full process of rotogravure cylinder production by Janoschka
Summary
TLDRThe video provides an in-depth look at the production workflow of Roto Gravure printing and embossing, focusing on the advanced technologies involved, such as electromechanical engraving, laser engraving, etching, and embossing. It explains the processes used to create high-quality printing cylinders, including electromechanical engraving for precise ink transfer, laser technology for soft vignettes, and etching for fine details. The video highlights Yanoka’s innovation in material handling, from steel and copper coatings to the final chrome plating. Emphasizing precision and customer-focused development, it illustrates how these methods ensure excellent print quality and efficiency in packaging, particularly in sectors like tobacco and luxury packaging.
Takeaways
- 😀 Roto gravure cylinders are built on steel bases, but innovations are being developed to reduce weight and improve handling.
- 😀 The copper layer on the cylinder base is applied through electroplating, forming the surface for engraving, etching, or embossing.
- 😀 RAR printing requires one cylinder per color, meaning four cylinders are needed for a full-color design.
- 😀 Electromechanical engraving ensures high-quality printing results on various substrates, using a diamond stylus to engrave cells into the copper surface.
- 😀 Laser engraving, developed in the 1990s, utilizes a zinc layer on top of the copper coating for high-resolution image reproduction and is ideal for soft vignettes and small fonts.
- 😀 Etching, a conventional process in rotary printing, uses a laser to remove etching resist, followed by chemical etching to reproduce the design on copper.
- 😀 Embossing technology creates three-dimensional features on printed materials, particularly in the tobacco and packaging industries.
- 😀 Two embossing rollers (male and female molds) are used to create detailed designs, ensuring precise texture and print quality.
- 😀 The chrome plating process protects the copper engraving from tarnishing and wear, enhancing the durability of the cylinder.
- 😀 Final quality control includes proof printing to check the accuracy of the engraved design and its printing behavior before dispatching the cylinders.
Q & A
What is the primary material used to create the base of a Roto gravier cylinder?
-The primary material used for the base of a Roto gravier cylinder is steel. However, ongoing market demands are prompting developments towards lighter and more innovative solutions.
How is the copper coating applied to the steel base of a Roto gravier cylinder?
-The copper coating is applied to the steel base through an electroplating process.
What are the main engraving techniques used in Roto gravier printing?
-The main engraving techniques used in Roto gravier printing include electromechanical engraving, direct laser engraving, etching, and embossing.
How does electromechanical engraving work in the production of Roto gravier cylinders?
-Electromechanical engraving works by using electromechanical pulses to drive a diamond stylus that engraves cells into the copper surface. The size and depth of these cells determine the ink volume to be transferred to the printing material.
What is the purpose of the laser engraving technique in Roto gravier printing?
-Laser engraving is ideal for reproducing soft vignettes and small fonts on substrates like aluminum. It uses a laser beam to create the image on the surface without physically touching the cylinder.
What is the main advantage of using the direct laser engraving system?
-The direct laser engraving system offers high-resolution image reproduction, sharp contours, and excellent half tones, making it ideal for printing detailed motifs with perfect accuracy.
How does the etching process work in Roto gravier printing?
-In the etching process, an etching resist is applied to the copper cylinder to protect it from feric chloride. The resist is then removed by laser, and the exposed copper is etched using a chemical solution, creating precise cells for engraving.
What is the role of the chrome plating in the Roto gravier cylinder production process?
-Chrome plating is applied as a final step in the production of Roto gravier cylinders. It protects the copper and engraving from tarnishing and wear, ensuring the durability and longevity of the cylinders.
What is the purpose of embossing technology in the production of Roto gravier cylinders?
-Embossing technology creates a three-dimensional tactile feature on the finished product. It is commonly used in print finishing, especially for packaging such as tobacco and cardboard, and involves the use of embossing rollers to form the design.
How is quality control managed in the production of Roto gravier cylinders?
-Quality control is handled through a proof print department where cylinders are tested with customer ink and substrate. Skilled experts perform final quality checks to ensure the manufactured cylinders meet the customer’s specifications before dispatch.
Outlines
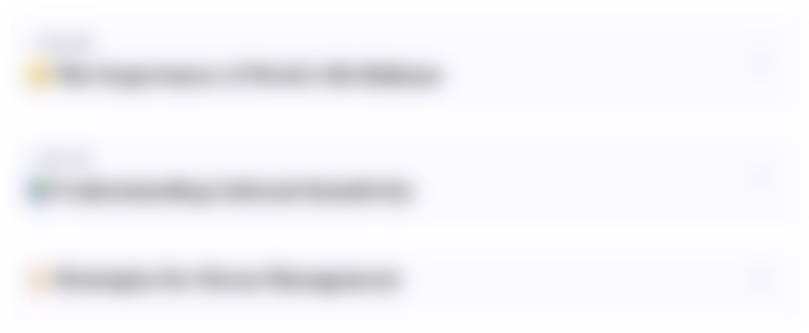
This section is available to paid users only. Please upgrade to access this part.
Upgrade NowMindmap
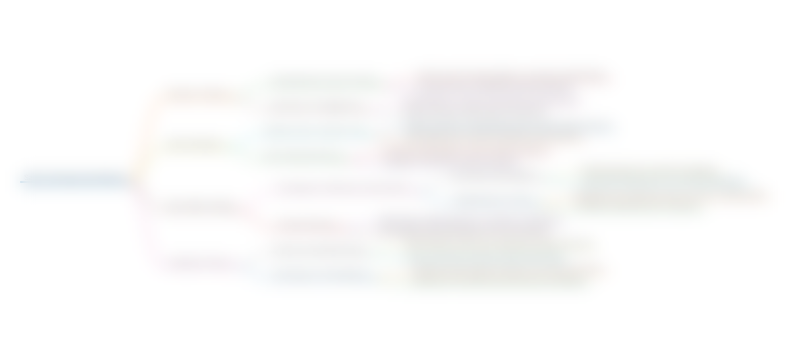
This section is available to paid users only. Please upgrade to access this part.
Upgrade NowKeywords
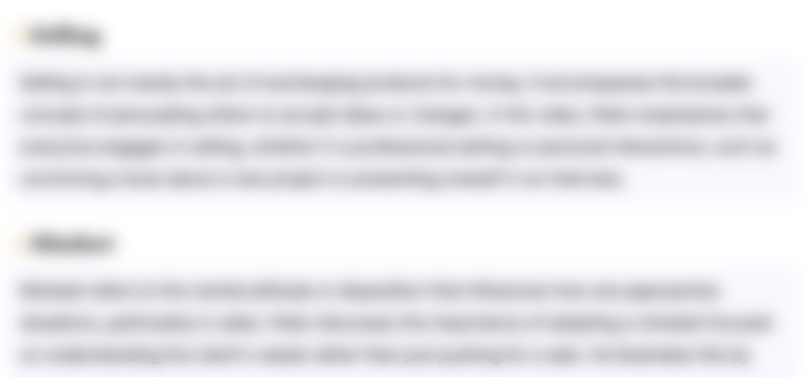
This section is available to paid users only. Please upgrade to access this part.
Upgrade NowHighlights
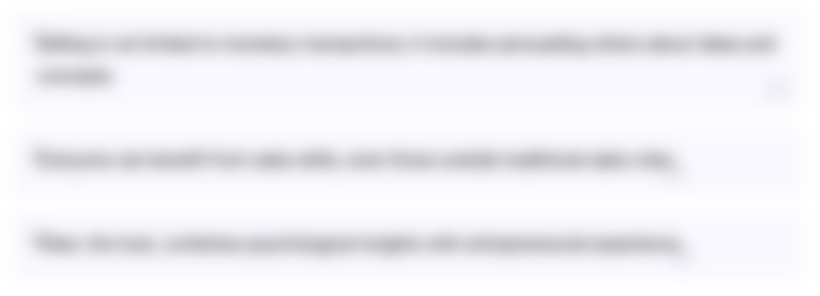
This section is available to paid users only. Please upgrade to access this part.
Upgrade NowTranscripts
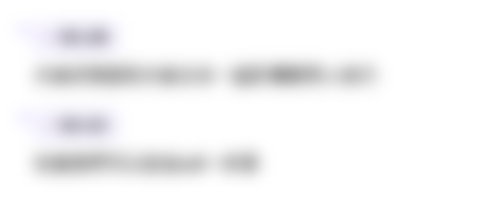
This section is available to paid users only. Please upgrade to access this part.
Upgrade NowBrowse More Related Video
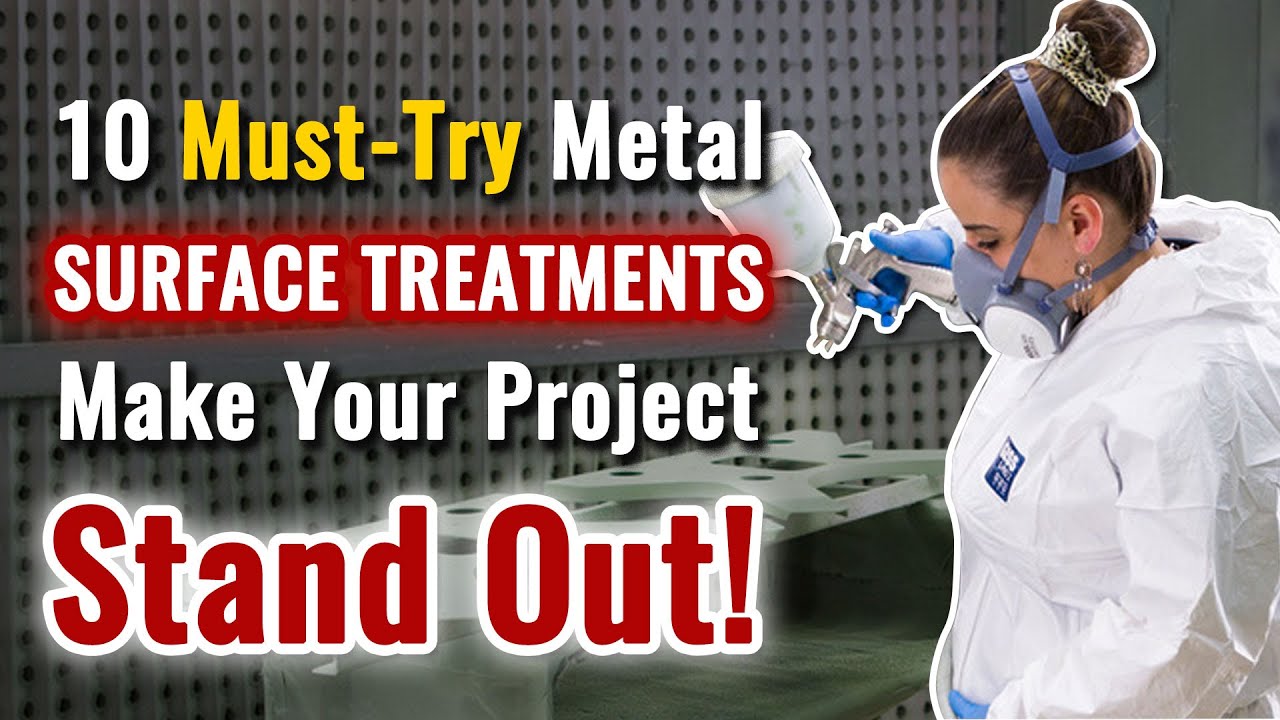
10 Metal Surface Treatment Techniques to Make Your Products More Cost-Effective!
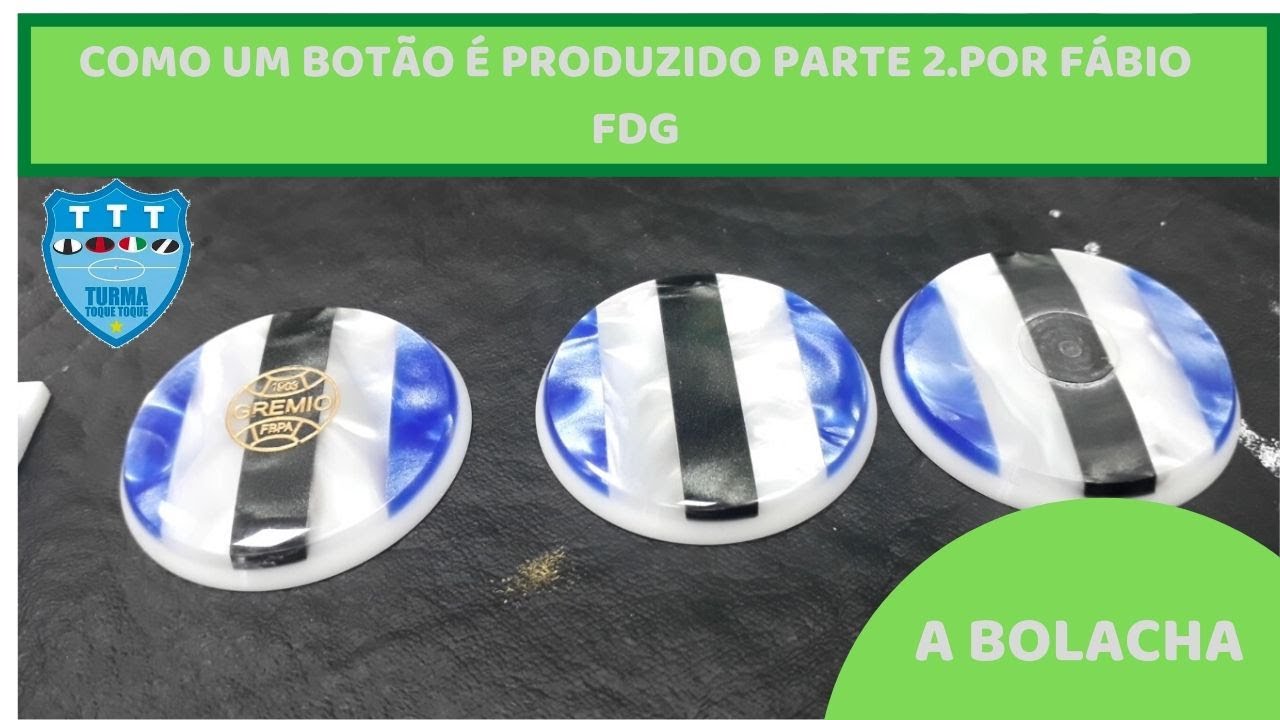
Futebol de Botão - Como um botão é produzido por Fábio FDG - parte 2

Product Review - Creality Falcon 2 Laser Engraver and Cutter
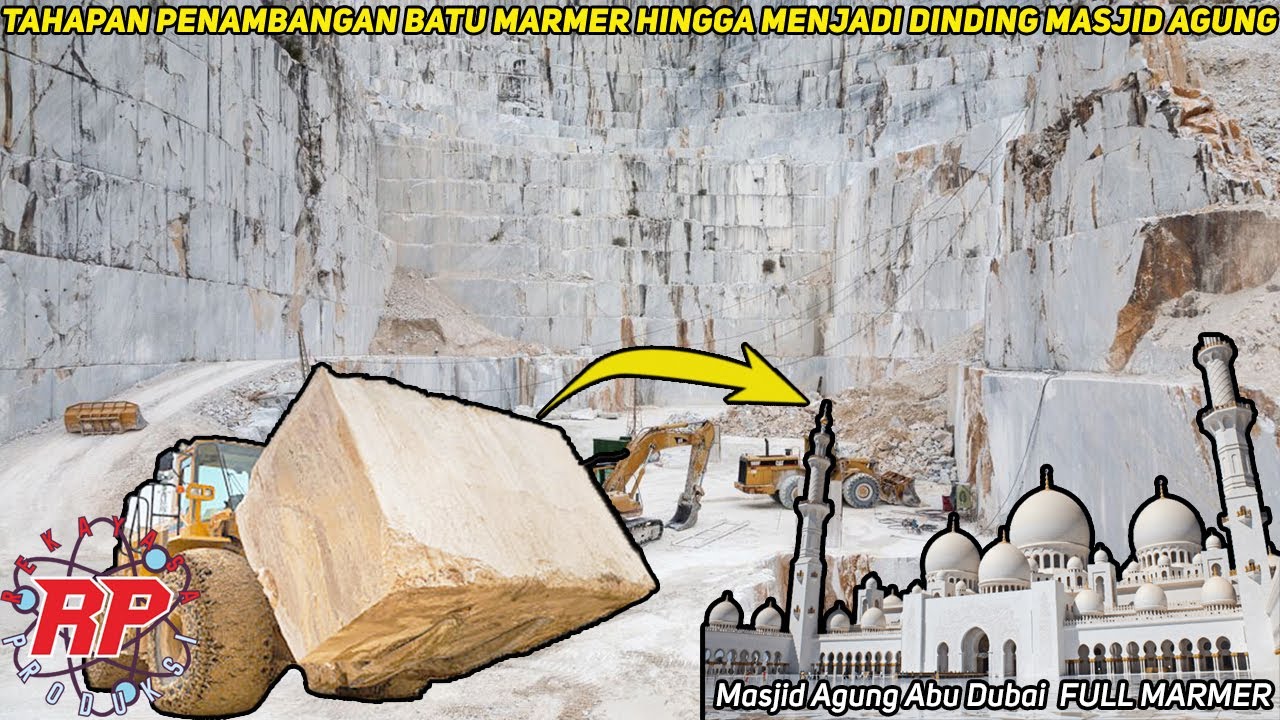
Documentary Of Marble Quarries Based In Greece | Extraction And Processing Marble

12 Packaging Design Terms You Should Know as a Graphic Designer
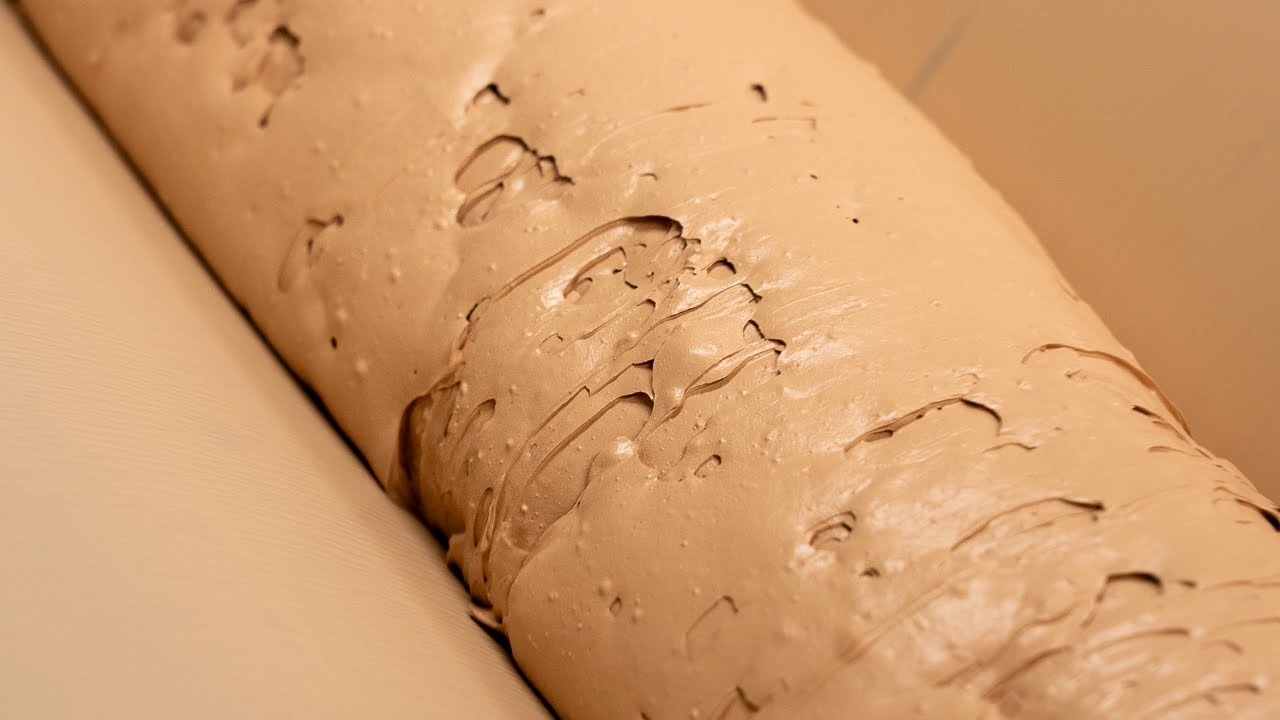
Like Ice Cream! Process of Making Makeup Cushion Foundation. Cosmetic Factory in Korea
5.0 / 5 (0 votes)