Pengertian Biaya Kualitas
Summary
TLDRIn this lecture on the introduction to quality management, the speaker discusses the concept of 'cost of quality' in product and service management. The video covers the three main categories of quality costs: prevention, assessment, and failure costs. It highlights the importance of investing in quality to ensure customer satisfaction, prevent operational inefficiencies, and stay competitive in the market. The speaker also explains how improving quality can reduce operational costs and increase customer loyalty, ultimately leading to higher profits. Examples from various industries, including IT and manufacturing, are used to illustrate these concepts.
Takeaways
- 😀 Quality costs refer to the expenses incurred in managing product quality, both in improving and maintaining quality, as well as the costs resulting from poor quality.
- 😀 The importance of quality costs lies in the fact that they can account for 20-30% of the total product price, making it essential for businesses to focus on quality management.
- 😀 Failure to ensure quality can lead to poor product sales and increased competition, whereas maintaining high quality helps retain customers and eliminates the need for expensive advertising.
- 😀 Investing in quality management can lead to operational cost reductions, such as fewer revisions and reworks, because high-quality products reduce the chances of failure.
- 😀 The basic concept of quality is when a product or service meets or exceeds customer expectations, ensuring that it addresses customer needs and desires.
- 😀 There are three main categories of quality costs: prevention costs, appraisal costs, and failure costs (which can be internal or external).
- 😀 Prevention costs are incurred before the product is made, such as training, process capability improvements, and quality planning and design.
- 😀 Appraisal costs are incurred after production to assess the quality of the product, including costs for testing, inspection, and quality audits.
- 😀 Failure costs arise when the product fails to meet quality standards. Internal failure costs are related to defects found before the product reaches the customer, while external failure costs relate to defects discovered after the product has been delivered to customers.
- 😀 Internal failure costs may include rework, design changes, excess inventory storage, and the purchase of new materials to fix defects.
- 😀 External failure costs include warranty claims, product returns, customer complaints, and any costs associated with handling post-sale issues like product dissatisfaction.
Q & A
What is the definition of quality cost mentioned in the script?
-Quality cost refers to the costs incurred in addressing quality issues, both in improving quality and the costs resulting from poor quality. It includes not only the expenses for enhancing quality but also for maintaining it.
Why is quality cost an important consideration in business?
-Quality cost is significant because it can account for 20-30% of the product's price. Without good quality, products may not sell, and businesses risk losing customers and market competitiveness.
How does improving quality impact customer loyalty?
-Improving product or service quality can increase customer loyalty. Satisfied customers are more likely to recommend the product to others, reducing the need for additional advertising costs.
What are the three main categories of quality costs according to Feigenbaum?
-The three main categories of quality costs are prevention costs, appraisal costs, and failure costs (both internal and external).
What is the role of prevention costs in quality management?
-Prevention costs are incurred before the product is produced. These costs are related to planning, training, and other activities that ensure the product is of high quality from the outset.
Can you give examples of costs associated with the prevention category?
-Examples include training costs for employees, costs of process capability improvement, vendor surveys, and the costs involved in quality planning and design.
What do appraisal costs involve?
-Appraisal costs are incurred after production and include expenses related to testing, inspections, quality audits, and the purchase of testing equipment and materials.
What are the two types of failure costs discussed in the script?
-Failure costs are divided into internal failure costs and external failure costs. Internal failure occurs before the product reaches the customer, while external failure happens after the product has been delivered to the customer.
What are some examples of internal failure costs?
-Internal failure costs include expenses related to rework, design changes, excess inventory storage, and the purchase of additional materials to correct defects.
What are some examples of external failure costs?
-External failure costs include warranty claims, product returns, customer complaints handling, and expenses related to product replacements or refunds.
Outlines
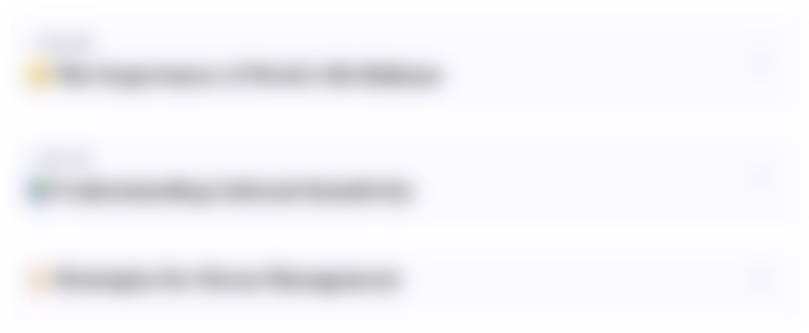
This section is available to paid users only. Please upgrade to access this part.
Upgrade NowMindmap
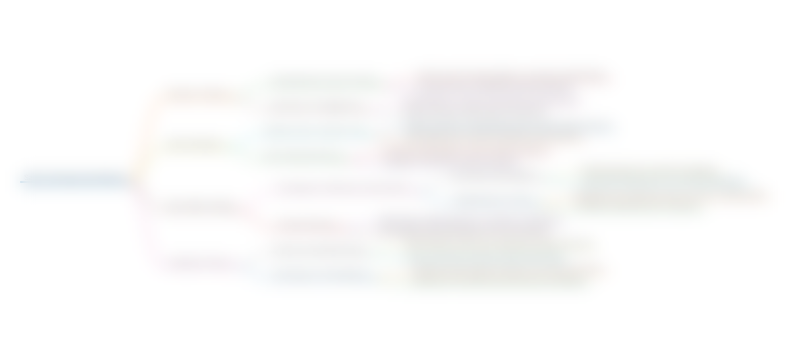
This section is available to paid users only. Please upgrade to access this part.
Upgrade NowKeywords
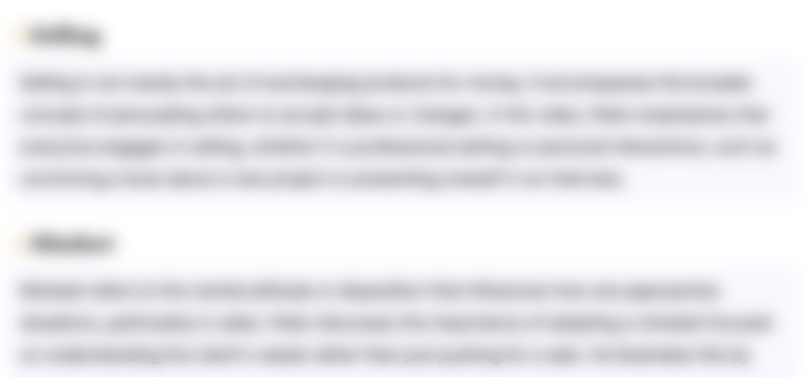
This section is available to paid users only. Please upgrade to access this part.
Upgrade NowHighlights
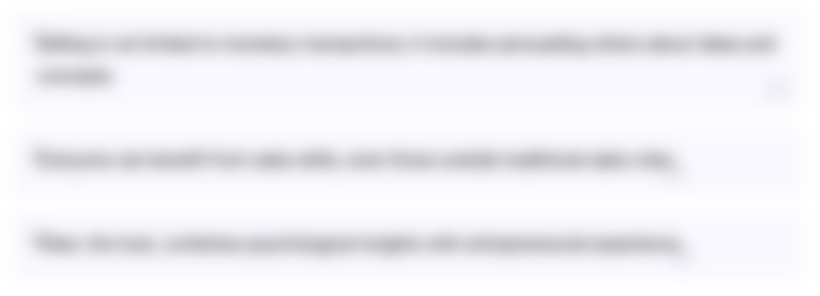
This section is available to paid users only. Please upgrade to access this part.
Upgrade NowTranscripts
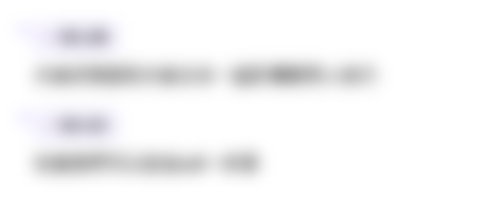
This section is available to paid users only. Please upgrade to access this part.
Upgrade Now5.0 / 5 (0 votes)