Telecurso 2000 - Processos de Fabricação - 09 Casa de ferreiro, espeto de aço
Summary
TLDRIn this educational video on forging processes, viewers explore the art of shaping metal through forging, both by hammering and pressing. The script introduces the different types of forging, including open and closed die forging, and highlights the importance of matrices in shaping metal. The video also delves into common defects in forged products, such as cracks and cold drops. Through detailed explanations and illustrations, the content emphasizes how forging is essential for producing high-strength parts like shafts, turbines, and large rings. Viewers also learn about the significance of temperature control and the tools involved in forging processes.
Takeaways
- 😀 Forging is a mechanical forming process that deforms material through hammering or pressing.
- 😀 The forging process is used to produce products or semi-finished parts with high mechanical resistance.
- 😀 Forging can be done through hammering, which uses rapid, successive blows, or pressing, which applies gradual pressure.
- 😀 The forging process can be done hot (above recrystallization temperature) to ensure material deformability.
- 😀 Modern forging uses machines and molds (matrices) to produce large quantities of parts, replacing traditional tools like anvils and hammers.
- 😀 A matrix (mold) is used to shape the metal during forging and can be open or closed.
- 😀 Forging by hammering results in deformation primarily in the outer layers of the material, while pressing ensures more uniform deformation in deeper layers.
- 😀 Pressing uses mechanical or hydraulic presses, which can apply substantial force ranging from 100 tons to 50,000 tons, depending on the equipment.
- 😀 Materials, including non-ferrous metals, can also be forged cold, but this is more common with specific types of materials.
- 😀 Common defects in forged parts include incomplete metal penetration (lack of reduction), surface cracks, internal cracks, and issues with the removal of excess material (rebarba).
Q & A
What is the process of forging?
-Forging is a mechanical forming process that deforms material through hammering or pressing. It is used to produce products or semi-finished parts with high mechanical strength.
What are the main types of forging?
-The two main types of forging are forging by hammering and forging by pressing. Hammering involves applying rapid, successive blows to the metal, while pressing uses gradual force applied at a lower speed.
How is forging by hammering different from forging by pressing?
-In forging by hammering, the metal undergoes rapid and successive blows, with the pressure decreasing as the metal deforms. This method mainly affects the outer layers of the material. In contrast, forging by pressing applies gradual compression, affecting deeper layers of the material and providing more uniform deformation.
What is the role of a die in forging?
-A die is essential in forging, providing the final shape of the piece. It withstands high compression forces, thermal stress, and mechanical shock, and is often made from forged steel or heat-treated material.
What is the difference between open-die forging and closed-die forging?
-In open-die forging, the dies have simple shapes, and the metal is cut into a billet, heated, and then deformed by successive hammer blows. Closed-die forging involves a metal die with a cavity where the heated metal fills the mold during compression, creating more detailed shapes.
What are common materials used in forging?
-Common materials used in forging include metals like steel, aluminum, and titanium. These materials are heated and deformed to create components such as shafts, turbine blades, and rings.
What is rebar and why is it important in forging?
-Rebar is the excess material that forms around the edges of the piece during closed-die forging. It helps ensure that the die cavity is filled properly, but it must be removed after forging to avoid defects.
What are some defects that can occur in forged products?
-Common defects in forged products include lack of reduction (incomplete metal penetration), surface cracks, rebar cracks, internal cracks, cold shuts, and oxide inclusions. These defects can result from improper material handling or forging conditions.
What is the process of forging at high temperatures?
-Forging at high temperatures involves heating the metal above its recrystallization temperature, typically using furnaces or induction heating. This process improves the material's malleability and reduces the force needed for deformation.
What are the stages of forging in closed-die processes?
-The stages of closed-die forging include cutting the metal to the required size (blanking), heating the metal, performing intermediate forging to shape the material, and then completing the final shaping in the die. Afterward, the piece undergoes heat treatment to remove stress and improve mechanical properties.
Outlines
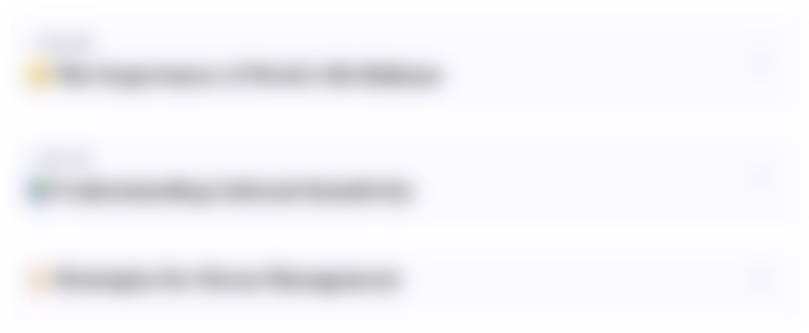
This section is available to paid users only. Please upgrade to access this part.
Upgrade NowMindmap
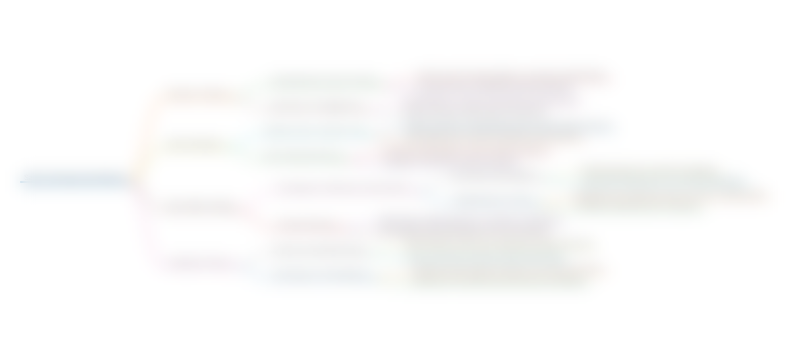
This section is available to paid users only. Please upgrade to access this part.
Upgrade NowKeywords
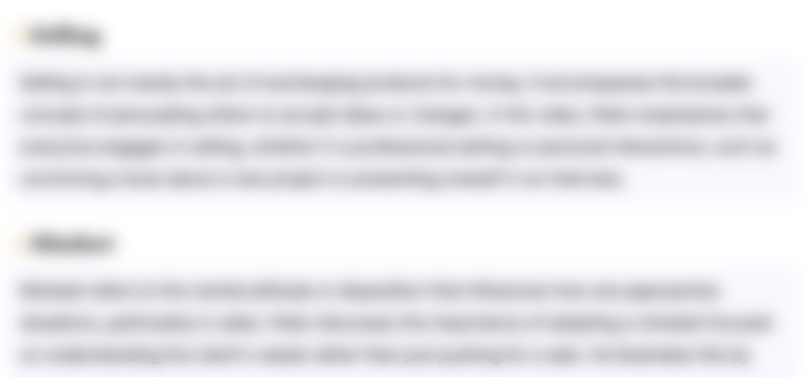
This section is available to paid users only. Please upgrade to access this part.
Upgrade NowHighlights
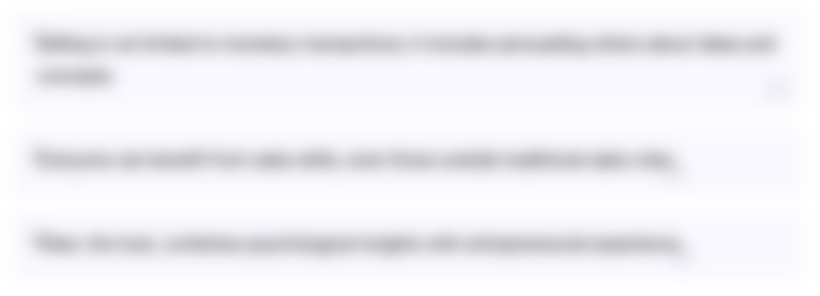
This section is available to paid users only. Please upgrade to access this part.
Upgrade NowTranscripts
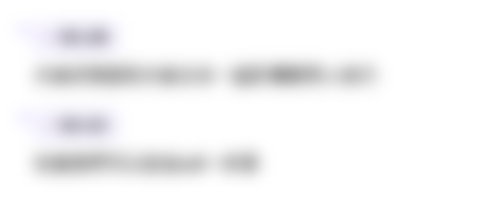
This section is available to paid users only. Please upgrade to access this part.
Upgrade NowBrowse More Related Video
5.0 / 5 (0 votes)