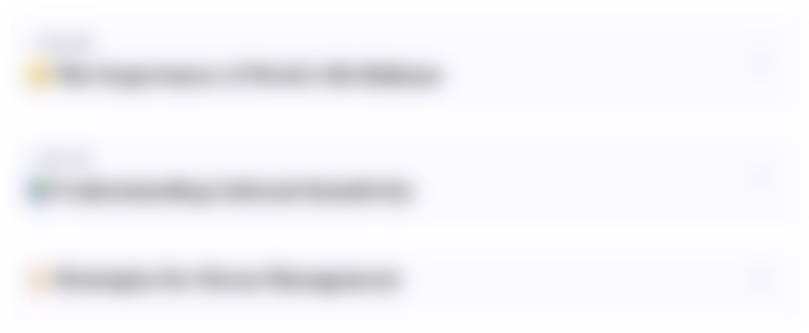
This section is available to paid users only. Please upgrade to access this part.
Upgrade NowMindmap
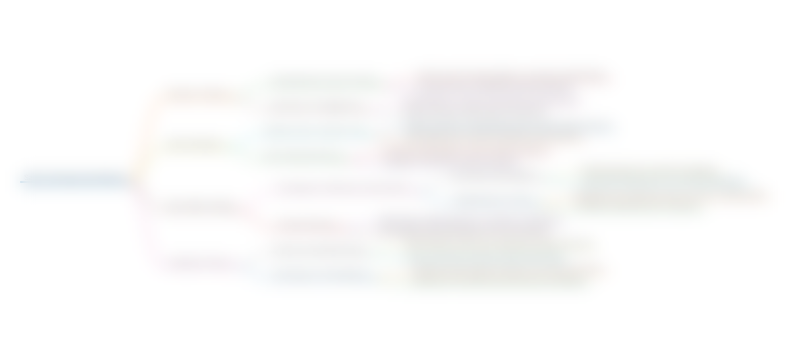
This section is available to paid users only. Please upgrade to access this part.
Upgrade NowKeywords
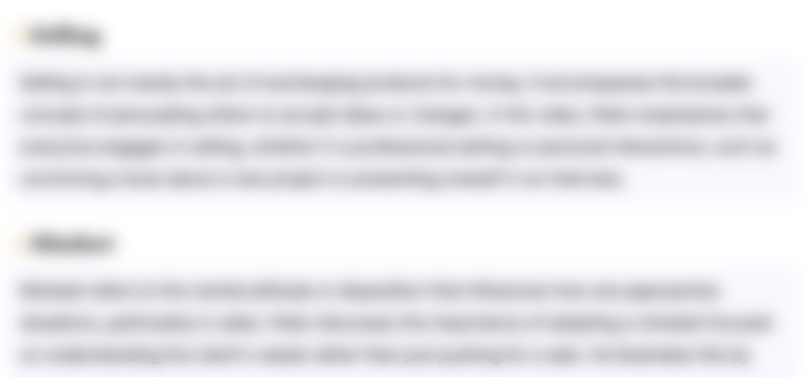
This section is available to paid users only. Please upgrade to access this part.
Upgrade NowHighlights
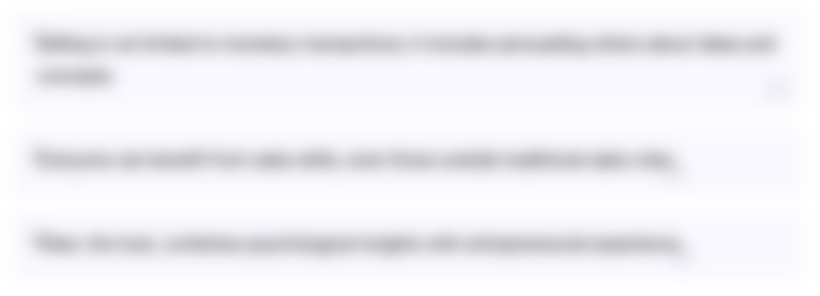
This section is available to paid users only. Please upgrade to access this part.
Upgrade NowTranscripts
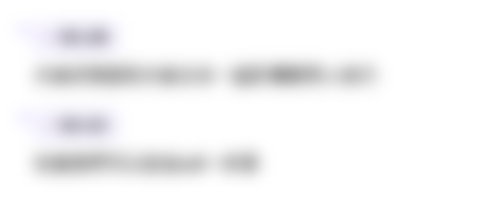
This section is available to paid users only. Please upgrade to access this part.
Upgrade NowBrowse More Related Video
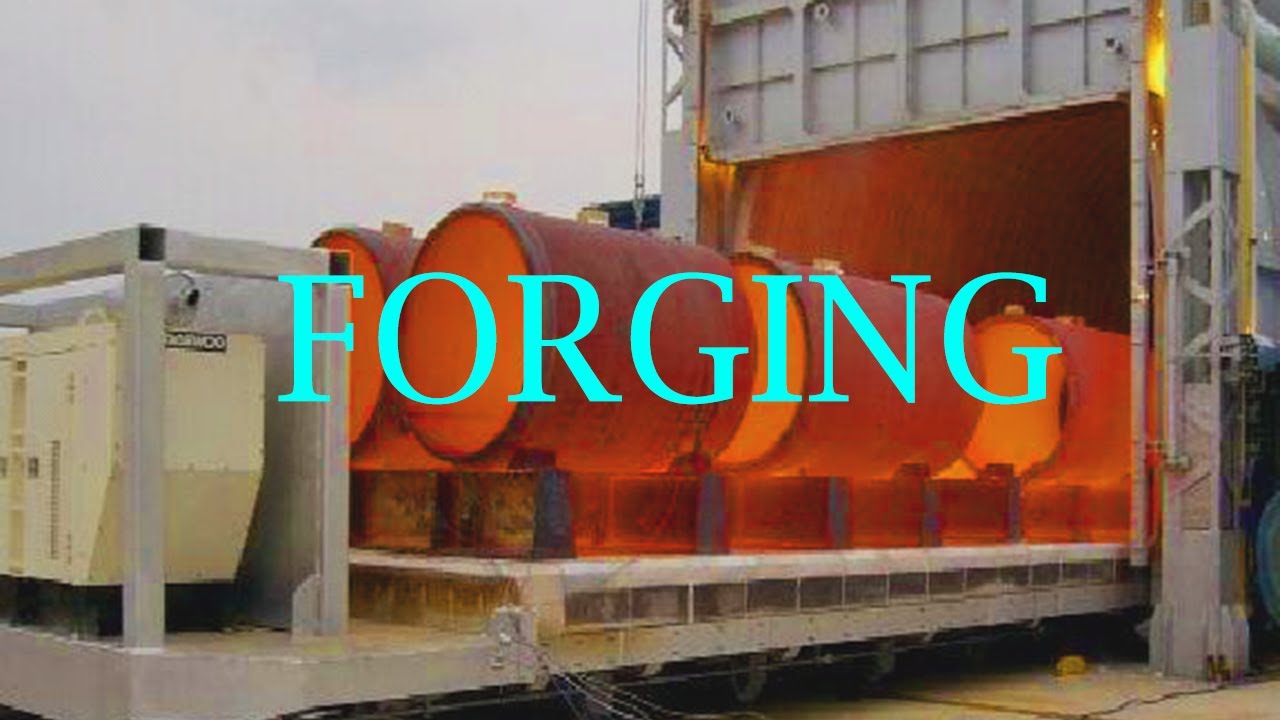
Teknik Pembentukan Logam (Forging)
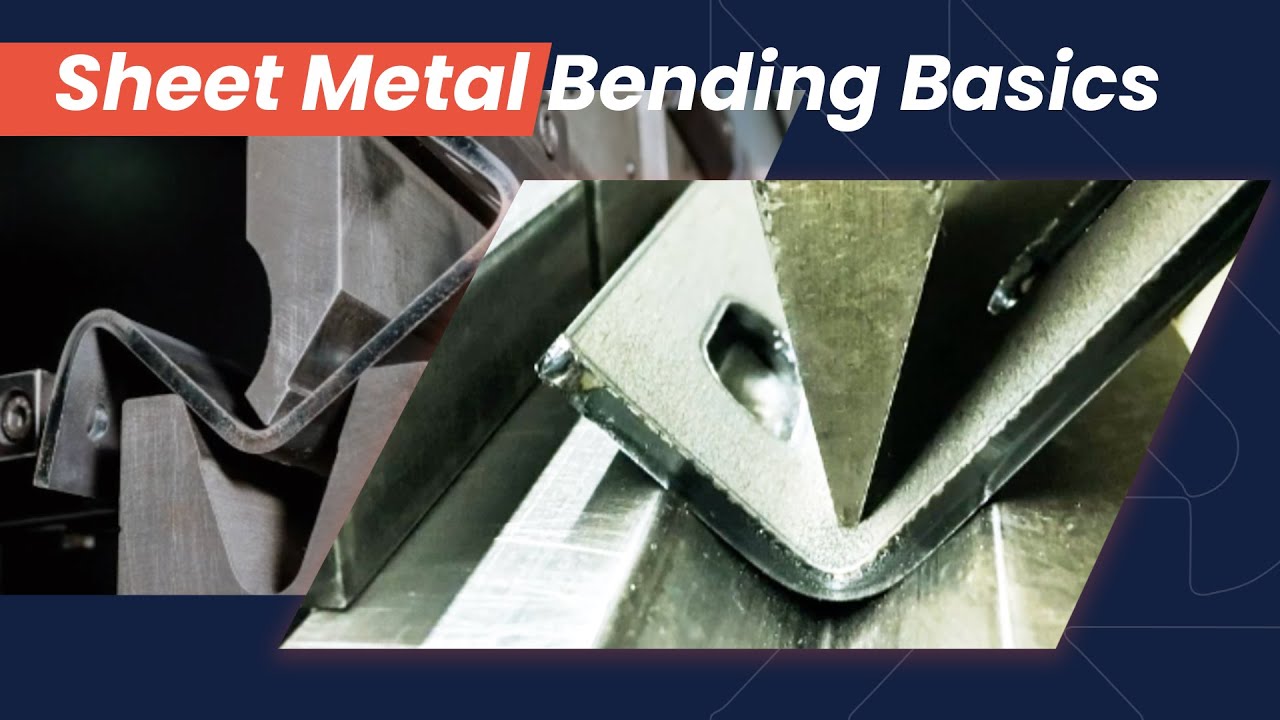
Sheet Metal Bending: Basics, Allowances, and Tips for Best Results
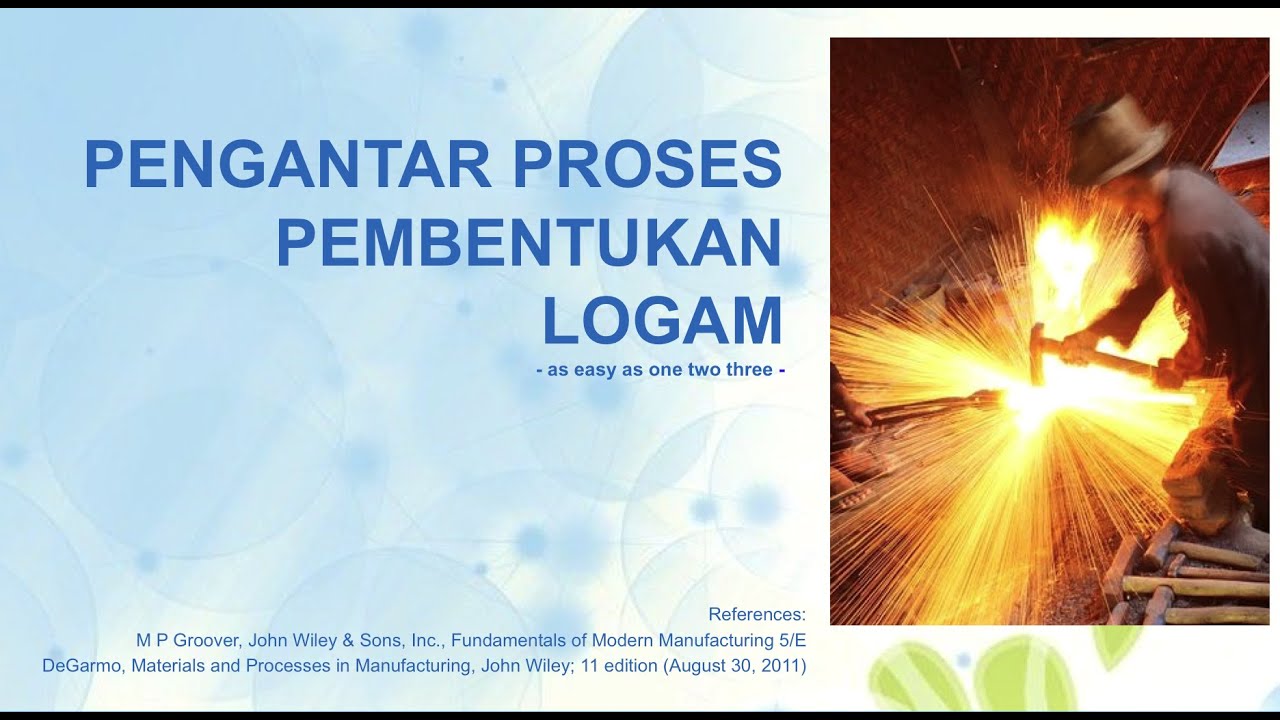
Proses Manufaktur - Pengantar Proses Pembentukan Logam - Intro to Metal Forming #BangDosen

Open die forging

Deformation Processes 1 Fundamental

Telecurso 2000 - Processos de Fabricação - 09 Casa de ferreiro, espeto de aço
5.0 / 5 (0 votes)