Managing Your Assets 03 - We Can't Manage the Unknown
Summary
TLDRThis video discusses the importance of visibility into industrial assets, focusing on Rockwell and non-Rockwell products within a facility. It explains how conducting an installed base evaluation helps identify and document parts, categorize their lifecycle status, and prioritize risk management. The video highlights the need for spares and replacement planning, particularly for discontinued or end-of-life products. The process involves assessing all equipment across the plant, generating detailed reports, and using tools like My Equipment from Rockwell for web-based management. This helps companies ensure they can maintain operations and plan for future upgrades effectively.
Takeaways
- ๐ Visibility into assets is crucial for understanding equipment types, planning for failures, and ensuring coverage in a facility.
- ๐ Installed base evaluation provides a comprehensive list of assets, enabling better management through documentation and risk assessment.
- ๐ Understanding the lifecycle status of equipment (active, mature, end-of-life, discontinued) helps prioritize replacements and repairs.
- ๐ An end-of-life product gives a window to decide whether to migrate away or secure spares, with a typical timeframe of 18 months to 2 years.
- ๐ Discontinued parts are no longer manufactured, which increases the risk of difficulty in procuring replacements.
- ๐ MyRockwell Equipment offers web-based visibility, making it easier to manage and share equipment information across multiple locations.
- ๐ The lifecycle maturity of parts can impact budgeting, planning, and decision-making within a facility.
- ๐ Summaries in the evaluation provide insights into the total value of automation components and their representation within the facility.
- ๐ The evaluation process includes breaking down equipment by line or area to help focus on critical systems needing attention.
- ๐ Having a documented base evaluation supports discussions around budgeting, priority decisions, and provides a verified status for the plantโs automation systems.
Q & A
What is the purpose of conducting an Installed Base Evaluation (IBE)?
-The purpose of conducting an Installed Base Evaluation (IBE) is to gain visibility into all assets within a facility, document their lifecycle statuses, and assess risks. It helps facility managers understand what equipment they have, prioritize replacements, manage spare parts, and make informed decisions about upgrades and maintenance.
How does lifecycle status help in managing equipment in a facility?
-Lifecycle status categorizes equipment into four stages: active, mature, end-of-life (EOL), and discontinued. This helps facility managers understand the risk associated with each piece of equipment. Active equipment is the most up-to-date, mature equipment is still supported but older, EOL equipment is being phased out, and discontinued equipment is no longer available for purchase, though repair services may still be available.
What are the four lifecycle categories defined by Rockwell for equipment?
-Rockwell defines four lifecycle categories: 1) Active: the latest and most advanced products; 2) Mature: products still in production and supported but have been replaced by newer models; 3) End-of-Life (EOL): products being phased out but still available for a limited time; 4) Discontinued: products no longer manufactured but can still be repaired.
What is the risk associated with discontinued equipment?
-The risk with discontinued equipment is that it can no longer be purchased new. While these products may still be supported and repaired by Rockwell, their limited availability can make obtaining necessary spare parts more difficult, potentially leading to extended downtime or operational challenges.
How does an Installed Base Evaluation help prioritize which assets need attention?
-An Installed Base Evaluation lists all assets and categorizes them based on lifecycle status. This allows facility managers to identify which equipment is at risk (e.g., discontinued items without spares) and prioritize actions such as procuring spare parts, upgrading systems, or migrating to newer technologies.
How does the My Equipment from Rockwell tool enhance the Installed Base Evaluation?
-My Equipment from Rockwell is a web-based platform that takes the data from the Installed Base Evaluation and makes it more accessible. It allows facility managers to share equipment data across teams or multiple facilities and provides a deeper look at the lifecycle status and risks, such as discontinued parts with no spares.
Why is visibility into the equipment important for facility management?
-Visibility into equipment allows facility managers to track asset statuses, manage risks, ensure equipment availability, and optimize operations. It helps prevent unplanned downtime, manage spare parts inventory, and ensure that outdated or discontinued equipment is appropriately addressed.
What is the significance of categorizing equipment by area or line in an Installed Base Evaluation report?
-Categorizing equipment by area or line helps prioritize which parts of the facility require immediate attention. For example, if a production line relies heavily on discontinued parts, it would be more critical to address than a line with mostly active equipment. This helps focus resources and ensure operational continuity.
How does the IBE report provide value in budgeting and priority discussions?
-The IBE report provides a documented overview of the facilityโs equipment status, which can be used in budgeting and priority discussions. It helps decision-makers understand the value of automation assets, identify potential risks, and plan for upgrades or replacements in a cost-effective manner.
What type of information can be found in a typical Installed Base Evaluation report?
-A typical Installed Base Evaluation report includes details on the part numbers, lifecycle status, quantity of assets, risk assessment, and inventory of spares. It may also include a summary of the total value of automation assets, their current lifecycle stages, and the proportion of assets at risk of becoming obsolete.
Outlines
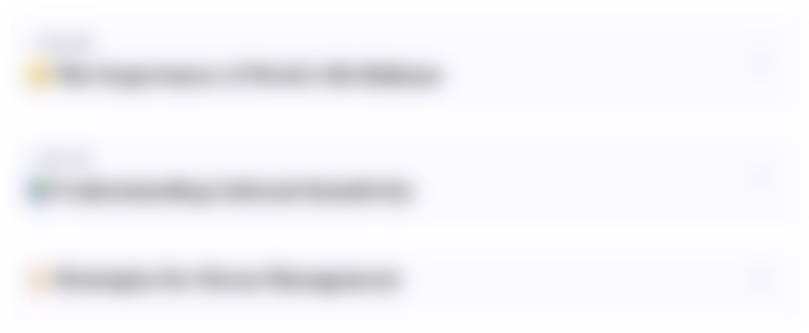
This section is available to paid users only. Please upgrade to access this part.
Upgrade NowMindmap
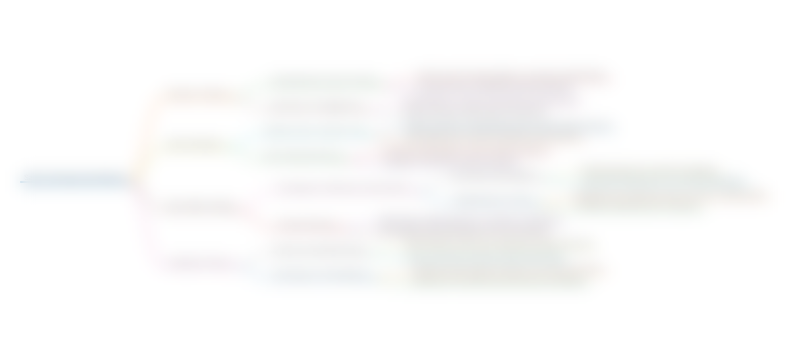
This section is available to paid users only. Please upgrade to access this part.
Upgrade NowKeywords
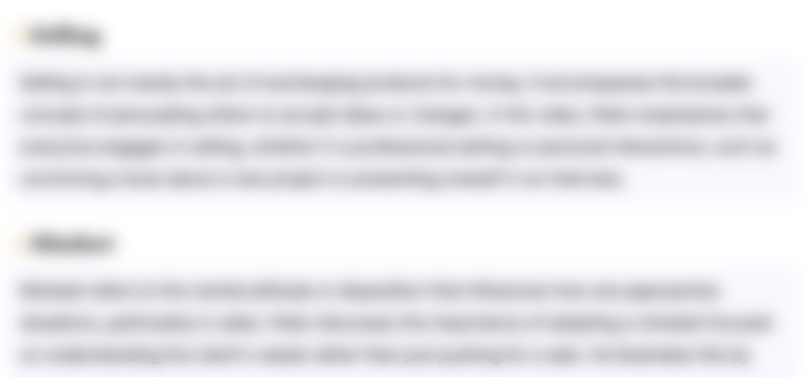
This section is available to paid users only. Please upgrade to access this part.
Upgrade NowHighlights
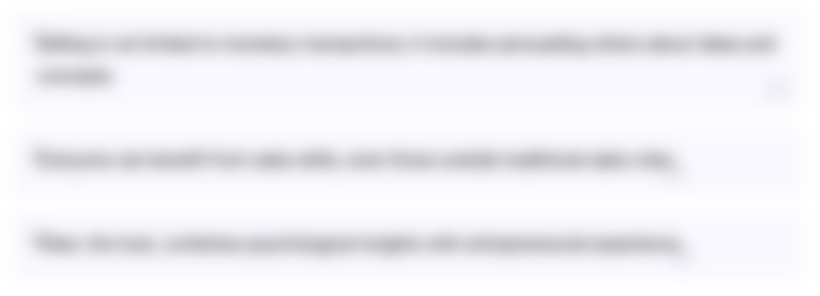
This section is available to paid users only. Please upgrade to access this part.
Upgrade NowTranscripts
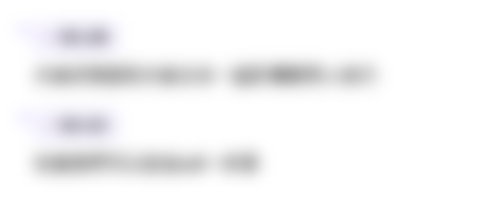
This section is available to paid users only. Please upgrade to access this part.
Upgrade Now5.0 / 5 (0 votes)