Panel Discussion: The Acceleration of Digitization in Manufacturing
Summary
TLDRIn this panel discussion, industry experts delve into the accelerating digitization of manufacturing. They explore innovations like digital twins, software-defined automation, and how technologies such as AI, IoT, and 3D printing are transforming the manufacturing landscape. Speakers discuss the challenges and opportunities in this digital evolution, emphasizing the importance of empowering engineers and workers with flexible, cloud-based tools. The conversation also highlights the shift towards self-service platforms and the human element in driving meaningful change, illustrating how continuous improvement and innovation are key to overcoming manufacturing challenges.
Takeaways
- ๐ The role of the Chief Storyteller at GE involves exploring innovative projects, particularly focusing on digitization and how AI and digital technologies are transforming the industry.
- ๐ Historical figures, such as Court Vaget and Ronald Reagan, worked as GE Storytellers, highlighting GE's longstanding history of storytelling within the company.
- ๐ The digital twin technology is transforming manufacturing by allowing the creation of virtual models of machines, production lines, and even entire industries, providing insights for optimization and maintenance.
- ๐ Software-defined automation focuses on creating a digital twin not just of physical machines, but of how they are designed to behave, helping to streamline and optimize industrial control processes.
- ๐ The shortage of skilled manufacturing workers is a significant issue, and tools like software-defined automation aim to bridge the gap by empowering engineers and developers with better resources and technologies.
- ๐ In manufacturing, the introduction of digital tools like Tulip has empowered employees at all levels, allowing them to take charge of their work processes and make continuous improvements from the bottom up.
- ๐ The integration of digital technologies and lean management practices has become crucial for adapting to rapid changes in demand and improving operational efficiency across manufacturing sectors.
- ๐ 3D printing is being applied to real-world problems, such as the creation of large-scale components for wind turbines, solving logistical challenges by printing structures that can't easily be transported.
- ๐ Digitization in manufacturing often involves a significant amount of manual work to implement and refine, with workers being the primary source of knowledge on what needs to be optimized and improved.
- ๐ Automation engineers, especially in Europe, are embracing cloud-based solutions that simplify their work by storing code and improving collaboration, making it easier to access and modify control systems.
- ๐ Real-time platforms that adapt to various types of manufacturing operations are key to scaling digital transformation, with companies like Stanley Black & Decker utilizing flexible platforms like Tulip to empower workers and drive innovation.
Q & A
What is the role of a Chief Storyteller at GE?
-The Chief Storyteller at GE is responsible for exploring interesting projects across the company, writing about how digital technologies like software, AI, and digitization are transforming industries. The role combines engineering expertise with a background in journalism to communicate these advancements.
How does GE's legacy relate to digitization in manufacturing?
-GE's legacy includes figures like court vaget and Ronald Reagan, who were early storytellers for the company. The company has been at the forefront of technological advancements, including the development of digital twins and AI-powered solutions that have evolved from early automation work in the 20th century.
What is a digital twin in the context of manufacturing?
-A digital twin is a virtual representation of a physical machine, system, or process. It allows manufacturers to monitor and optimize performance remotely, identifying malfunctions or inefficiencies before they happen. This technology extends to entire production lines or even entire industries like airlines and hospitals.
How does Software Defined Automation contribute to digital transformation in factories?
-Software Defined Automation focuses on virtualizing factory processes by treating industrial control systems as compute instances, much like cloud-based software. This approach helps optimize the behavior of machines, reduces manual interventions, and allows for real-time control and adjustments in the factory environment.
What challenges exist in the industrial control system market, and how does Software Defined Automation address them?
-A key challenge is the reliance on proprietary hardware, leading to long lead times and inflexibility in factory setups. Software Defined Automation addresses this by decoupling hardware from software, allowing factories to rapidly adjust their control systems and reduce reliance on slow, costly hardware updates.
What is the significance of the concept of 'VUCA' in manufacturing, as mentioned by Chris Denning?
-'VUCA' stands for Volatility, Uncertainty, Complexity, and Ambiguity. Chris Denning highlighted it as a key framework for understanding the continuous changes in manufacturing, particularly how companies like Stanley Black & Decker adapt to these challenges through innovation, lean manufacturing, and digitization.
How does Stanley Black & Decker integrate digitization into its manufacturing processes?
-Stanley Black & Decker integrates digitization through platforms like Tulip, which empower workers at all levels of the manufacturing process. These tools allow employees to adapt to changes quickly, implement continuous improvements, and enhance decision-making capabilities on the factory floor.
What is the importance of bottom-up innovation in manufacturing, according to the panelists?
-Bottom-up innovation is crucial because it empowers workers at the operational level to identify problems and suggest solutions. This approach leads to more meaningful and practical improvements, as workers are directly involved in the process and understand the intricacies of the systems they are working with.
How does the move to cloud-based control systems impact industrial engineers?
-Cloud-based control systems alleviate the burden on industrial engineers by simplifying the storage and management of control code. It reduces the reliance on physical storage methods like USB drives and streamlines access to critical information, making it easier to implement changes and updates remotely.
What role does 3D printing play in the future of manufacturing, especially in industries like wind turbine production?
-3D printing is playing a transformative role by allowing for the production of complex components that would otherwise be difficult or expensive to manufacture. For example, GE uses 3D printing to create components for wind turbines, including concrete bases for towers, addressing logistical challenges in transporting large parts.
Outlines
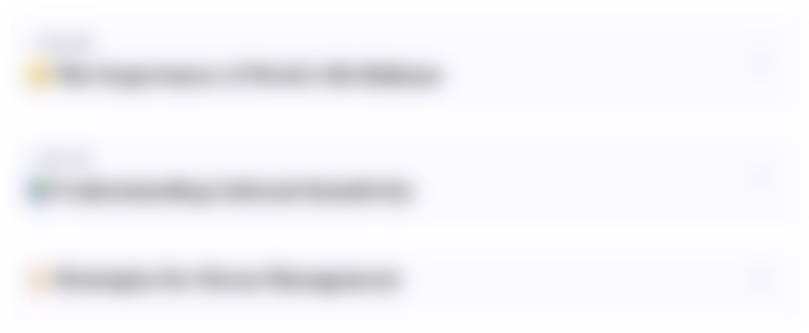
This section is available to paid users only. Please upgrade to access this part.
Upgrade NowMindmap
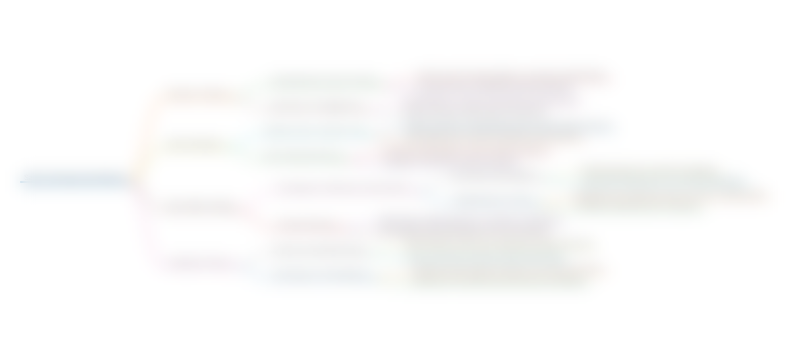
This section is available to paid users only. Please upgrade to access this part.
Upgrade NowKeywords
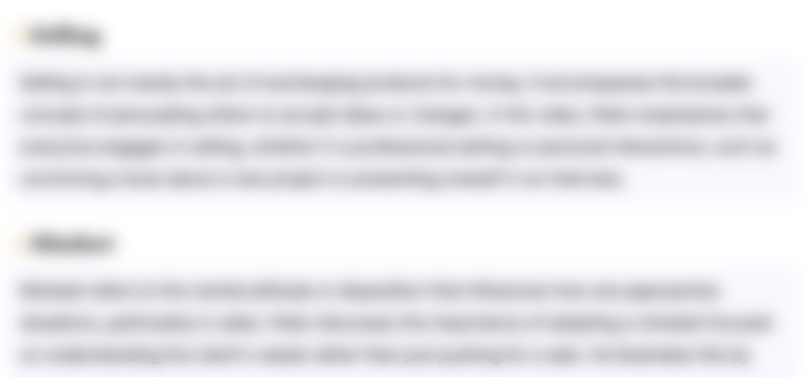
This section is available to paid users only. Please upgrade to access this part.
Upgrade NowHighlights
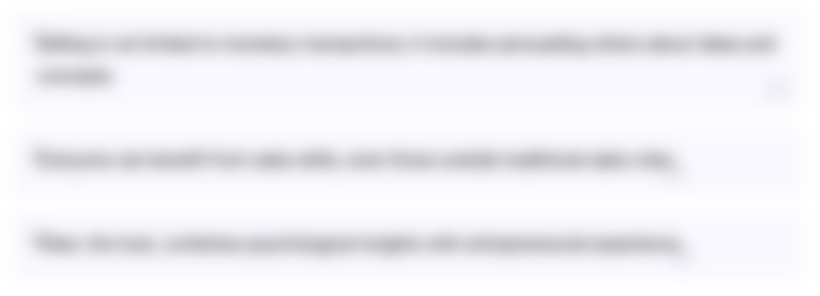
This section is available to paid users only. Please upgrade to access this part.
Upgrade NowTranscripts
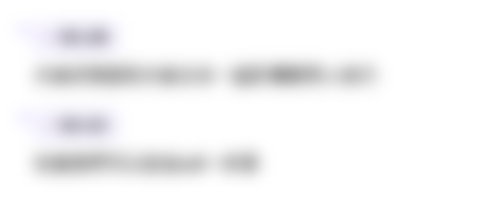
This section is available to paid users only. Please upgrade to access this part.
Upgrade Now5.0 / 5 (0 votes)