Intel Supply Chain Strategy | semiconductor chip Shortage | Global crisis Supply Chain Case Study
Summary
TLDRIn 2007, Intel Corporation faced the challenge of reducing supply chain costs for their low-power Atom processor chip, targeting affordability for emerging markets. With an initial price of $20 per unit and supply chain expenses at 40% of the unit cost, Intel needed a radical approach. They adopted a 'make to order' strategy, reducing order cycle time from nine weeks to two, and supply chain costs per chip to under $1. Through initiatives like the 'Just Say Yes' program, Intel improved customer responsiveness and demand forecasting. The 'Low-Cost Supply Chain Project' led to a significant cost reduction, enabling Intel to deliver Atom chips at a more competitive rate, boosting their potential to double their business.
Takeaways
- 🌟 Intel Corporation, a leading semiconductor manufacturer, aimed to reduce the supply chain cost for its Atom chip to meet affordability targets.
- 💡 The Atom chip was a low-power processor designed for mobile devices, consumer electronics, and light computing, with a significant impact on Intel's unit economics.
- 💰 Traditional Intel processors had a supply chain cost of 5.5% of the unit price, but for the Atom chip, this was initially 40% higher than the target due to its lower price point.
- 🚀 Intel aimed to ship 20 million Atom processors in the first year, recognizing the potential for a large market in emerging economies.
- 🛠 The 'Make to Order' strategy was adopted to streamline the supply chain, reducing order cycle times and inventory levels.
- 🔧 Intel launched the 'Just Say Yes' program to improve customer responsiveness, reduce order fulfillment delays, and enhance overall customer satisfaction.
- 📈 The initiative focused on improving order change response times, committing to delivery dates, reducing inventory, and automating processes to increase efficiency.
- 📊 A team led by Mr. Kelso was tasked with creating a low-cost supply chain, aiming to deliver 900 million units annually at reduced costs while improving customer service.
- 🕒 The order cycle time for the Atom chip was reduced from nine weeks to just two weeks, significantly cutting supply chain costs per unit.
- 📉 The supply chain cost reduction for the Atom chip was more than four dollars per unit, making it more affordable and competitive in the market.
- 📚 The script emphasizes the importance of innovative supply chain strategies and customer-focused initiatives in achieving business goals and cost reductions.
Q & A
What was Intel Corporation's task regarding the Atom chip?
-Intel Corporation was tasked to reduce the supply chain cost of the Atom chip to meet affordability targets before the product launch.
What was the average selling price of Intel's traditional processors?
-Intel's traditional processors were sold for around $100 per unit on average.
What was the introductory price of the Atom chip, and what was the expected future price?
-The introductory price of the Atom chip was $20, which was expected to fall to $10.
What percentage of the unit cost did the supply chain and inventory costs constitute for Intel's traditional processors?
-The supply chain and inventory costs for Intel's traditional processors were 5.5 percent of the unit cost.
Why was the supply chain cost for the Atom chip significantly higher than for traditional processors?
-The supply chain expenses for the Atom chip were higher due to its low introductory price, making the supply chain costs 40 percent of the unit cost, which was not justifiable compared to the high cost of traditional processors.
How many Atom processors did Intel expect to ship in the first year of its launch?
-Intel expected to ship around 20 million Atom processors in the first year of its launch.
What was the annual revenue potential for Intel in the devices represented by the Atom chip?
-The devices represented an annual revenue potential of $10 billion or more for Intel.
What was Intel's strategy to reduce supply chain costs for the Atom chip?
-Intel's strategy included implementing a 'make to order' model, reducing order cycle time, and decreasing inventory levels.
What was the 'Just Say Yes' program aimed at achieving?
-The 'Just Say Yes' program aimed to improve business processes based on real customer needs, focusing on quick and positive responses to change order requests, reducing inventory levels, and improving internal efficiency.
What was the objective of the 'Low-Cost Supply Chain Project' led by Mr. Kelso?
-The objective was to create the ability to deliver up to an additional 900 million units a year at lower product costs by 2012 while increasing customer service.
What was the final order cycle time for the Atom chip after the supply chain improvements?
-The order cycle time for the Atom chip was reduced from nine weeks to just two weeks.
What was the achieved supply chain cost reduction per unit for the Atom chip?
-Intel achieved a supply chain cost reduction of more than four dollars per unit for the twenty-dollar Atom chip.
Outlines
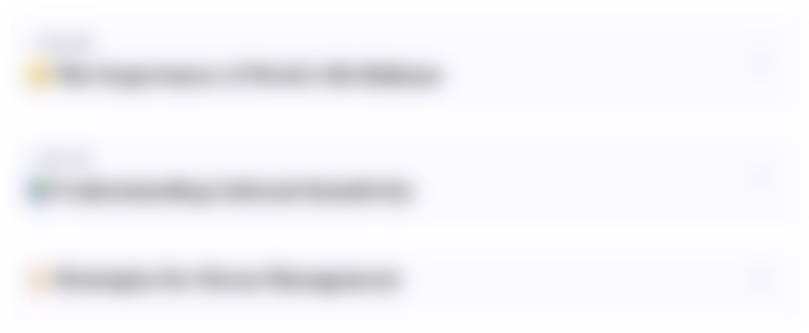
This section is available to paid users only. Please upgrade to access this part.
Upgrade NowMindmap
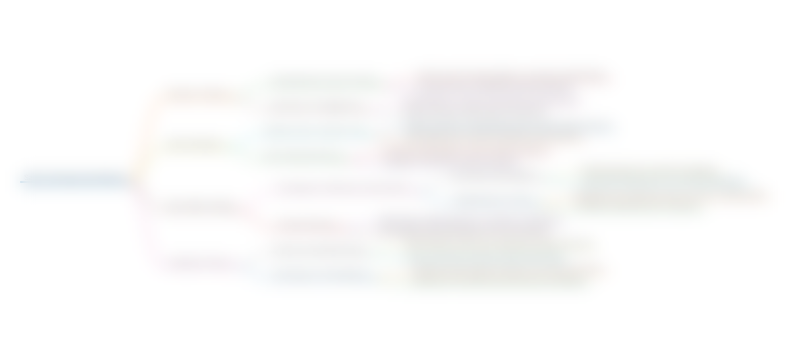
This section is available to paid users only. Please upgrade to access this part.
Upgrade NowKeywords
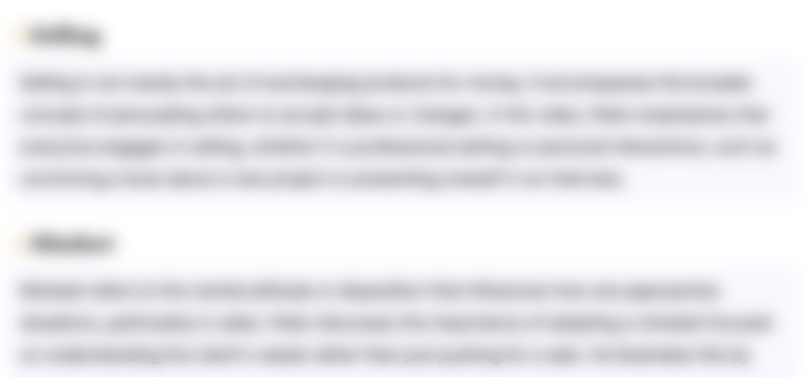
This section is available to paid users only. Please upgrade to access this part.
Upgrade NowHighlights
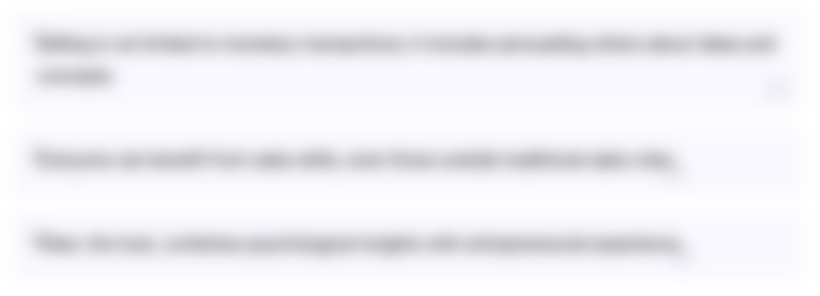
This section is available to paid users only. Please upgrade to access this part.
Upgrade NowTranscripts
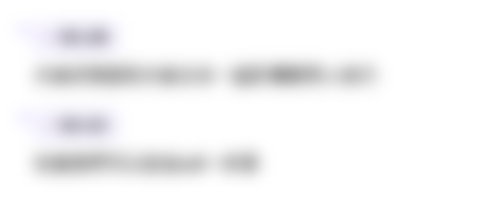
This section is available to paid users only. Please upgrade to access this part.
Upgrade NowBrowse More Related Video

Mcdonalds India | Mcdonalds Supply chain Strategy of French Fries | Supply chain Optimization | SCM

Intel Core i9-10900K Vs AMD Ryzen 9 3900XT : MANA PROCESSOR YANG TERBAIK ?

Why China is winning the EV war
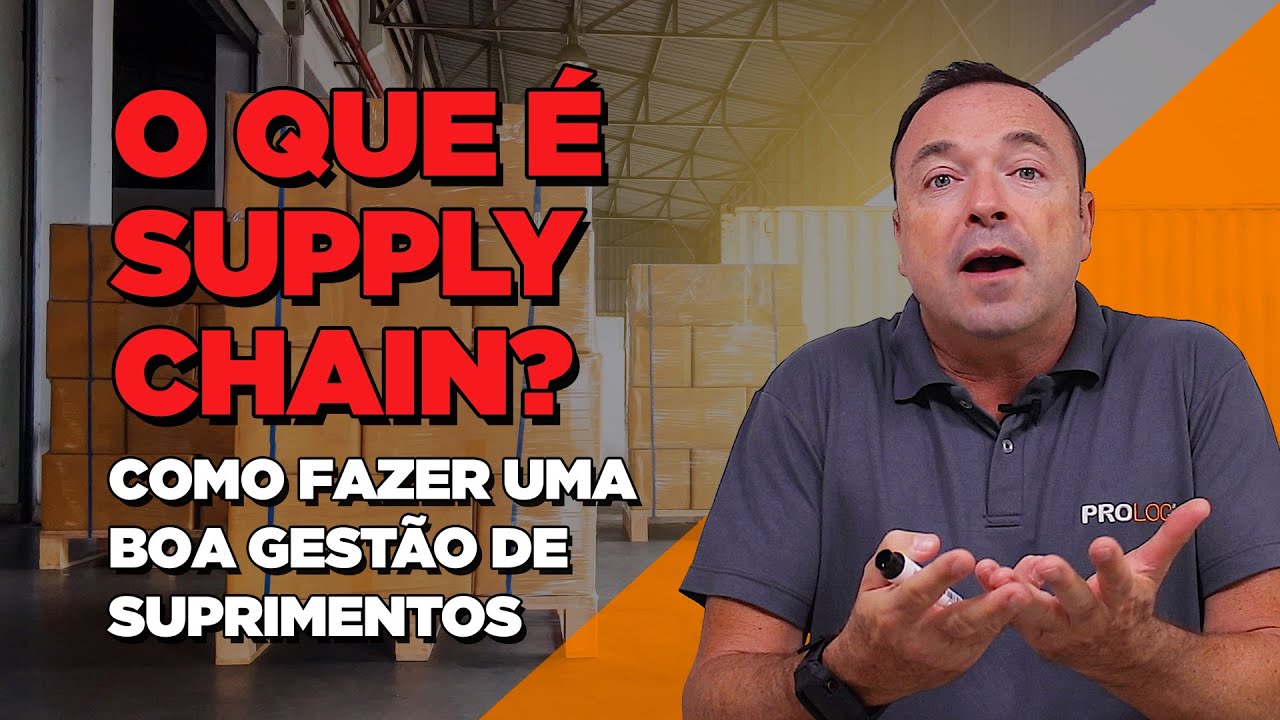
SUPPLY CHAIN - Tudo sobre CADEIA DE SUPRIMENTOS

Supply Chain Trends 2024 | What You NEED to Know!
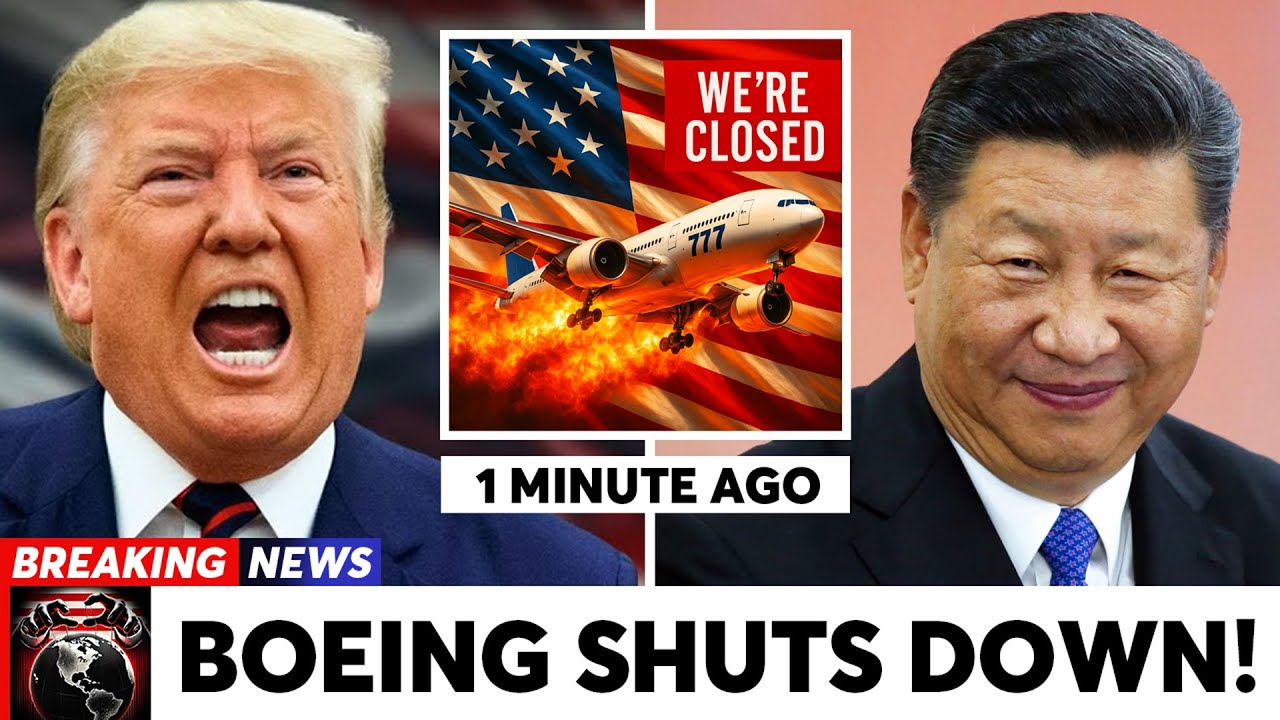
1 MIN AGO: Trump MELTS DOWN as Boeing SHUTS DOWN U.S. Production — Trump's Reaction SAYS It All
5.0 / 5 (0 votes)