Explaining the Cost of Quality, the 4 Cost Categories and Juran’s Quality Cost Curve
Summary
TLDRIn this video, Andy Robertson from CQE Academy explains the **Cost of Quality** (CoQ), a concept crucial for businesses aiming to optimize quality management. The video covers the four key categories of CoQ: Prevention, Appraisal, Internal Failures, and External Failures, highlighting how each contributes to both good and poor quality costs. Robertson emphasizes the importance of prevention in minimizing costs and introduces Dr. Juran’s Quality Cost Curve, demonstrating that the lowest cost of quality occurs when products achieve 100% conformity. The video offers valuable insights for quality engineers looking to understand and manage quality-related costs effectively.
Takeaways
- 😀 Prevention costs are essential for avoiding defects and non-conformances before they occur.
- 😀 Appraisal costs involve activities such as testing and inspections to ensure product conformity.
- 😀 Internal failure costs arise when defects are detected before shipment to the customer (e.g., scrap, rework).
- 😀 External failure costs are the most expensive and occur when defects are discovered after shipment (e.g., warranty claims, recalls).
- 😀 The cost of quality is composed of both the cost of good quality (prevention and appraisal) and the cost of poor quality (failures).
- 😀 Duran’s quality cost curve shows that the lowest total cost of quality occurs when a product achieves 100% conformance with no defects.
- 😀 Investing in prevention and appraisal is more cost-effective in the long run than dealing with internal and external failures.
- 😀 Benjamin Franklin's quote, 'An ounce of prevention is worth a pound of cure,' emphasizes the importance of preventing quality issues rather than addressing them later.
- 😀 Activities such as design input analysis, vendor qualification, and process planning all fall into the prevention cost category.
- 😀 External failure costs, such as lost customers and reputation, are the most damaging and can result from inadequate prevention and appraisal efforts.
- 😀 The goal of quality management is to eliminate poor quality costs by ensuring that products are built conforming to requirements from the start.
Q & A
What are the four cost of quality categories introduced by Armon V. Feigenbaum?
-The four cost of quality categories are Prevention, Appraisal, Internal Failures, and External Failures.
What is the main difference between cost of good quality and cost of poor quality?
-Cost of good quality includes activities that prevent or appraise quality (Prevention and Appraisal), while cost of poor quality involves the costs associated with defects or failures (Internal Failures and External Failures).
How can you categorize a cost related to testing and auditing products?
-Testing and auditing costs fall into the Appraisal category, as they are designed to evaluate, measure, or inspect products to ensure conformity to requirements.
Why does Benjamin Franklin's quote, 'An ounce of prevention is worth a pound of cure,' apply to quality management?
-The quote emphasizes the importance of preventing quality issues before they occur, rather than spending resources to fix problems after they arise, which aligns with the focus on Prevention costs in quality management.
What are some examples of Prevention costs in a manufacturing environment?
-Prevention costs include activities like product design, supplier quality management, risk management tools (e.g., DFMEA), employee training, equipment maintenance, and quality improvement projects.
What is the key difference between Prevention and Appraisal costs?
-Prevention costs focus on activities that prevent defects from occurring, while Appraisal costs focus on activities that inspect, measure, and evaluate products to ensure they meet quality standards.
What types of costs are associated with Internal Failures?
-Internal failure costs include expenses like scrap, rework, re-inspection, root cause investigations, excess inventory, lost labor, and equipment downtime due to defects detected before shipment to the customer.
What are External Failure costs and why are they the most expensive?
-External failure costs are the costs associated with defects found after the product has been shipped to the customer. These are the most expensive due to warranty claims, repairs, lost sales, customer complaints, and reputational damage.
How does the Duran Quality Cost Curve relate to quality management?
-The Duran Quality Cost Curve illustrates the relationship between cost and quality, showing that the total cost of quality is minimized at 100% conforming products, with the lowest cost occurring when quality is highest.
What happens to the costs of poor quality as product conformity decreases?
-As product conformity decreases, the costs of poor quality, including internal and external failure costs, increase exponentially due to issues like customer dissatisfaction, warranty claims, and lost reputation.
Outlines
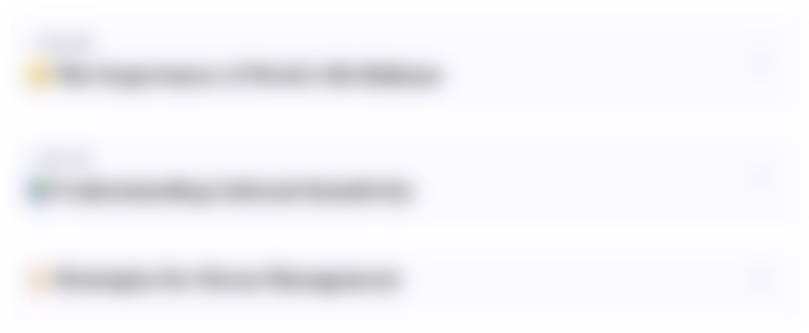
This section is available to paid users only. Please upgrade to access this part.
Upgrade NowMindmap
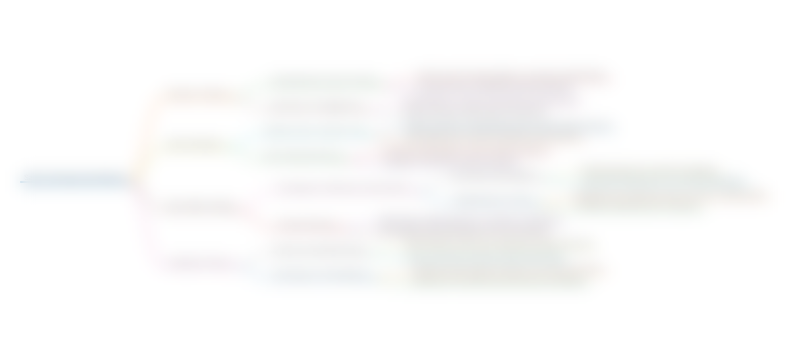
This section is available to paid users only. Please upgrade to access this part.
Upgrade NowKeywords
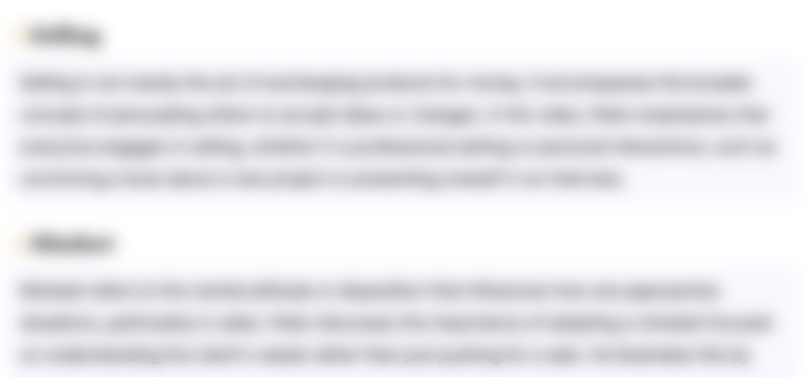
This section is available to paid users only. Please upgrade to access this part.
Upgrade NowHighlights
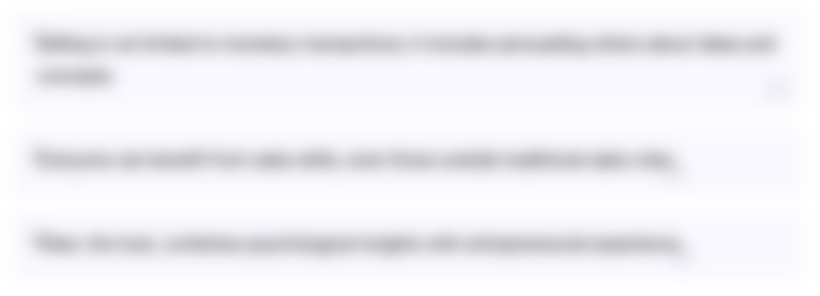
This section is available to paid users only. Please upgrade to access this part.
Upgrade NowTranscripts
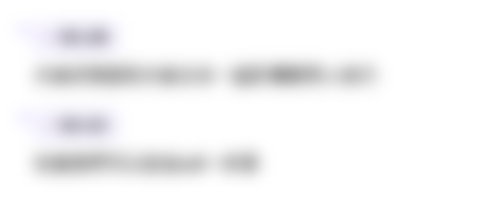
This section is available to paid users only. Please upgrade to access this part.
Upgrade NowBrowse More Related Video
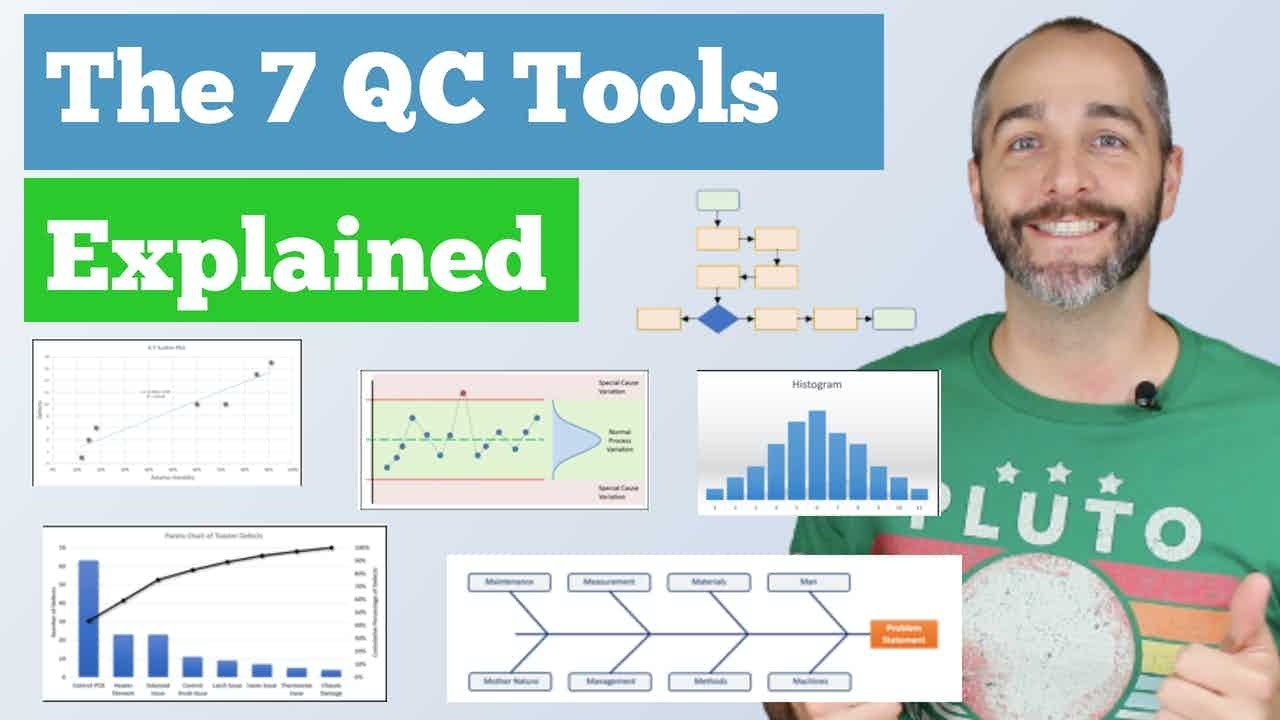
The 7 Quality Control (QC) Tools Explained with an Example!

Pengertian Biaya Kualitas
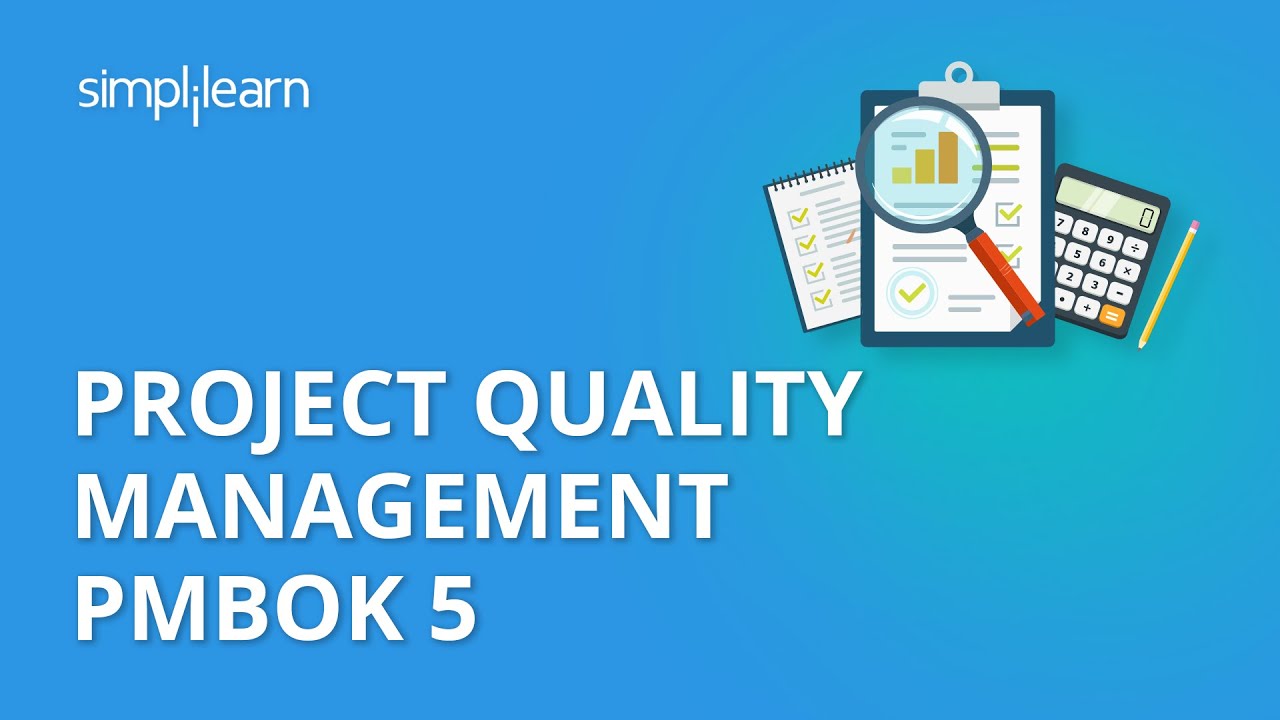
Project Quality Management PMBOK 5 | PMP® Training Videos | Project Management Tutorial |Simplilearn
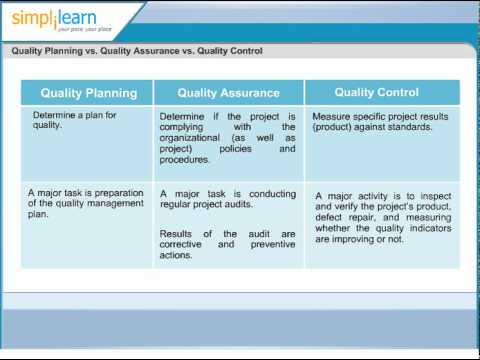
Quality Planning vs Quality Assurance vs Quality Control | Project Quality Management
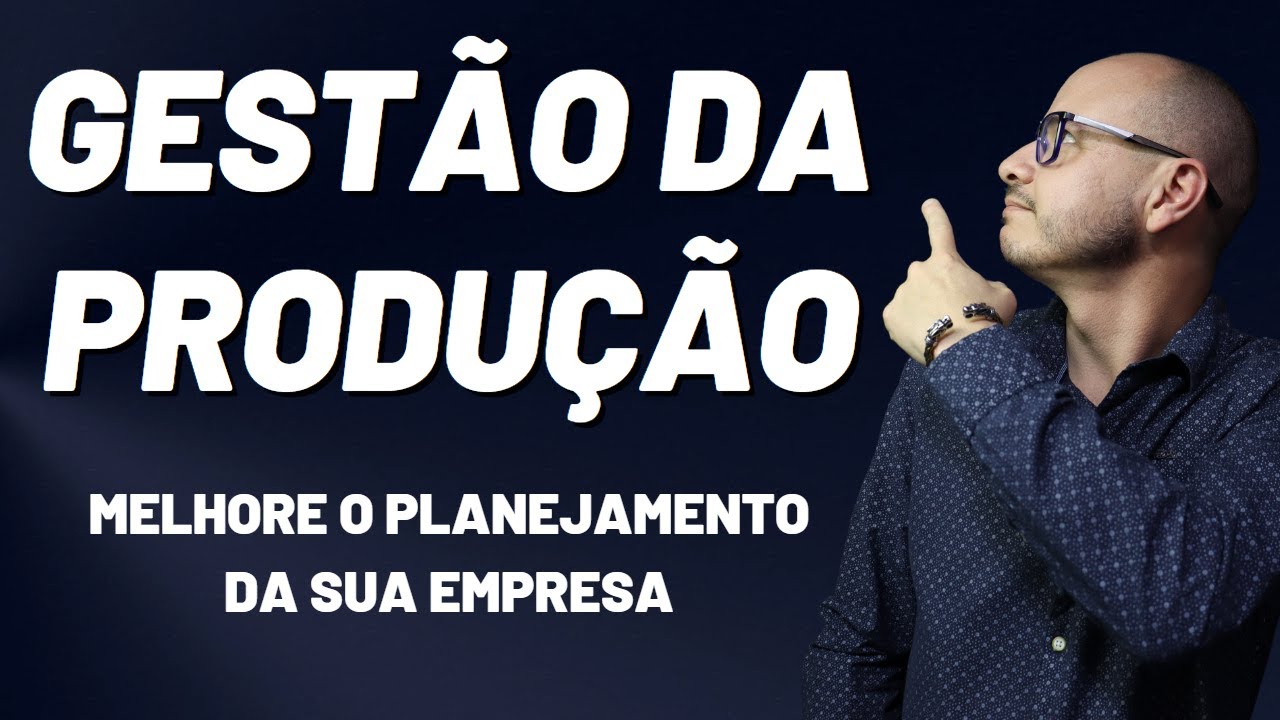
GESTÃO DA PRODUÇÃO I PROCESSOS INDUSTRIAIS I GERENCIAMENTO DA PRODUÇÃO
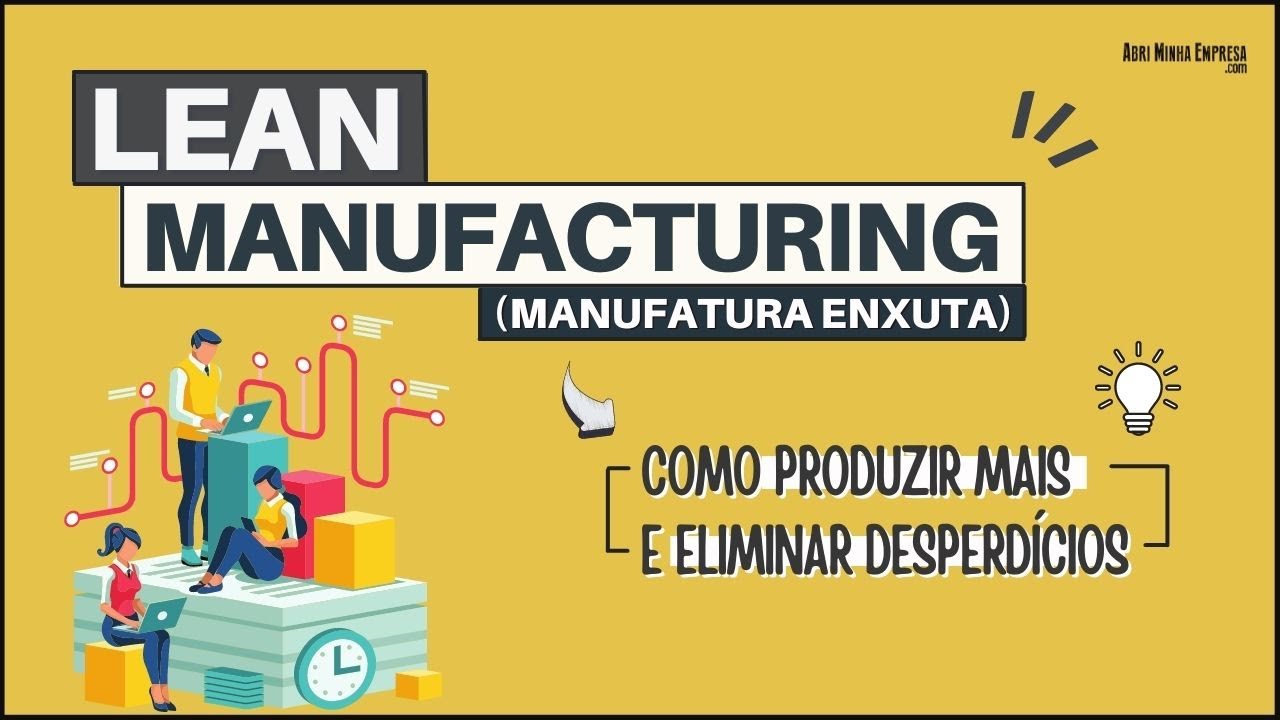
LEAN MANUFACTURING (Manufatura Enxuta) | Conheça os 8 Principais Tipos de Desperdícios
5.0 / 5 (0 votes)