Konsep Dasar Load and Resistance Factor Design (LRFD) pada Struktur Baja | Lightboard
Summary
TLDRThis video explains the basic concepts of designing steel structures using the LRFD (Load and Resistance Factor Design) method, which is currently applied in Indonesian regulations. The method focuses on comparing loads (Q) with resistance (R) to ensure structural safety. It highlights factors like overloads due to building function changes, misestimations of loads, or construction errors. The video also covers the importance of considering various types of loads (dead, live, wind, seismic) and how to factor them in the design, adjusting strength and load factors for accuracy and safety in steel structure planning.
Takeaways
- 😀 LRFD (Load and Resistance Factor Design) is a method used for steel structure design, adopted in Indonesia based on the American code AISC 360, 2010.
- 😀 The core concept of LRFD involves comparing loads (Q) and resistance (R), both of which are assumed to be random and variable.
- 😀 Load is not always constant; it can exceed the expected value (overload), especially due to changes in building function or inaccuracies in estimation.
- 😀 Factors contributing to overload include a change in building function (e.g., converting classrooms to dormitories) and inaccurate estimations of wind loads.
- 😀 Changes in construction or structural details, such as variations in beam support conditions, can lead to overloads if not accounted for.
- 😀 Strength (resistance) can be affected by variations in material properties, such as weaker steel or poor workmanship in fabrication, reducing the overall resistance.
- 😀 LRFD requires that the applied load (Q) must not exceed the reduced resistance (R) to ensure safety.
- 😀 The design code uses a strength reduction factor (φ) to adjust the assumed resistance, accounting for the possibility of under-strength materials.
- 😀 A load factor (γ) is applied to increase the expected loads, helping to account for the possibility of overloads.
- 😀 There are various types of loads to consider in structural design, including dead loads (permanent), live loads (variable), wind loads, and seismic loads, each having different characteristics and impacts on the structure.
- 😀 The ultimate load is calculated by multiplying all loads by their respective load factors, and the final design strength is calculated by applying the strength reduction factor to the nominal strength.
- 😀 The LRFD method ensures safety by balancing load increases with resistance decreases, making the design adaptable to real-world variations and uncertainties.
Q & A
What does LRFD stand for and how is it applied in steel structure design in Indonesia?
-LRFD stands for Load and Resistance Factor Design. It is a method used in steel structure design in Indonesia that compares the load and resistance of a structure, ensuring that the load (Q) does not exceed the resistance (R). This method was adopted from the American standards, specifically AISC 360, and applied in the Indonesian SNI 17292 (2015).
Why is the concept of load and resistance treated as random phenomena in LRFD?
-In LRFD, both load (Q) and resistance (R) are treated as random phenomena because they can vary. For instance, loads may fluctuate due to changes in usage or environmental conditions, while resistance can vary based on material quality or construction methods.
What are the main reasons that can lead to overload in a structure?
-Overload can occur due to three main reasons: changes in the building's function (e.g., converting a classroom into a dormitory), inaccurate load estimation (e.g., underestimating wind load), and changes in the construction process (e.g., incorrectly assuming fixed beams when they are actually pinned).
What is the difference between overload and understrength in the context of structural design?
-Overload occurs when the actual load exceeds the design load, while understrength happens when the actual strength of the materials is less than expected. Overload could be caused by changes in function or inaccurate estimations, while understrength could result from variations in material quality or dimensions.
How does LRFD address the issue of understrength in structural materials?
-To address understrength, LRFD applies a strength reduction factor (Φ), which reduces the assumed material strength. This accounts for uncertainties such as variations in material quality or construction inaccuracies, ensuring safety even when strength is lower than expected.
What is the role of load factors in LRFD?
-Load factors in LRFD are used to increase the load values in the design to account for potential overload situations. These factors are typically greater than one, reflecting the possibility of exceeding the expected load during the life of the structure.
How do load factors and strength reduction factors work together in LRFD?
-Load factors and strength reduction factors work together in LRFD by adjusting the load and resistance values. The load factor increases the load to accommodate potential overloads, while the strength reduction factor reduces the assumed material strength to account for understrength scenarios. Together, they ensure the structure is safe under variable conditions.
What types of loads must be considered in the LRFD method for structural design?
-The LRFD method considers several types of loads: dead loads (permanent structural components), live loads (variable loads depending on usage), wind loads, seismic loads (lateral forces), and additional loads like rain. These loads are combined in the design calculations.
What is the significance of ultimate loads and how are they calculated in LRFD?
-Ultimate loads are the loads that are factored by the load factor to account for potential overload. They are calculated by multiplying the basic load values by the appropriate load factor. The ultimate load is then compared to the reduced resistance to ensure structural safety.
What are the next steps in the design process after considering the ultimate load and reduced strength?
-After calculating the ultimate load (Q × Load Factor) and the reduced strength (R × Strength Reduction Factor), the next step is to ensure that the ultimate load is less than or equal to the reduced strength. If this condition is met, the structure is considered safe. Further calculations, including assessing each structural element, are done to finalize the design.
Outlines
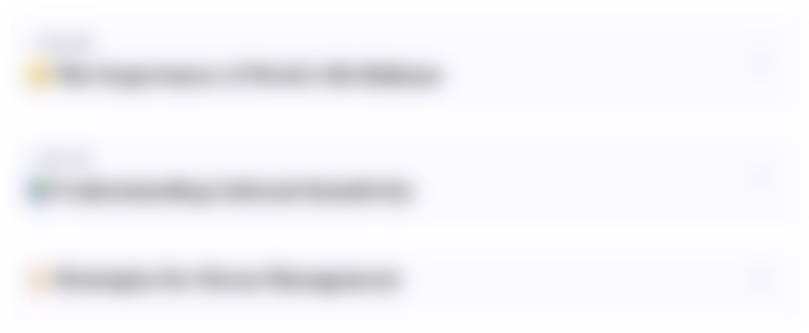
This section is available to paid users only. Please upgrade to access this part.
Upgrade NowMindmap
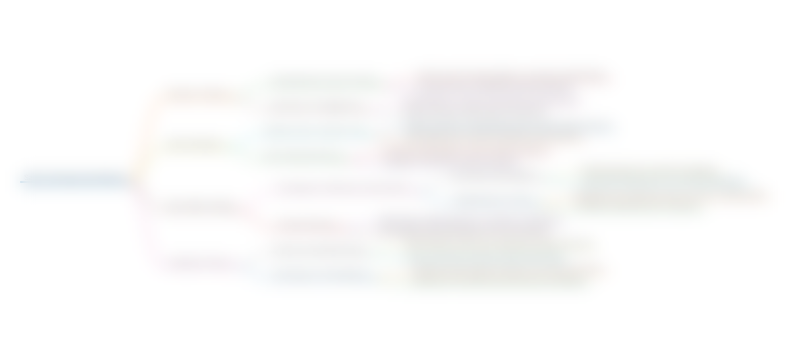
This section is available to paid users only. Please upgrade to access this part.
Upgrade NowKeywords
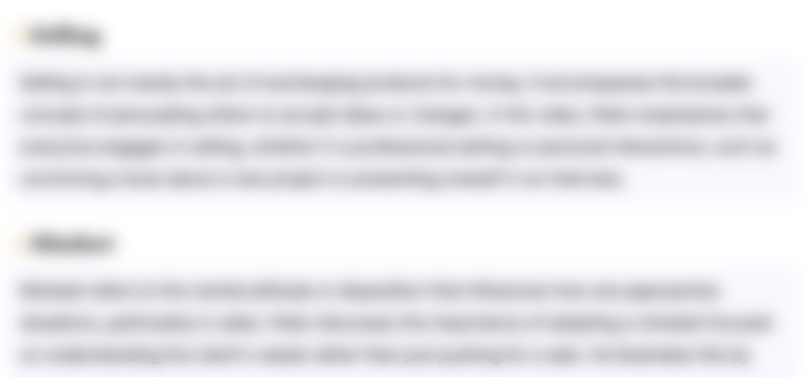
This section is available to paid users only. Please upgrade to access this part.
Upgrade NowHighlights
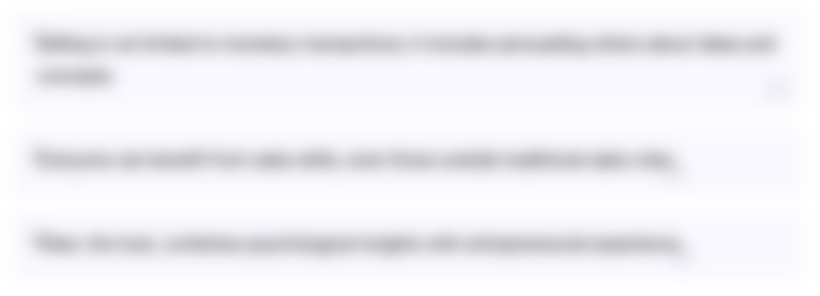
This section is available to paid users only. Please upgrade to access this part.
Upgrade NowTranscripts
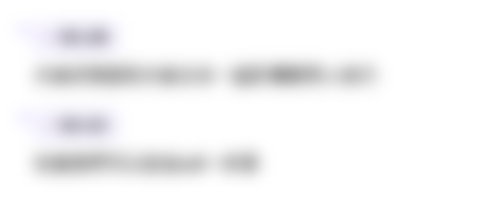
This section is available to paid users only. Please upgrade to access this part.
Upgrade NowBrowse More Related Video
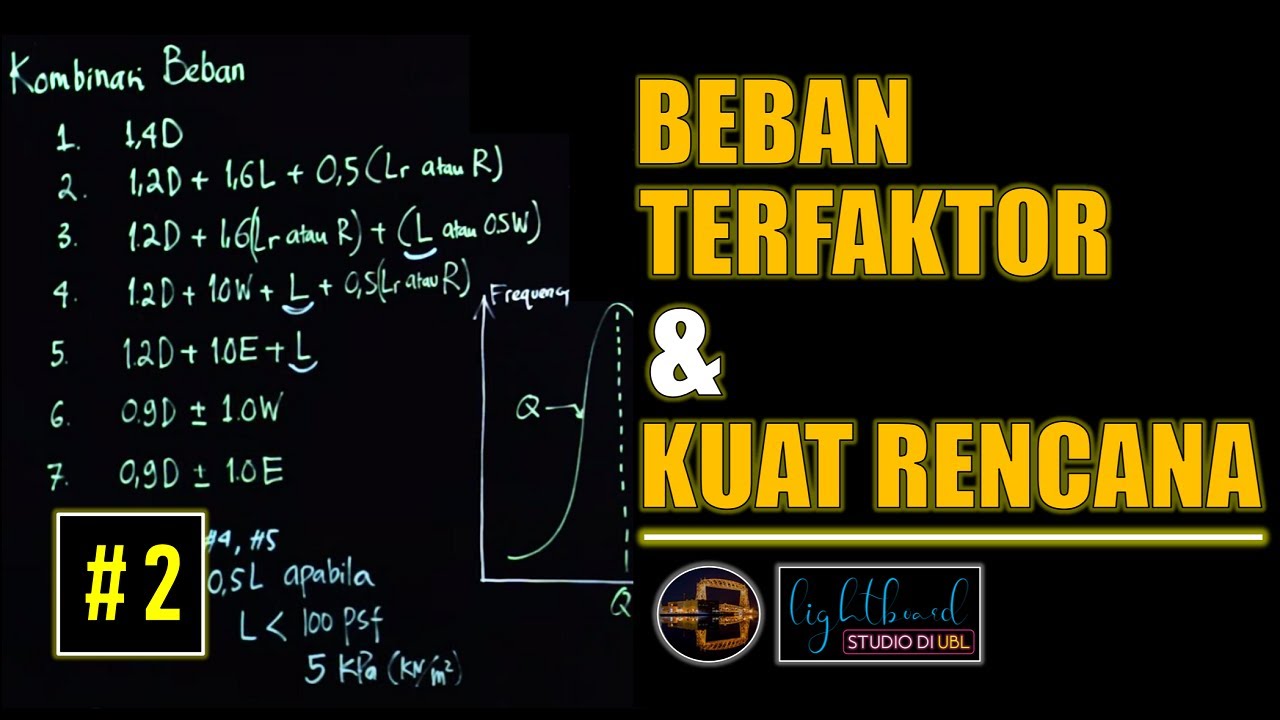
Beban Terfaktor (Ultimate Load) dan Kuat Rencana (Design Strength) Struktur Baja | Lightboard

NSCP 2015 LOAD PROVISION AND LOAD COMBINATIONS

Steel Plate Girder (Eurocode 3)-Summary By Dr.Ina
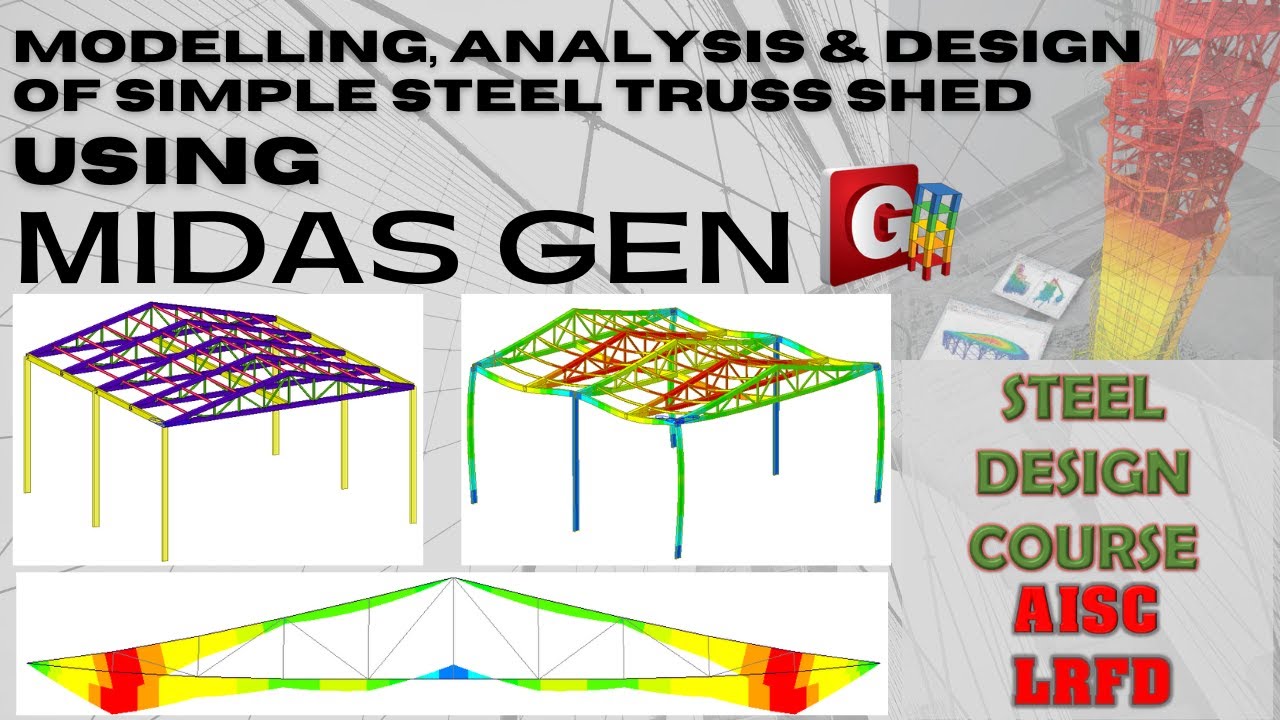
Steel Structures: Analysis/Design Course using MIDAS GEN - SIMPLE STEEL TRUSS SHED (Part 1)
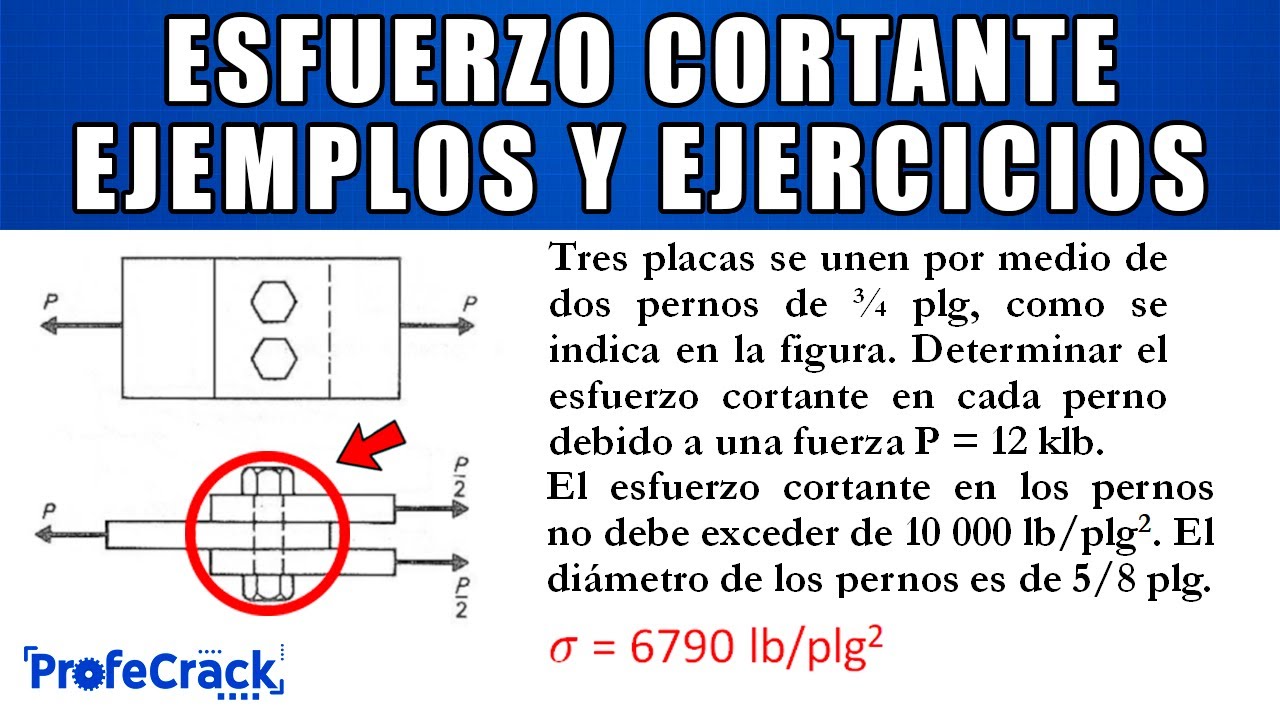
Esfuerzo Cortante: Ejemplos y Ejercicios Resueltos ✅ [Pernos y Placas] Mecánica de Materiales Fácil
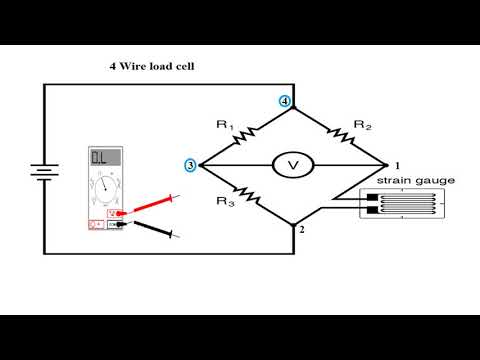
How to test a load cell
5.0 / 5 (0 votes)